Magasinet i Varvsstaden, Malmö
Jagaregatan 4
211 19
Malmö, Suède
Architect
Owner
Contact Details

Climate Zone Dfc
Altitude 2
HDD 2403
CDD 17
Conservation Area:
Oui
Level of Protection:
q1 (the building is of particular cultural and historical value and must not be altered).
Year of last renovation:
0
Secondary use:
NA
Building occupancy:
Permanently occupied
Number of occupants/users:
150
Building typology:
Industrial building
Number of floors:
3
Basement yes/no:
No
Number of heated floors:
3
Gross floor area [m²]:
4500,0
Thermal envelope area [m²]:
4276,0
NFA calculation method:
Sweden
External finish:
Exposed brickwork
Internal finish:
Plastered (on hard)
Roof type:
Pitched roof


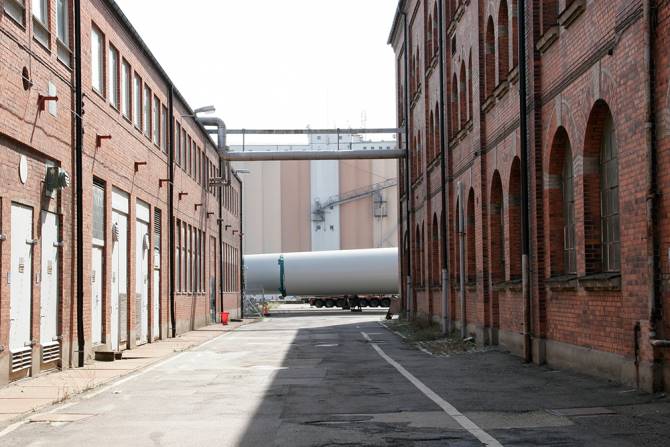
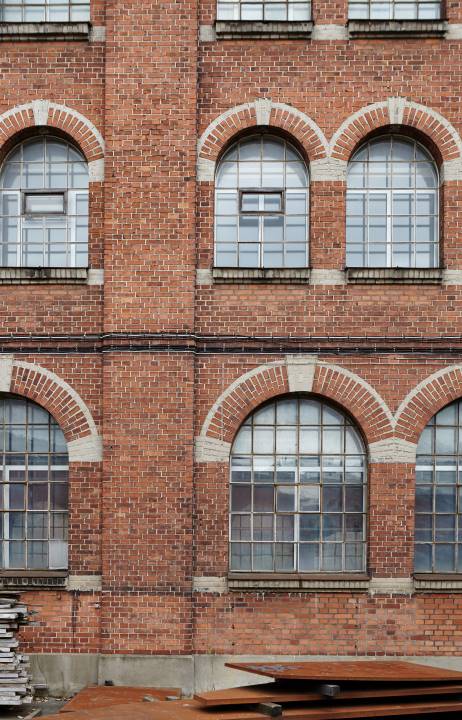
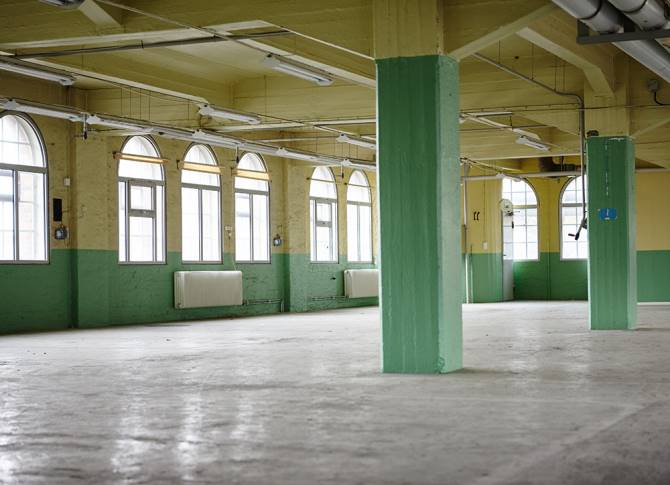
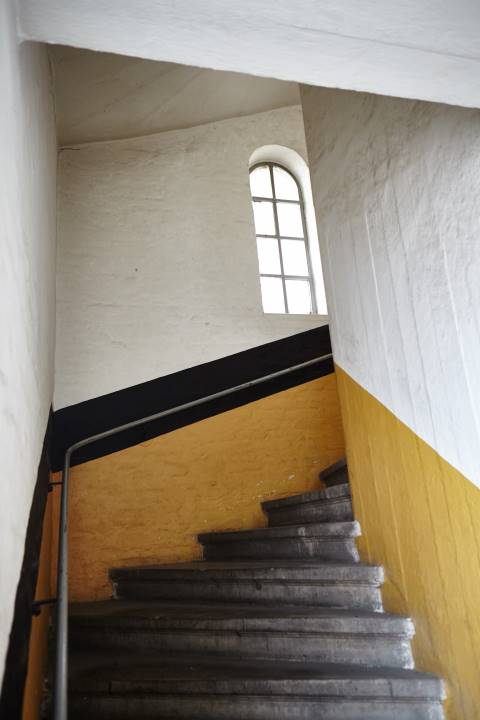
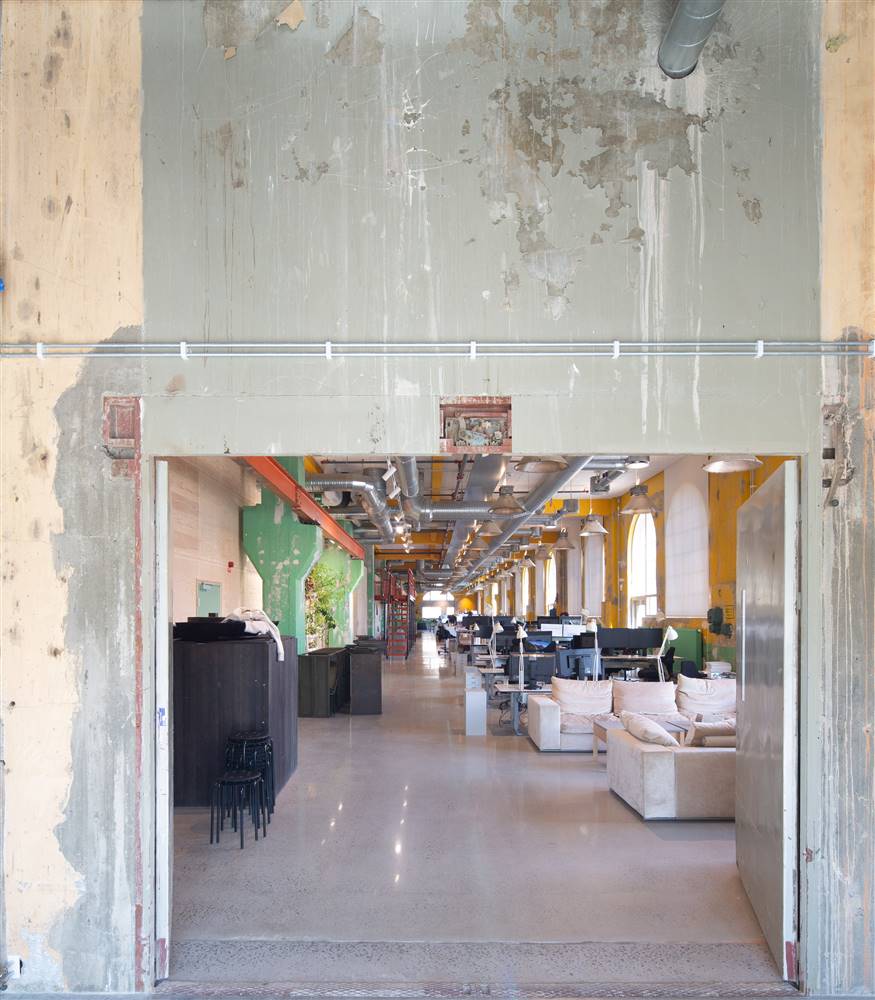
.jpg)
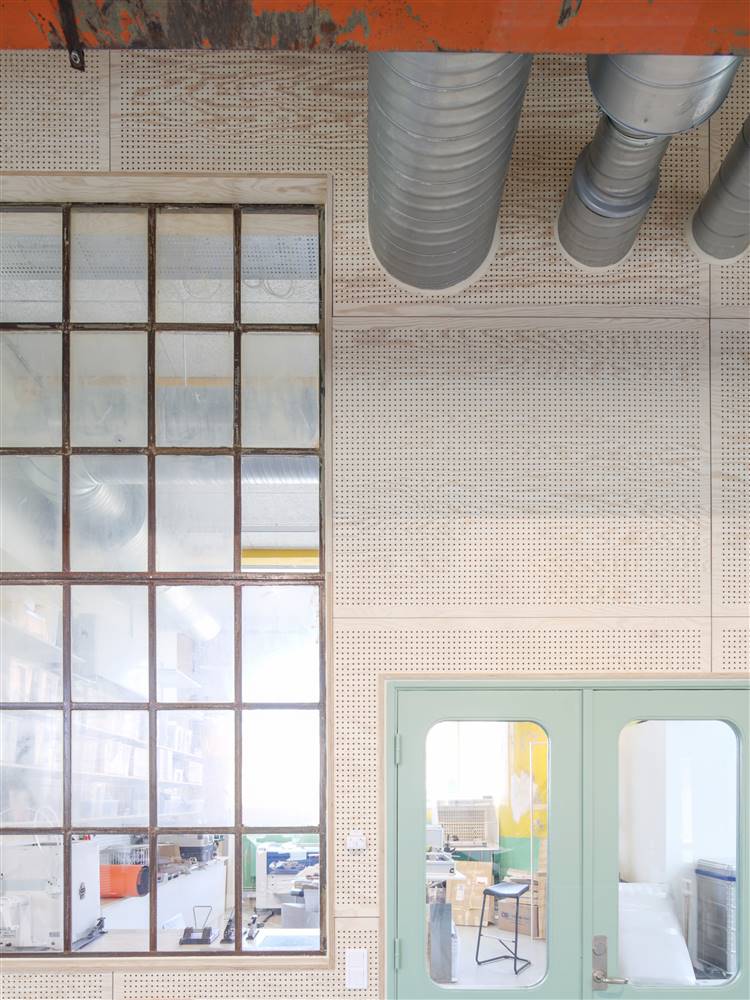
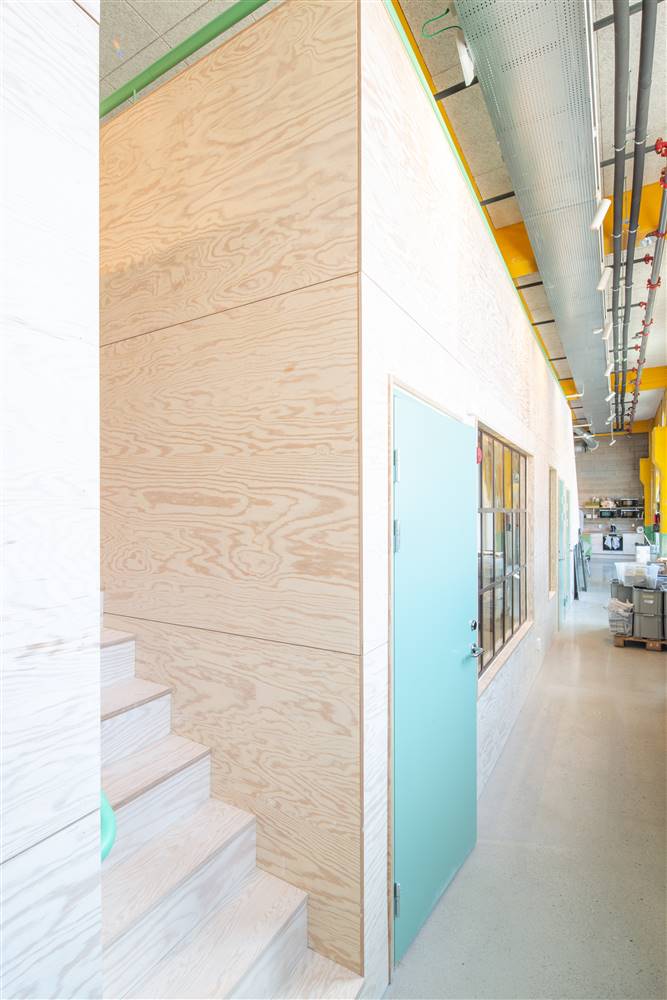
.jpg)
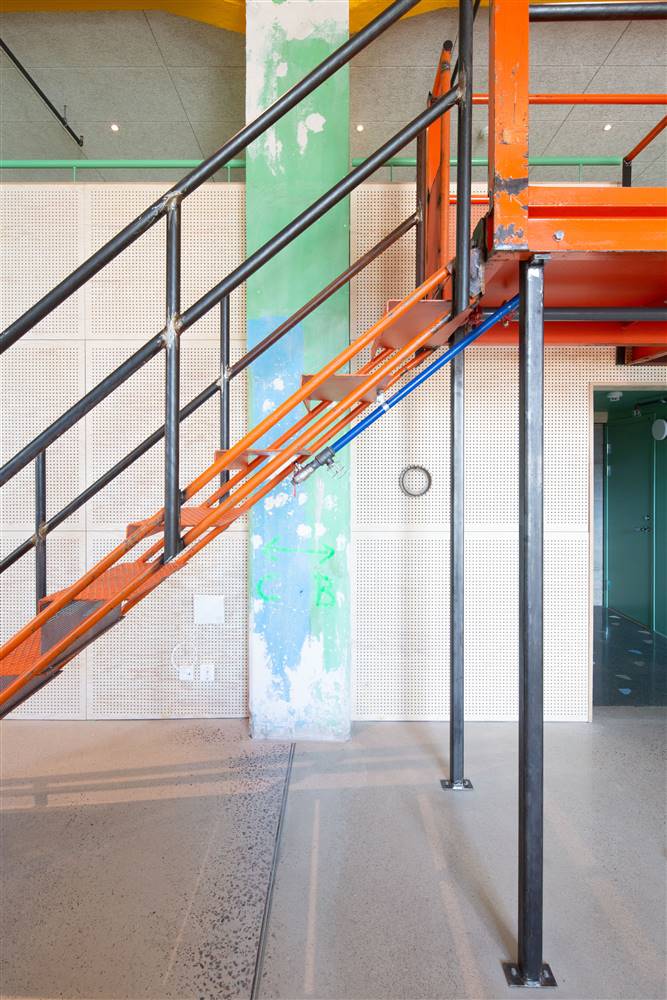
.jpg)
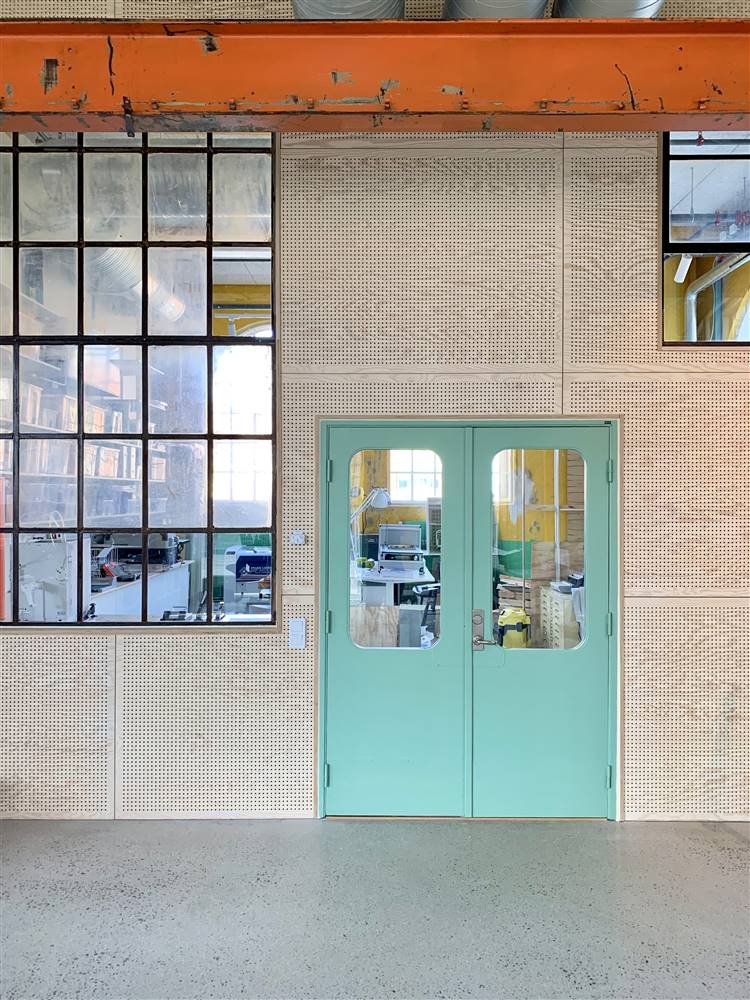
.jpg)
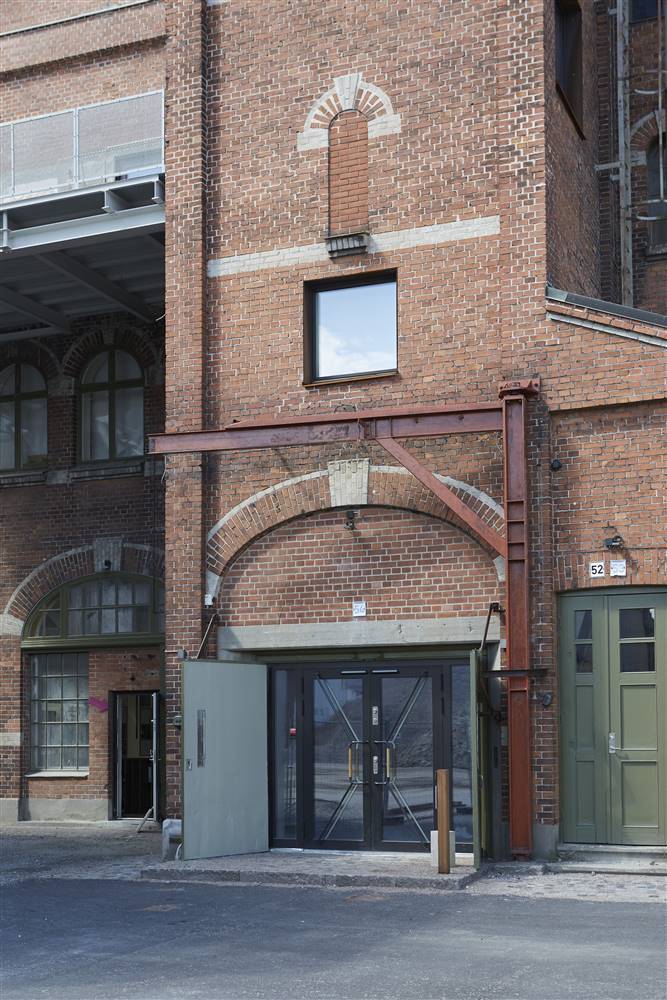
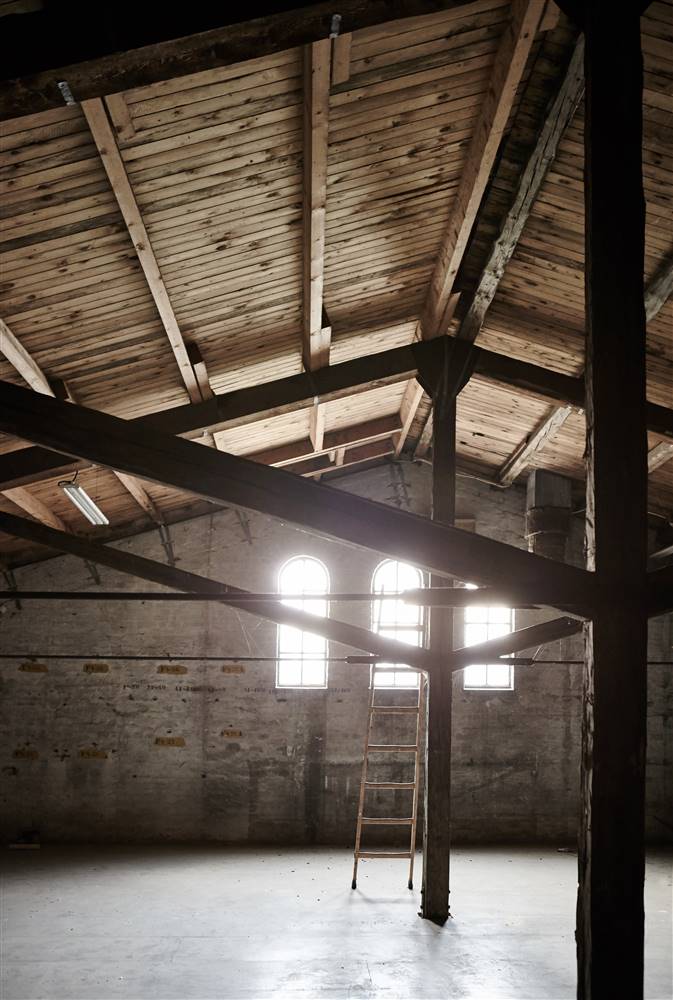
.jpg)
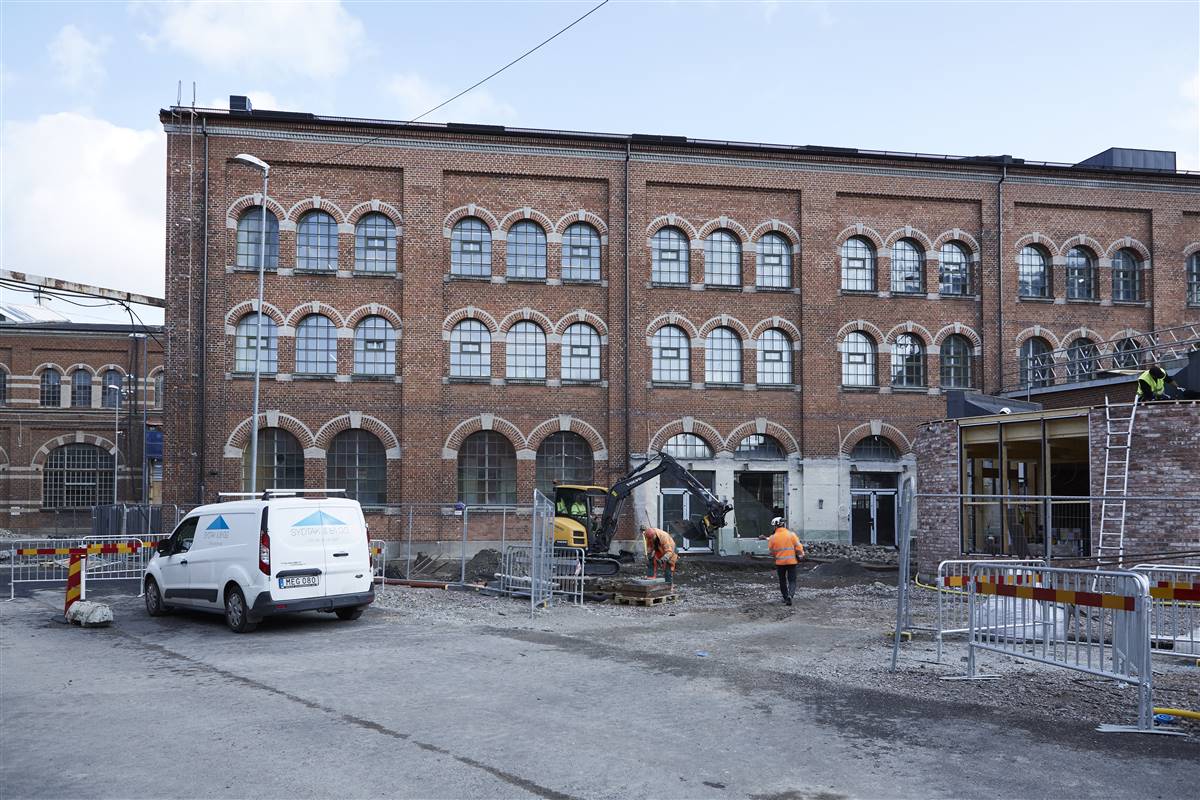
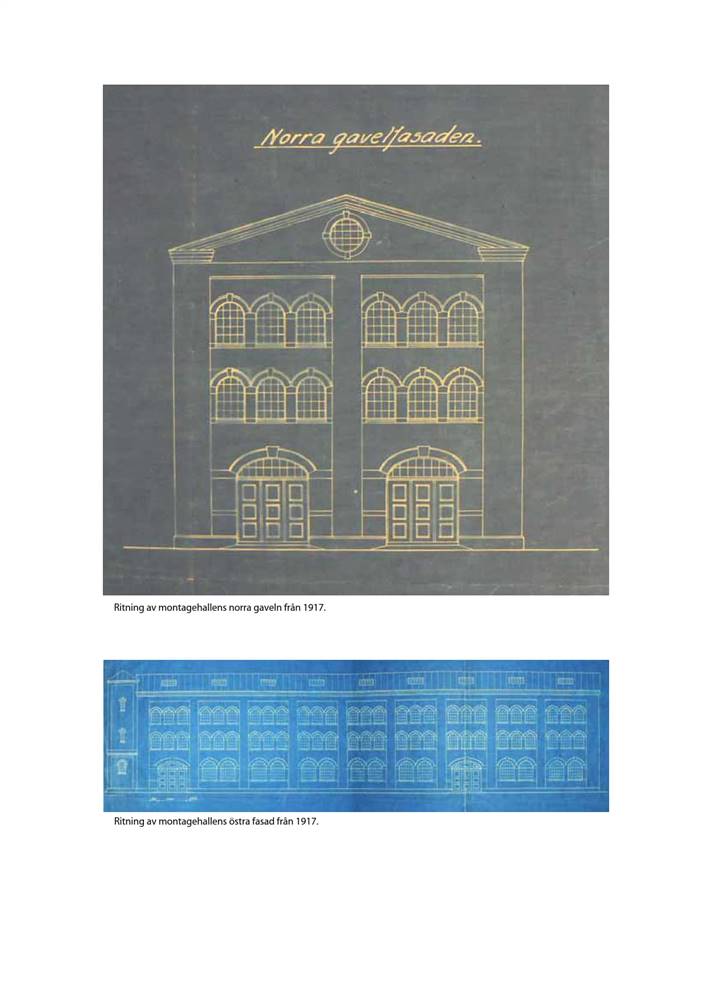
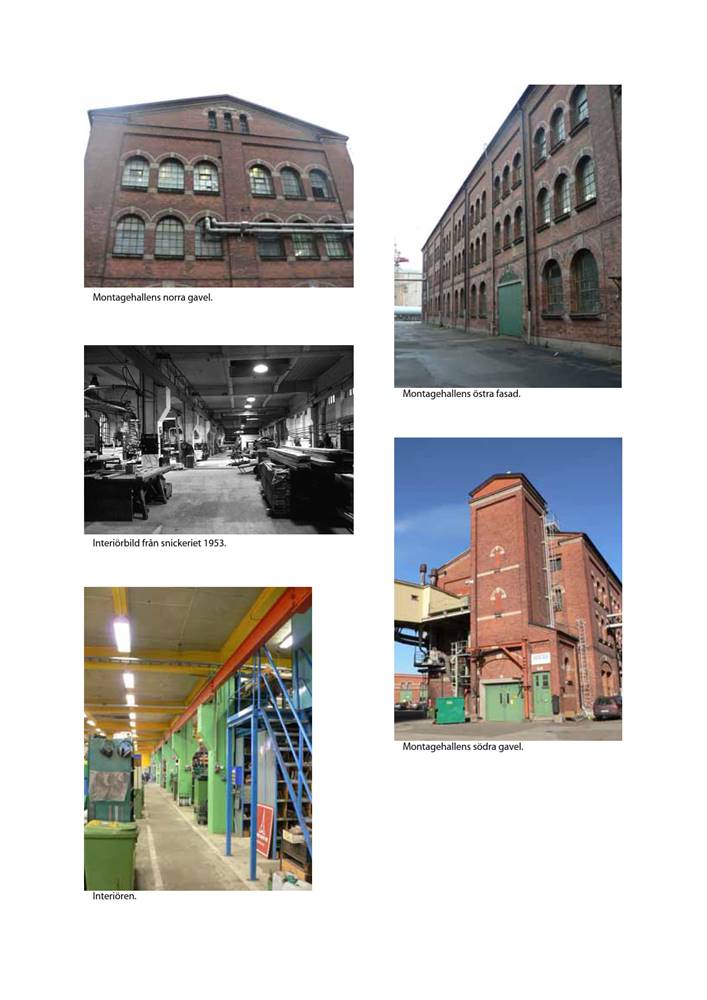
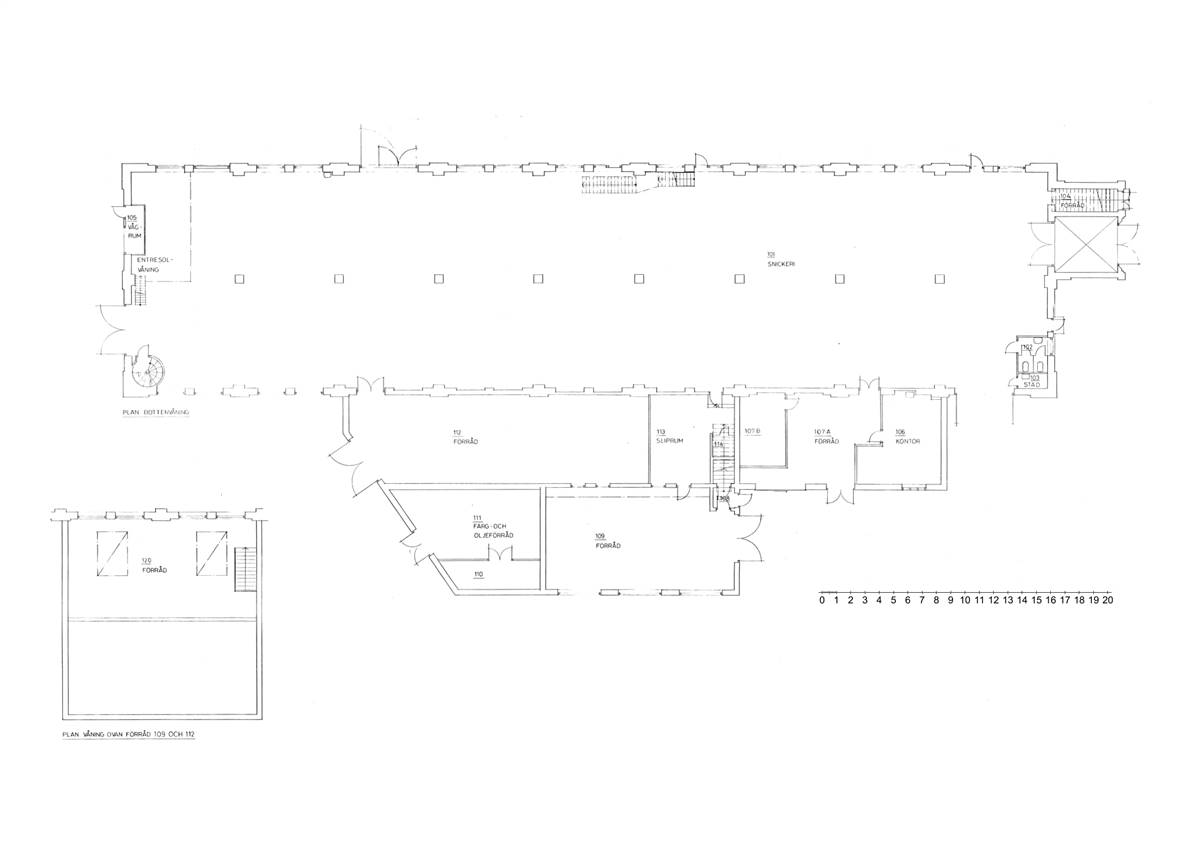
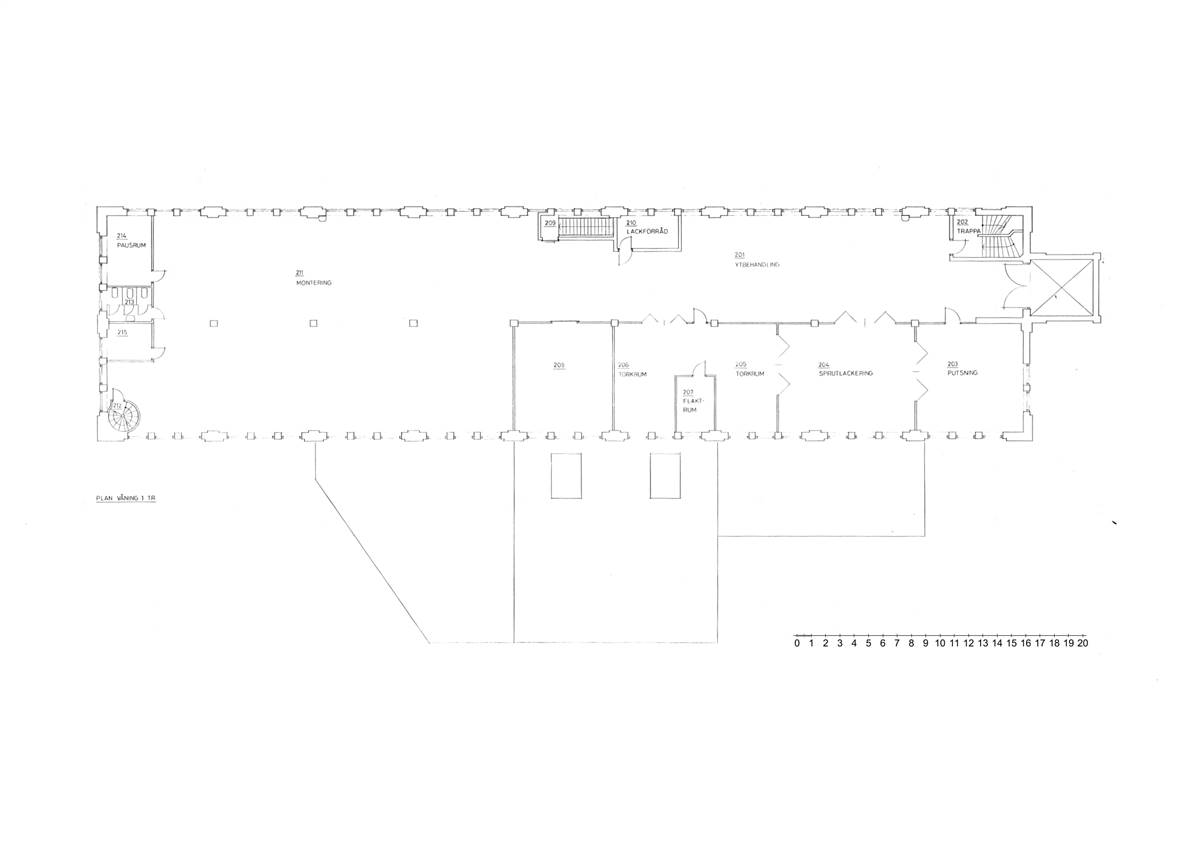
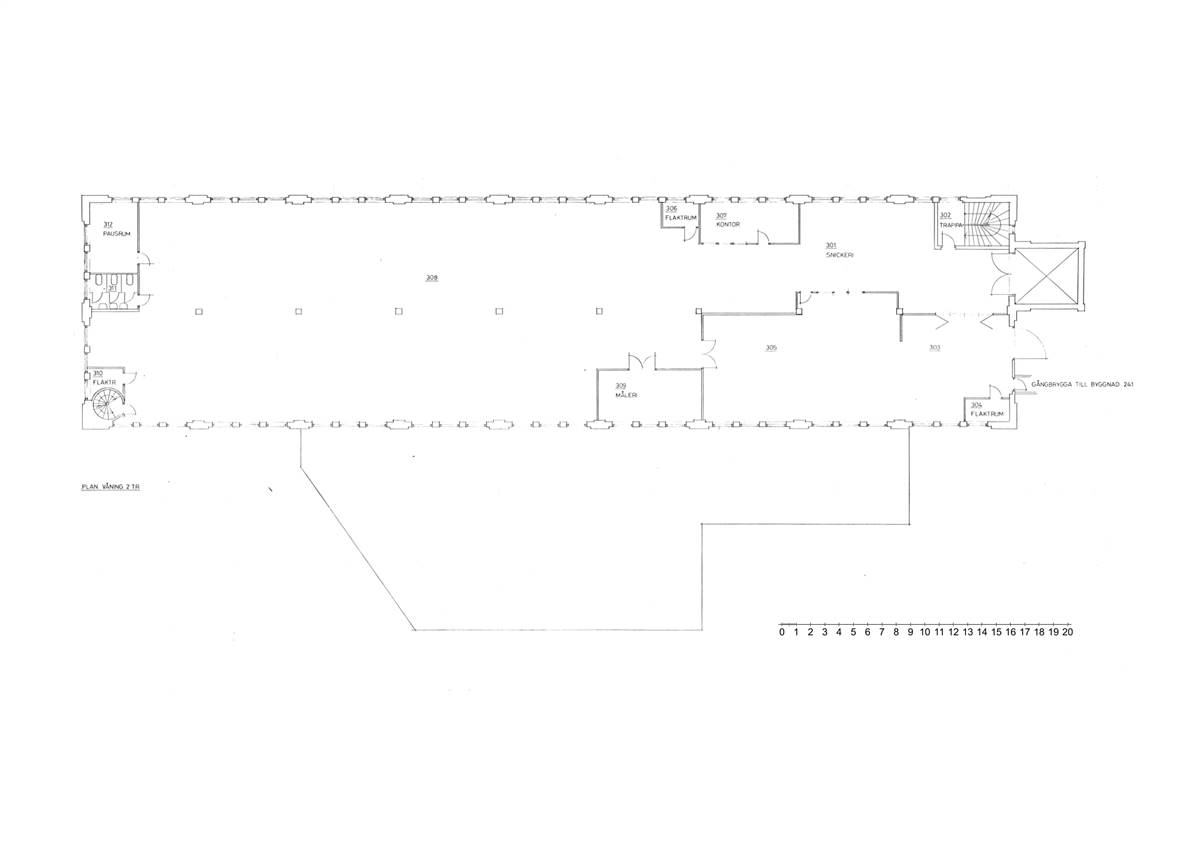
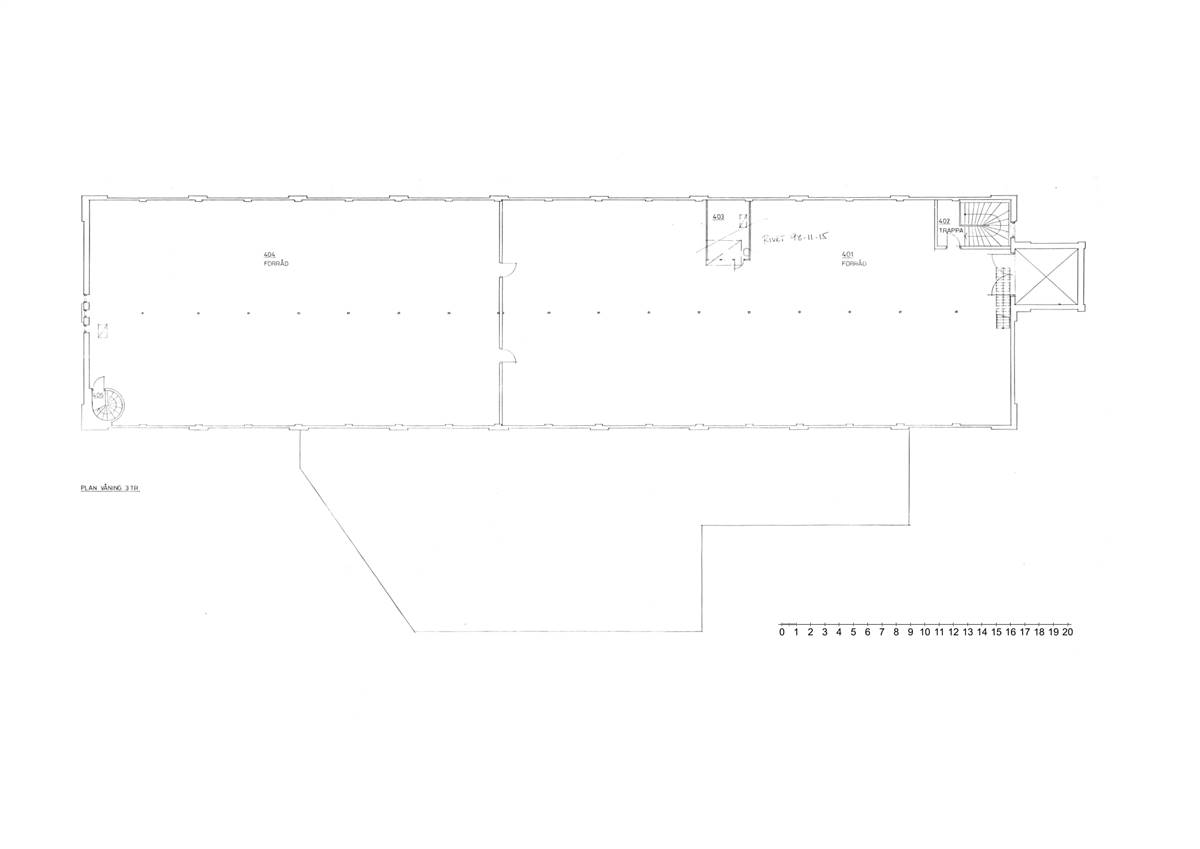
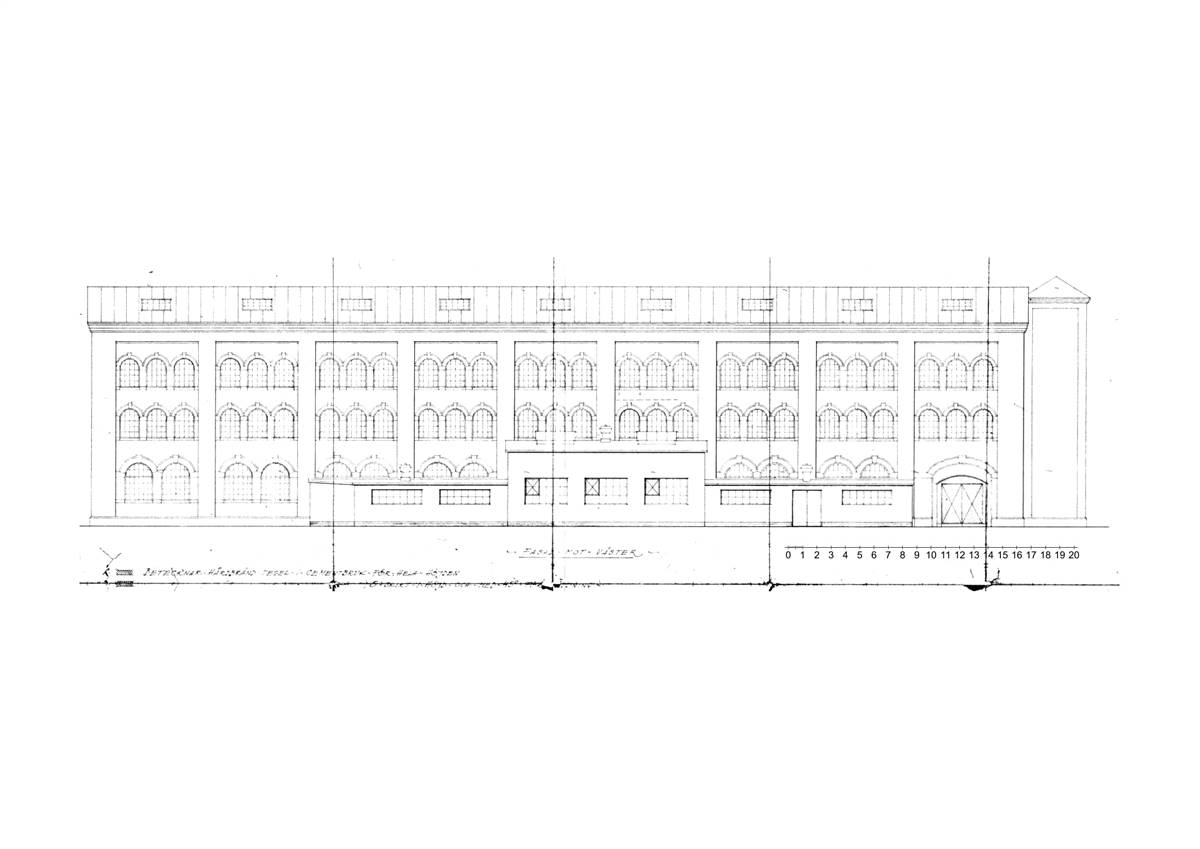
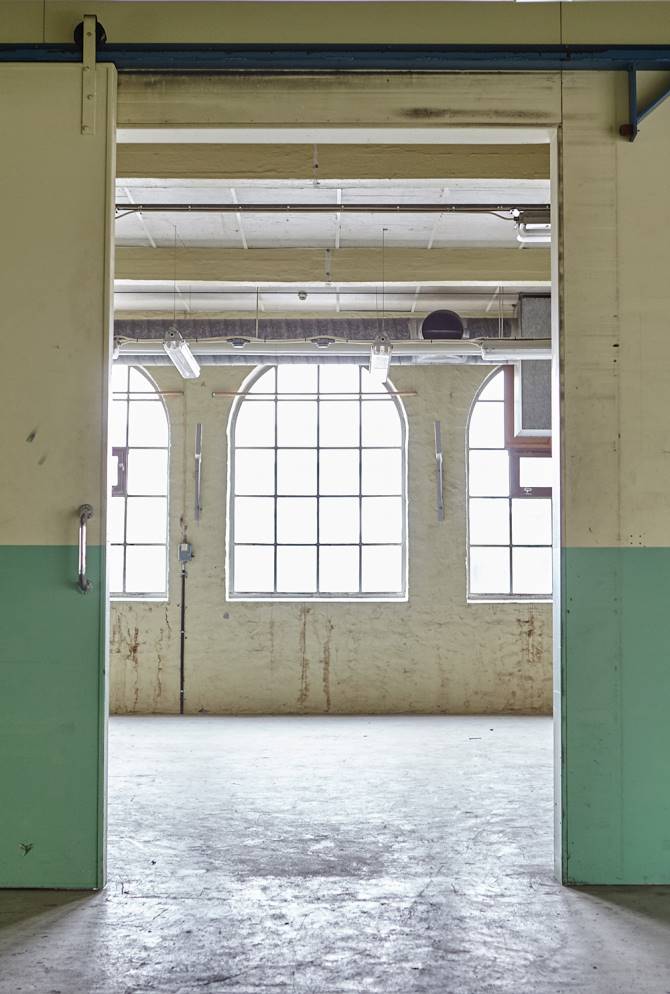
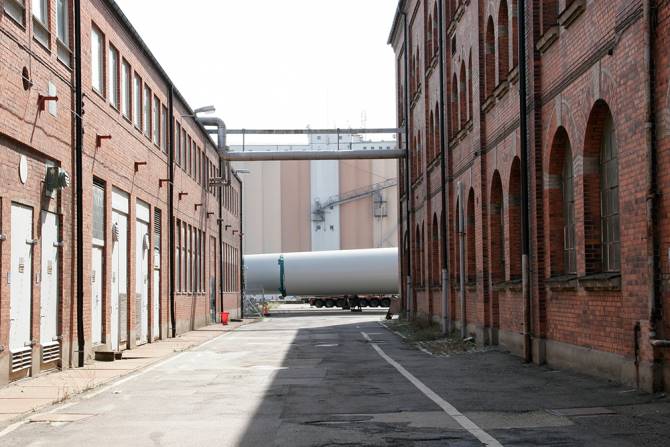
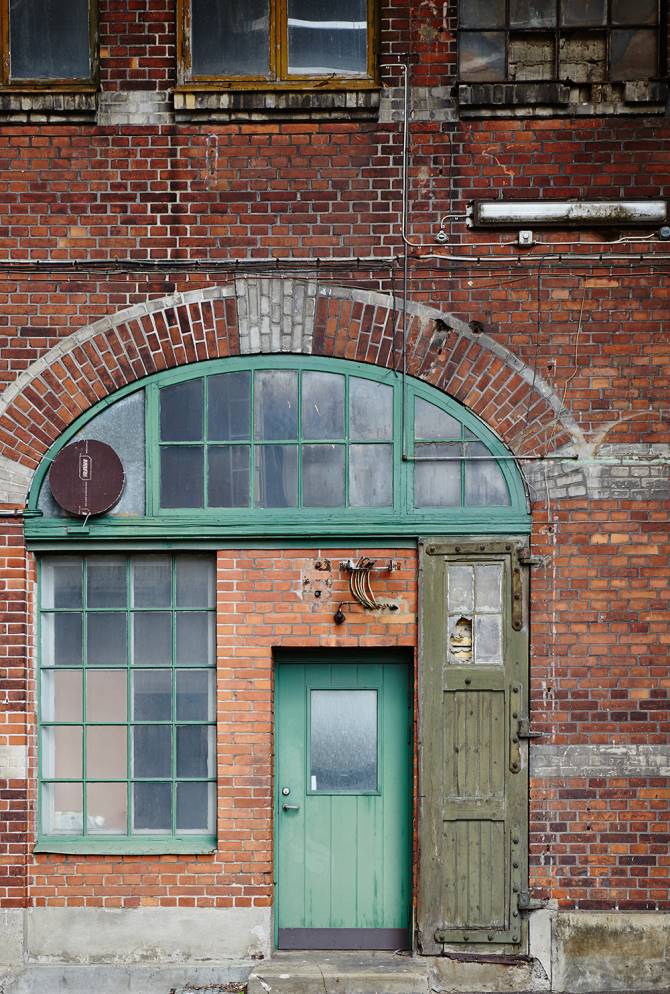
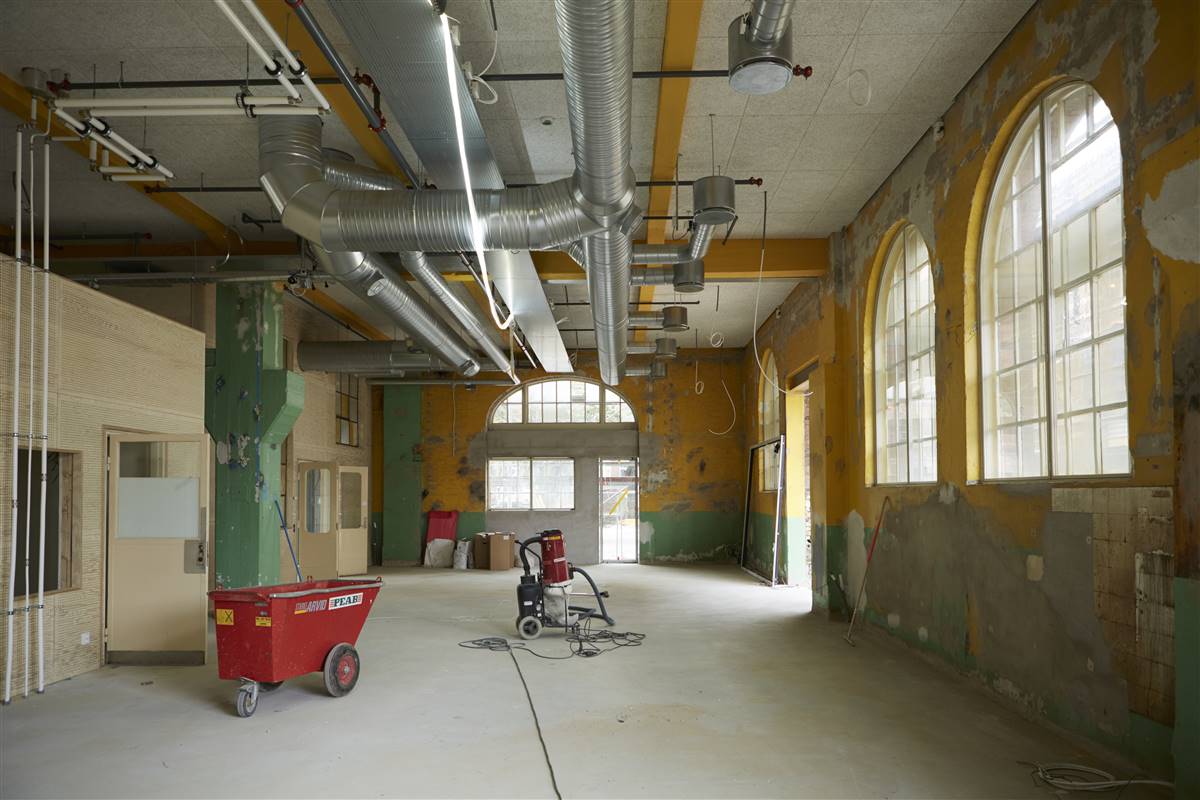
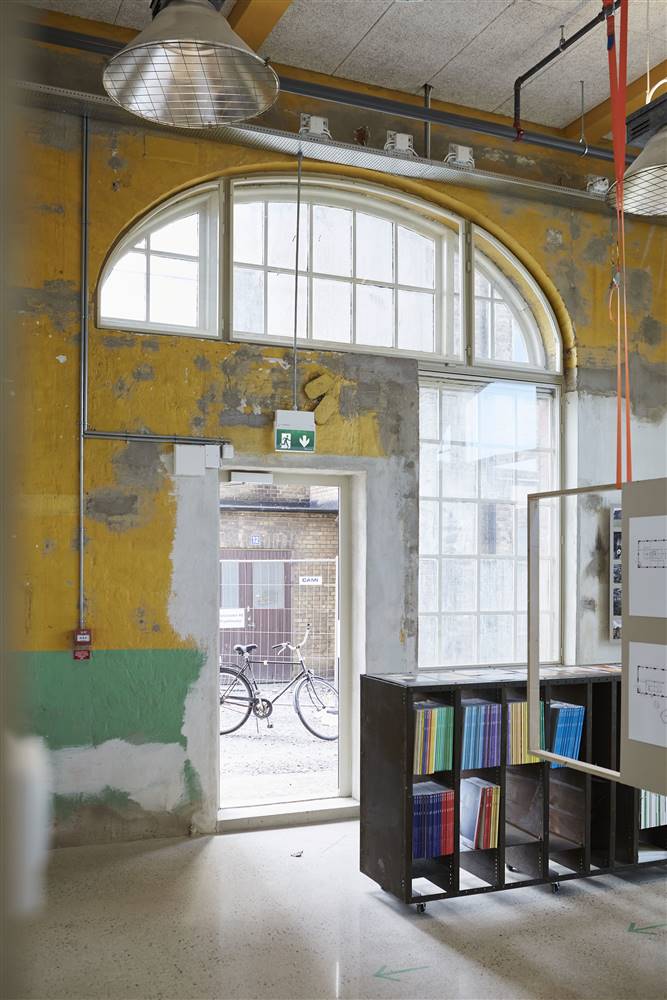
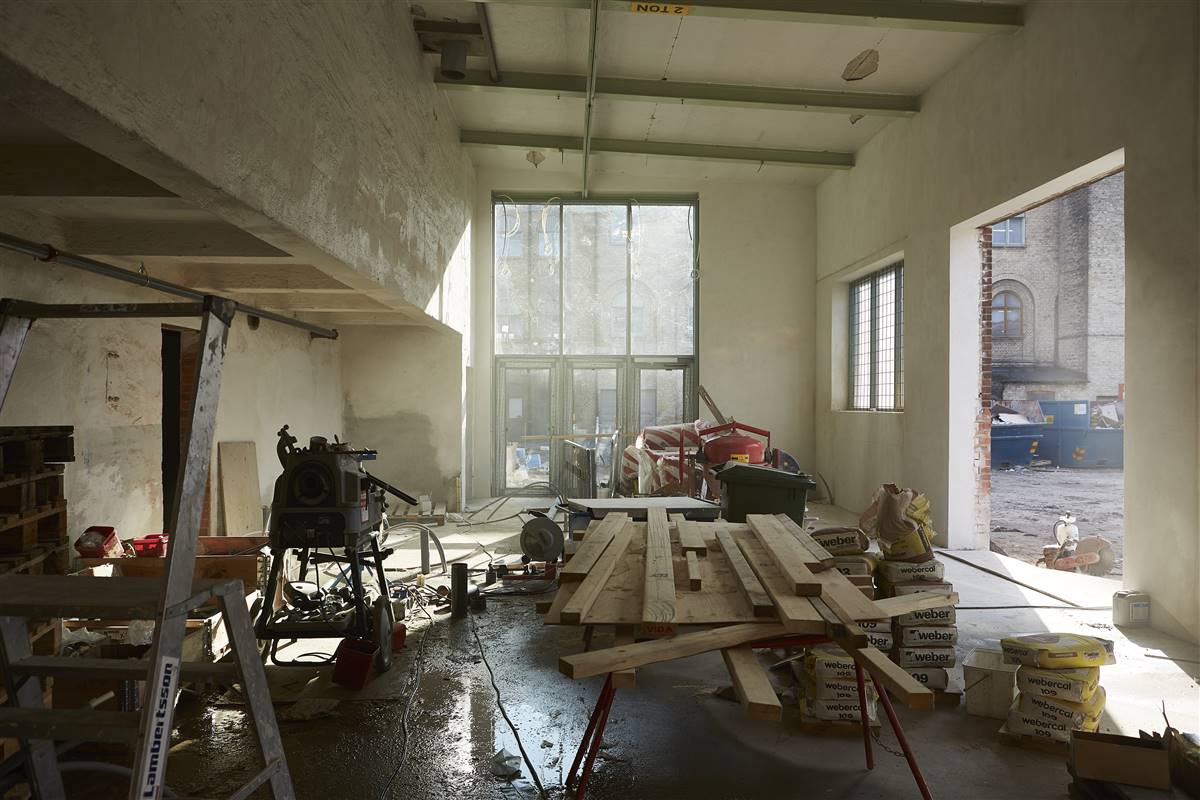
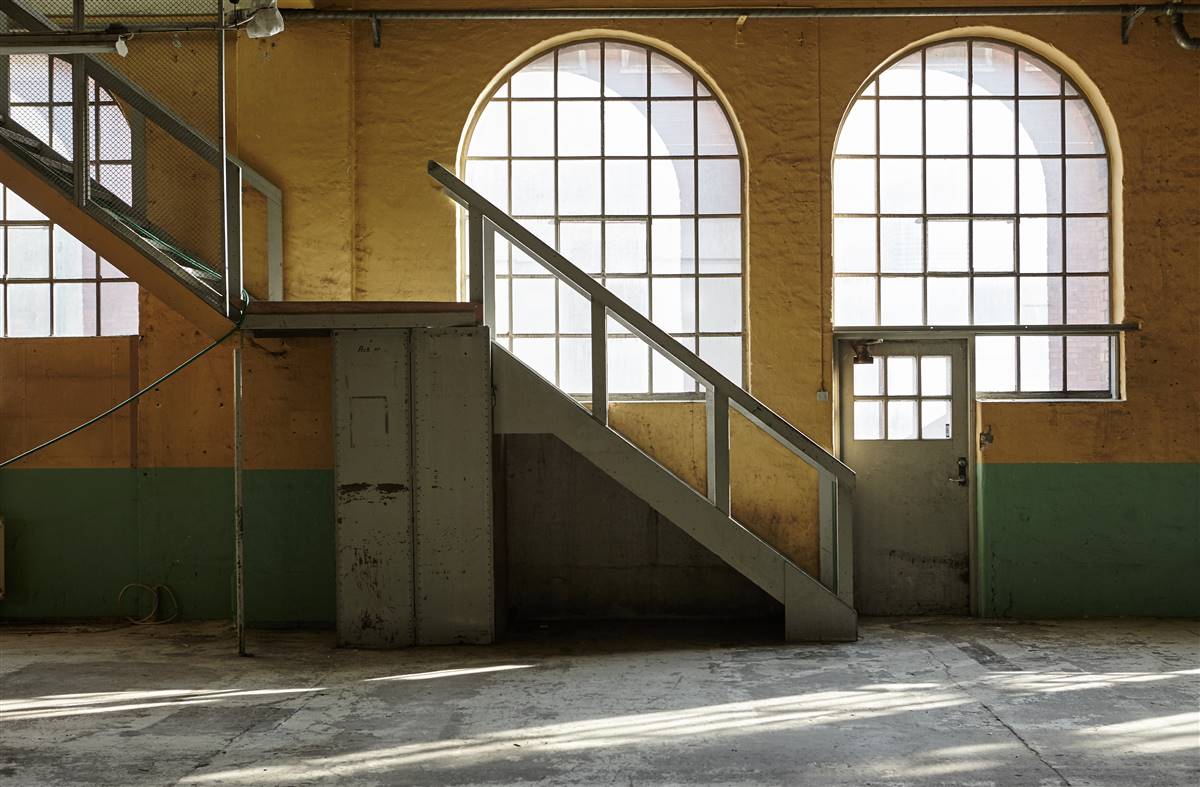
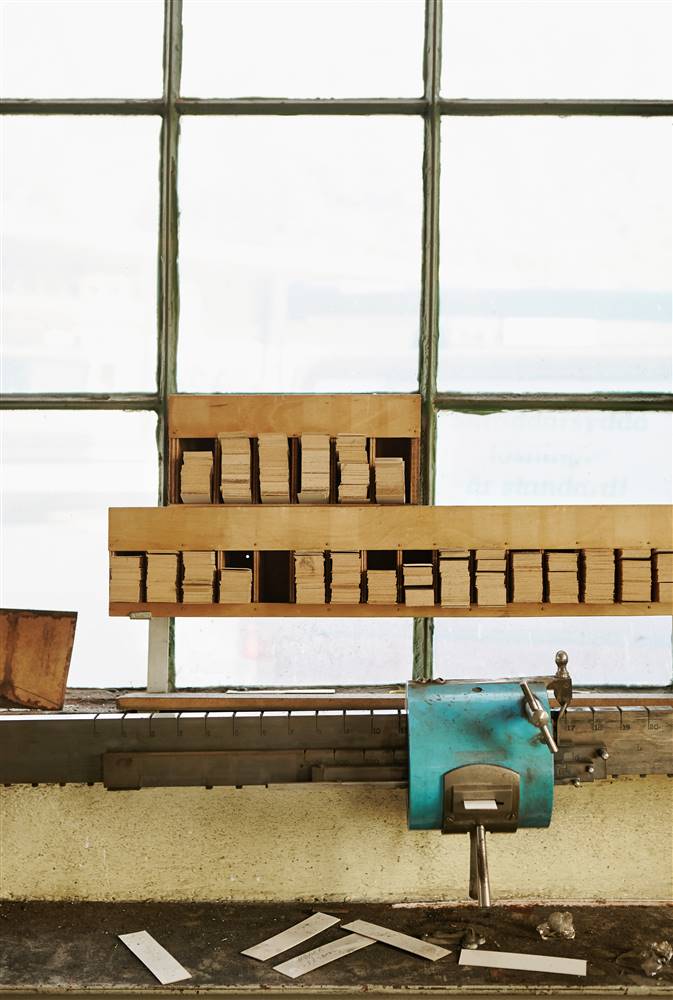
RENOVATION PROCESS
Architecture
BUILDING DESCRIPTION
State of repair
HERITAGE SIGNIFICANCE
Aim of retrofit
Wingårdhs Architects ab
Jagaregatan 4, 211 19 Malmö
Hygrothermal assessment NA
Life Cycle Analysis (LCA) NA
Other NA
RETROFIT SOLUTIONS
External Walls
External walls without additional insulation
External walls with additional insulation
The walls consist of brick walls of varying thickness between floors. Floors 1 and 2 consist of 510 mm thick brick walls. Here there would be risks with additional insulation, which in the worst case could lead to frost cracking in the walls. For this reason, it has been decided that additional insulation will not be applied on these storeys.
The cultural heritage value of the exterior walls on floors 1 and 2 is not affected as no changes have been made to the existing walls.
510 mm
5 mm
510mm
5 mm
On floors 3 and 4, where the wall thickness is less, it was considered appropriate to insulate the walls with 50 mm Multipor, λ=0.040. This is diffusion-open and thus well suited for this particular implementation.
The conditions for further internal insulation of the walls have been investigated in consultation with the structural engineer and the archaeologist and a solution has been found together so as not to negatively affect the heritage value and character of the existing external walls.
380 mm
5 mm
380mm
50 mm
5 mm
Windows
Existing windows that have been restored and additionally insulated.
On the inside of the existing windows, a modern type of window cassette will be installed. Window manufacturers have been contacted to select a suitable window cassette. A thermal window will be installed to achieve a low U-value to minimise energy consumption and reduce the risk of cold draughts. Some difficulties have been encountered in the selection of the window cassette. These consist of large windows and heavy structures that are difficult to install without compromising the aesthetic appearance of the building. In order to ensure that the space between the window cassette and the existing glass does not become too hot, and thus to avoid the risk of the old windows cracking from the heat, some caution has been taken with low U and G values. The chosen window cassettes have been considered suitable from this point of view by the window supplier.
Existing windows are preserved and consist of glass in cast iron windows. Some glass has been replaced and consists of flat glass. Other glass is blown glass from the building period (probably 2-3 mm thick). thick). The ratio between replaced glass and original glass is about 1:3. The solar shading cannot be placed on the outside of the building as it affects the aesthetic and cultural values of the building. Solar shading will therefore be placed on the inside.
Existing window type | Fixed window |
Existing glazing type | Single |
Existing shading type | NA |
Approximate installation year | 1917 |
New window type | Double window |
New glazing type | Double |
New shading type | Moveable shading |
Other interventions
ROOF
GROUND FLOOR
The existing roof was badly damaged, so the roof was additionally insulated and the roofing felt was replaced.
The existing roof could not be insulated from the inside due to the desire to preserve the existing ceiling. This means that insulation can only be added further out in the structure, which places certain limitations on the amount of insulation that can be added without destroying the aesthetic expression of the building (200mm mineral wool). This applies with the exception of the technical spaces (fan rooms) where the insulation will be located at the top of the construction. There, additional insulation can be placed on the inside of the roof as the space will not be accessible for the building users (another 150 mm of mineral wool). Moisture risks have also been taken into account.
10 mm
25 mm
120 mm
20 mm
20 mm
180 mm
20 mm
25 mm
120 mm
Existing floors on the ground are removed and insulation is added where possible. This means that the floors will be insulated (200mm foam) up to a small distance from the walls.
The existing floor was not considered historically valuable.
160 mm
150 mm
200 mm
160 mm
HVAC
HEATING
VENTILATION
AIR CONDITIONING
DOMESTIC HOT WATER
The renovation involved changing the heating system. The building is supplied by district heating.
The measures were carried out without major intervention in the existing structure.
New primary heating system | |
---|---|
New system type | District heating |
Fuel | Biomass |
Distribuition system | Radiators |
Nominal power | kW |
A new ventilation system (FTX) with heat recovery has been installed.
The new freestanding ventilation system affects the aesthetic value of the rooms but at the same time helps to maintain the original industrial character of the building's interiors.
Original roof build-up | New ventilation system |
---|---|
Type ventilation system | Centralized |
Type flow regime | Overflow |
Heat recovery | Oui |
Humitidy recovery | No |
Nominal power | 0.35-10.0 L/s m² kW |
Electric power | 1,8 kW |
Control system | Konstant |
A cooling system exists only in the electrical control centre, production demo hall, chemical storage and production lab. The system consists of a district cooling system where water is cooled in one place and distributed via pipes in the building. Cooling pipes are connected to cooling installations in the fan room on the attic floor. From there, cooling pipes are routed at the ceiling to units for connection of the combi battery and out to fan air coolers placed on the wall.
The district cooling system is located in the technical areas where no historical value is affected.
New cooling system | |
---|---|
Type | NA |
Distribuition system | Air |
Nominal power | NA kW |
Electric power | kW |
The renovation also included the installation of a new hot water system with hot water circulation (HWC). A pump constantly circulates the hot water so that it is always available at every tap. This also reduces the risk of bacterial growth, as the water never gets cold or stagnant in the pipes. Hot water is stored in a hot water source in the sub-centre.
The measure was carried out without major intervention in the existing structure.
New DHW system | |
---|---|
Type | with heating system |
Hot_water_tank | Oui |
With heat recovery | No |
Energy Efficiency
Voluntary certificates: No
Primary Energy 177,4 kWh/m2.y
Consumption_estimation_After: 94,4 kWh/m2.y
Primary Energy
Consumption_estimation_Calculation_method: Dynamic simulation (e.g. EnergyPlus)
Consumption_estimation_Including_DHW: Oui
Consumption_estimation_After: 177,4 kWh/m2.y
Costs
Drygt 120Mkr (about 10.000.000 Euros) (total)
Amount includes: The budget includes all costs, i.e. property costs, early stage feasibility study, design, rental/marketing, construction costs, developer costs (authorities/fees, etc.), financing, etc. What is not included is the demolition/stream cleaning and soil decontamination, which were not part of the redevelopment project itself but were carried out at an earlier stage.
No