Freihof Sulz
Schützenstraße 14
6832
Sulz, Austria
Architect
Owner
User
Contact Details
Other Information
Restaurant and events at Freihof Sulz, Schützenstraße 14, A-6832 Sulz
https://nachhaltigwirtschaften.at/de/hdz/projekte/sanierung-oekologischer-freihof-sulz.php
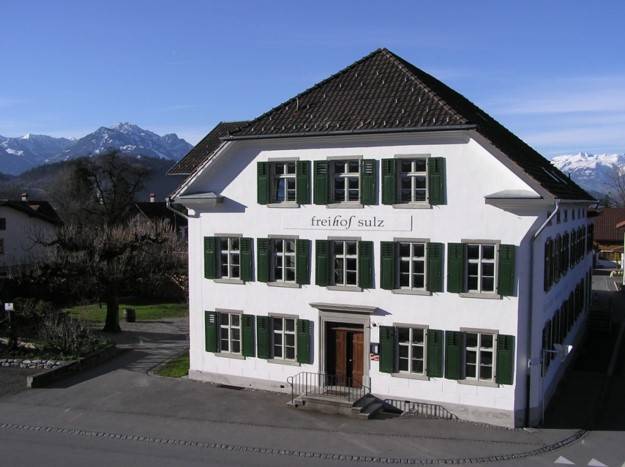
Climate Zone feuchtes und warmes Kontinentalklima Dfb
Altitude 502 m a.s.l.
HDD 3681
CDD 63
Conservation Area:
No
Level of Protection:
Bescheid
Year of last renovation:
2006
Year of previous renovation:
1900
Secondary use:
Wholesale & Retail
Building occupancy:
Permanently occupied
Number of occupants/users:
20
Building typology:
Detached house
Number of floors:
3
Basement yes/no:
Yes
Number of heated floors:
3
Gross floor area [m²]:
1034,0
Thermal envelope area [m²]:
1549,0
Volume [m³]:
3,103
NFA calculation method:
NGF (de)
External finish:
Rendered
Internal finish:
Wood panelling
Roof type:
Pitched roof
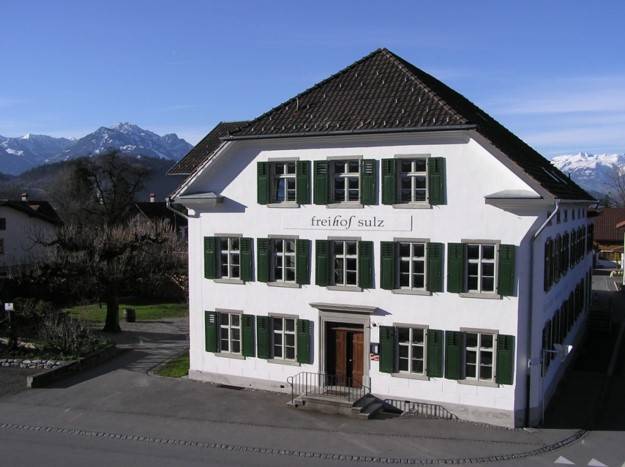
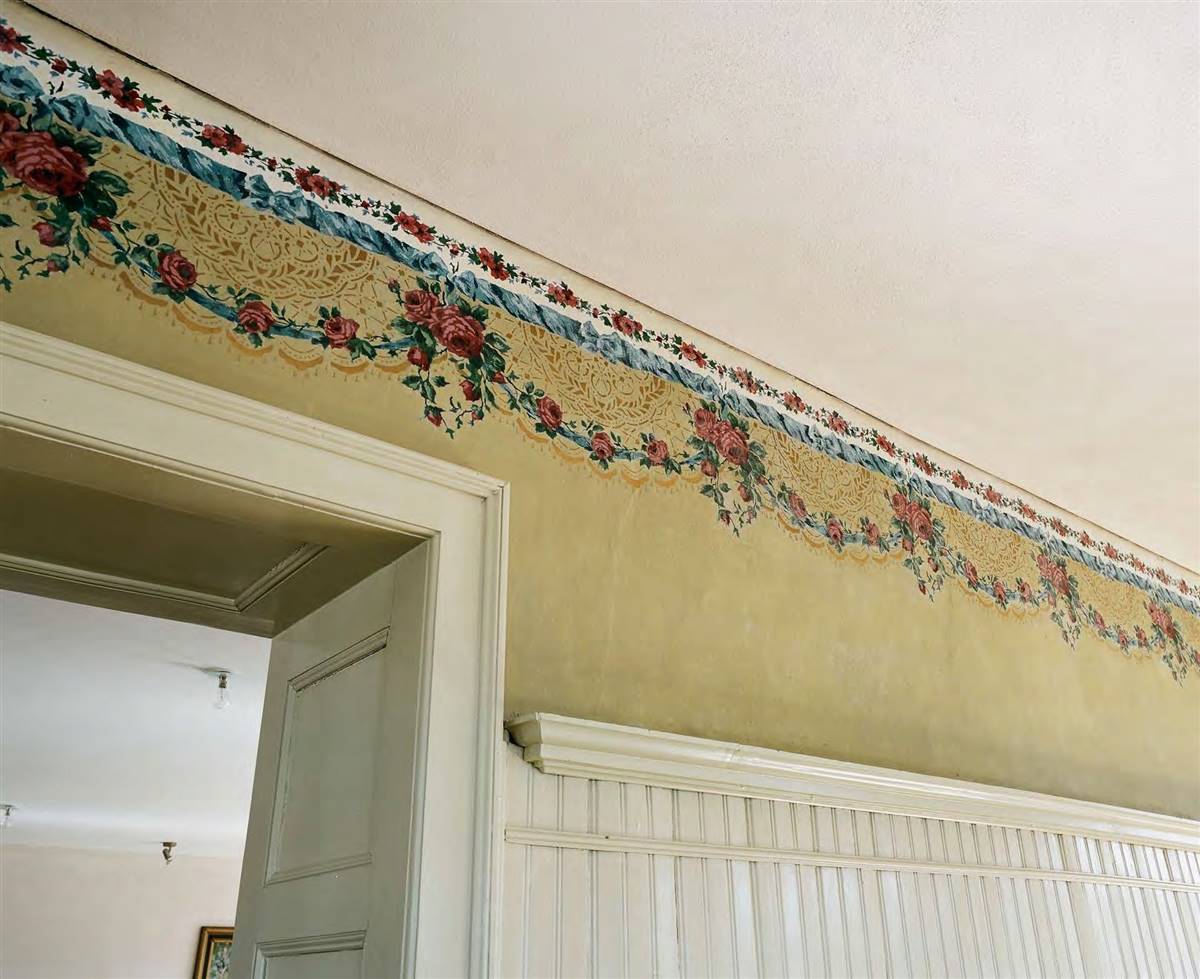
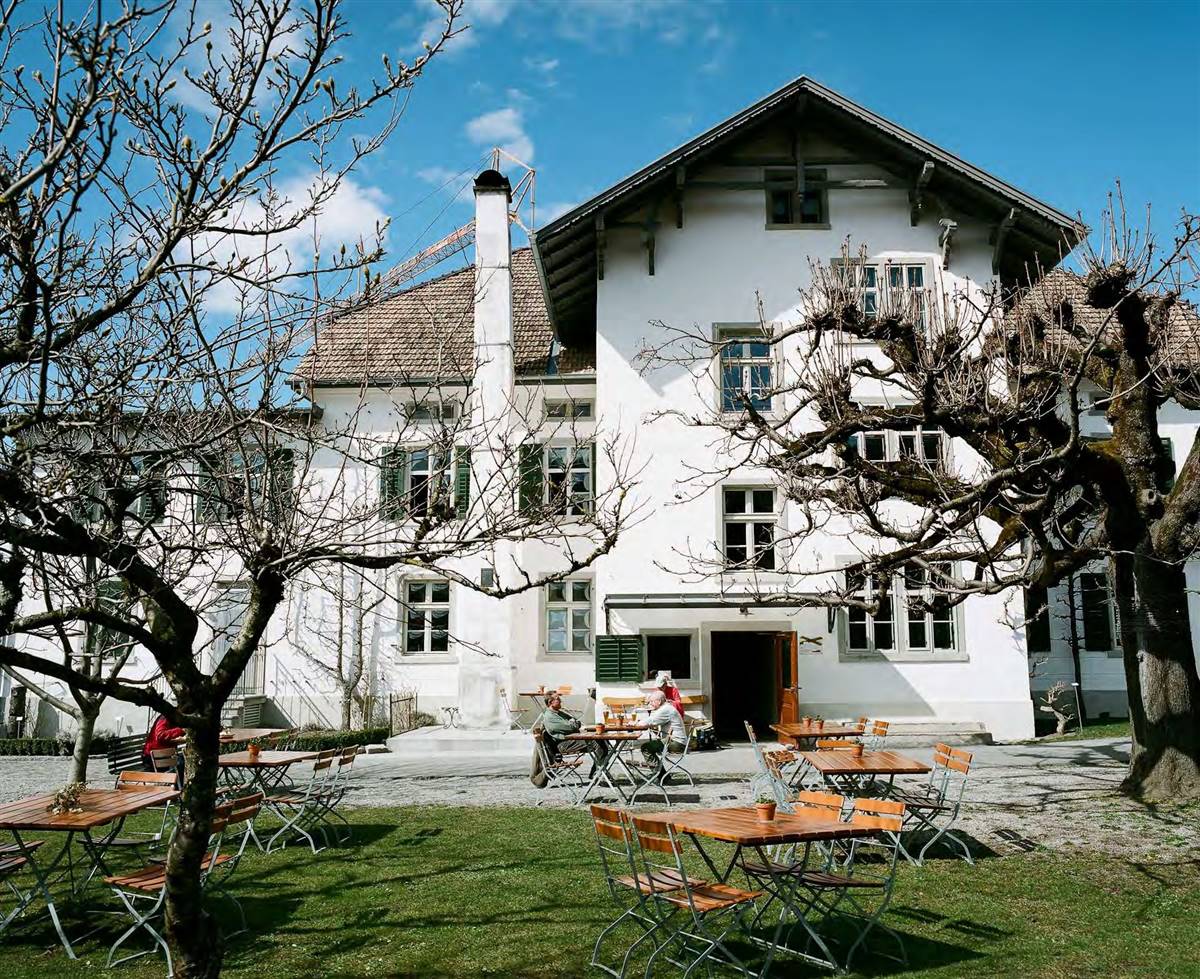
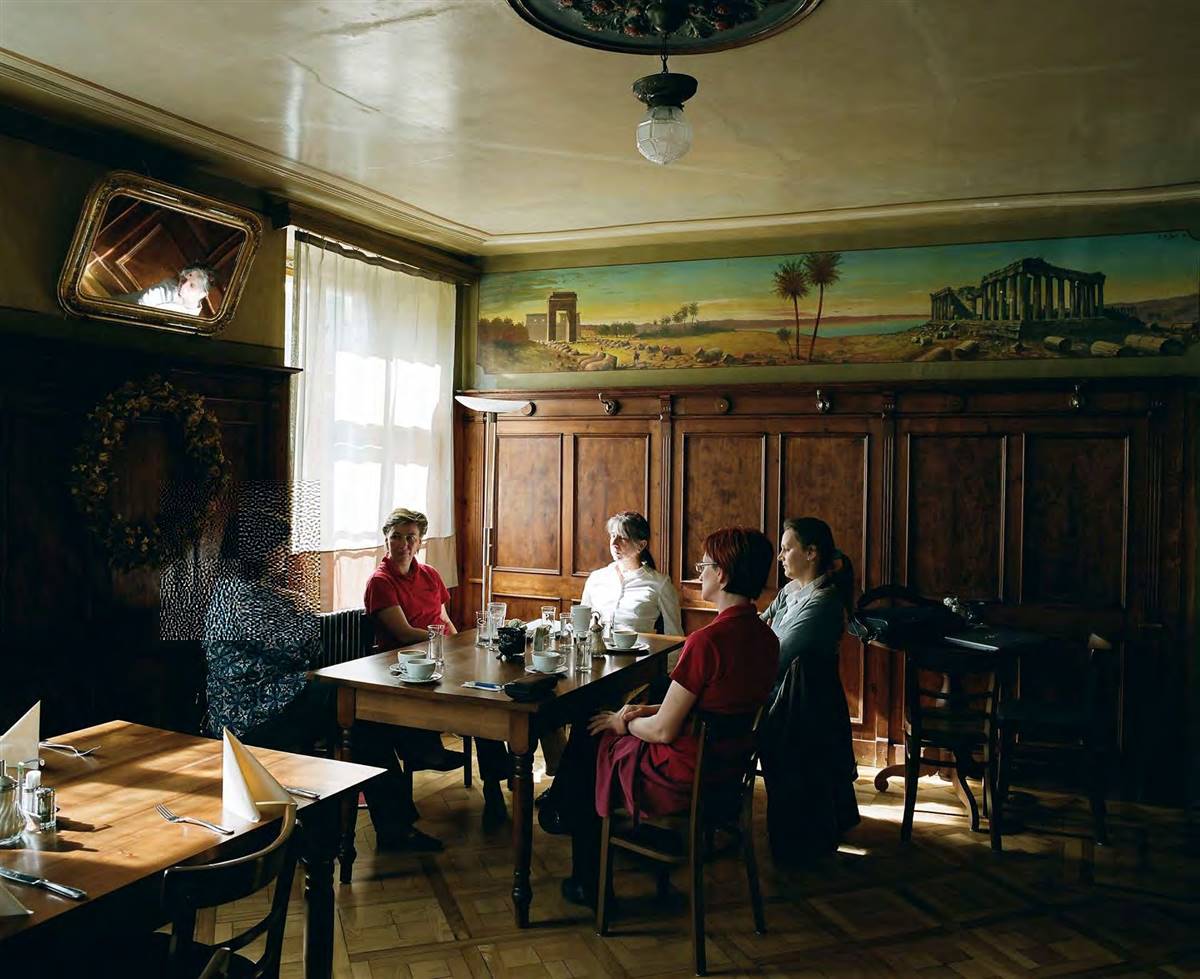
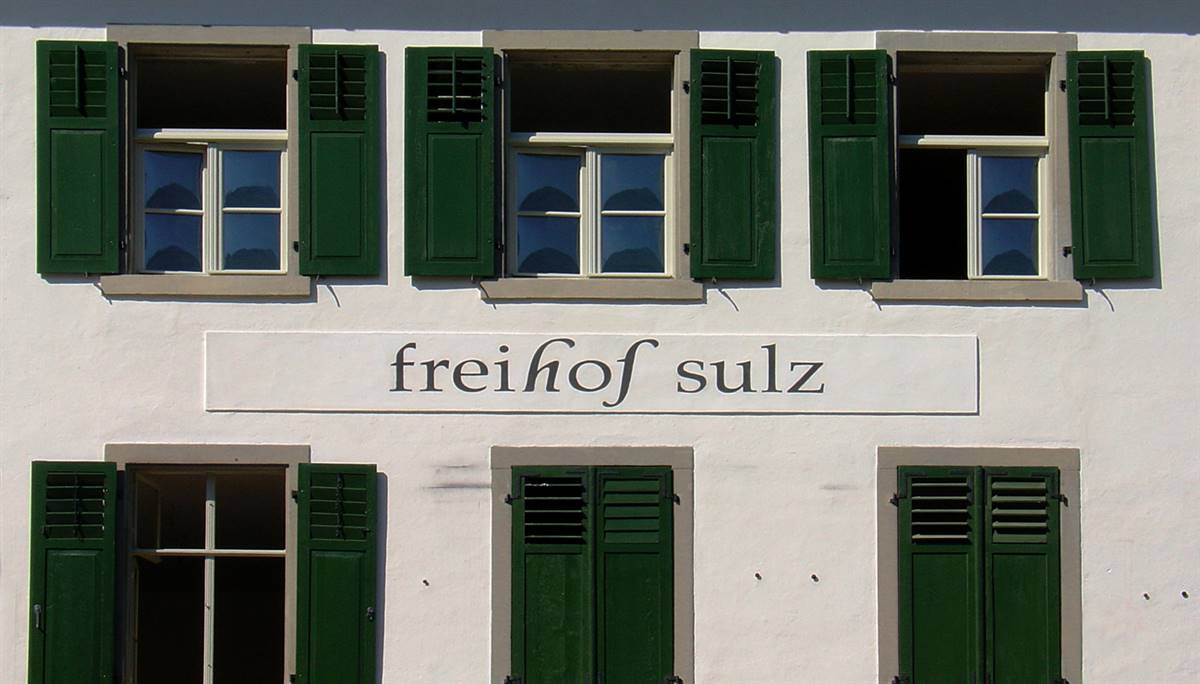
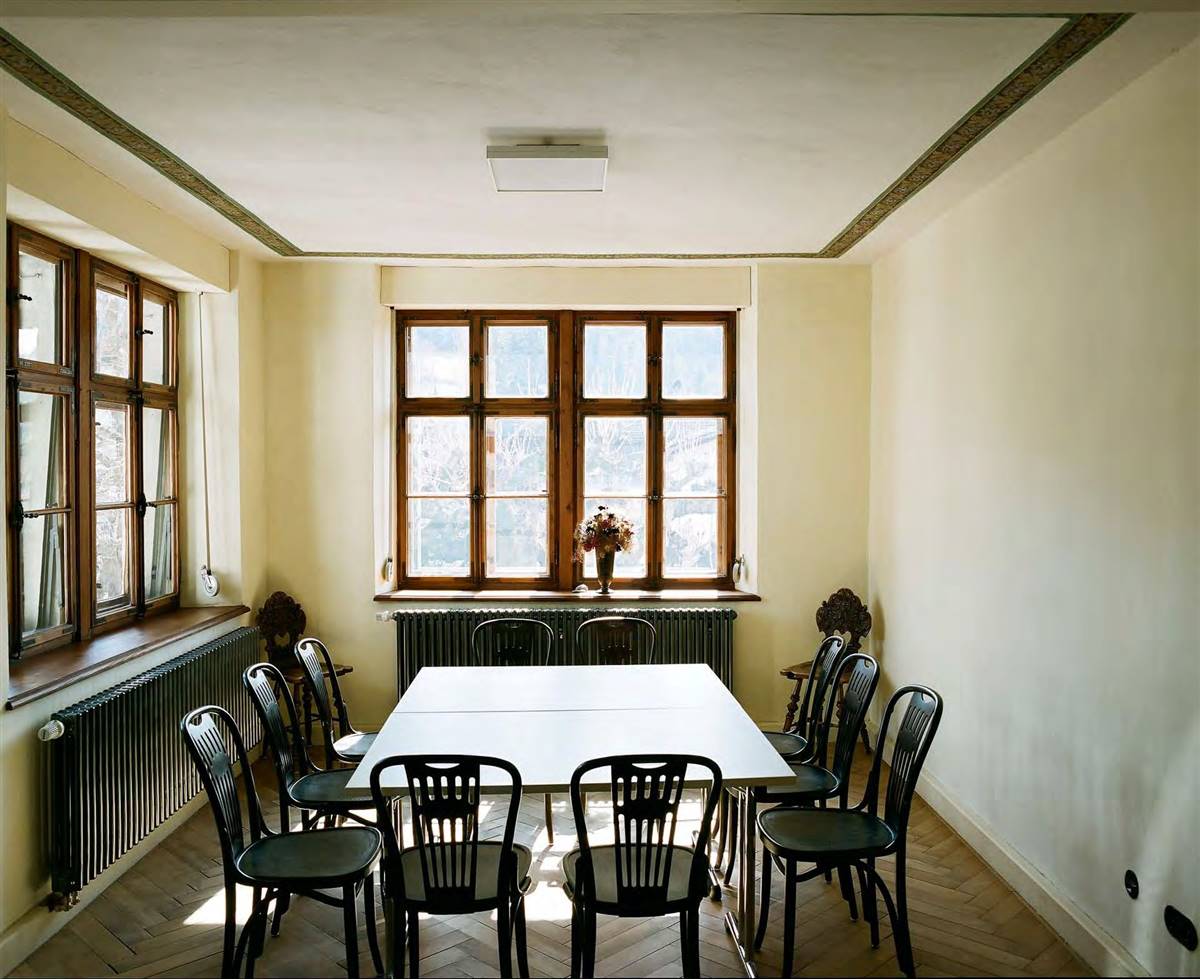
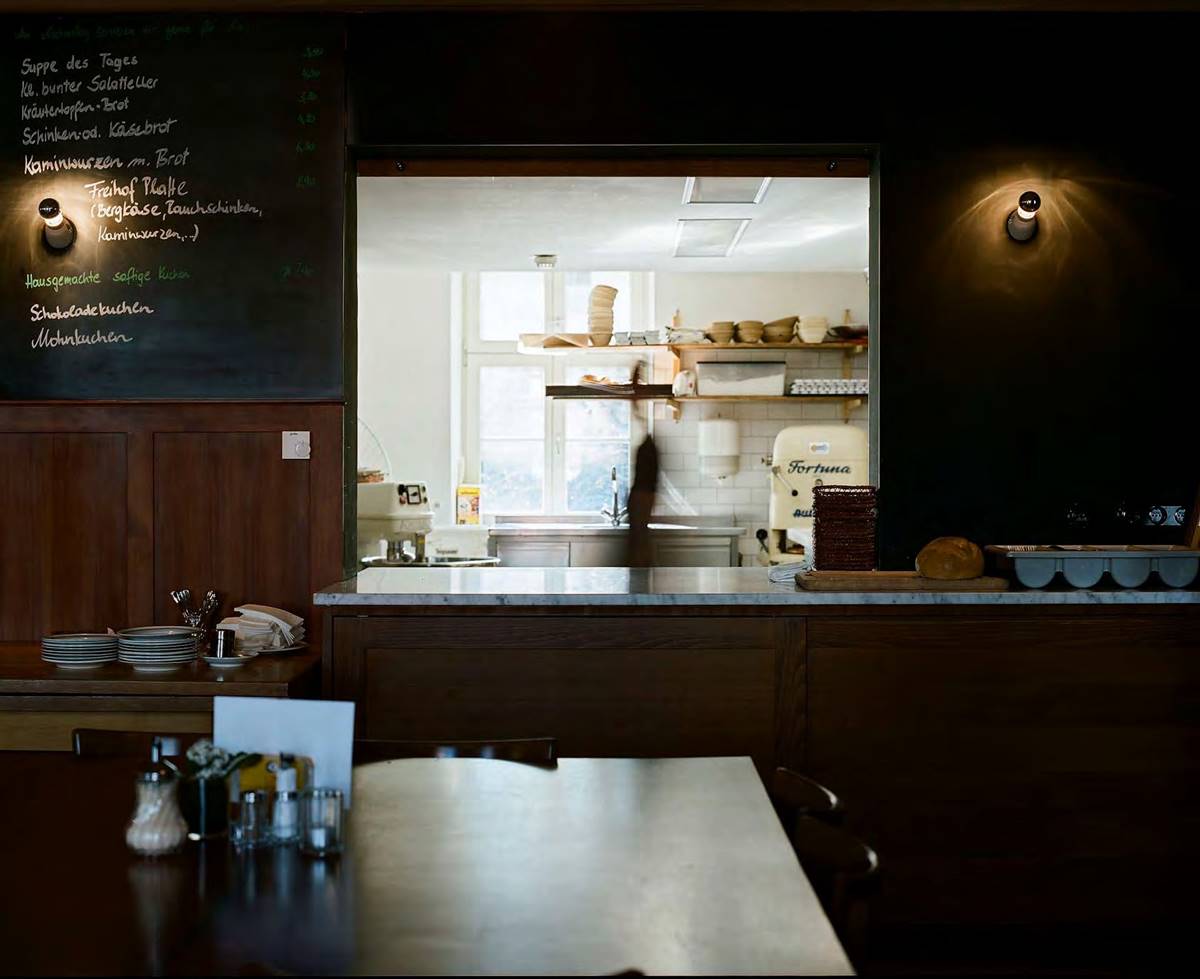
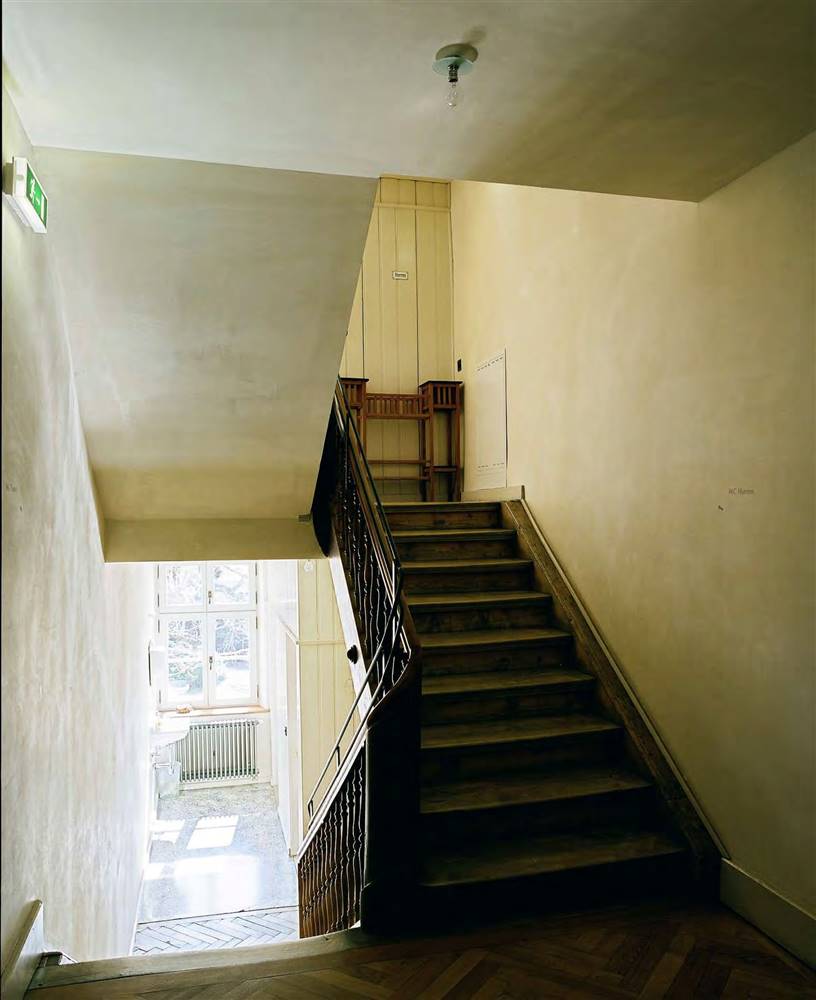
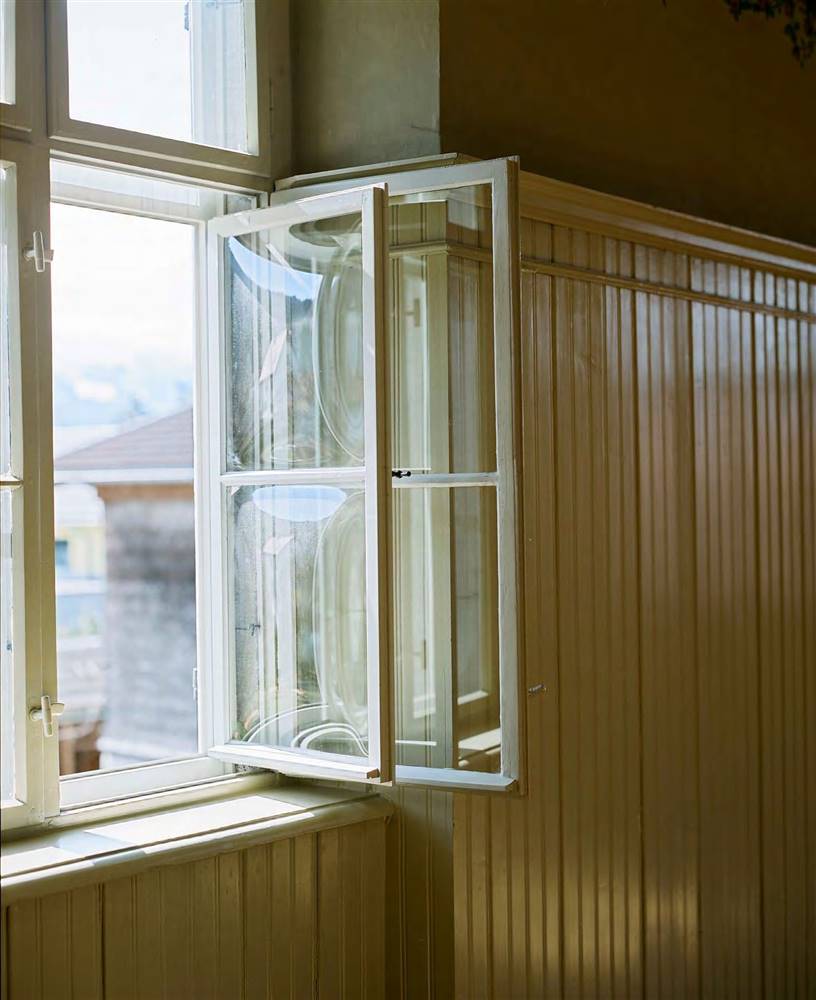
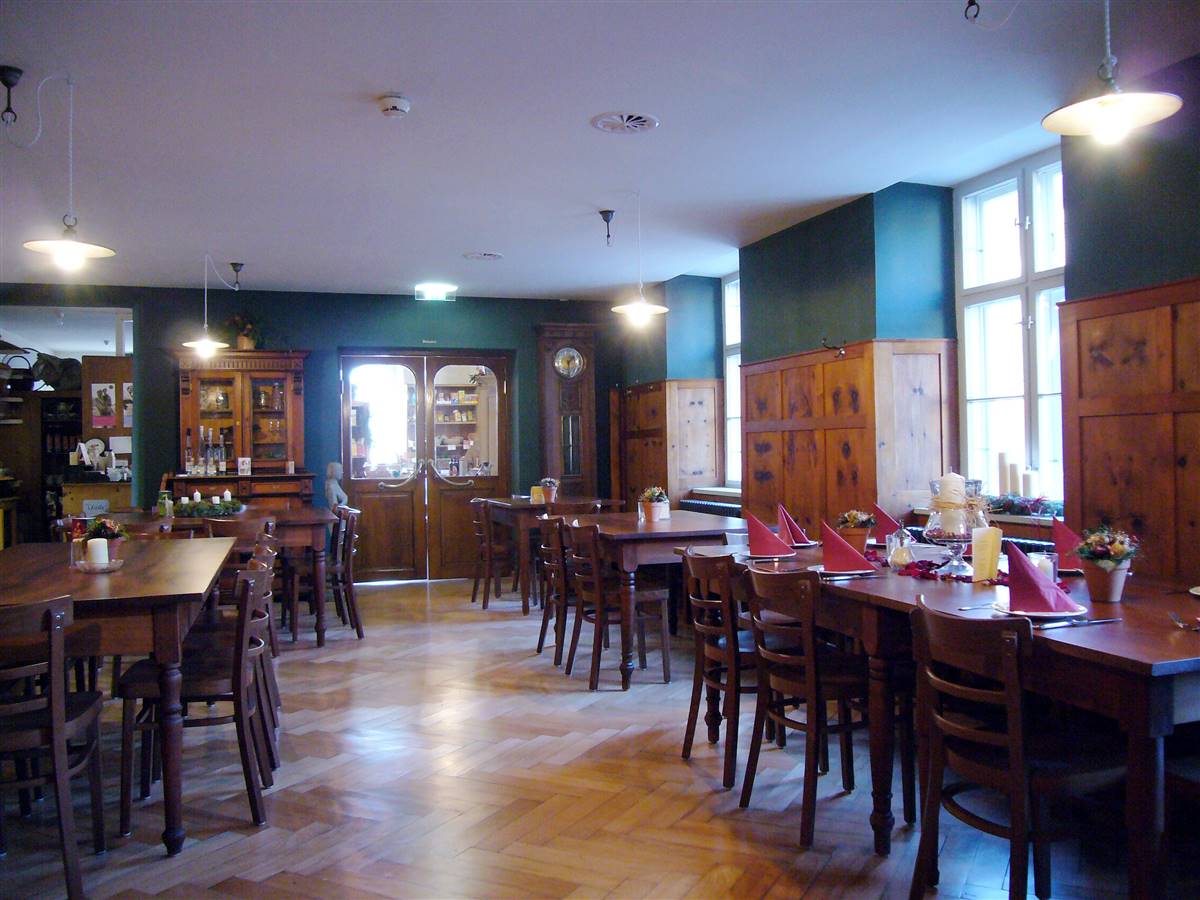
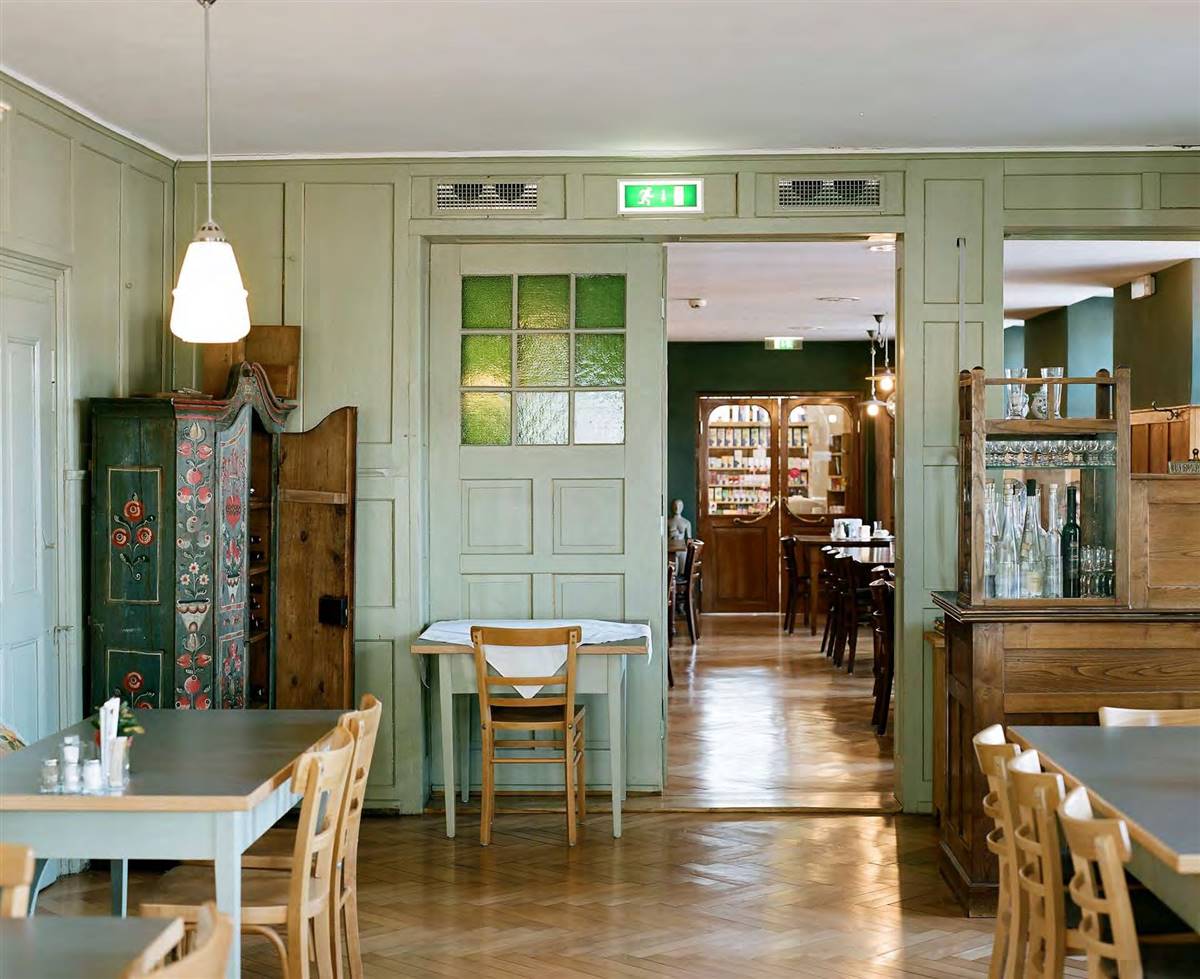
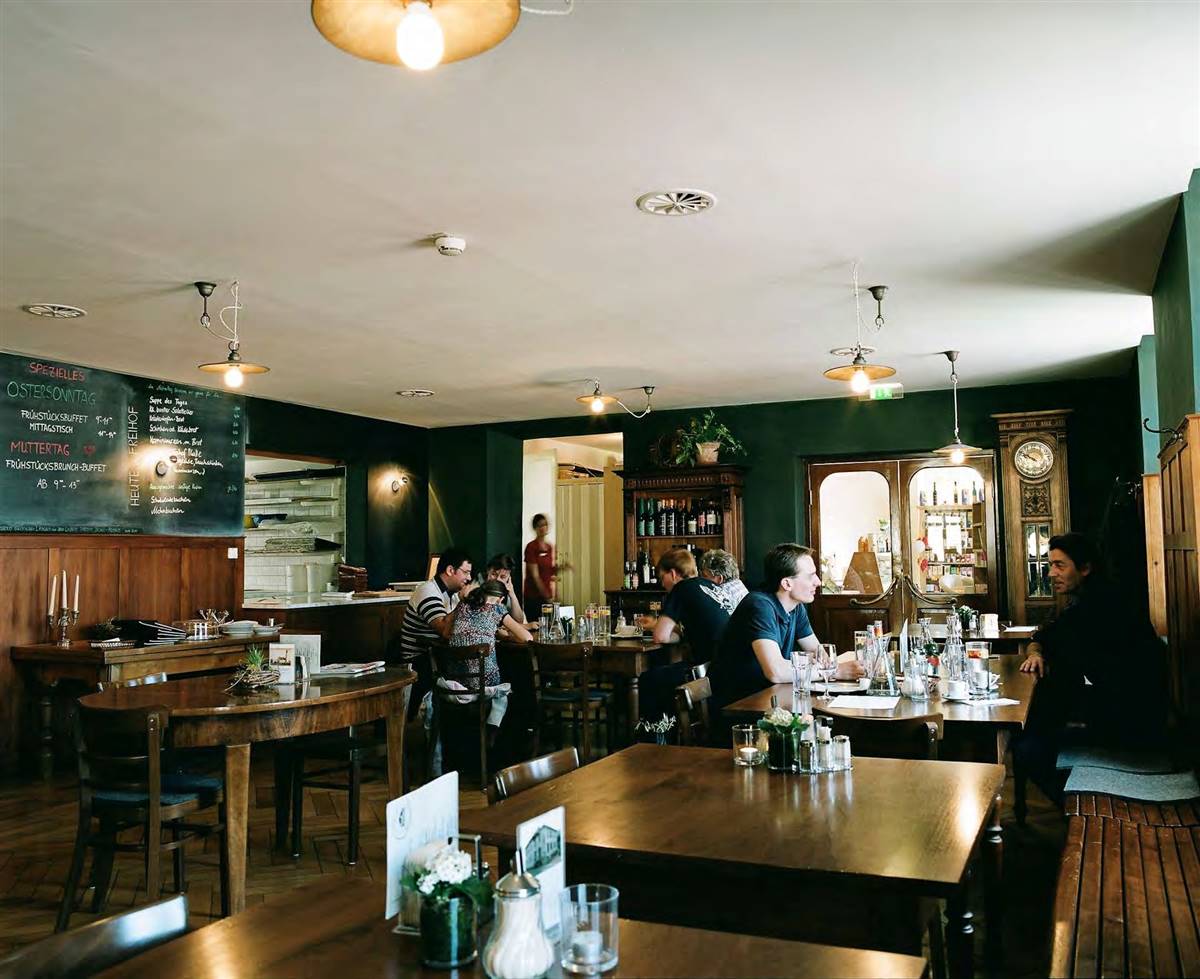
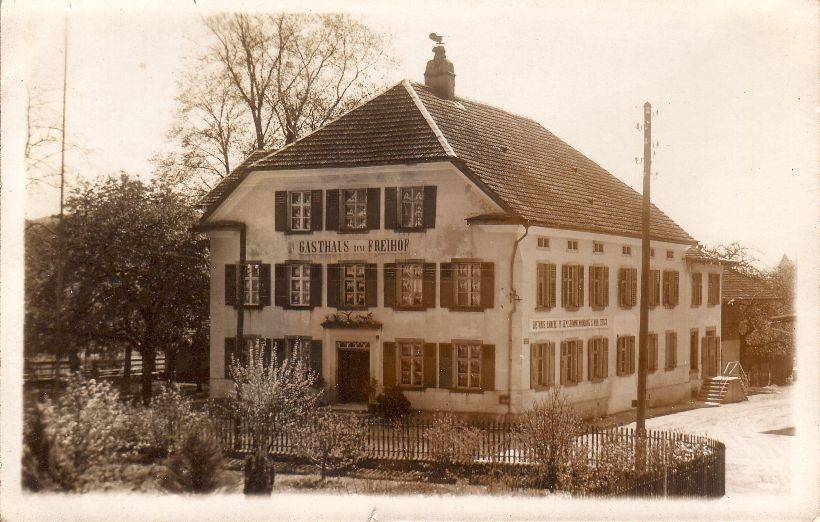
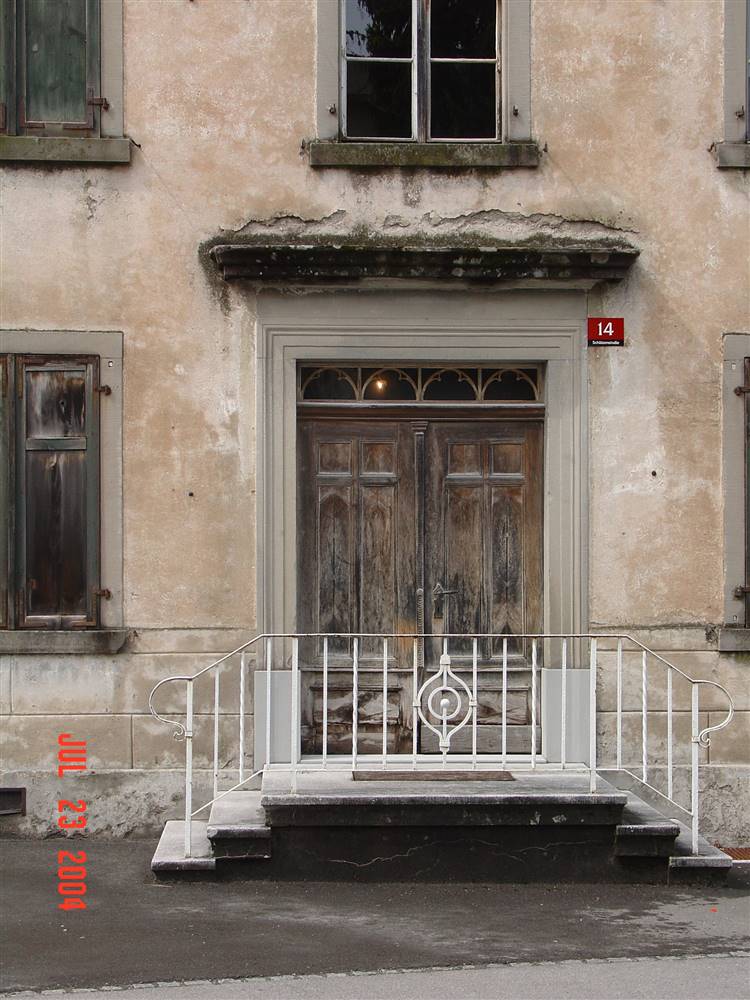
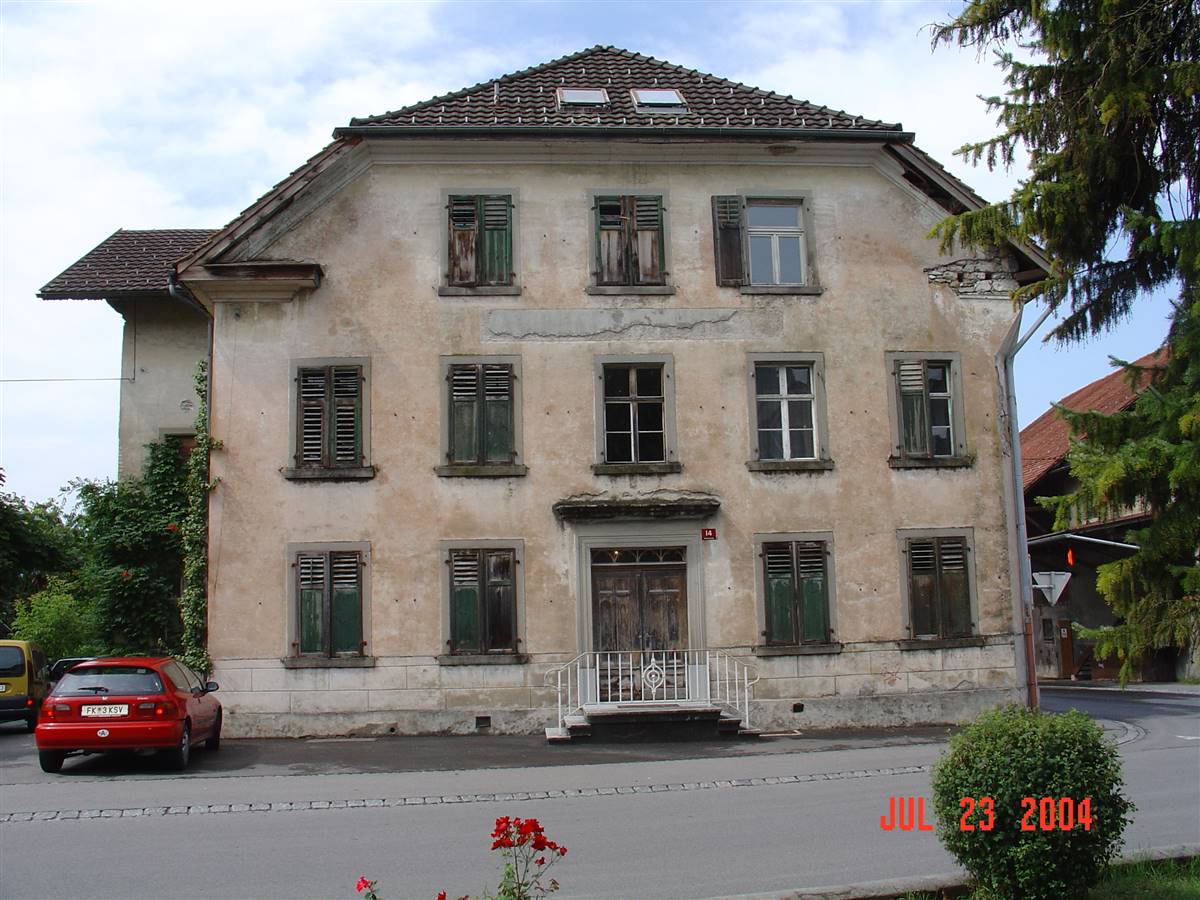
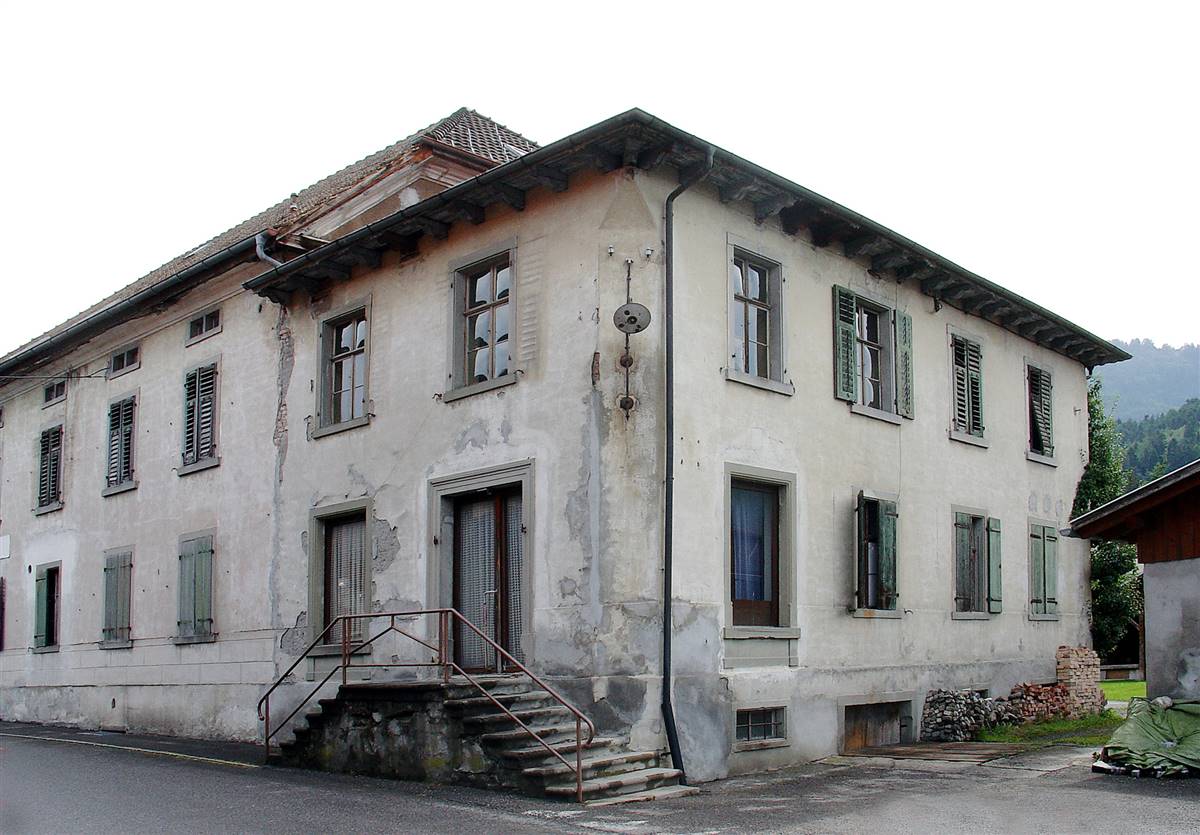
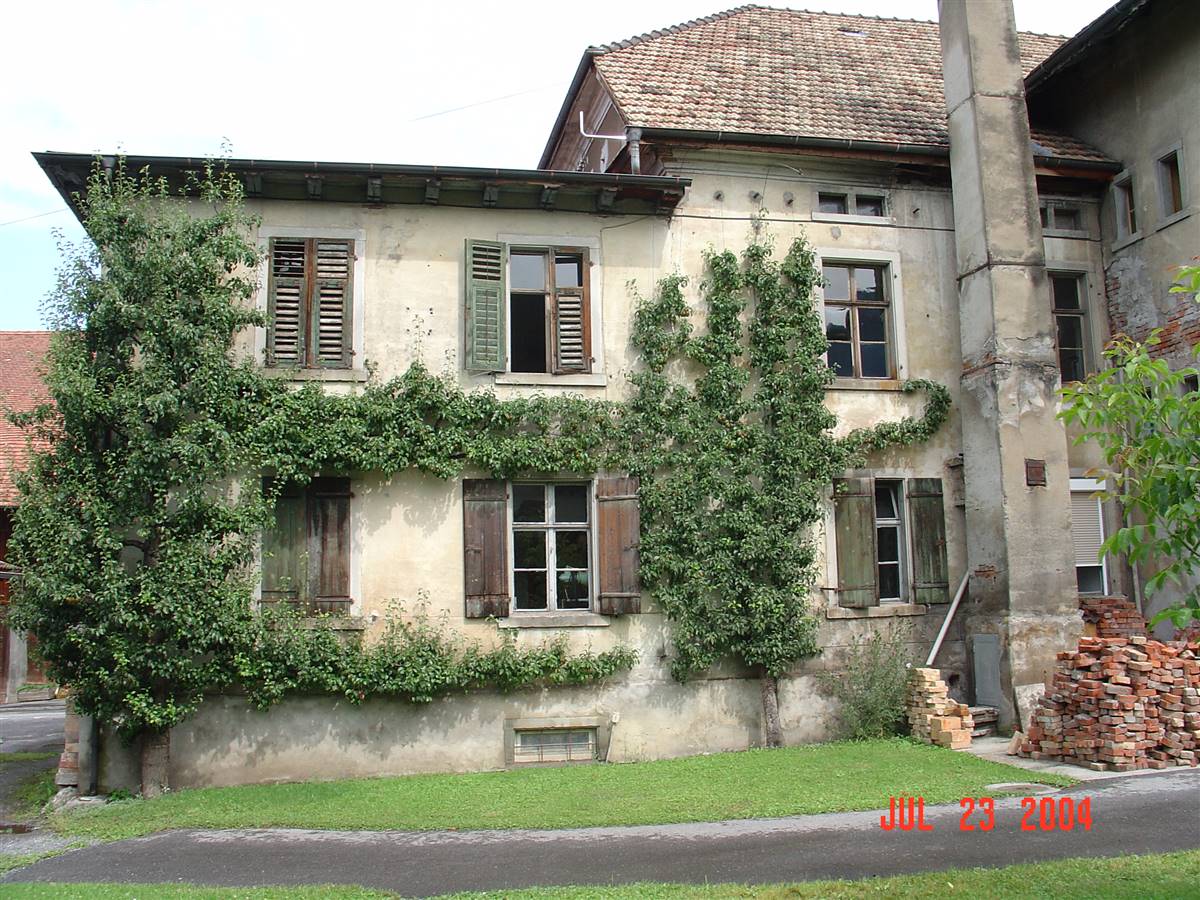
RENOVATION PROCESS
Architecture
BUILDING DESCRIPTION
State of repair
HERITAGE SIGNIFICANCE
Aim of retrofit
Wohnbauförderung Land Vorarlberg
Landhaus, 6901 Bregenz
Energieinstitut Vorarlberg, BM Harald Gmeiner
Stadtstr.33 6850 Dornbirn
DI Dr. Andrea Sonderegger
Oberfeldgasse 14, 6922 Wolfurt
Arch. DI Beate Nadler-Kopf
Eisplatzstraße 1-1a A 6845 Hohenems
nadler-kopf@aon.at
DI. Mag. Barbara Keiler
Amtsplatz 1 6900 Bregenz
vorarlberg@bda.gv.at
Gebhard Bertsch
Dorfstrasse 192 A-6713 Ludesch
Gebhard Bertsch
Dorfstrasse 192 A-6713 Ludesch
DI Dr. Karl Torghele
Lustenauerstraße 64 6850 Dornbirn
Mag. Martin Rauch
Quadernstrasse 7, 6824 Schlins, Österreich
Hygrothermal assessment Bauphysikalisches Gutachten zu den Bauteilaufbauten
Life Cycle Analysis (LCA) Produktdeklarationsdatenbank „ÖBOX“ und die Kriterien der Vorarlberger Wohnbauförderung für den Gebäudeausweis
RETROFIT SOLUTIONS
External Walls
Natural stone wall with internal islation and internal plastering
The exterior walls, which did not have any plaster or paintings worthy of preservation on the inside, were insulated on the inside and a new plaster was applied. Except for two rooms, it was possible to install interior insulation in the plastered rooms everywhere. The rooms with interior wood panelling worth preserving were not insulated. The interior insulation was made with sustainable material wood fibre. To avoid possible later damage to the wooden beams in the natural stone masonry, the insulation thickness of the interior insulation had to be reduced on 6 cm. The insulation was pulled up over the ceiling. Where the ceiling was still ok, the edge area was cut open so that the insulation could be installed. The window reveals were insulated from the inside as shown in the picture on the left. The interior plaster was executed with lime.
The external appearance of the building was preserved, thus preserving the elements worthy of preservation. No interior insulation was applied to the interior panelling and paintings worthy of preservation, like the painting in the "Rosensaal"
30 mm
620 mm
10 mm
30mm
620 mm
60 mm
10 mm
Windows
cambered box-type windows in the groundfloor
New thermal insulation glazing and frames in kitchen and 2 upper floors
On the ground floor, where possible, the well preserved cambered windows have been retained. These are box-type windows with curved panes on the outside, which both open inner wards. Inside there is normal single glazing.
Due to the protection of historical monuments and well preserved cambered windows, the decision was made to retain the box-type windows. Repaired and replaced using old wood material parts that were rotten, fell off or were infested with pests. New wood was used for large damaged areas. Holes were filled in, irregularities were sandpapered or puttyled. Old varnish was sanded off, the oil rubbed off with spirit. The windows were glazed out, the old putty was removed. With a special tool, only loose spots were sanded and then patched because otherwise, the paint would not have adhered. Afterwards, they puttied with linseed oil putty. The renewed glass was coated with a low-E coating. Partly the glass was re-glazed. In the listed rooms on the ground floor, the old cambered glass was used. The fittings were rubbed off and after a function check they were lubricated and set up. Windows were partly machined at the bottom with a planing machine to ensure tightness. Glazing was done without silicone, instead, oil glue putty was applied with a spatula. Weather shanks were removed and new ones made of larch wood were fitted. For sealing, sheep's wool was stuffed from the outside and grouted with acrylic. Inside, the carpenter sanded, puttyled and patched the frames and checked and reattached the fittings. In some cases, holes had to be drilled on the sides and the frames screwed to the masonry. Shutters are designed to match the sunlight. Depending on the floor, direction and use, the shutters are partly closed at the bottom and are equipped with fixed slats or adjustable slats for display. Shutters were partly in very bad condition. They were also repaired as described above.
Existing window type | Box-type window |
Existing glazing type | two single glazings as box-type windows |
Existing shading type | Outer shutter |
Approximate installation year | 1900 |
New window type | Box-type window |
New glazing type | two single glazings as box-type windows with low-e |
New shading type | Outer shutter |
New window solar factor g [-] | 0,7 |
The existing box-type windows on the first and second floors and in the kitchen were replaced by thermal insulation glazing. The existing historical windows in good condition were installed on the ground floor. The second picture on the right shows the old window.
In order to make the windows look similar, the outer glazing was also designed with a camber, just like the original. The thermal insulation glazing was installed in new wooden frames, which were inspired by the old ones, but are no longer box-type windows.
Existing window type | Box-type window |
Existing glazing type | two single glazings as box-type windows |
Existing shading type | Outer shutter |
Approximate installation year | 1900 |
New window type | Double window |
New glazing type | Double |
New shading type | Outer shutter |
New window solar factor g [-] | 0,65 |
Other interventions
OTHER
MEASURES TO INCREASE AIRTIGHTNESS
Windproof connections of the masonry to the window frames were implemented. The joint between sandstone and window frame was sealed with acrylic, sheep's wool and lime plaster. The historic box-type window was repaired by carpentry work, thus increasing the airtightness.
HVAC
HEATING
VENTILATION
DOMESTIC HOT WATER
The old heating system with tiled stoves was supplemented with a pellet heating system and solar heating in the adjacent building. A pellet heating system with 110 kW heating capacity from Fröhling was installed in the adjacent building. The situation in the main house was not realized for the following reasons: Use of the rooms for other purposes, partly rooms were too low, main reason: no chimney available, outside chimney on the facade did not fit to the object.
Ceiling heating in the Rosensaal and partly wall heating and also radiators. The main reason for the ceiling heating is that walls and floors are in good condition and only the ceiling needed to be renewed. Bread is baked every day. The radiant heat of the oven contributes significantly to heating the ground floor, the staircase and the Rosensaal foyer above the oven. The waste heat from the exhaust air of the baking oven is fed into the heat recovery of the ventilation system and used for heating purposes.
New primary heating system | New secondary heating system | |
---|---|---|
New system type | Condensing | Stove |
Fuel | Biomass | Biomass |
Distribuition system | Radiating ceiling | direkt, Kachelofen, Backofen |
Nominal power | 110 kW | 5 kW |
Ventilation system for the kitchen, the restaurant and the dining room: 3850m³ nominal air output with heating register 19 kW, with heat recovery by cross-flow heat exchanger for dining room and restaurant.
The ventilation system is installed in the basement. The exhaust air is discharged via an exhaust chimney in the adjacent building so that there are no visible elements on the outside of the main building.
Original roof build-up | New ventilation system |
---|---|
Type ventilation system | Centralized |
Type flow regime | Cascade |
Heat recovery | Yes |
Humitidy recovery | No |
Nominal power | 19 kW |
Electric power | 1,7 kW |
Control system | Die Bedienung der Lüftungsanlage erfolgt über einen zentralen Steuer- und Regelschrank. Sämtliche Anlagenfunktionen werden über eine DDC–Regelung überwacht und gesteuert. Für die Bedienung steht ein Fernbedientableau in der Küche zur Verfügung. |
Domestic hot water is also produced by pellet heating and solar thermal energy. It is delivered via decentral heat exchanger stations.
Pellet heating and solar thermal energy in the adjacent building.
New DHW system | |
---|---|
Type | with heating system |
Hot_water_tank | Yes |
With heat recovery | No |
RENEWABLE ENERGY SYSTEMS
SolarThermal
Biomass
On the adjacent building, 56m² of Doma Flach solar collectors were integrated into the existing roof. The energy is stored in 4400l buffer storage with integrated stainless steel tanks. The solar collectors are mainly used for domestic water heating in summer and partial solar space heating. Due to the low-temperature heating system, energy from the solar system is used in the heating system during the transition period. The additional heating is provided by the pellet stove as required.
The plant is not visible from the access road and is located on the adjacent building.
SolarThermal System | |
---|---|
Type | Flat collector |
Collector area | 56,0 m² |
Elevation angle | 20,0 |
Azimuth | 45,0 |
Overall yearly production | 15500,0 kWh |
DHW contribuition | 8500,0 kWh |
Cooling contribuition | 0,0 kWh |
Energy Efficiency
Voluntary certificates: No
Consumption_estimation_Before: 167 kWh/m2.y
Consumption_estimation_After: 55,77 kWh/m2.y
Primary Energy
Consumption_estimation_Calculation_method: NA
Consumption_estimation_Including_DHW: No
Type_of_monitoring: Punctual
Description: Thermography
Internal Climate
A resident during the interview: "Walking through the Freihof, you can still feel the life of our ancestors. The history of the house comes alive. The revitalisation of the house through an inn-restaurant, organic food shop, health shop, seminar rooms and various therapists are the absolutely right concept for this traditional place. I feel very comfortable in my shop. When deciding on the location, the ecological orientation of the house, the great range of rooms, the opportunities to meet the Freihof guests, as well as the possibilities for cooperation with colleagues from the health and consulting sector were decisive for me".
Costs
In general, it can be concluded that additional costs have arisen due to structural adjustments, technical upgrades and official requirements. The ecological choice of materials was of secondary importance in monetary terms. The optimisation is the basis of the detailed planning and the ecological tender. In addition to material and construction optimisations, findings from the HdZ demo project "Restoration in protected areas" were used for the preparation of ecological tenders, which also made it possible to use ecological and possibly more expensive building materials in line with the "best bidder principle". Additional costs for ecological material selection, energy-saving Construction and building services resulted in 373,876 €.
4000 € Pellet für Heizung und Warmwasser (2019, netto) (total)
(includes DHW) Yes
Annual electricity cost
800 € Stromkosten, nach Nachrüsten einer PV-Anlage 200 € (total)
Lifecycle cost
No
Environment