Maison Rubens
rue Rubens 92
1030
Schaerbeek, Belgique
Owner
User
Contact Details
Other Information
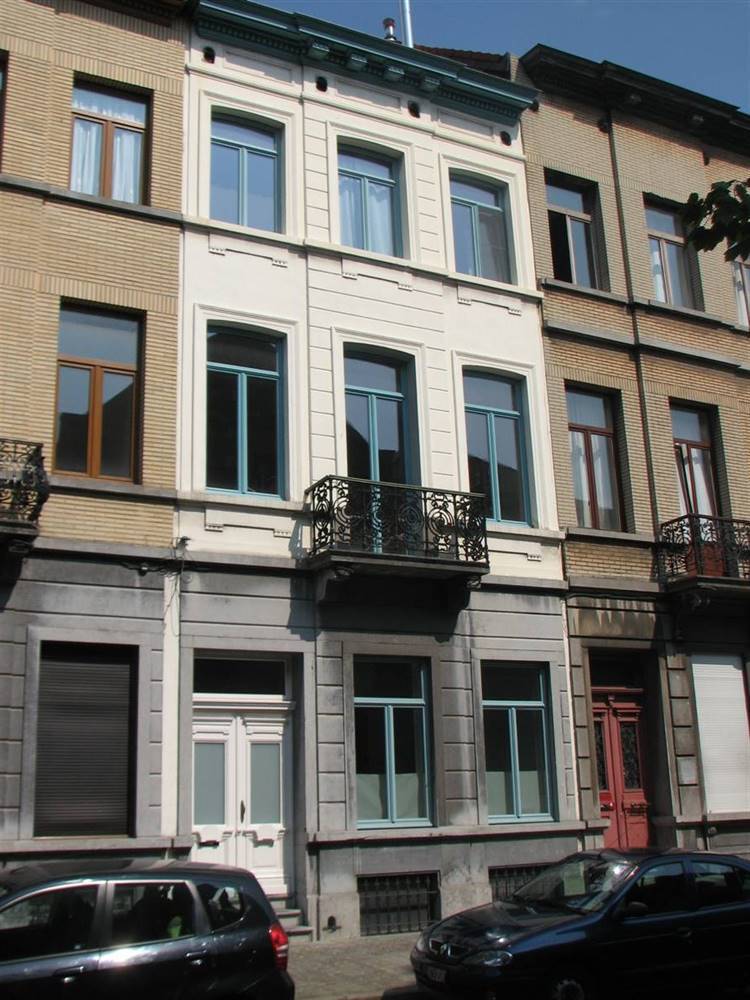
Climate Zone Cfc
Altitude 30
HDD 5
CDD 1
Conservation Area:
No
Level of Protection:
NA
Year of last renovation:
2008
Year of previous renovation:
2008
Secondary use:
Offices
Building occupancy:
Permanently occupied
Number of occupants/users:
4
Building typology:
Terraced
Number of floors:
3
Basement yes/no:
Oui
Number of heated floors:
4
Thermal envelope area [m²]:
373,06
Volume [m³]:
794,83
NFA calculation method:
SHON (fr)
External finish:
Rendered
Internal finish:
Plastered (on hard)
Roof type:
Pitched roof
RENOVATION PROCESS
Architecture
BUILDING DESCRIPTION
State of repair
HERITAGE SIGNIFICANCE
Aim of retrofit
Bruxelles environnement
Avenue du Port 86C 3000 B-1000 Bruxelles
EcoRce
Rue de Fragnée 67A, 4000 Liège
Hygrothermal assessment no
Life Cycle Analysis (LCA) no
RETROFIT SOLUTIONS
External Walls
Front facade
Rear Facade
Front façade Inside: partial Internal insulation to keep the stucco ornamentations (moldings on the ceiling and moldings cornice marks)
In order to keep the aspect of the front façade the insulation is from the inside but to conserve the wall and stucco (ceiling and cornice moldings marks) the insulation was only partial with woodfiber panels.
20 mm
400 mm
20 mm
20mm
400 mm
76 mm
10 mm
Rear Facade: External insulation of the whole facade. Moreover, the window sills in natural stone have been replaced by fine aluminium plate which touch the insulation (XPS panels). the brick chimney have been destroyed above roof level.
no
400 mm
20 mm
20mm
100 mm
400 mm
20 mm
Windows
tradition oak frame window
The windows were replaced with new wooden (oak) ones, almost identical, with the original shape
All windows (frame glazing) have been changed mostly with triple glazing.
Existing window type | Casement window |
Existing glazing type | Single |
Existing shading type | NA |
Approximate installation year | 1888 |
New window type | Casement window |
New glazing type | Triple |
New shading type | NA |
New window solar factor g [-] | 0,49 |
Other interventions
ROOF
GROUND FLOOR
MEASURES TO INCREASE AIRTIGHTNESS
the pitched roof and flat roofs have been insulated
The bituminous coating of the flat roof has been replaced with new synthetic membrane
200 mm
400 mm
200 mm
22 mm
180 mm
10 mm
10 mm
The floor between the basement and the ground floor has been renovated, insulated as the the stair case from the basement to the ground floor
The wooden flooring has been conserved on the ground floor and the insulation has been done on the basement side. but unfortunately the arches ceiling in the basement has been hiden by the insulation
20 mm
20 mm
100 mm
0 mm
150 mm
20 mm
1 mm
1800 mm
1500 mm
A smart vapour barrier installed on the interior side of the pitched roof, Rear Façade and insulated part of the front façade covered with plaster guaranting wall airtightness, An airtight seal has been added at the entrance door and window frame. in between the basement and the ground floor a vapour barrier installed has been installed
HVAC
HEATING
VENTILATION
DOMESTIC HOT WATER
New gas condensed boiler new ventilation system
most of the heater were conserved
New primary heating system | New secondary heating system | |
---|---|---|
New system type | Condensing | Stove |
Fuel | Gas | Biomass |
Distribuition system | Radiators | Air |
Nominal power | 3.5 à 17.2 kW kW | kW |
new overflow system
The overflow system involves a lots of ducts. Most of the time their are set inside the suspended ceiling. Because the stucco ornamentation should be conserved the ducts have been placed into the chimney pipe. the air is blown in the room from the lateral side of the chimney toward the external wall to decrease all condensation risk. the ventilation system has been place in the basement and the duct were insulated
Original roof build-up | New ventilation system |
---|---|
Type ventilation system | Centralized |
Type flow regime | Overflow |
Heat recovery | Oui |
Humitidy recovery | Oui |
Nominal power | kW |
Electric power | 0,0 kW |
Control system |
the fluid-circulation system passes through one serpentine in a tank of 300L
no
New DHW system | |
---|---|
Type | decentral boiler |
Hot_water_tank | Oui |
With heat recovery | Oui |
RENEWABLE ENERGY SYSTEMS
SolarThermal
Biomass
SolarThermal System | |
---|---|
Type | Flat collector |
Collector area | 5,4 m² |
Elevation angle | 37,0 |
Overall yearly production | 0,0 kWh |
wood stove
na
Biomass System | |
---|---|
Type | |
Storage size | |
Origin of biomass | |
Overall yearly production | kWh |
Energy Efficiency
Voluntary certificates: No
Primary Energy 16983 kWh/y
Consumption_estimation_After: 45 kWh/m2.y
Primary Energy
Consumption_estimation_Calculation_method: Steady state simulation (e.g. EPC, PHPP)
Consumption_estimation_After: 16983 kWh/y
Type_of_monitoring: Continuous
Costs
The owners have received subsidies for the total renovation. "energy premium and renovation premium" from government.
1175 euros/m² eurosexcluding VAT (per m2)
Amount includes: it includes all the construction (materials/landscaping/realization) and conception (5000euros excluding VAT) 100euros/m² have been subsided by brussels environnment
Cost of energy related interventions:
75000 euros excluding VAT (total)
Amount includes: it includes the interior and exterior insulation, the windows, the roofs (flat and pitched) the solarfocus boiler, the gas condensing boiler (Vitodens 300W), the ventilation (Aerosilent van Drexel und Weiss) and monitoring. This amount represents 1/3 of the total budget
Environment
A rainwater storage has been installed in the garden