Musikschule Velden
Bäckerteichstraße 1
9220
Velden am Wörthersee, Austria
Architect
Owner
User
Contact Details
Other Information
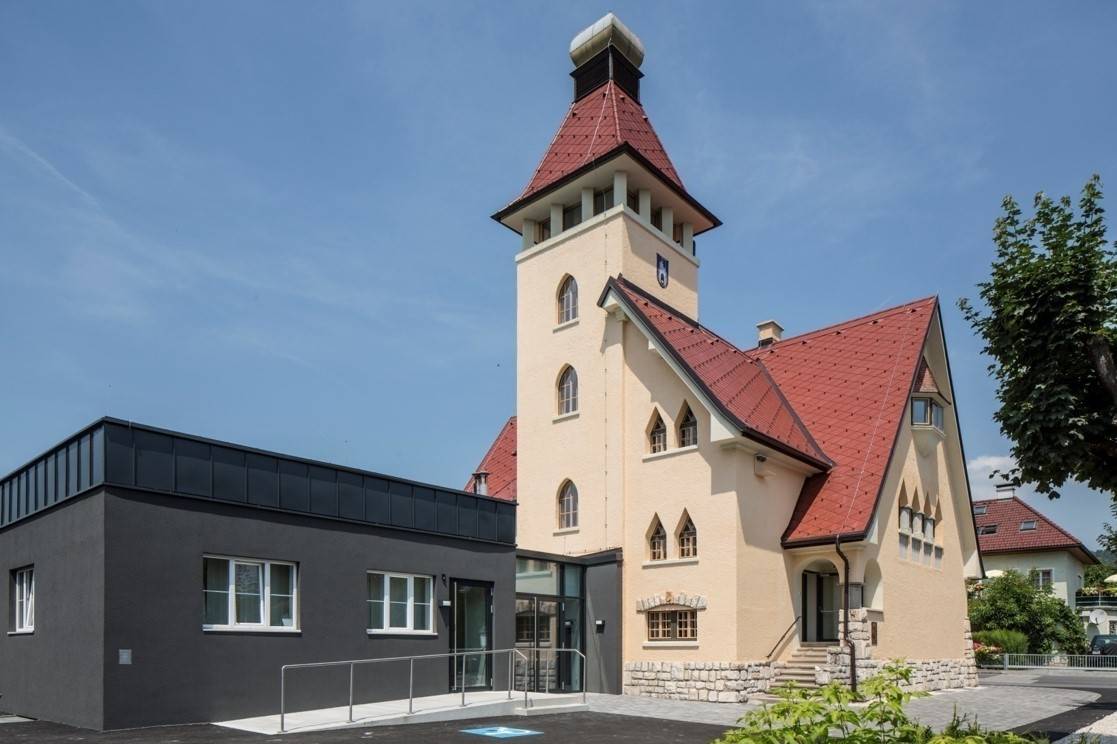
Climate Zone Dfb
Altitude 455 m a.s.l.
HDD 3753
CDD 100
Conservation Area:
No
Level of Protection:
DMSG § 2a
Year of last renovation:
2015
Year of previous renovation:
0
Secondary use:
NA
Building occupancy:
Discontinuous occupancy (i.e. holiday home)
Number of occupants/users:
0
Building typology:
Detached house
Number of floors:
5
Basement yes/no:
Yes
Number of heated floors:
4
Gross floor area [m²]:
1099,0
Thermal envelope area [m²]:
1732,0
Volume [m³]:
3062,0
NFA calculation method:
NGF (de)
External finish:
Rendered
Internal finish:
Plastered (on substructure)
Roof type:
Pitched roof
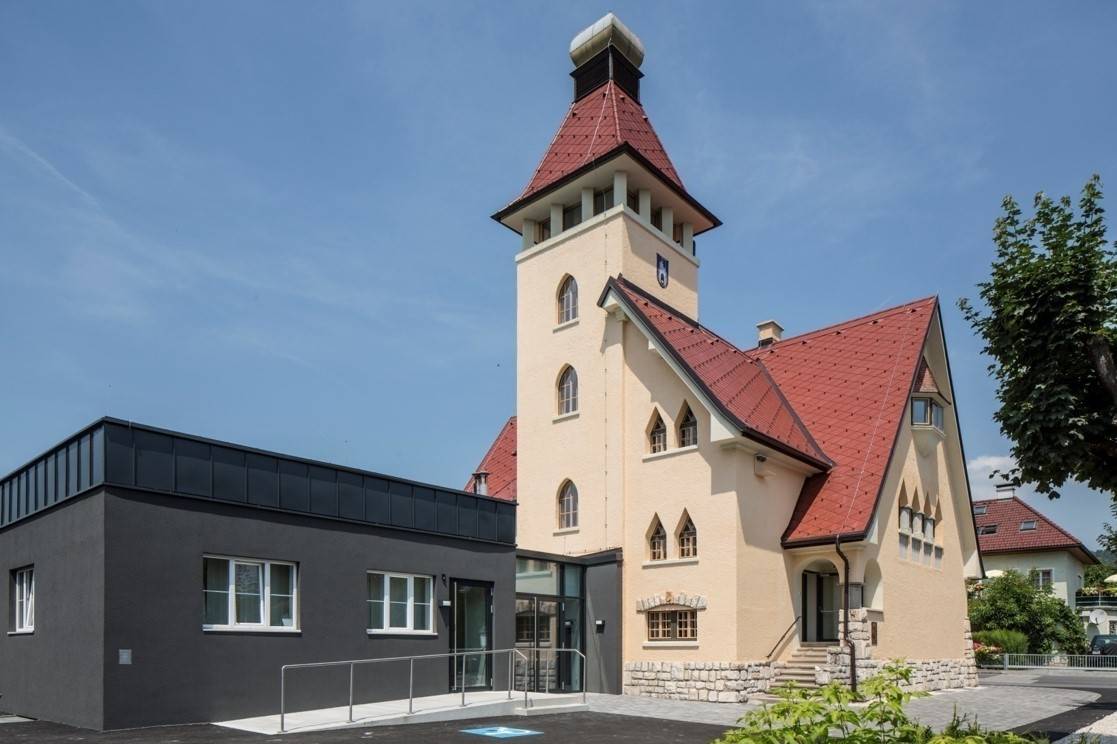
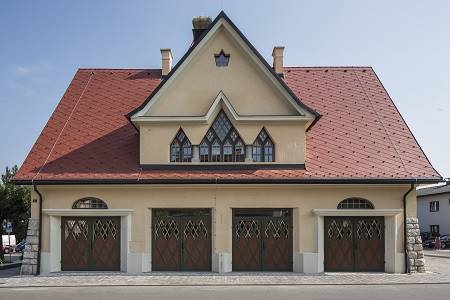
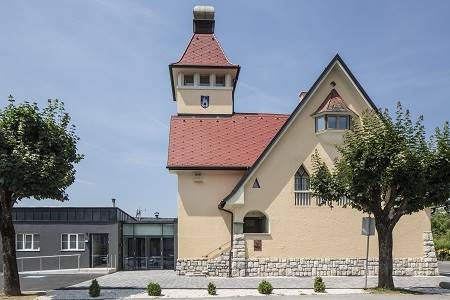
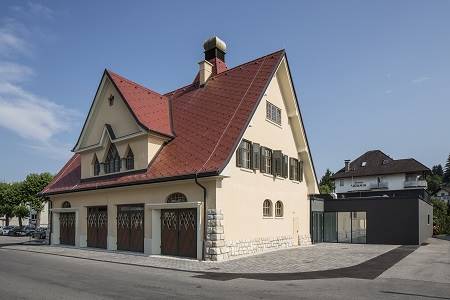
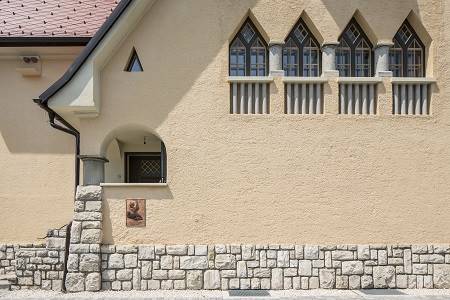
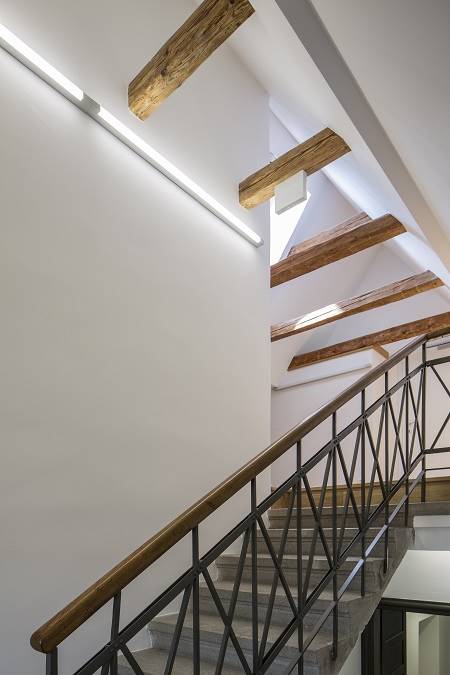
RENOVATION PROCESS
Architecture
BUILDING DESCRIPTION
State of repair
HERITAGE SIGNIFICANCE
Aim of retrofit
Market town of Velden am Wörther See
Seecorso 2, A-9021 Klagenfurt/Wörthersee
Director of music school
Bäckerteichstraße 1, A-9220 Velden am Wörthersee
Arch + more ZT GmbH
Dr. Karl-Renner-Weg 14, A-9220 Velden am Wörthersee
Federal Monuments Authority Austria - Department for Carinthia
Alter Platz 30, A-9020 Klagenfurt am Wörthersee
IPJ Ingenieurbüro P. Jung GmbH
Luftbadgasse 3/8, A-1060 Wien-Mariahilf
Other Blower-door test
RETROFIT SOLUTIONS
External Walls
Außenwand 45
The façade was restored on the outside and adapted to the original colour scheme for reasons of monument protection. On the inside, the thermal renovation was executed with an internal insulation in the form of 8 cm calcium silicate boards, whereby care had to be taken that the existing construction would not suffer any damage in the long term.
The adaptation of the façade to its original condition and the choice of thin insulating panels on the inside of the exterior walls ensured to preserve the original character of the building. Also, Calcium silicate boards were selected as insulation material with regards to protection of historical monuments, ecology and summer overheating protection.
20 mm
400 mm
20 mm
20mm
400 mm
20 mm
80 mm
2 mm
2 mm
Windows
Gate windows
Box-type windows
The window openings could not be changed. The window joints (also the structural joints) of the historic windows were resealed and window seals were milled in. Due to this an air tightness 0.8 1/h could be achieved. Inner wings were replaced with insulating glass. The outer color of the windows was changed to the original one. On the inside at the level of the internal insulation, thermal insulation glazing was installed.
The U-values could only be approximated, since the windows are historic box-type windows that were reworked (single glazing on the outside, inner wing with doulbe glazing, with sealing plane). U-value existing window (frame and glas) about 2,5 W/m²k. U-value new window (frame and glas) about 0,82 W/m²k.
Existing window type | Box-type window |
Existing glazing type | Single |
Existing shading type | NA |
Approximate installation year | 1926 |
New window type | Box-type window |
New glazing type | Double |
New shading type | NA |
New window solar factor g [-] | 0,67 |
The window openings could not be changed. The window joints (also the structural joints) of the historic windows were resealed and window seals were milled in. Due to this an air tightness 0.8 1/h could be achieved. Inner wings were replaced with insulating glass. The outer color of the windows was changed to the original one. On the inside at the level of the internal insulation, thermal insulation glazing was installed.
The U-values could only be approximated, since the windows are historic box-type windows that were reworked (single glazing on the outside, inner wing with doulbe glazing, with sealing plane). U-value existing window (frame and glas) about 2,5 W/m²k. U-value new window (frame and glas) about 1,30 W/m²k.
Existing window type | Box-type window |
Existing glazing type | Single |
Existing shading type | NA |
Approximate installation year | 1926 |
New window type | Box-type window |
New glazing type | Double |
New shading type | NA |
New window solar factor g [-] | 0,54 |
Other interventions
ROOF
GROUND FLOOR
MEASURES TO INCREASE AIRTIGHTNESS
The existing wooden construction doubled to the inside and in order to guarantee the thermal renovation, additional insulation with cellulose was installed on the inside. Furthermore, the existing roof covering was renewed.
The appearance of the roof was kept, but the colour changed to the original. Cellulose was chosen as a insulation material with regards to protection of historical monuments, ecology and summer overheating protection.
5 mm
20 mm
160 mm
5 mm
1 mm
219 mm
300 mm
1 mm
24 mm
25 mm
The existing floor in the event hall without basement and the floor of the existing basement were completely removed and rebuilt with XPS (with Austrian eco-label).
There were no issues with conservation regarding the ground floor.
60 mm
60 mm
120 mm
1 mm
40 mm
20 mm
10 mm
Window joints (including component joints) of the historic windows were resealed and window seals were milled in, and interior sashes were replaced with insulated glass. A possible backflow of the interior insulation was taken into account by completely removing old layers of paint and applying new layers with notched trowel, so that a backflow is kept to a minimum.
HVAC
HEATING
VENTILATION
It was the conversion to 100% renewable district heating, for which proof of delivery was requested. The heat delivery system consists of underfloor heating on the ground floor in the area where the floor structure was redone, and radiators on the upper floors. In addition, a comfort ventilation system (2 units, 1x for the hall and 1x for the classrooms) with heat recovery was implemented.
For the comfort ventilation system, the fresh air intake and exhaust air discharge was carried out via the historic chimneys, as this was not possible on the facade.
New primary heating system | |
---|---|
New system type | District heating |
Fuel | Industrial heat, biomass and gas |
Distribuition system | Radiating floor, radiators and air |
Nominal power | 42 kW |
The building was equipped with two central and one decentralized comfort ventilation system. One unit is located in the attic room above the theory room and supplies the classrooms and the theory room on the 1st floor as well as the classrooms on the top floor. The second unit was installed in the existing technical room and supplies the event hall, the assembly hall and the basement. The decentralised ventilation unit operates the sanitary facilities and is located on its flat roof. Outside air and exhaust air are led over the existing chimneys. Linen sacks on the ceilings of the classrooms ensure an extremely gentle air supply. Heat recovery: Room air technology with variable air volume flow, air exchange rate for air tightness test (n50) = 0.8 1/h, additional air exchange rate (nx) = 0.056 1/h, no heating function, no cooling function, own heat recovery system, degree of heat supply = 80 %, own geothermal heat exchanger, degree of utilization EWT = 20 %. Type of ventilation: no night ventilation, bypass system available, no humidifier, limitation of maximum air volume flow, maximum air volume flow = 2970 m3/h.
The fresh air intake and exhaust air discharge was carried out via the historic chimneys, as this was not possible on the historic facade.
Original roof build-up | New ventilation system |
---|---|
Type ventilation system | 2 centralised and 1 decentraliced systems |
Type flow regime | Overflow |
Heat recovery | Yes |
Humitidy recovery | No |
Nominal power | No information kW |
Electric power | kW |
Control system | Air exchange takes place according to air tightness test (n50) = 0.8 1/h |
RENEWABLE ENERGY SYSTEMS
Photovoltaic
The new PV is situated on a part of the buiding with a flat roof. The average yield of the PV system is about 10,000 kWh per year, of which about 40% is consumed in the renovated building and the remaining electricity is passed on to the neighboring doctor's office.
The PV was installed on the part of the building, which is not under conservation.
Photovoltaic System | |
---|---|
Type | NA |
Collector area | 80,0 m² |
Total nominal power | 10,0 kW |
Overall yearly production | 9600,0 kWh |
Energy Efficiency
Voluntary certificates: The klimaactive gold award for competence in climate protection for the renovation of the music school Velden states that his building combines highest energetic and ecological quality with professional execution and thus meets the building standard of klinaaktiv gold.
Consumption_estimation_Calculation_method: Calculation according to energy certificate for site climate
Consumption_estimation_Before: 418,05 kWh/m2.y
Consumption_estimation_After: 27,24 kWh/m2.y
Primary Energy
Consumption_estimation_Calculation_method: Calculation according to energy certificate for site climate
Consumption_estimation_Including_DHW: Yes
Consumption_estimation_Before: 856,2 kWh/m2.y
Consumption_estimation_After: 247,4 kWh/m2.y
Type_of_monitoring: Continuous
Description: Two classrooms were monitored according to their climate (temperature) during summer.
External Climate
Type_of_monitoring: Continuous
Internal Climate
There is an ongoing exchange with the users in which the building is optimized, also the temperature. This is especially necessary in the case of a high-quality refurbishment, as not everything can work at the start of operation and thus an ongoing evaluation is necessary to achieve user satisfaction.
There were many constructive discussions with the future users of the music school during the planning phase regarding user comfort. Especially the resulting air supply via air bags works very well. The feedback from the users, especially regarding ventilation and sound insulation, is very positive.
The window openings could not be changed, therfore, the lighting system inside was designed to be daylight-dependent.
Since the building is used as a music school , sound decoupling between classrooms and room acoustics through the installation of individual elements (additional Plexiglas suspension, Ecophon tw. on walls) were important.
Costs
Investment costs applied for: € 1,460,826. Environmentally relevant costs: € 937,001. Funding basis: € 661,584. Subsidies: € 283,858.
€ 1.460.826,00 (total)
No
Environment
emissions_at_use_stage_before_intervention: NA NA
emissions_at_use_stage_after_intervention: 31.40 kg/m²y per m2
emissions_before_use: 48,.40 kg/m²y