Ritterhof
Niedersonthofener Street 8
87448
Waltenhofen-Oberdorf, Germania
architetto
Contact Details
Other Information
visit of the health food store possible
Climate Zone Dfb
Altitude 741 s.l.m.
HDD 3730
CDD 47
Conservation Area:
No
Level of Protection:
Year of last renovation:
2016
Year of previous renovation:
2005
Secondary use:
Offices
Building occupancy:
Permanently occupied
Number of occupants/users:
6
Building typology:
Detached house
Number of floors:
3
Basement yes/no:
Si
Number of heated floors:
3
Gross floor area [m²]:
845,0
Thermal envelope area [m²]:
0,0
Volume [m³]:
5000,0
NFA calculation method:
NGF (de)
External finish:
Exposed woodwork
Internal finish:
Plastered (on substructure)
Roof type:
Pitched roof
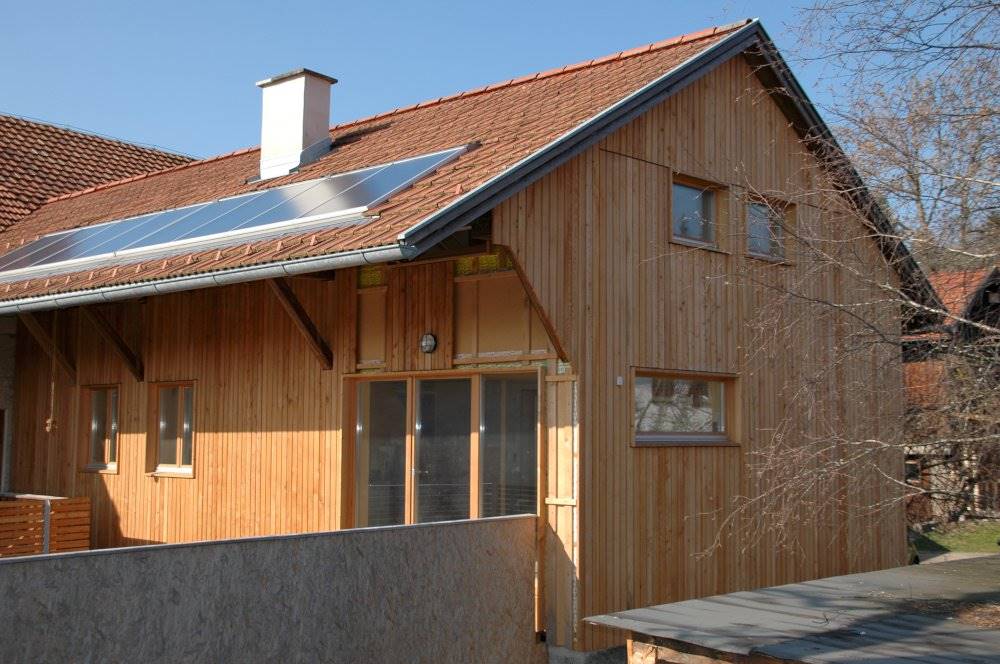
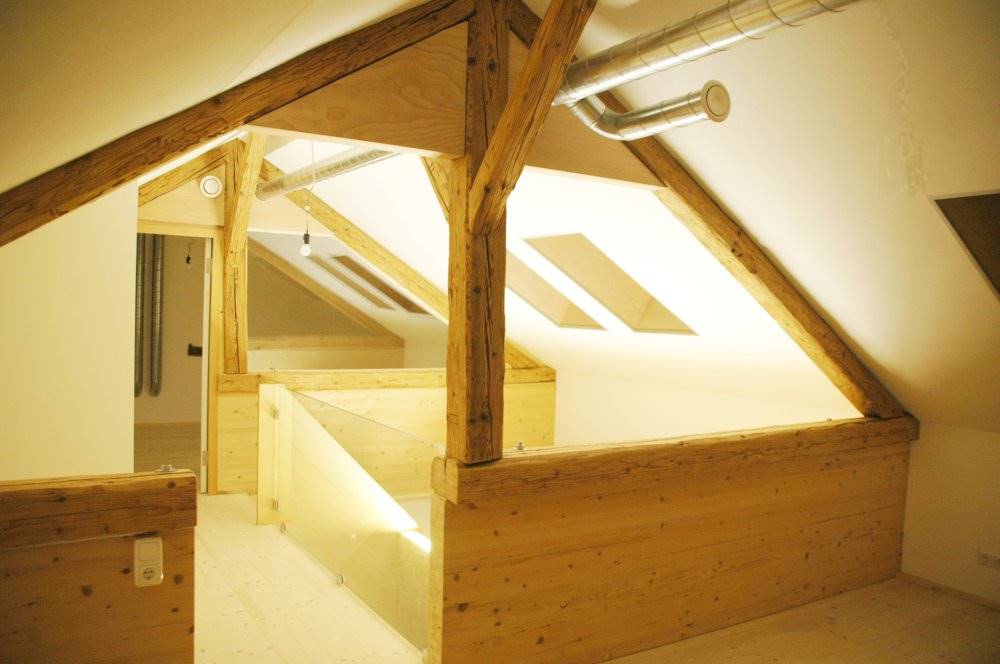

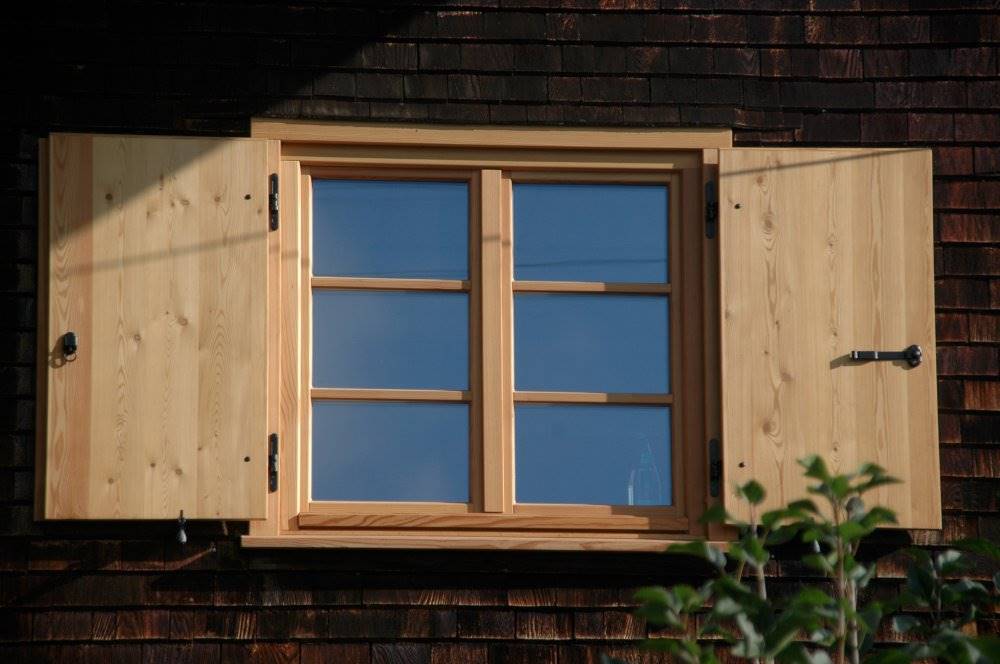
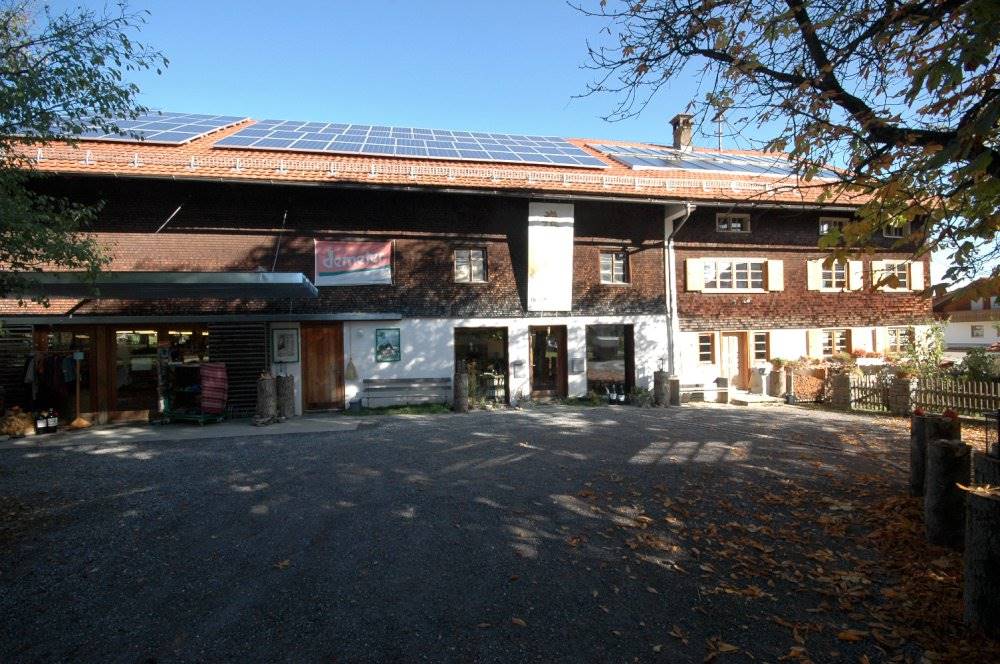
RENOVATION PROCESS
Architecture
BUILDING DESCRIPTION
State of repair
HERITAGE SIGNIFICANCE
Aim of retrofit
Michael Felkner
Niedersonthofener Straße 8, 87448 Waltenhofen-Oberdorf
felkner@architekt-felkner.de
Tel.+498379/7468
Hygrothermal assessment WUFI (Wärme- und feuchteschutztechnische Simulation)
Life Cycle Analysis (LCA) -
Other Solartechnik, Bauteiltemperierung und Passivhaustechnik
RETROFIT SOLUTIONS
External Walls
Shingled walls of the residential part
Northern wall of the residential part
Walls of the granny annexe
Quarry stone walls of the stable
Walls of the barn, today a shop
Since the shigles on the southern and western facade of the residential building were very weAfter the application of a wind paper approx. 16cm flexible wood fibre mats installed, on top of this wood boarding, clay building boards, wall radiant heating and clay plaster. This construction has the advantage that moisture can dry off both to the room and to the outside.ll preserved, these walls were insulated from the interior.
In the parlour, the only room in the 360m² house, the two outer walls remained without insulation, because the renovation revealed a beautiful old wall panelling that was to be preserved. Therefore, when installing the new windows and repairing the panelling, only the tightness was improved.
20mm
40 mm
160 mm
1 mm
160 mm
0 mm
20 mm
The plastered, almost windowless north side of the building was doubled up on the outside with squared timbers, blown out with 28 cm cellulose in between and covered on the outside with softwood fibreboard and clad with vertical wooden boarding.
This meant that no characteristic element of the building was lost, and external insulation is easier to implement in terms of building physics.
0mm
0 mm
20 mm
280 mm
160 mm
0 mm
20 mm
The annex in the north (today: granny annexe) had an externally timber-clad timber frame construction. After gutting, 9 columns remained, between which, as in the new building, new wooden stud walls were placed, which were given a stiffening and airtight planking with OSB boards on the room side. On the outside, the studs were planked with a latex-impregnated softwood fibreboard under rough-sawn larch wood formwork. On the room side, an installation level was provided and clad with economy formwork and wooden clay panels. The walls were then plastered with clay.
The former cow and horse stables are built of approx. 60 cm thick quarry stone masonry and, due to the lack of a horizontal moisture barrier, transported massive amounts of moisture upwards from the subsoil. Installing a damp-proof barrier was not an option due to the unstable statics, and injections did not seem very promising in view of the cavities between the quarry stones. The only way to dry out the masonry would be to use the so-called component temperature control system, in which 30-gram water flows through a copper pipe installed in the plinth area all year round.
Since only a small part of the masonry is an exterior wall, the heat loss is acceptable.
For the shop space, the exterior walls were completely renewed (in reinforced concrete or masonry) and well insulated on the outside.
0mm
0 mm
Windows
Windows upper floor
Window ground floor
In 2008, the windows on the upper floor were changed to triple glazing: natural larch wood windows were installed, the pitch of which is oriented towards the existing building. The circumferential reveal frame allows the layers of the wall construction to be tightly connected.
The old windows were single glazed and frost patterns regularly formed on the windows.
Existing window type | Double window |
Existing glazing type | Single |
Existing shading type | Outer shutter |
New window type | Double window |
New glazing type | Triple |
New shading type | The Ritterhof has partly rigid sun protection and folding shutters. |
New window solar factor g [-] | 0,0 |
The windows on the ground floor were replaced with double glazing in 2004.
The old windows were single glazed and frost patterns regularly formed on the windows.
Existing window type | Double window |
Existing glazing type | Single |
Existing shading type | Outer shutter |
New window type | Double window |
New glazing type | Double |
New shading type | The Ritterhof has partly rigid sun protection and folding shutters. |
New window solar factor g [-] | 0,0 |
Other interventions
ROOF
GROUND FLOOR
MEASURES TO INCREASE AIRTIGHTNESS
When the Ritterhof was acquired, the roof was leaking and had to be renewed. In 1989, the roof was renovated - in the first approach without energetic measures, and with the option of making the roof spaces usable in the future.
In the meantime, the attic of the granny flat has been developed and the roof slope has been insulated with 22 plus 8 cm of insulation. In the other areas, the top floor level remains the thermal envelope: In the block building, the ceiling to the undeveloped attic was insulated between and under the beams with soft wood fibre boards, and the ceiling above the shop and office was also insulated with 20-26 cm insulation.
0 mm
In the stable the wooden floor was removed, the soil was excavated down to the foundation level, a concrete floor slab with 20cm of thermal insulation was installed and a floor covering of OSB boards was built on top. An equivalent approach was taken with the grown floor of the barn when the shop was removed.
The false floor of the wooden beam ceiling above the natural cellar (under the residential house) was renewed and provided again with a moisture-regulating clay coating, whereby the remaining cavity was filled with wood shavings for insulation and an airtight layer of soft wood fibre boards was inserted above it. Solid wood flooring was installed throughout.
In all measures, attention was also paid to air tightness, especially at the transition from one component to another. This is illustrated here by the example of the granny annexe: During the renovation, new wooden post-and-beam walls were placed between the columns, which were given a bracing and airtight planking of OSB boards on the room side. For the floor, beams were laid on the brick cap ceiling, the spaces between them being filled with wood shavings. OSB boards also serve as the support material for the floor structure. This created a stiffening and tight envelope all around. However, the puncture points of three load-bearing beams of the roof construction detract from the result of the airtightness test, because the cracks in the old beams simply could not be made 100% tight.
HVAC
HEATING
VENTILATION
DOMESTIC HOT WATER
In the beginning, the Ritterhof was only heated with individual stoves. In 1998 a gas boiler with wall radiant heating was installed throughout the building. In 2000 the gas boiler was replaced by a log boiler. In 2018, the logwood boiler was replaced by a pellet boiler with optimized storage tank. In the residential house, the kitchen and the living room are not connected to the central heating system, as the stove there is enough to keep comfortable temperatures.
In the kitchen of the granny annexe there is a room-air-independent Greithwald cooker with heat exchanger, which heats the installation room during the heating period and enables cooking and baking at the same time. Excess heat is fed into the storage tank and reaches the other rooms via the wall-mounted radiant heating surfaces, so that the tenants only have to light a fire every other evening in winter.
New primary heating system | New secondary heating system | |
---|---|---|
New system type | Boiler | Stove |
Fuel | pellets | Wood |
Distribuition system | Radiating wall | Air |
Nominal power | 32 kW | kW |
The individual building areas are also equipped differently in terms of ventilation: The granny flat, generally renovated with passive house components, has a ventilation system with heat recovery. The architect's office is naturally ventilated (4-5 people on 100m²), but a ventilation system was considered and can easily be added.
In the shop, the 36W fan built into the wall allows excess heat to be removed from the salesroom in the morning hours during the summer and cool air to be drawn in via a supply air opening on the north-west side.
Original roof build-up | New ventilation system |
---|---|
Type ventilation system | Depending on area |
Type flow regime | NA (Natural) |
Heat recovery | No |
Humitidy recovery | No |
Nominal power | - kW |
Electric power | kW |
Control system | - |
At the beginning of the renovation measures, the Ritterhof had no connection to the sewage system.
Today, the domestic hot water is mainly heated by the pellet boiler, with a solar system supporting the heating and covering most of it in summer.
New DHW system | |
---|---|
Type | with heating system |
Hot_water_tank | Si |
With heat recovery | No |
RENEWABLE ENERGY SYSTEMS
SolarThermal
Photovoltaic
Biomass
In 1998, the Ritterhof got its first solar system with 20 m² and buffer storage (1700 l), which heats the architectural office with a solar coverage of about 70%. In 2008, as part of the renovation of the family home, this was enlarged to 40m² and the buffer storage was increased to 4850 litres (for which the obsolete gas tank was converted). The granny annexe has its own solar system with 12m² of solar panels and 700l buffer tank, hich completely covers the hot water demand outside the heating period.
The solar system is barely visible on the only slightly sloping roof.
SolarThermal System | |
---|---|
Type | Flat collector |
Collector area | 52,0 m² |
Elevation angle | 35,0 |
Azimuth | 0,0 |
Overall yearly production | 0,0 kWh |
Heating_contribuition | 0,0 kWh |
DHW contribuition | 0,0 kWh |
Cooling contribuition | 0,0 kWh |
In 2004 a PV system with 4. 4 kWp was installed and in 2008 a further one with 9. 68 kWp was installed on the southern roof.
The consumption of electrical energy is roughly congruent with the yields from the installed photovoltaic system, which is barely visible on the only slightly sloping roof.
Photovoltaic System | |
---|---|
Type | |
Collector area | 90,0 m² |
Total nominal power | 14,0 kW |
Elevation angle | 35,0 |
Azimuth | 0,0 |
Overall yearly production | 15000,0 kWh |
Heating contribuition | 0,0 kW |
DHW contribuition | 0,0 kW |
Cooling contribuition | 0,0 kW |
Lighting contribuition | 0,0 kW |
Main heating of the building is a pellet heating system
In the living area, the parlour and kitchen are heated by a basic stove and tiled stove.
The granny flat, on the other hand, is heated via the Greithwald heart (heating every other day, see HVAC).
Biomass System | |
---|---|
Type | Pellet |
Storage size | |
Origin of biomass | |
Overall yearly production | 42750,0 kWh |
Energy Efficiency
Voluntary certificates: In 2007 the Ritterhof was awarded the first place of the KfW Energy Efficiency Award “Energetic Modernization of Commercial Buildings. ” Architectural office in 3-litre standard - 33kWh/m²a solar coverage 70%. Natural food shop: no heating energy as shop, 33kWh/m²a for residential use. Granny flat with passive house technology in 3-litre standard: dena model project Factor 10 refurbishment.
Consumption_estimation_Calculation_method: Derived from energy bills
Consumption_estimation_After: 60 kWh/y
Primary Energy
Consumption_estimation_Calculation_method: Derived from energy bills
Consumption_estimation_Including_DHW: Si
Consumption_estimation_After: 12 kWh/m2.y
Internal Climate
Thanks to the renovation, the rooms are now evenly warm, due to the well-insulated basement ceiling. The wall jet heaters on the well-insulated exterior walls in combination with the mud plaster create a particularly pleasant atmosphere.
In order to achieve good air quality, regular ventilation is required, as there is no ventilation system and the new windows are airtight.
The house is not comparable with a new building (in timber construction) in terms of sound insulation.
Costs
Various funding for the renovation. In 2005, the architect received an award from dena (German Energy Agency) for the renovation of the granny annexe and the return above the former horse stable.
No