Farmhouse Straub
87527
Sonthofen, Germania
architetto
Contact Details

Climate Zone transition region between marine and continental climate
Altitude 890 s.l.m.
HDD 4398
CDD 0
Conservation Area:
No
Level of Protection:
Year of last renovation:
2018
Year of previous renovation:
0
Secondary use:
NA
Building occupancy:
Permanently occupied
Number of occupants/users:
10
Building typology:
Detached house
Number of floors:
2
Basement yes/no:
Si
Number of heated floors:
2
Gross floor area [m²]:
664,91
Thermal envelope area [m²]:
831,1
Volume [m³]:
1404,6
NFA calculation method:
NGF (de)
External finish:
Exposed woodwork
Internal finish:
Exposed woodwork
Roof type:
Pitched roof

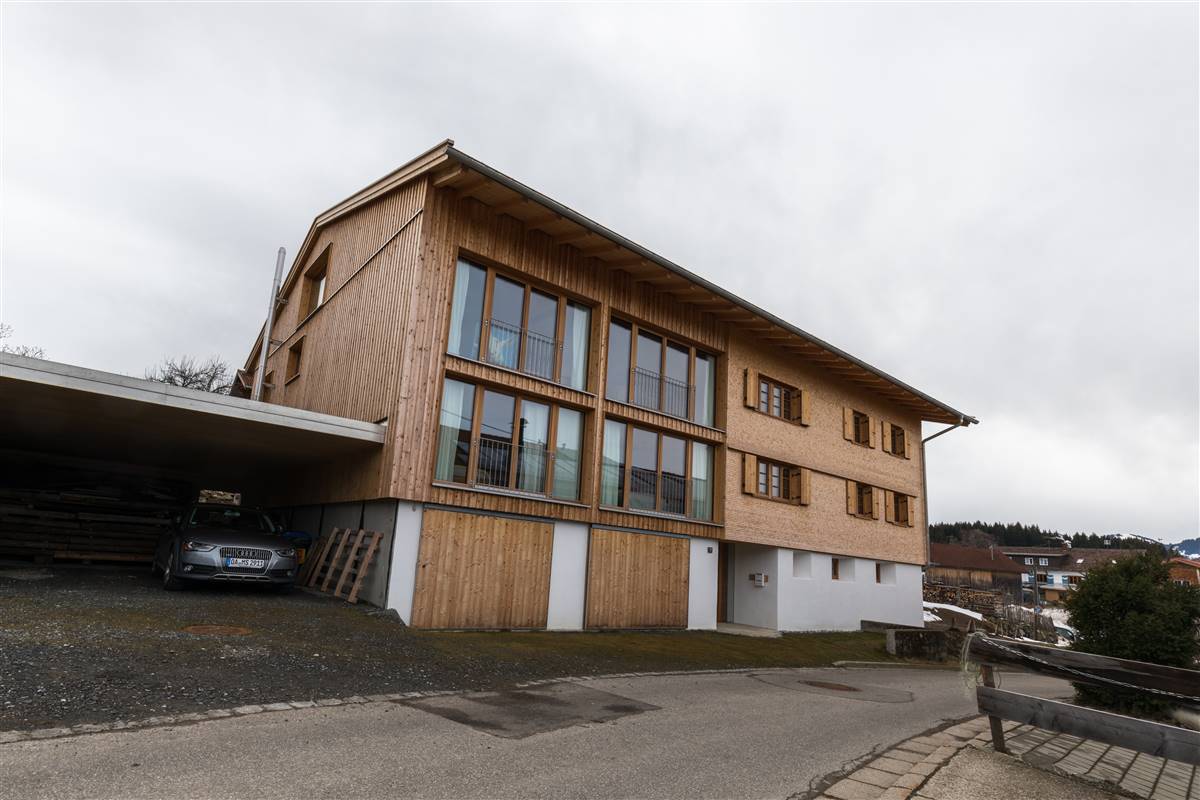
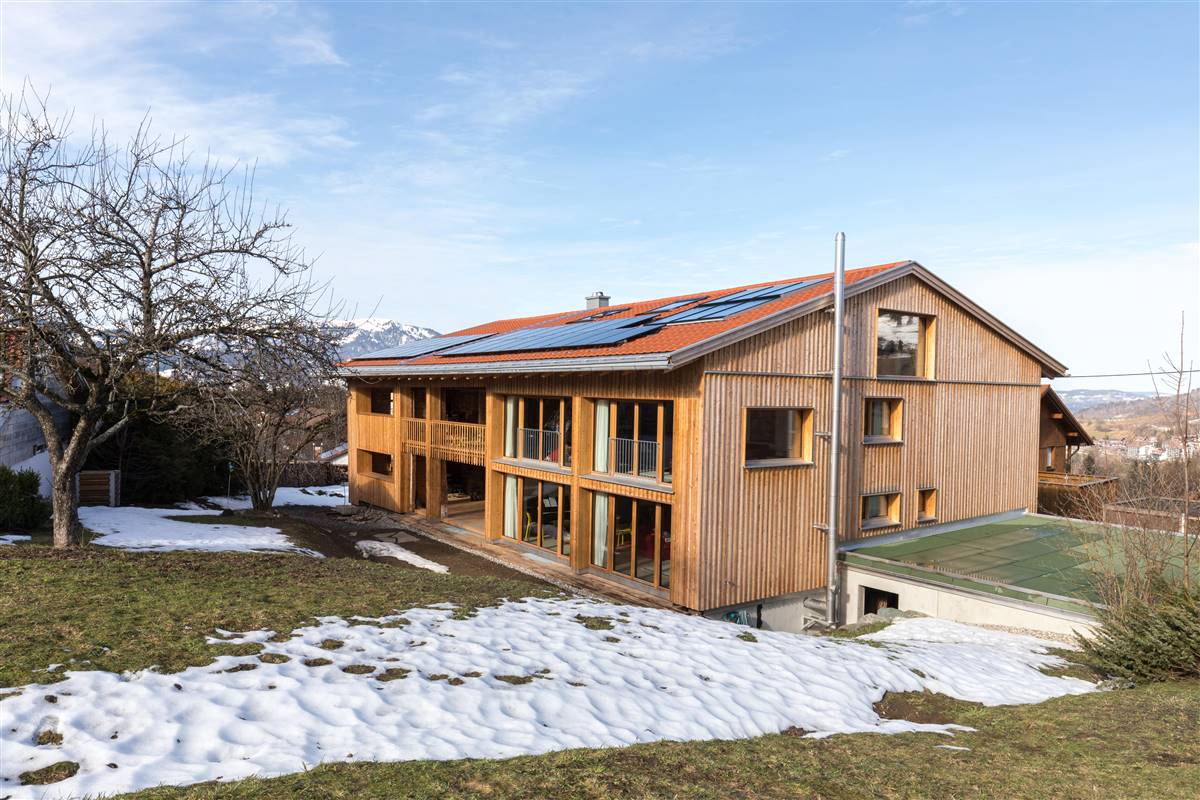
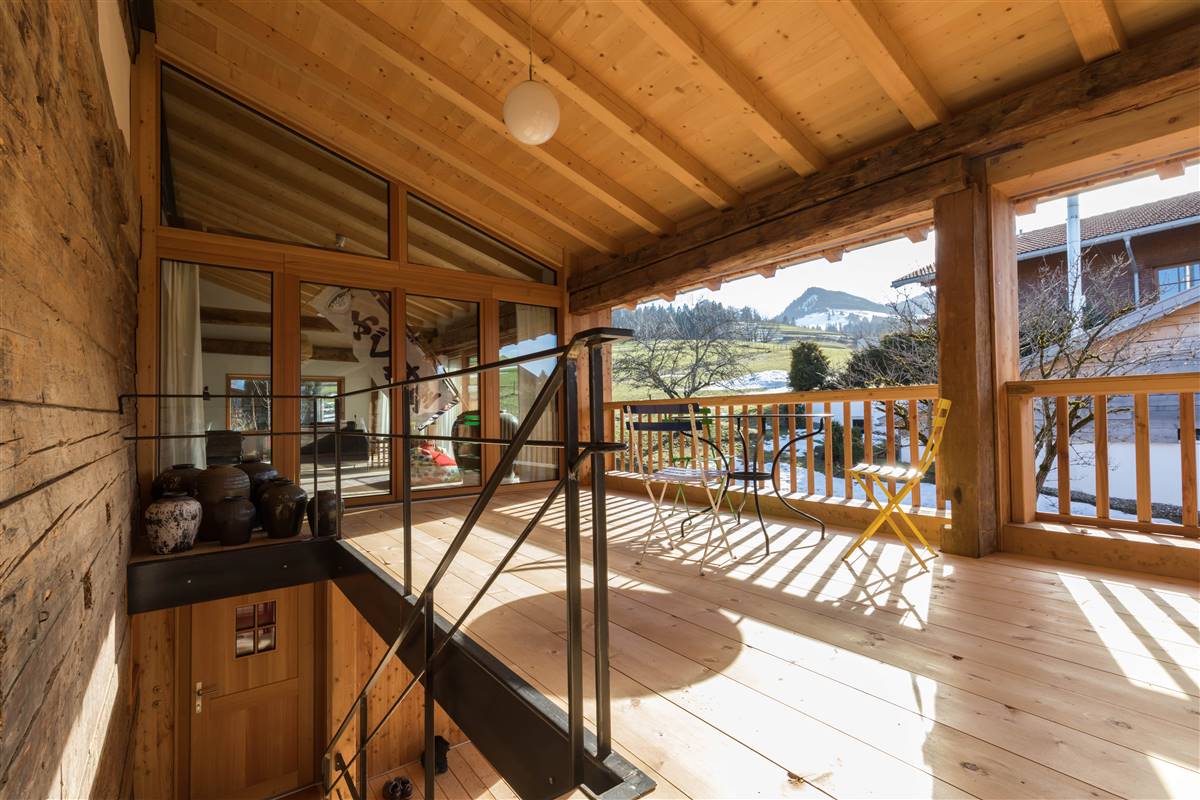
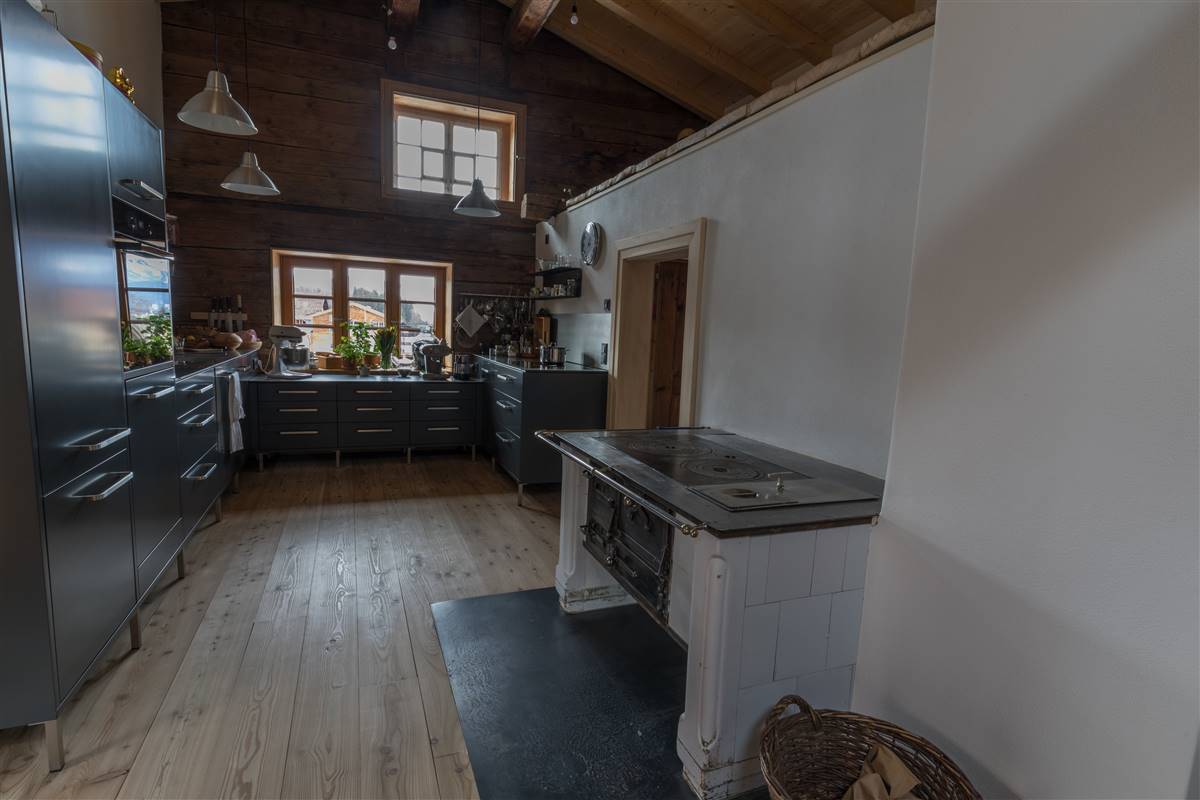
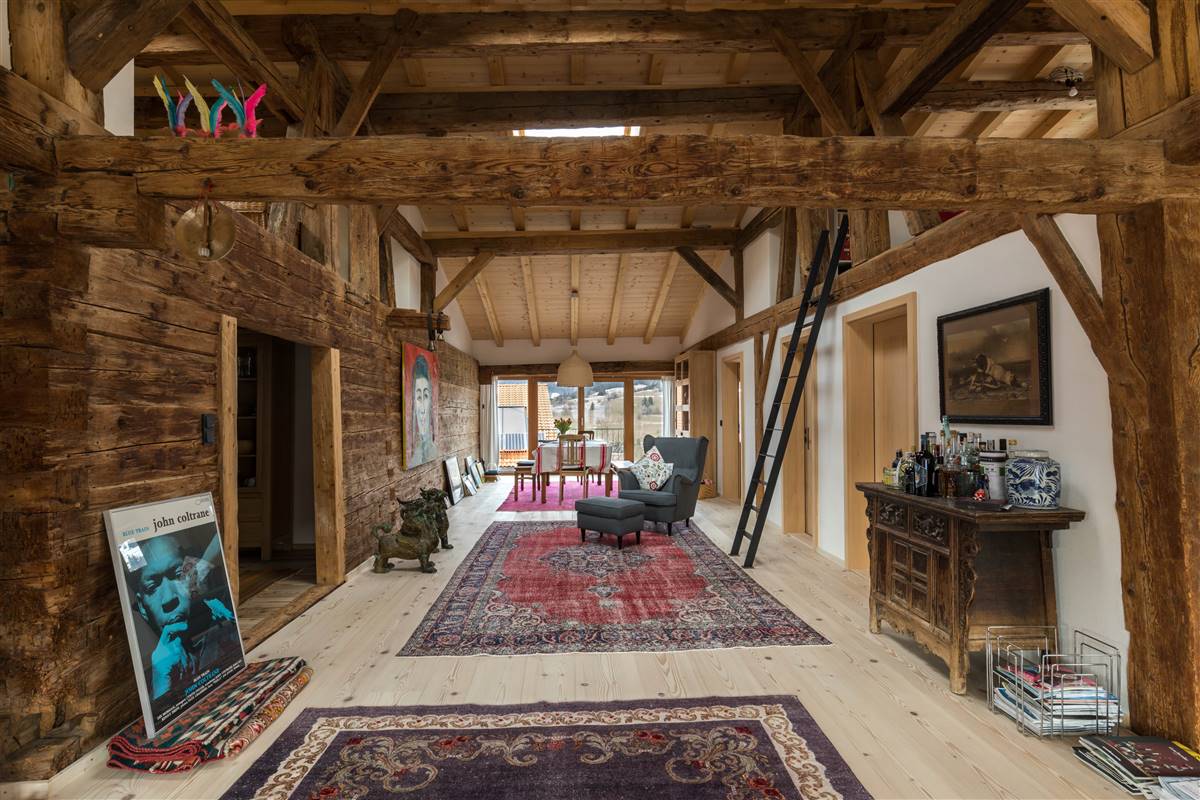
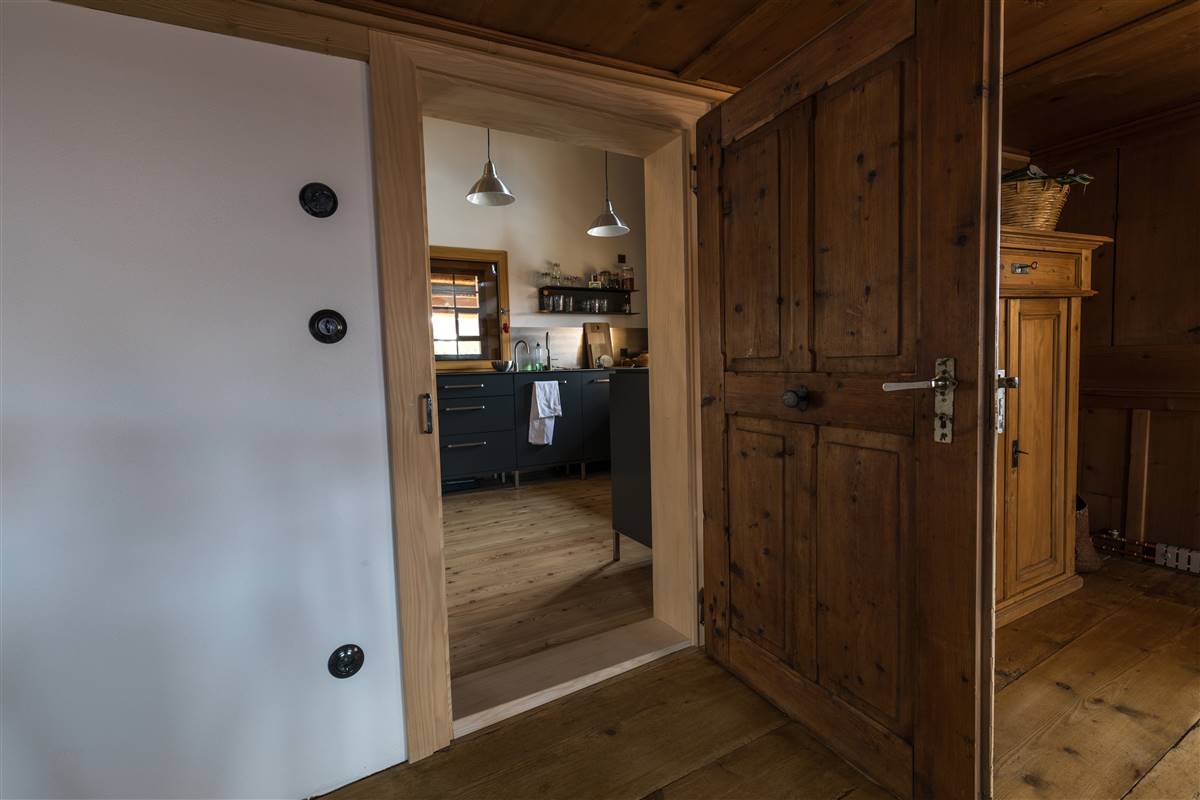
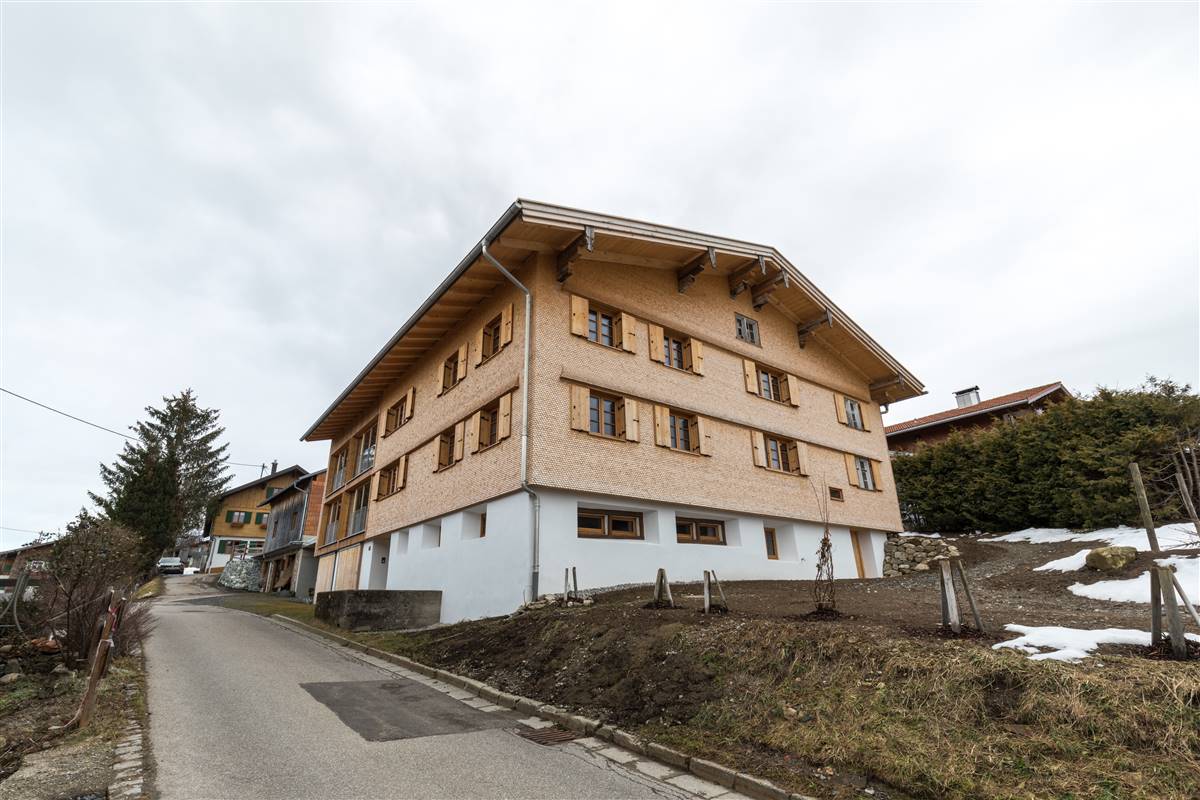
RENOVATION PROCESS
Architecture
BUILDING DESCRIPTION
State of repair
HERITAGE SIGNIFICANCE
Aim of retrofit
Michael Felkner
Niedersonthofener Straße 8, 87448 Waltenhofen-Oberdorf
RETROFIT SOLUTIONS
External Walls
Log wall, exterior insulation
Log wall, interior insulation
barnwall
The block construction of the farmstead is thermally insulated on the outside: a total of 24 cm of cellulose insulation is blown in between the battened construction timber. A 6 cm thick latex-impregnated wood fibre board, which could also have been plastered, but in this case was shingled, forms the finish.
The choice of materials for the interior plaster (clay plaster), the insulation (cellulose insulation and wood fibre boards) and the façade (wooden shingles) is very sustainable, adapts to the existing building and guarantees an extended lifespan of the existing wall.
15 mm
140 mm
20 mm
30mm
140 mm
240 mm
60 mm
The block wall to the veranda is insulated on the inside with 20 cm wood fibre board and also finished with clay plaster.
This way it is possible to keep the historic materials visible. The veranda are located where once there were the laundry and privy.
15 mm
160 mm
30mm
200 mm
160 mm
Additional timber framed wall in front of the existing beams with 28 cm cellulose insulation and 6 cm wood fibre insulation boards on both sides. The inner wood fibre board also serves as an installation layer, the adjoining OSB board as a vapour barrier. Towards the rooms, the new construction is mostly plastered, outside again with vertical wooden boarding.
The historical bolt work and the special roof structure are kept visible on the inside. They are protected from weather conditions and cold by the timber-framed wall in front of it.
200 mm
20 mm
30mm
60 mm
15 mm
280 mm
60 mm
Windows
Window in the barn
Window in the farmhouse, first floor box-type window north side
Window in the farmhouse
Preserved original windows
New window with triple glasing
no existing window before at this spot
Existing window type | no existing window before at this spot |
Existing glazing type | no existing window before at this spot |
Existing shading type | NA |
New window type | Sliding window |
New glazing type | Triple |
New shading type | NA |
New window solar factor g [-] | 0,53 |
New window with triple glasing
The box-type windows were replaced by wooden double windows with glazing bars. Their design is inspired by the historical window division.
Existing window type | Box-type window |
Existing glazing type | Single |
Existing shading type | Outer shutter |
Approximate installation year | 1940 |
New window type | Double window |
New glazing type | Triple |
New shading type | Outer shutter |
New window solar factor g [-] | 0,53 |
New window with triple glasing
In general, the historical windows have specific divisions of glazing bars depending on their direction. The design of every new window in the farmhouse is inspired by the historical window division of the northern facade. The windows were replaced by wooden double windows with glazing bars.
Existing window type | Double window |
Existing glazing type | Single |
Existing shading type | Outer shutter |
Approximate installation year | 1900 |
New window type | Double window |
New glazing type | Triple |
New shading type | Outer shutter |
New window solar factor g [-] | 0,53 |
In some areas, the original windows were retained: In the loggia, for example, where an improvement of the thermal properties was not necessary.
The original windows in the gable on the west wall were also repaired and preserved and an additional window level was added on the inside
Existing window type | Sash window |
Existing glazing type | Single |
Existing shading type | NA |
New window type |
Other interventions
ROOF
GROUND FLOOR
OTHER
MEASURES TO INCREASE AIRTIGHTNESS
The existing roof truss was kept and new rafters and insulation were installed.
The shape and the structure of the roof were kept and because of the removed ceiling it is now visible from the living room underneath. The rafters were mostly replaced and can also be seen from the inside due to the exterior insulation.
20 mm
30 mm
140 mm
2 mm
60 mm
280 mm
15 mm
Due to the low clear hight of the first floor and the basement, the bottom and the ceiling of the basement were lowered. The ceiling of the basement got an insulation.
Because of the more appropriate clear hight the first floor complies with modern demands. Therefore this huge intervention is absolutly justifyable.
180 mm
40 mm
24 mm
200 mm
20 mm
30 mm
20 mm
At the south side the barn was transformed into loggias for entering the apartments and relaxing.
The nowadays unnecessary farming use was replaced by an outside relaxing area inside the loggias including an open staircase. Since that there is an additional value for this space and the main entrance was kept at the south side of the building.
No blower door test was carried out (yet), but an airtightness concept was drawn up in the planning phase, which was also carried out accurately - not least due to the constant presence of the architect, especially in the final phase of the interior construction. Since not all areas are plastered, the airtight layer does not follow the internal plaster, as is often the case, but essentially the vapour retarders - in the roof and in most of the external walls - which were connected well to each other. The transition from the externally insulated area of the block wall to the internally insulated area (facing the veranda) remains the weakest point.
HVAC
HEATING
DOMESTIC HOT WATER
The existing ovens moved from the first floor to the second floor, but they are not the main heat source anymore. The demanded heat is now generated by a pellet boiler and a solar heating system.
The fact that the historic stoves have been preserved and continue to be used lends authenticity to the entire building. Thanks to the use of biomass, the building also performs very well in terms of primary energy: of the heating requirement for space heating of 13,350 kWh (see balance sheet as graph and table), which results in a final energy requirement of 15,464 kWh including losses and auxiliary energy, only 4,200 kWh of primary energy requirement remain - this corresponds to 7.4 kWh/m².
New primary heating system | New secondary heating system | |
---|---|---|
New system type | Stove | NA |
Fuel | Biomass | Solar energy |
Distribuition system | Radiating wall | Radiating wall |
Nominal power | 18,0 kW | kW |
Hot water is produced by the solar system in summer, which is supported by the pellet boiler in winter. In a renovated building like this, domestic hot water accounts for a good third of the final energy demand.
Since the flat pitched roof the solar modules can not be seen from the surroundings.
New DHW system | |
---|---|
Type | with heating system |
Hot_water_tank | Si |
With heat recovery | No |
RENEWABLE ENERGY SYSTEMS
SolarThermal
Photovoltaic
During the renovation a solar energy plant was installed on the rooftop, which supports the domestic hot water production.
Since the flat pitched roof the solar modules can not be seen from the surroundings, so the appearance is not disturbed. Besides that the solar energy plant reduces the demand of primary energy, so the building can be used more sustainable.
SolarThermal System | |
---|---|
Type | Flat collector |
Collector area | 12,0 m² |
Elevation angle | 15,0 |
Azimuth | 0,0 |
Overall yearly production | 3106,09 kWh |
Heating_contribuition | 0,0 kWh |
DHW contribuition | 3106,09 kWh |
Cooling contribuition | 0,0 kWh |
During the renovation a photovoltaic system was installed on the rooftop, which produces electricity.
As well as the solar energy plants the pv-modules can not be seen from the surroundings, so the appearance is not disturbed. Besides that the pv-modules reduces the demand of primary energy, so the building can be used more sustainable.
Photovoltaic System | |
---|---|
Type | NA |
Collector area | m² |
Elevation angle | 15,0 |
Heating contribuition | 0,0 kW |
DHW contribuition | 0,0 kW |
Cooling contribuition | 0,0 kW |
Energy Efficiency
Voluntary certificates: KfW-Effizienzhaus 55
Consumption_estimation_Calculation_method: Steady state simulation (e.g. EPC, PHPP)
Consumption_estimation_After: 47,3 kWh/m2.y
Primary Energy
Consumption_estimation_Calculation_method: Steady state simulation (e.g. EPC, PHPP)
Consumption_estimation_Including_DHW: Si
Consumption_estimation_After: 12,3 kWh/m2.y
Internal Climate
The demanded temperature for the inside is 20 ° C.
The indoor quality is fine.
The position and sizes of the existing windows in the farmhouse have not been altered, so there is no change in lightning. On the other hand the new windows in the barn have modern sizes, so the rooms behind them seem bright and friendly.
The acoustic comfort is fine.
NA
Costs
The cost breakdown of 930'000,-€ includes both the energetic renovation (with 530'000,-€) and the adaptation to age-appropriate living (with 400'000,-€), including VAT of 19%. The following subsidies could be used: 1.)Subsidy from the KfW programme "Energy-efficient renovation": 3x120'000,- at 0.75% interest, 10 years fixed interest and 144'000,- repayment subsidy (thanks to reaching KfW Efficiency House 55. 2.)Subsidy from KfW's "Altersgerecht Umbauen" programme: 3x50,000 at 0.75% interest, 10 years fixed interest. 3.) Bafa heating subsidy: approx. 20'000,-€ investment subsidy 4.) KfW Building Assistance Programme 4'000,- € subsidy 5.) District programme construction support 4'000,-€ subsidy. So, in addition to the favourable interest rate, approx. 172'000,-€ came from the state.
1640,- € (per m2)
Amount includes: The cost breakdown of 930'000,-€ includes both the energetic renovation (with 530'000,-€) and the adaptation to age-appropriate living (with 400'000,-€), including VAT of 19%.
Cost of energy related interventions:
930,-€ (per m2)
Amount includes: This value includes not only the additional costs for the energy-efficient refurbishment, but also all the investments in connection with the energy-efficient refurbishment, i.e. also all the repairs and maintenance measures that are necessary anyway.
No