House Maurer, Wolfurt
Hofsteigstrasse 33
6922
Wolfurt, Austria
architetto
Owner
Contact Details
Other Information
https://www.holzbaukunst.at/events-aktivitaeten/holzbaupreis-2019/objekt/561.html
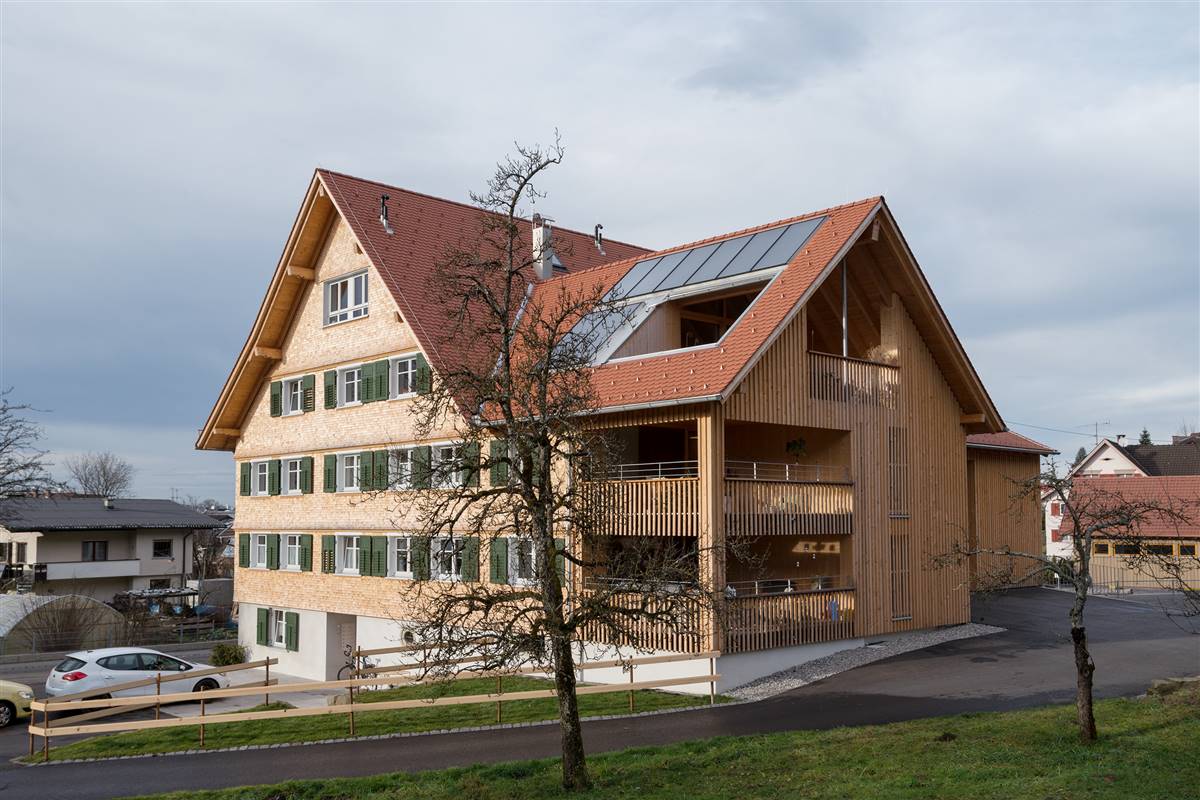
Climate Zone Cfb
Altitude 416 s.l.m.
HDD 2125
CDD 57
Conservation Area:
Si
Level of Protection:
Rheintalhäuser
Year of last renovation:
1989
Year of previous renovation:
2015
Secondary use:
NA
Building occupancy:
Permanently occupied
Number of occupants/users:
12
Building typology:
Tenement (apartments)
Number of floors:
4
Basement yes/no:
Si
Number of heated floors:
4
Gross floor area [m²]:
886,0
Thermal envelope area [m²]:
1370,0
Volume [m³]:
2436,0
NFA calculation method:
NGF (de)
External finish:
Exposed woodwork
Internal finish:
Exposed woodwork
Roof type:
Pitched roof
RENOVATION PROCESS
Architecture
BUILDING DESCRIPTION
State of repair
HERITAGE SIGNIFICANCE
Aim of retrofit
Baukultur Management Gmbh
Hof 651a, 6867 Schwarzenberg
office@baukulturgmbh.com
Tel.+43 5512 6061-0
Barbara Keiler
Amtsplatz 1, 6900 Bregenz
barbara.keiler@bda.gv.at
Tel.+43 676 88325 471
Stefan Küng
Feldweg 11, 6922 Wolfurt
beratung@stefankueng.at
Tel.+43 650 490 112 6
Hygrothermal assessment No
Life Cycle Analysis (LCA) No
Other No
RETROFIT SOLUTIONS
External Walls
shingled wooden rope with panelling inside
The wooden rope was insulated inside and outside with wooden insulation boards
On the outside a shingle umbrella was used again. The panelling inside was replaced by sheetrock.
15 mm
30 mm
120 mm
20 mm
15mm
50 mm
120 mm
0 mm
100 mm
30 mm
34 mm
Windows
wooden windows with insulating glass and partly still laminated glass
In the existing building mainly softwood windows with a 110 mm frame were installed. These were replaced by IV 88 profiles in spruce.
The division of the existing windows and shutters has been retained.
Existing window type | Double window |
Existing glazing type | Double |
Existing shading type | Outer shutter |
Approximate installation year | 1989 |
New window type | Double window |
New glazing type | Triple |
New shading type | Outer shutter |
New window solar factor g [-] | 0,5 |
Other interventions
ROOF
GROUND FLOOR
MEASURES TO INCREASE AIRTIGHTNESS
The previous cold roof was removed and insulated.
From the outside, the roof shape was preserved. A loggia was only integrated into the attached new building section.
20 mm
40 mm
160 mm
20 mm
90 mm
24 mm
160 mm
100 mm
0 mm
42 mm
The basement ceiling was renewed. The existing building had a solid wooden ceiling with fill. During the renovation an insulated reinforced concrete ceiling was installed thus increasing the clear height on the ground floor.
The measure increased the residential value and is not visible from outside.
12 mm
30 mm
50 mm
30 mm
80 mm
30 mm
140 mm
80 mm
20 mm
20 mm
10 mm
RENEWABLE ENERGY SYSTEMS
SolarThermal
Solar system on the new building part for hot water
The roof of the old building on the road worthy of protection was not changed.
Roof-integrated version on extension
SolarThermal System | |
---|---|
Type | Flat collector |
Collector area | 17,8 m² |
Elevation angle | 35,0 |
Azimuth | 64,0 |
Overall yearly production | 6000,0 kWh |
Heating_contribuition | 0,0 kWh |
DHW contribuition | 6000,0 kWh |
Cooling contribuition | 0,0 kWh |
Energy Efficiency
Voluntary certificates: No
Primary Energy 42649 kWh/y
Consumption_estimation_Before: 142 kWh/m2.y
Consumption_estimation_After: 35 kWh/m2.y
Primary Energy
Consumption_estimation_Calculation_method: Steady state simulation (e.g. EPC, PHPP)
Consumption_estimation_Including_DHW: Si
Consumption_estimation_Before: 57718 kWh/y
Consumption_estimation_After: 42649 kWh/y
Type_of_monitoring: Punctual
Description: Energy costs for heating and hot water were 2975€ for all residential units in 2019.
Internal Climate
The apartments are bright and sunny, as soon as the sun shines they are warmed by the sun.
Impact sound and structure-borne noise are bad because of the wooden floors, it requires understanding tenants.
Costs
No information on construction costs
2975€ (total)
Lifecycle cost
No