Town Hall Burgkunstadt
Vogtei 5
96224
Burgkunstadt, Germania
architetto
Owner
User
Contact Details
Other Information
opening hours: Mon+Wed 08:00-12:00 and 13:00-16:00, Thu 08:00-12:00 and 14:00-18:00, Fri 08:00-12:00
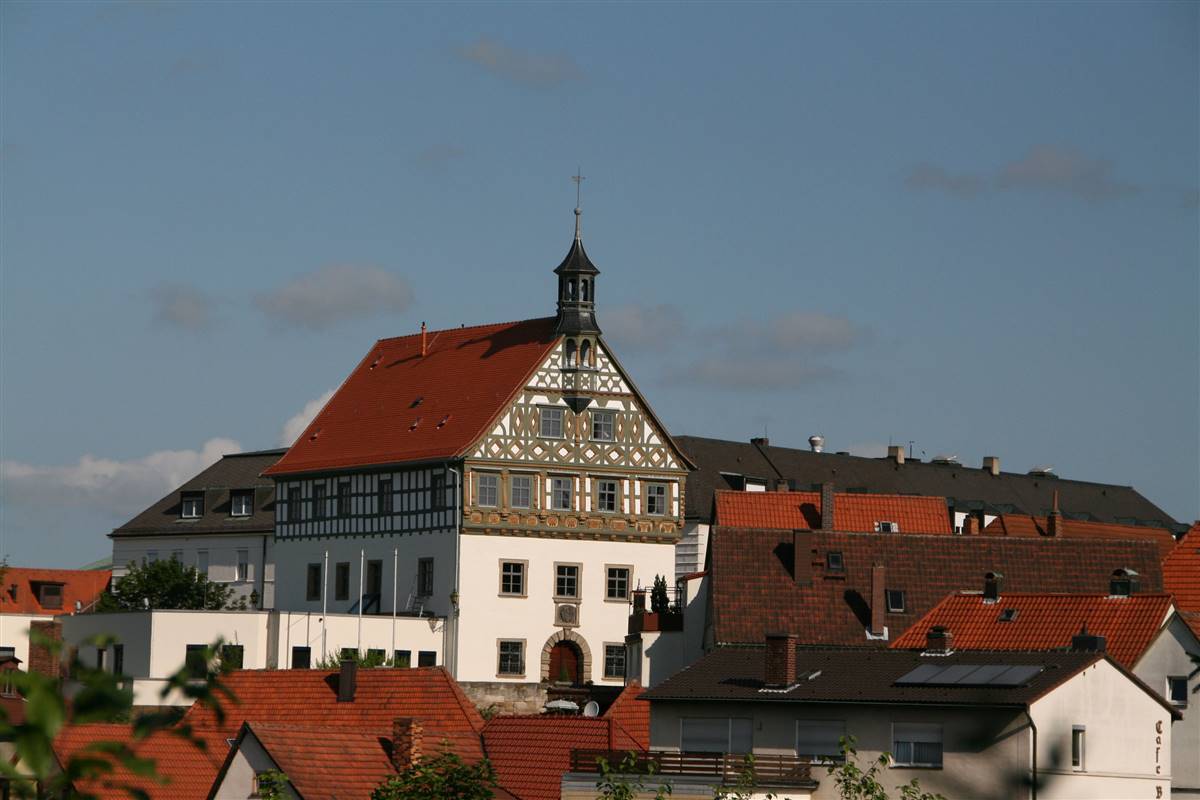
Climate Zone cfb
Altitude 306 s.l.m.
HDD 2682
CDD 464
Conservation Area:
Si
Level of Protection:
Year of last renovation:
2009
Year of previous renovation:
1979
Secondary use:
Offices
Building occupancy:
Permanently occupied
Building typology:
Detached house
Number of floors:
6
Basement yes/no:
Si
Number of heated floors:
3
Gross floor area [m²]:
1006,0
Thermal envelope area [m²]:
679,0
Volume [m³]:
1641,0
NFA calculation method:
NGF (de)
External finish:
Rendered
Internal finish:
Plastered (on hard)
Roof type:
Pitched Roof
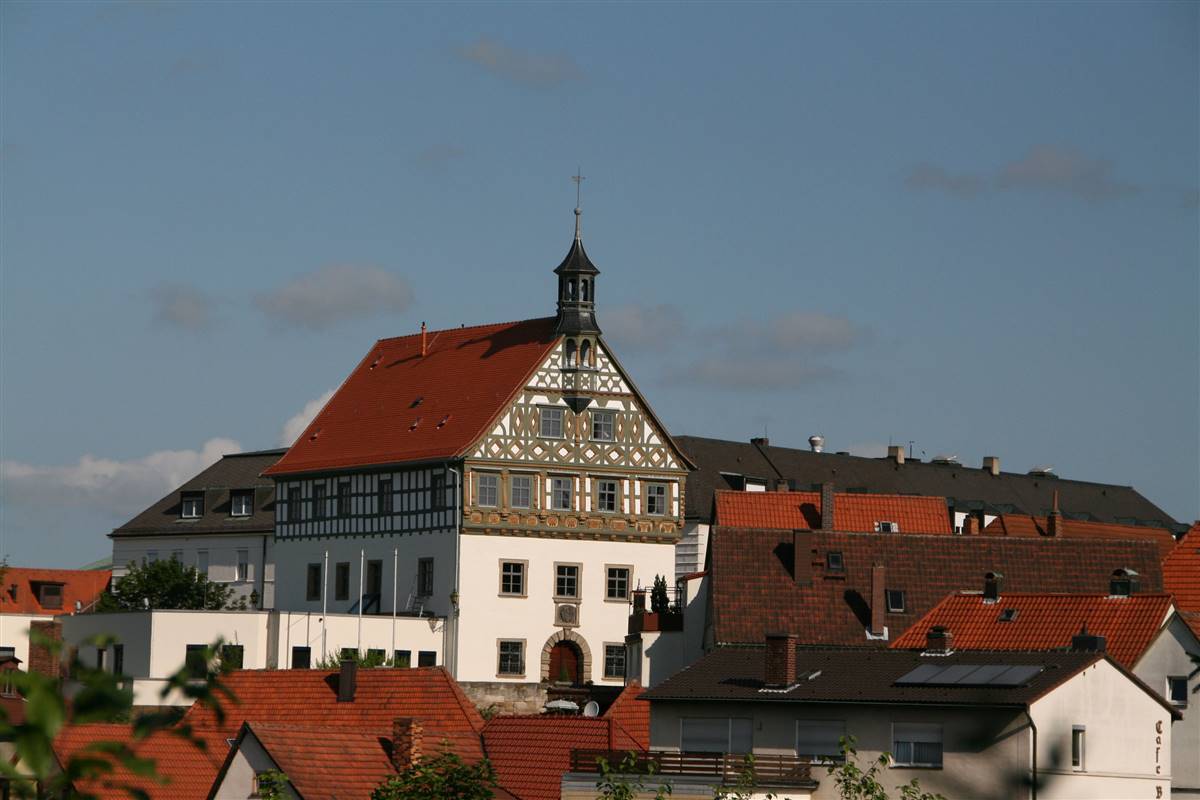
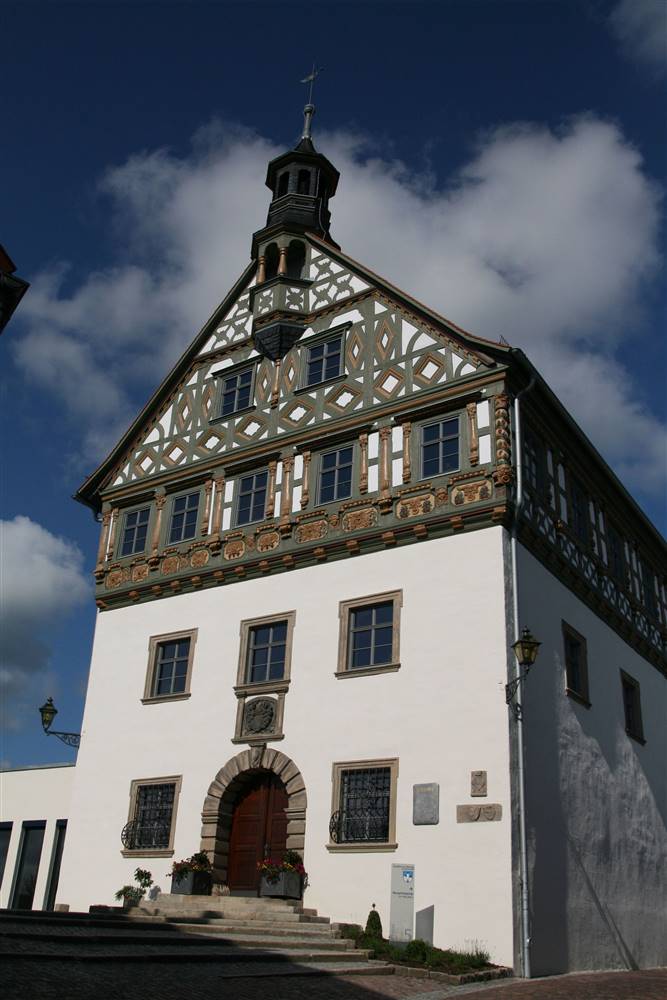
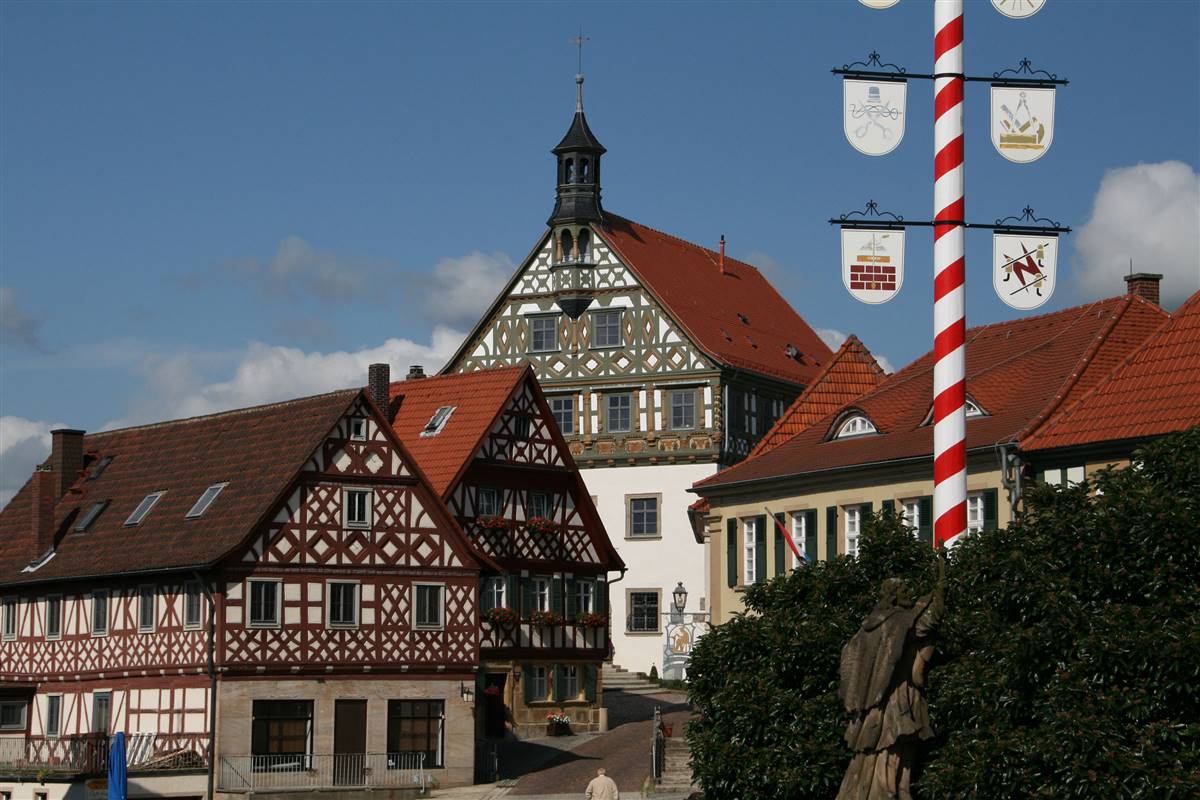
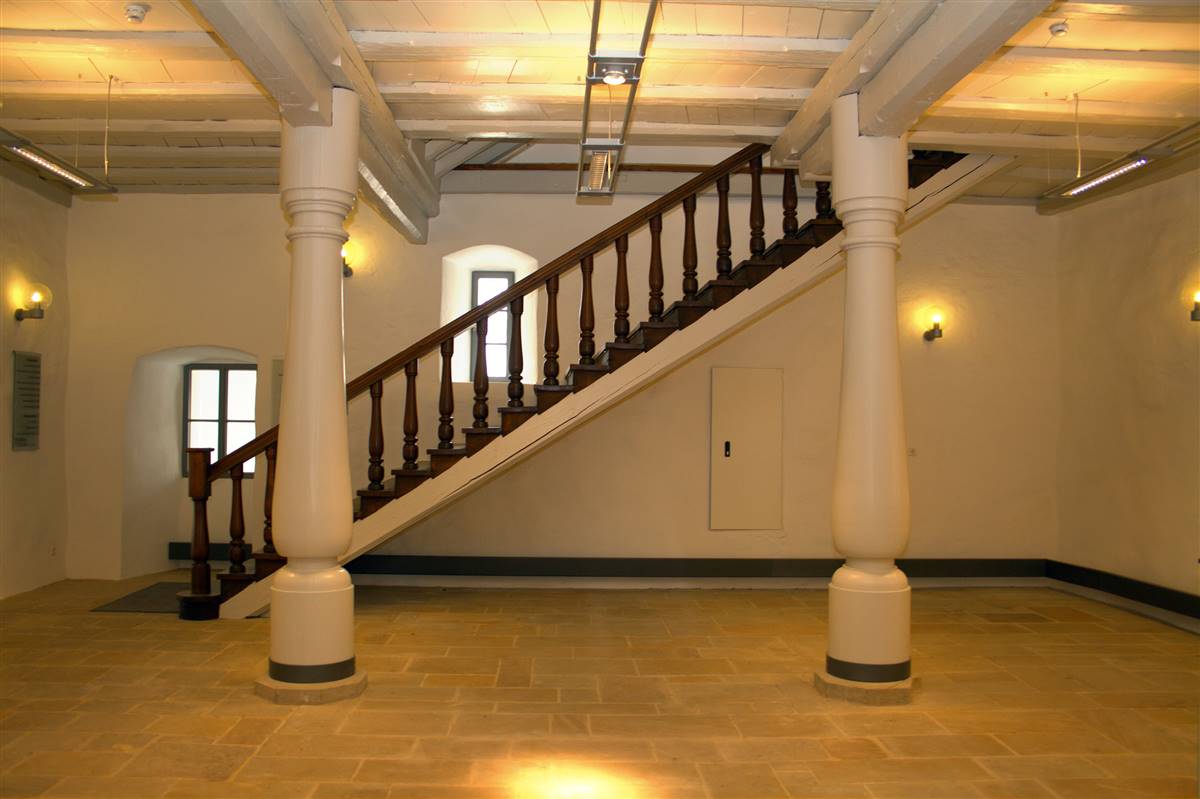
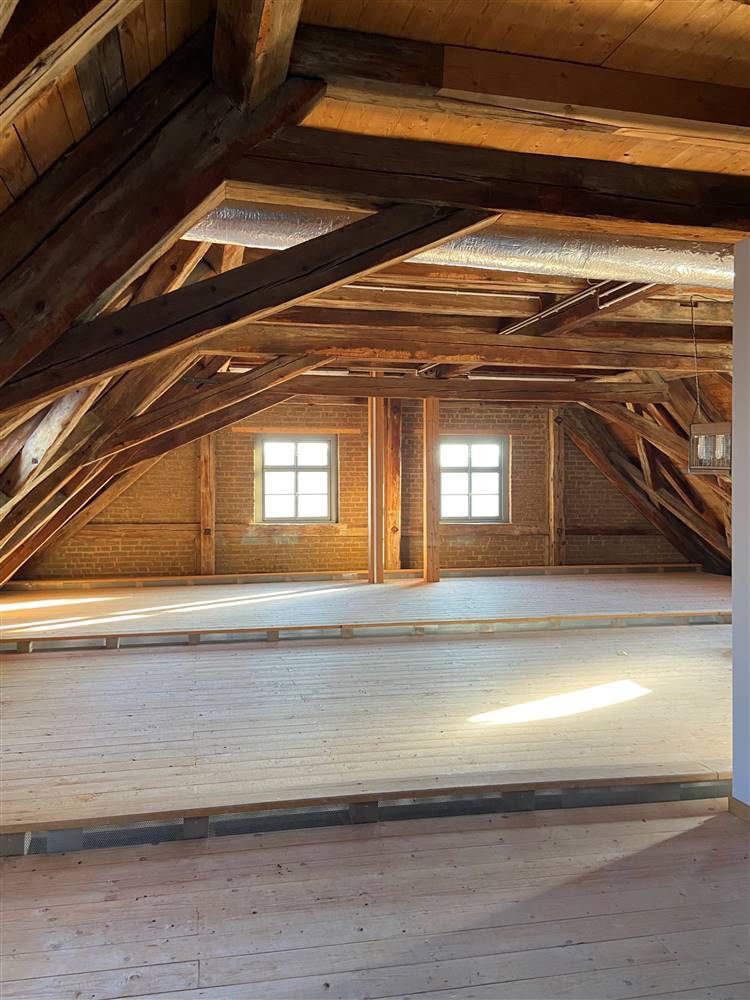
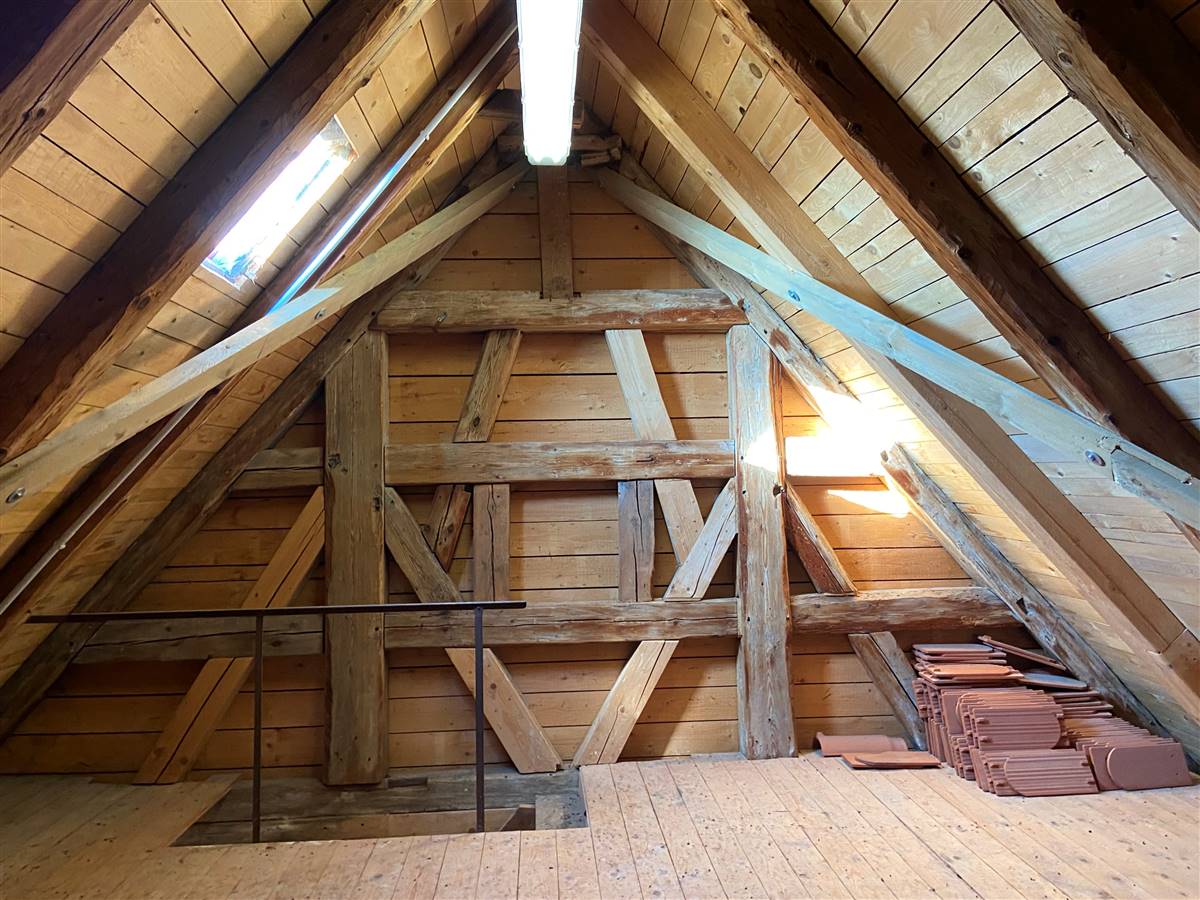
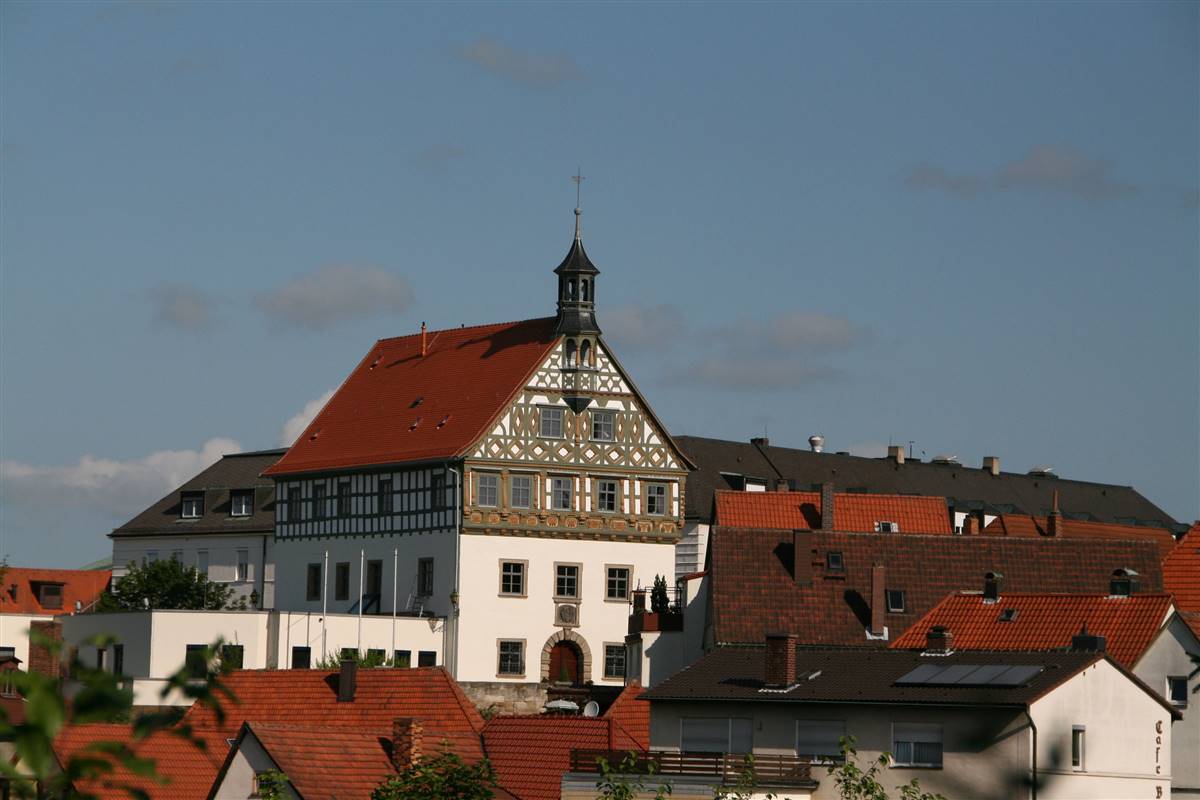
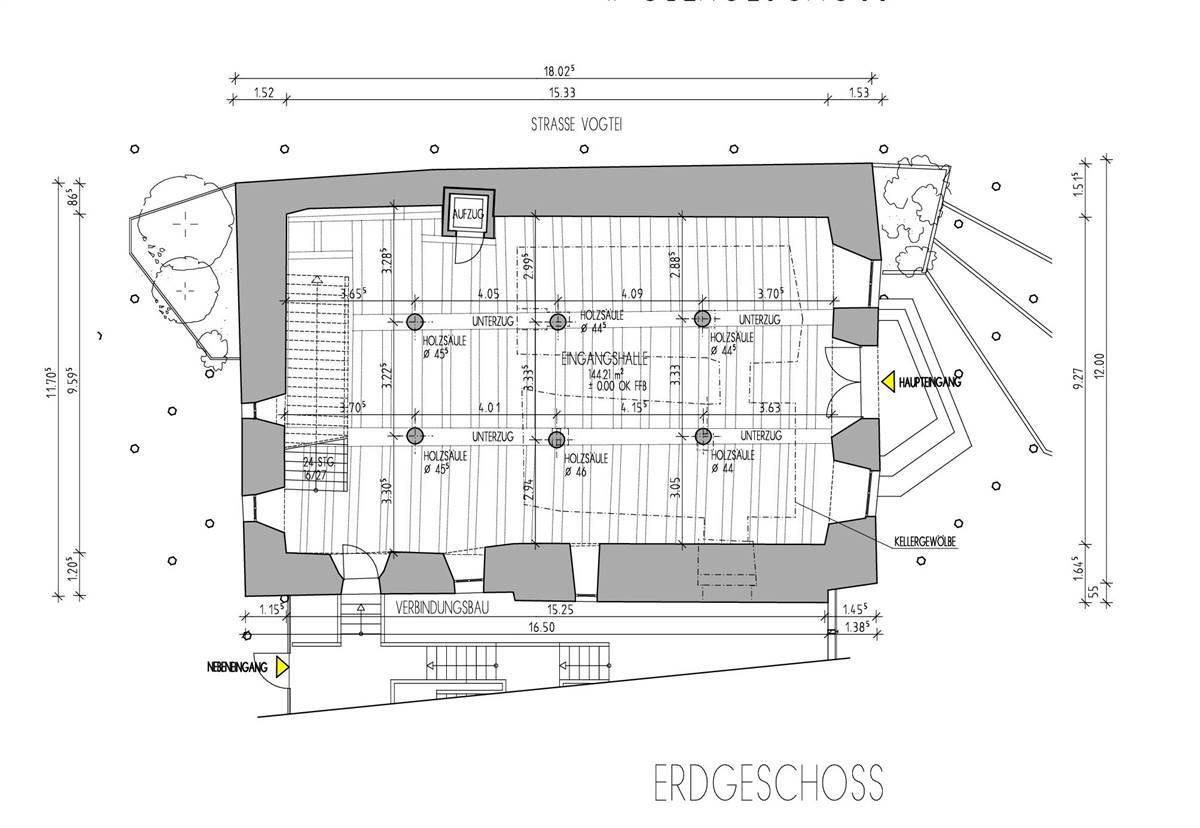
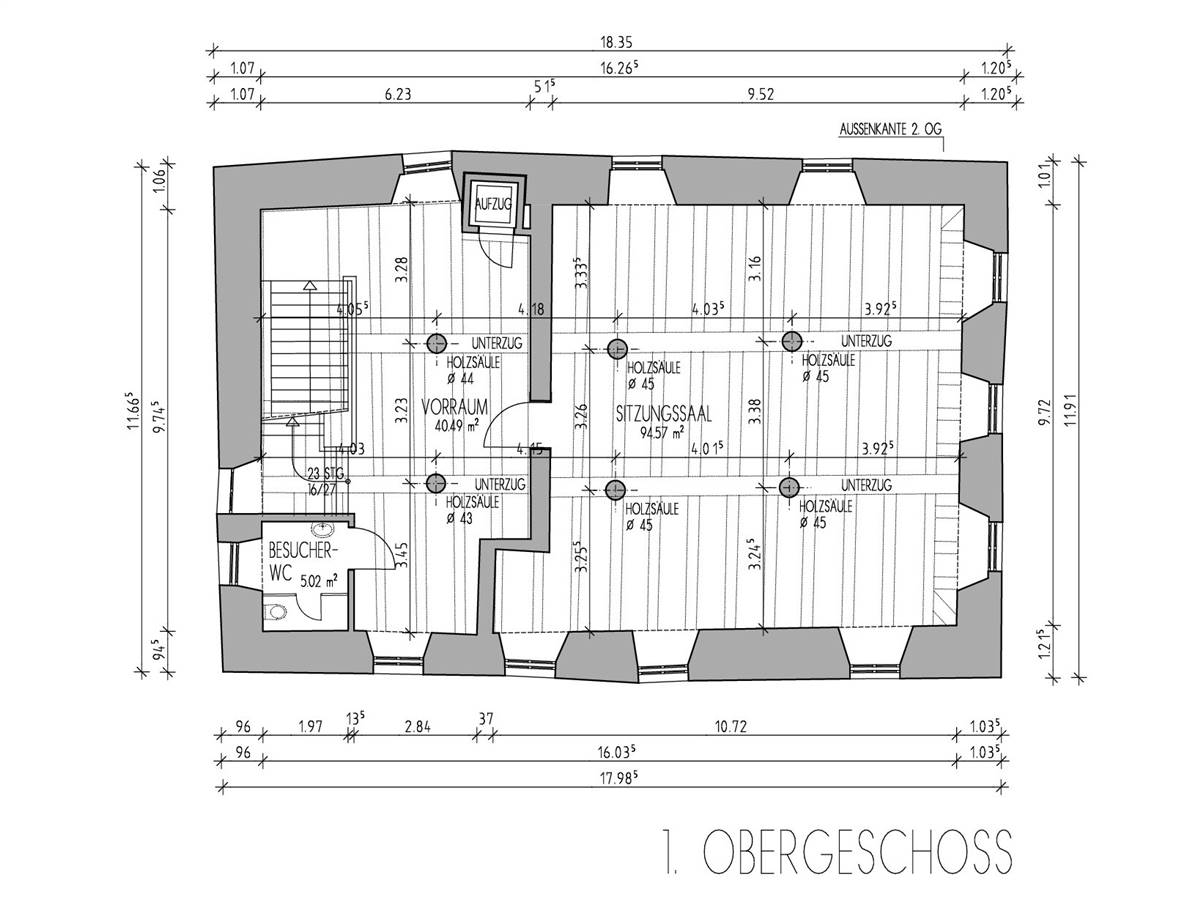
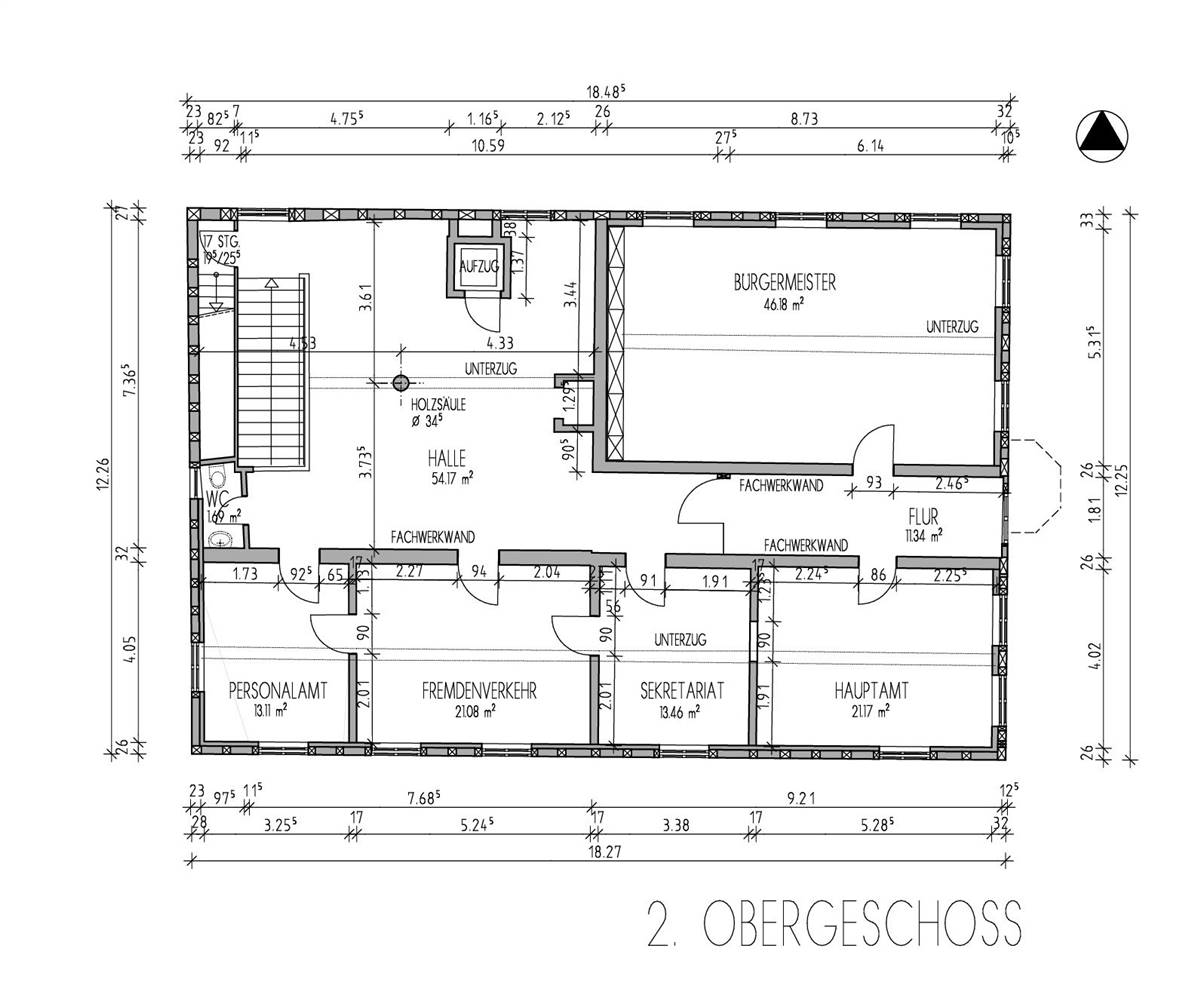
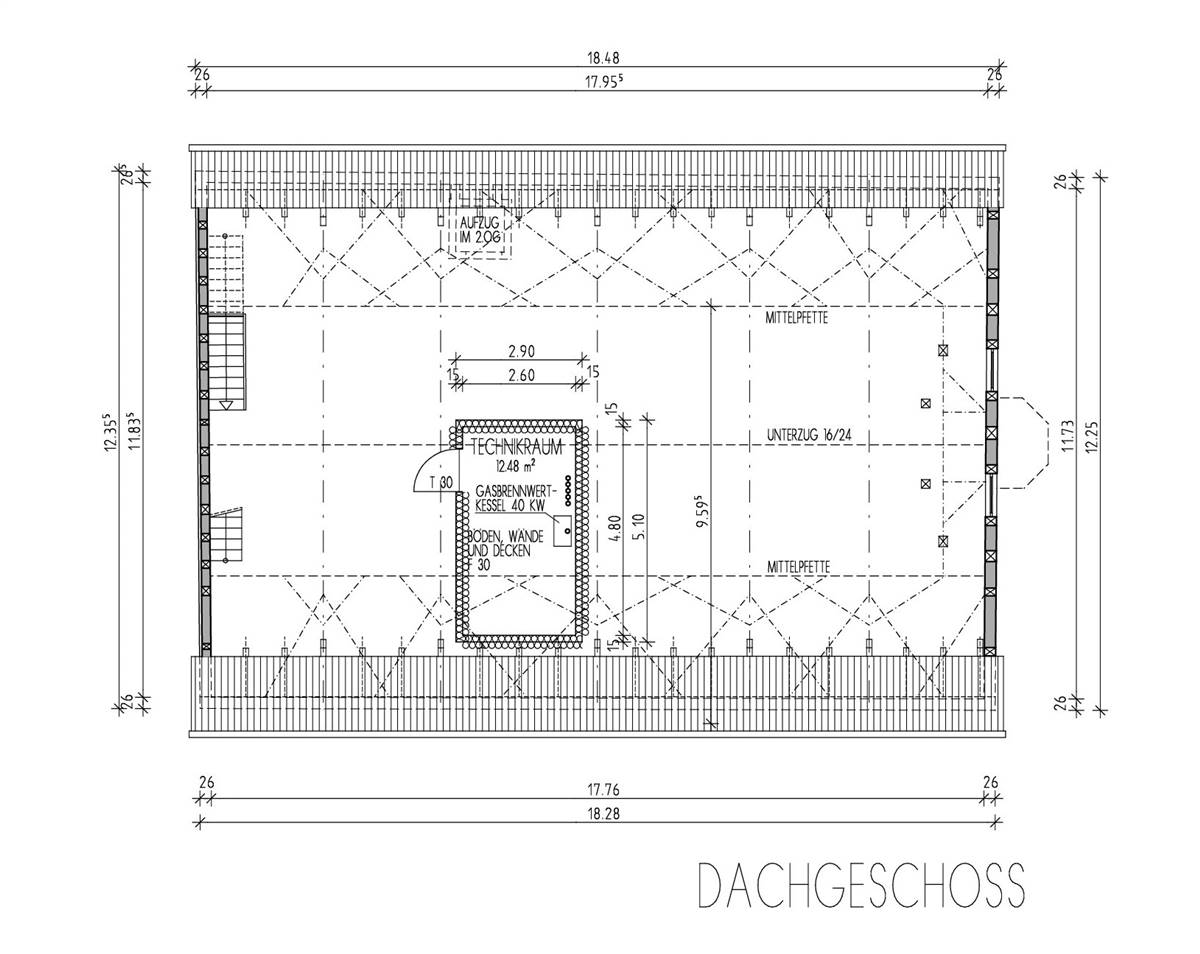
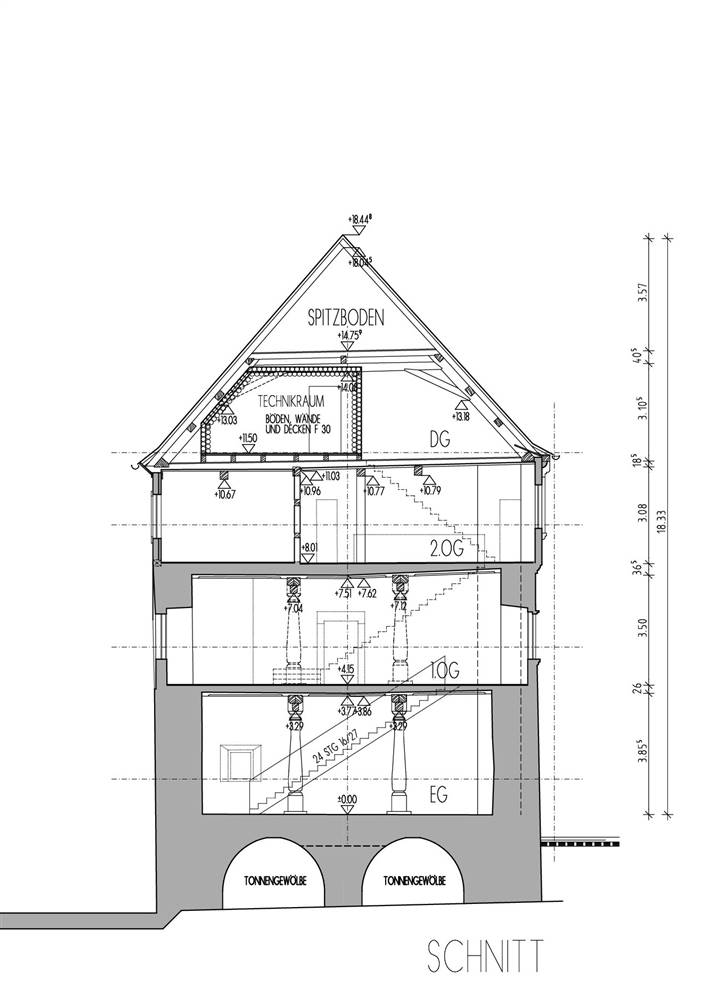
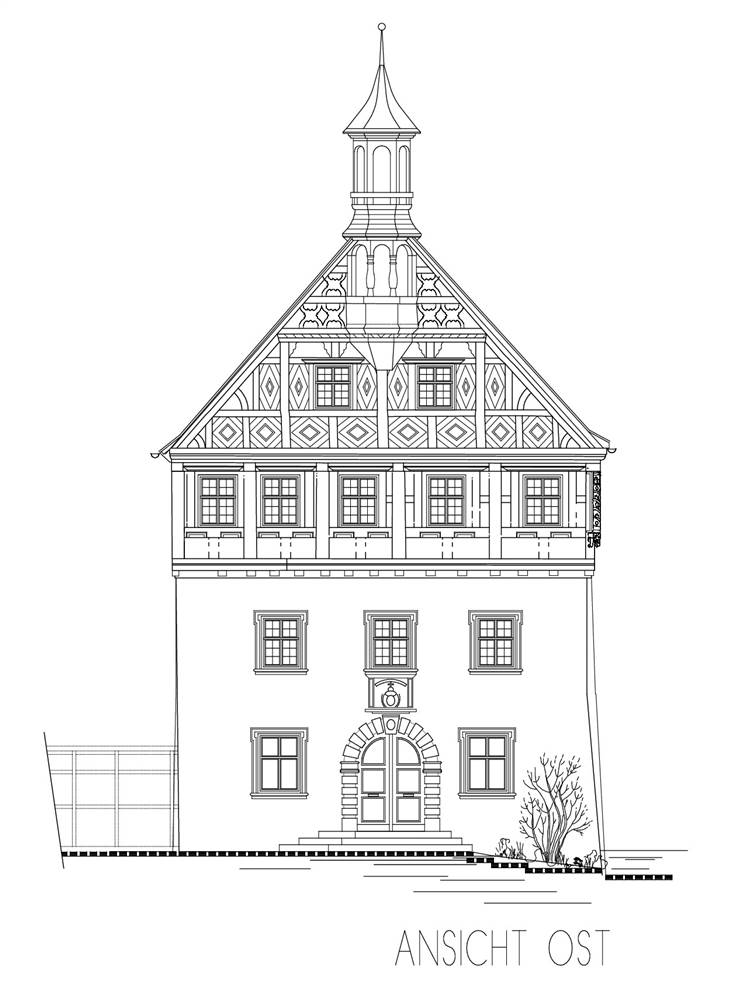
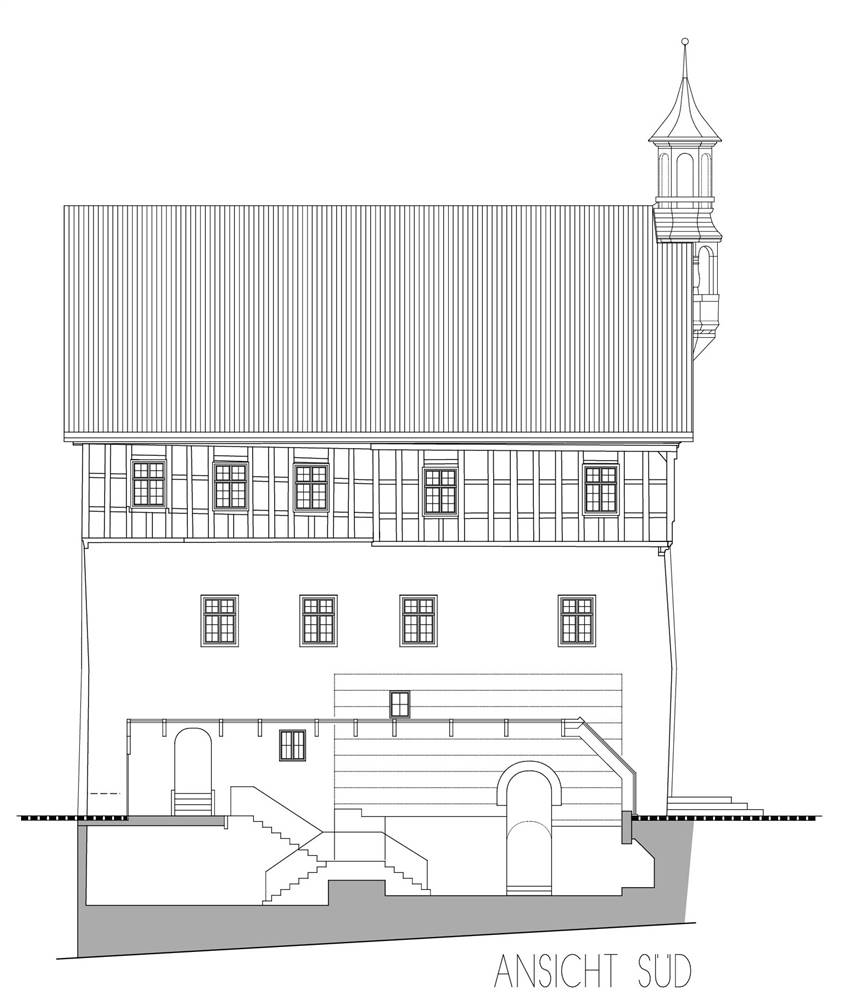
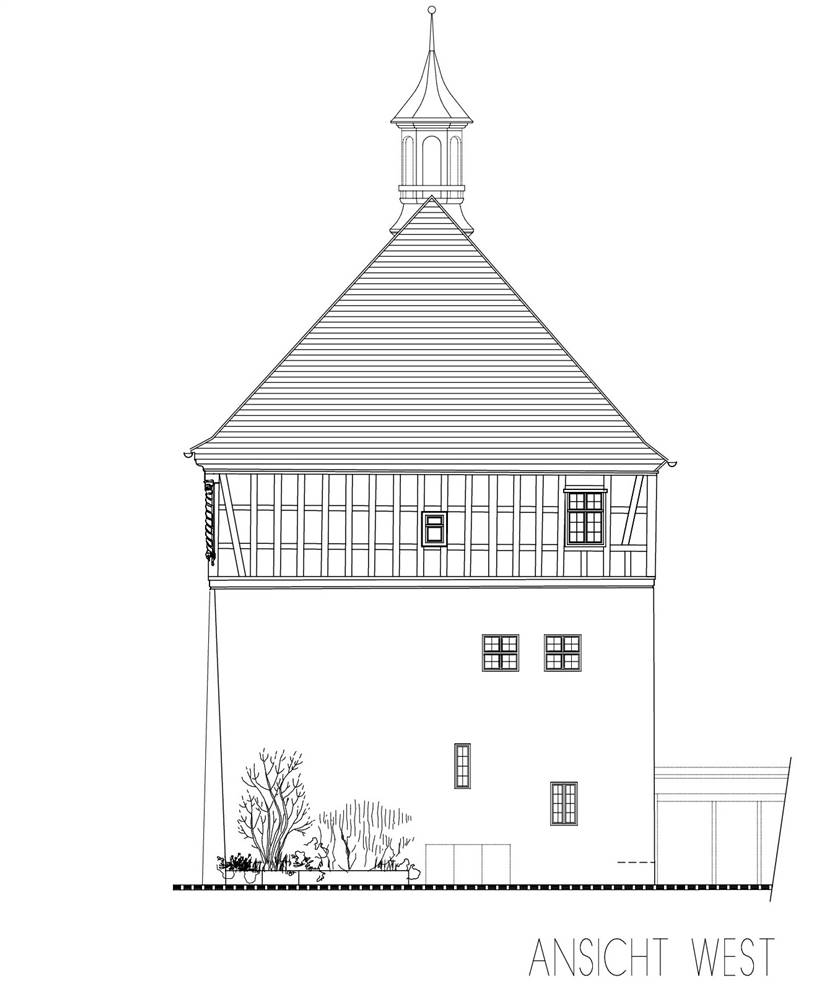
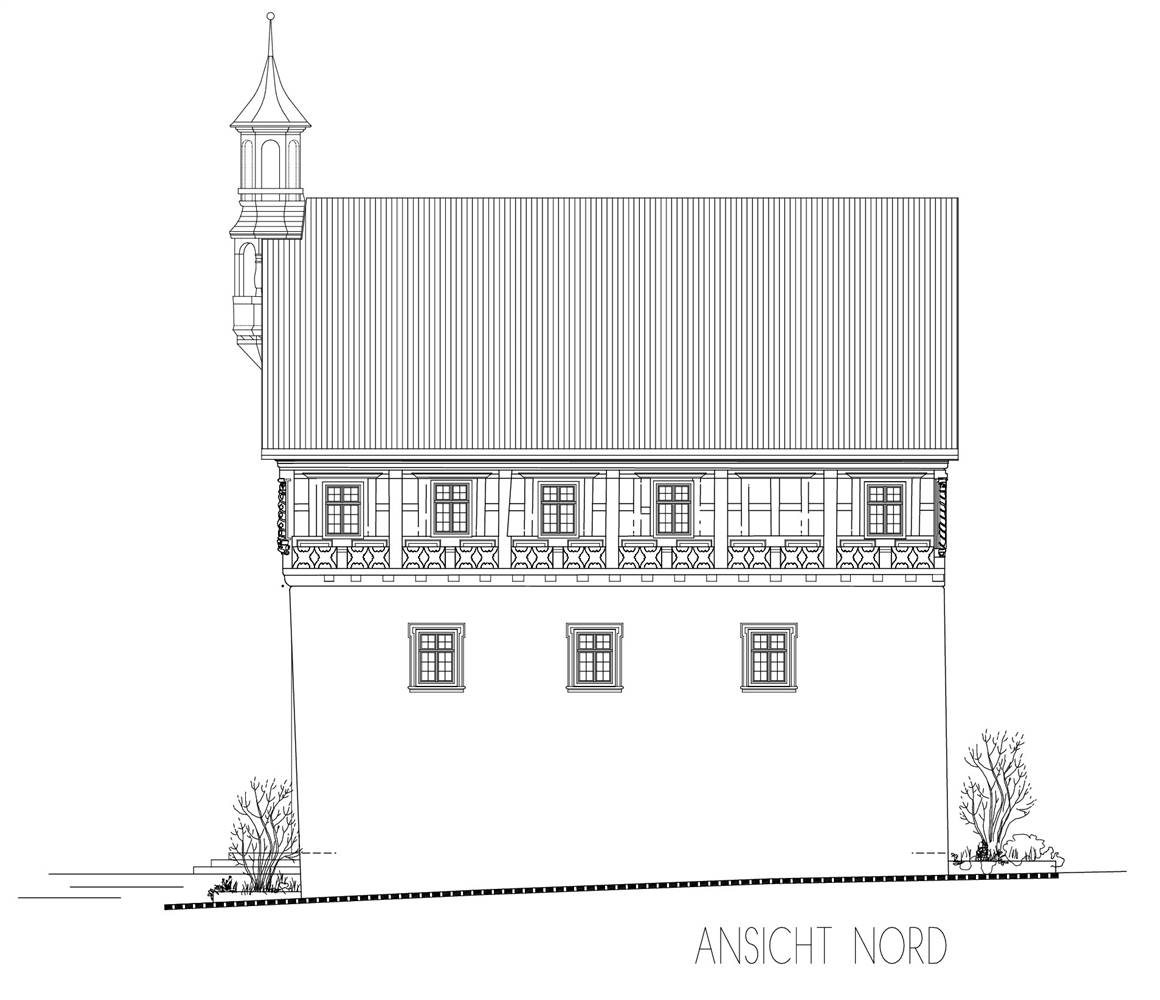
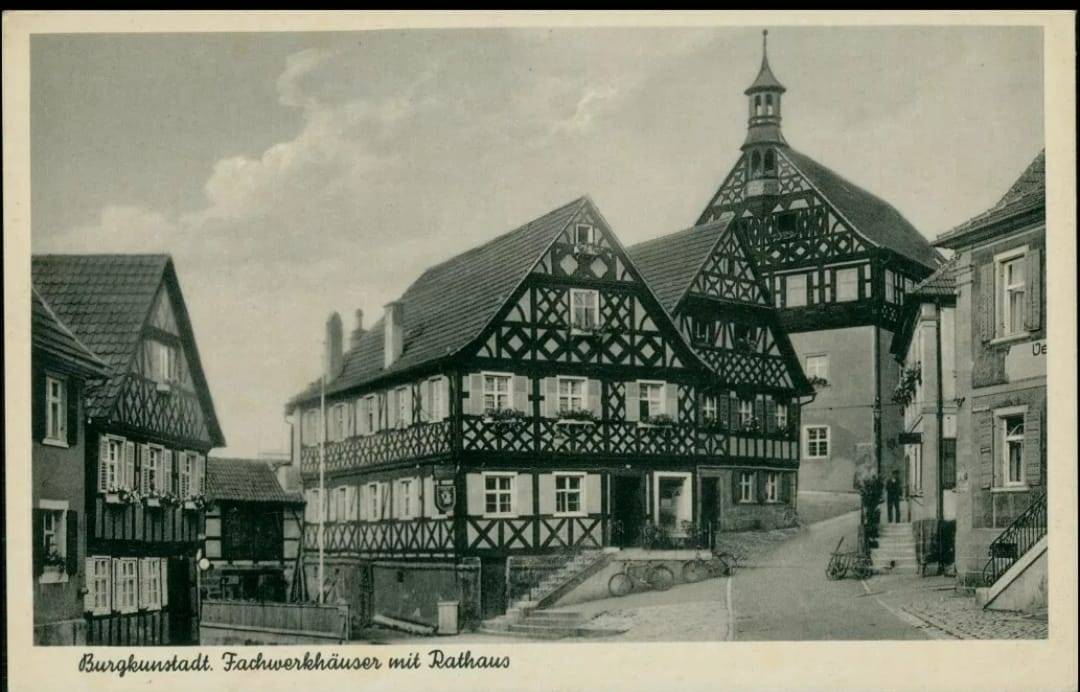
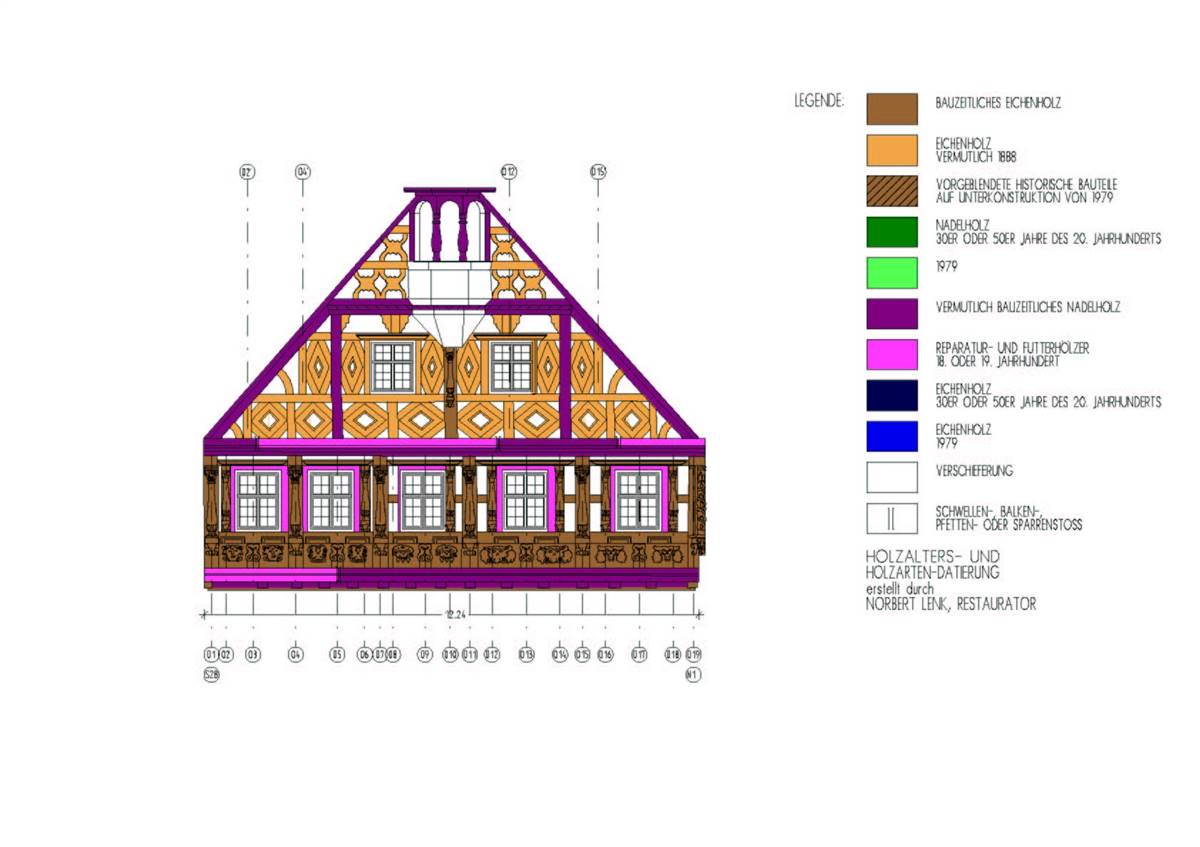
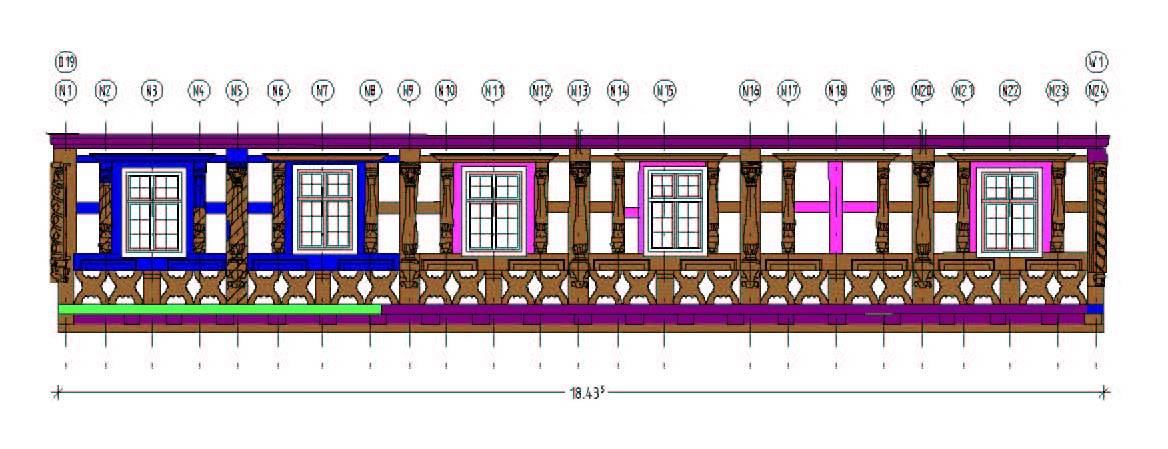
.jpg)
RENOVATION PROCESS
Architecture
BUILDING DESCRIPTION
State of repair
HERITAGE SIGNIFICANCE
Aim of retrofit
Stadt Burgkunstadt
Vogtei 5, 96224 Burgkunstadt
rathaus@burgkunstadt.de
Tel.09572 / 388 0
Hofmann Erhalten & Gestalten
Bergstr. 4, 96167 Königsfeld
info@hofmann-erhalten-gestalten.com
Tel.09207 / 9500
Architekturbüro Huth
Dr.-Baur-Siedlung 6a, 96224 Burgkunstadt
info@architektbuero-huth.de
Tel.09572 / 79 00 83
Bayr. Landesamt für Denkmalpflege
Schloss Seehof 1, 96117 Memmelsdorf
DST_Seehof@blfd.bayern.de
Tel.0951 / 4095 0
Ingenieurbüro Burges + Döhring
Schlehenbergstr. 1, 95448 Bayreuth
info-bt@bdingenieure.de
Tel.09209 / 982 0
Ingenieurbüro Reichenbach & Henkel
Tiefe Gasse 28, 96224 Burgkunstadt - Kirchlein
info@rh-ing.de
Tel.09572 / 3818 0
Institut für Gebäudeanalyse (Bauphysik)
München
Restaurator Norbert Lenk
Langfeldstraße 23, 91077 Neunkirchen am Brand
n.lenk@t-online.de
Tel.09134 / 909012
RETROFIT SOLUTIONS
External Walls
half-timbering 2nd floor
massive masonry ground und first floor
In the course of the renovation, the previous infill was completely removed. Afterwards, the timber-work was repaired. The new infill was lined with special lightweight clay bricks from Claytec. In addition, internal lightweight clay insulation boards were installed to improve the insulation performance. Today, the wall temperature control is achieved by means of a wall heating system embedded in clay plaster. The wood carvings were repaired in a manner appropriate to the monument by filling them with a special wood crack paste from the Caparol company. Then all wooden elements were painted with a linseed oil paint.
During the refurbishment in 1970, a colour scheme in brown tones had been chosen. However, since the non-diffusion-open paint had caused some damage, it was completely removed in the course of the current renovation. In close cooperation with the monument conservation authorities and after an extensive research and investigations on the building, it was possible to determine the original colour shade applied by Jörg Hoffmann
0 mm
3mm
10 mm
20 mm
55 mm
70 mm
115 mm
20 mm
In order to improve the statics of the massive basement floor, the affected components were needled and grouted on the one hand. On the other hand, the floor slabs were structurally integrated. There were no energy-saving measures carried out on the masonry walls. Since the building was divided into different temperature zones and the ground floor only has a low temperature, the temperature losses are limited due to the poor U-value of the wall. The savings could not be taken into account in the standardized calculations according to the EneV, which is why the losses in the ground floor are relatively high in the verification. However, if one assumes that only a target temperature of 16° is reached there, the losses would be approx. 70% lower.
15 mm
1000 mm
20 mm
15mm
1000 mm
20 mm
0 mm
Windows
box window
The existing box-type windows were completely replaced in the renovation process. In addition, they were equipped with sun protection.
From an energy point of view, insulating glazing was to be installed, although this did not comply with the guidelines of the heritage office. For this reason, a classic drawn glass from the Schott company was used for the exterior panes of the insulating glass windows. This is characterised by its uneven surface, which is created by using the Fourcault method in the manufacturing process. So the original appearance of the façade could be retained.
Existing window type | Box-type window |
Existing glazing type | Single |
Existing shading type | NA |
Approximate installation year | 1979 |
New window type | Casement window |
New glazing type | Double |
New shading type | Inner shutter |
New window solar factor g [-] | 62,2 |
Other interventions
ROOF
GROUND FLOOR
OTHER
MEASURES TO INCREASE AIRTIGHTNESS
Due to the existing damage and the lack of static stability, the affected components were removed and supplemented or completely replaced. Furthermore, the connections between the roof and the wall were strengthened in order to sufficiently reinforce the supporting structure. Yet, energetic measures were not implemented at the truss. Hence, the new ceiling above the 2nd floor serves as the upper finish of the thermal envelope. Since the attic is not used, the floor structure here could be ventilated to prevent moisture damage.
Due to the pollution burden, most of the ceilings were dismantled and replaced by new constructions. Elements important for the preservation of monuments, such as the planks of the plank ceiling and the exposed formwork, were retained. After cleaning, these components were given a special coating that traps the pollutants, but otherwise remains vapour-permeable. In the general process, as much as possible of the historical structure was preserved during the constructional interventions.
28 mm
60 mm
120 mm
35 mm
80 mm
2 mm
45 mm
The floor structure was retained. However, since the existing underfloor heating was very sluggish due to the high floor construction, the entrance hall was supplemented with a baseboard heating system.
-
Another energy-saving measure was the differentiation of the building into its various usage zones. The individual areas, such as the entrance hall, conference room and administrative rooms, were divided into different temperature zones. This classification was then used to develop appropriate energy-related measures.
So unused areas, such as the roof truss and the vaulted cellar, could be preserved in their original form.
To ensure better airtightness, all new constructions were made airtight and the corresponding joints were specially sealed. The connections were sealed with sealing tapes.
HVAC
HEATING
VENTILATION
DOMESTIC HOT WATER
Before the renovation, the town hall was supplied with electric storage heating. The two new gas condensing boilers heat both the historic old building and the new extension. The heating system is located in the technical room on the first floor together with the ventilation system.
-
New primary heating system | |
---|---|
New system type | Condensing |
Fuel | Gas |
Distribuition system | Radiating wall |
Nominal power | 45 kW |
As a result of the renovation, the town hall received a ventilation system that supplies the administrative rooms on the 2nd floor.
-
Original roof build-up | New ventilation system |
---|---|
Type ventilation system | Centralized |
Type flow regime | |
Heat recovery | Si |
Humitidy recovery | |
Nominal power | kW |
Electric power | kW |
Control system |
Hot water is generated by decentralized instantaneous water heaters.
-
New DHW system | |
---|---|
Type | decentral boiler |
Hot_water_tank | No |
With heat recovery | No |
Energy Efficiency
Voluntary certificates: No
Primary Energy 112,5 kWh/m2.y
Consumption_estimation_After: 51,222 kWh/y
Primary Energy
Consumption_estimation_Calculation_method: NA
Consumption_estimation_Including_DHW: Si
Consumption_estimation_After: 112,5 kWh/m2.y
Costs
The renovation of the old building and the construction of the extension were financed with the help of various grants: Städtebauförderung: 200.000€ E-Fond (Denkmalpflege): 230.000€ Oberfrankenstiftung: 266.000€ Bayer. Landestiftung: 150.00€
3 Mio. € (total)
Amount includes: The investment costs include both the €1.8 million for the renovation of the old building and the €1.2 million for the new building.
No