Villa Castelli
23822
Bellano (LC), Italia
architetto
Owner
User
Contact Details
Other Information
International Passive House Conference Leipzig 2015: „Umfassende energetische Modernisierung einer denkmalgeschützten Villa am Comer See“ Interior Insulation Congress Dresden 2015: „Energetische Sanierung von Baudenkmalen am Beispiel Sanierung der Villa C
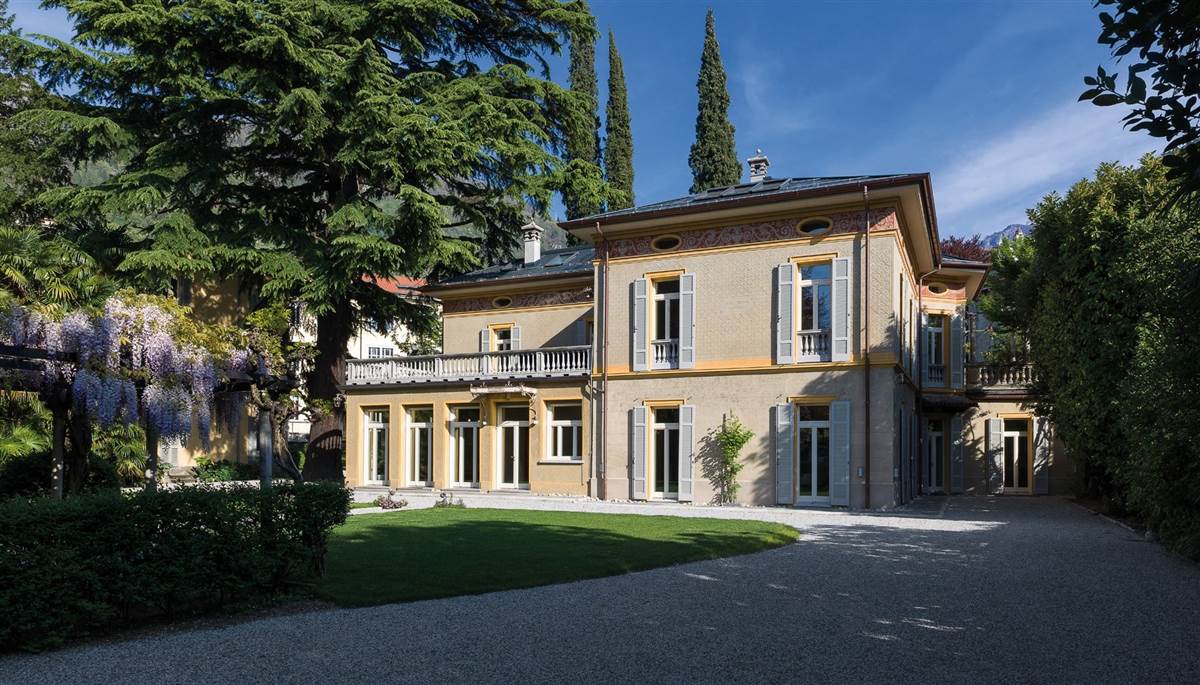
Climate Zone Cfb
HDD 1453
CDD 99
Conservation Area:
Si
Level of Protection:
Building worth preserving (vincolo architettonico) and situated in a protected area (vincolo paesaggistico).
Year of last renovation:
2013
Year of previous renovation:
1939
Secondary use:
Residential (rural)
Building occupancy:
Permanently occupied
Number of occupants/users:
4
Building typology:
Detached house
Number of floors:
3
Basement yes/no:
No
Number of heated floors:
3
Gross floor area [m²]:
680,0
Thermal envelope area [m²]:
1269,91
Volume [m³]:
2606,24
NFA calculation method:
Useful area (it)
External finish:
Rendered
Internal finish:
Plastered (on hard)
Roof type:
Pitched roof
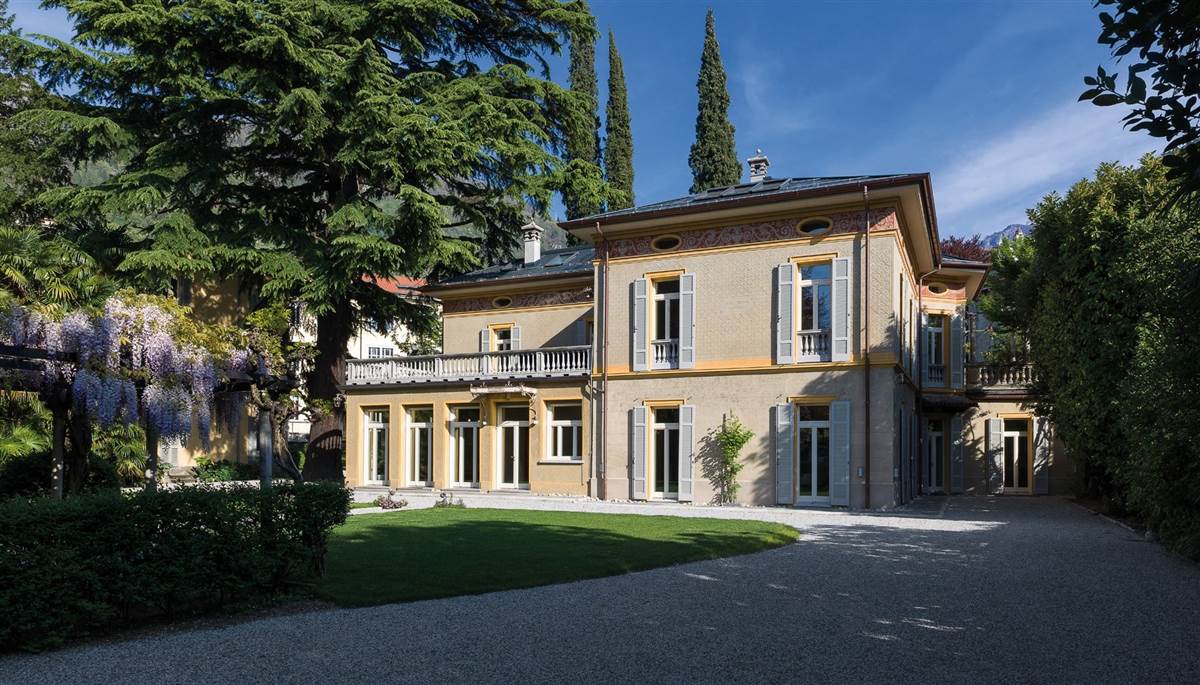
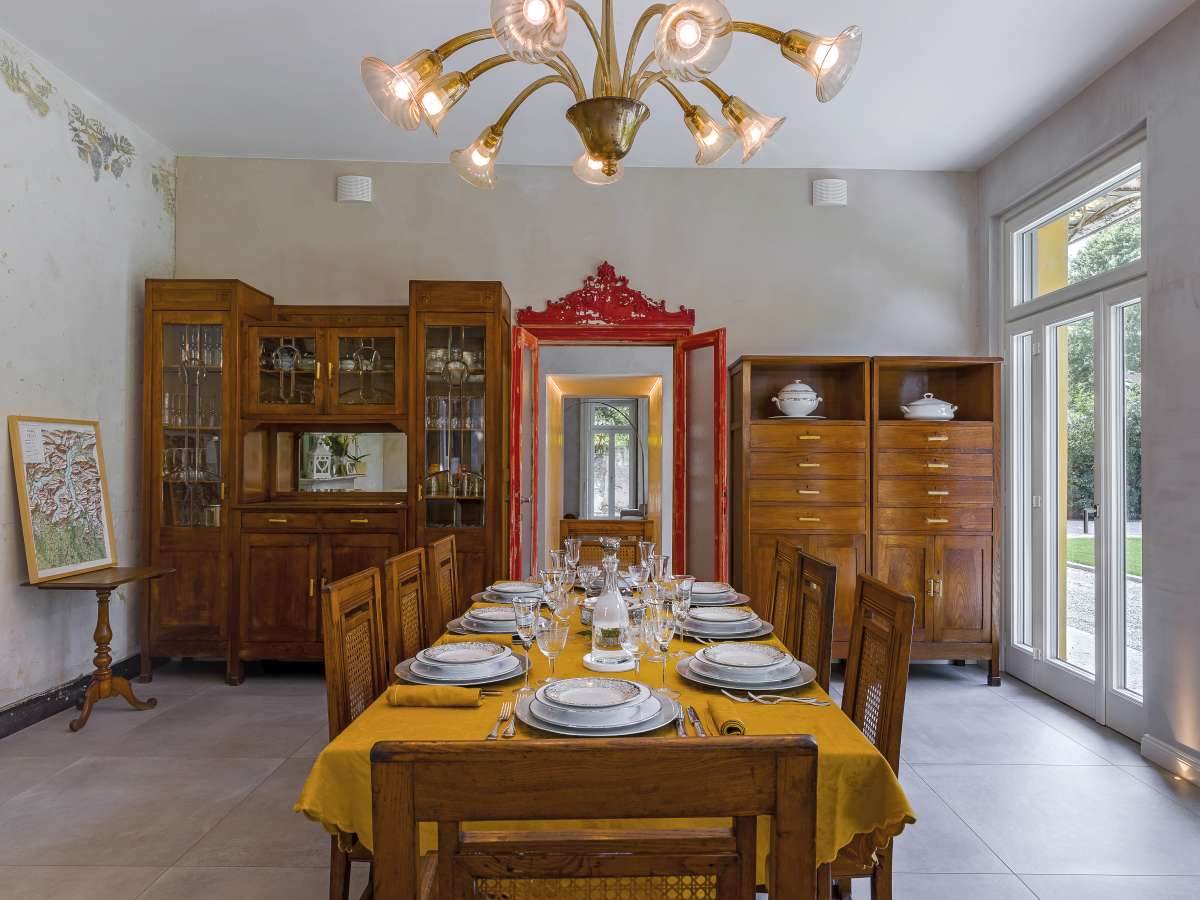
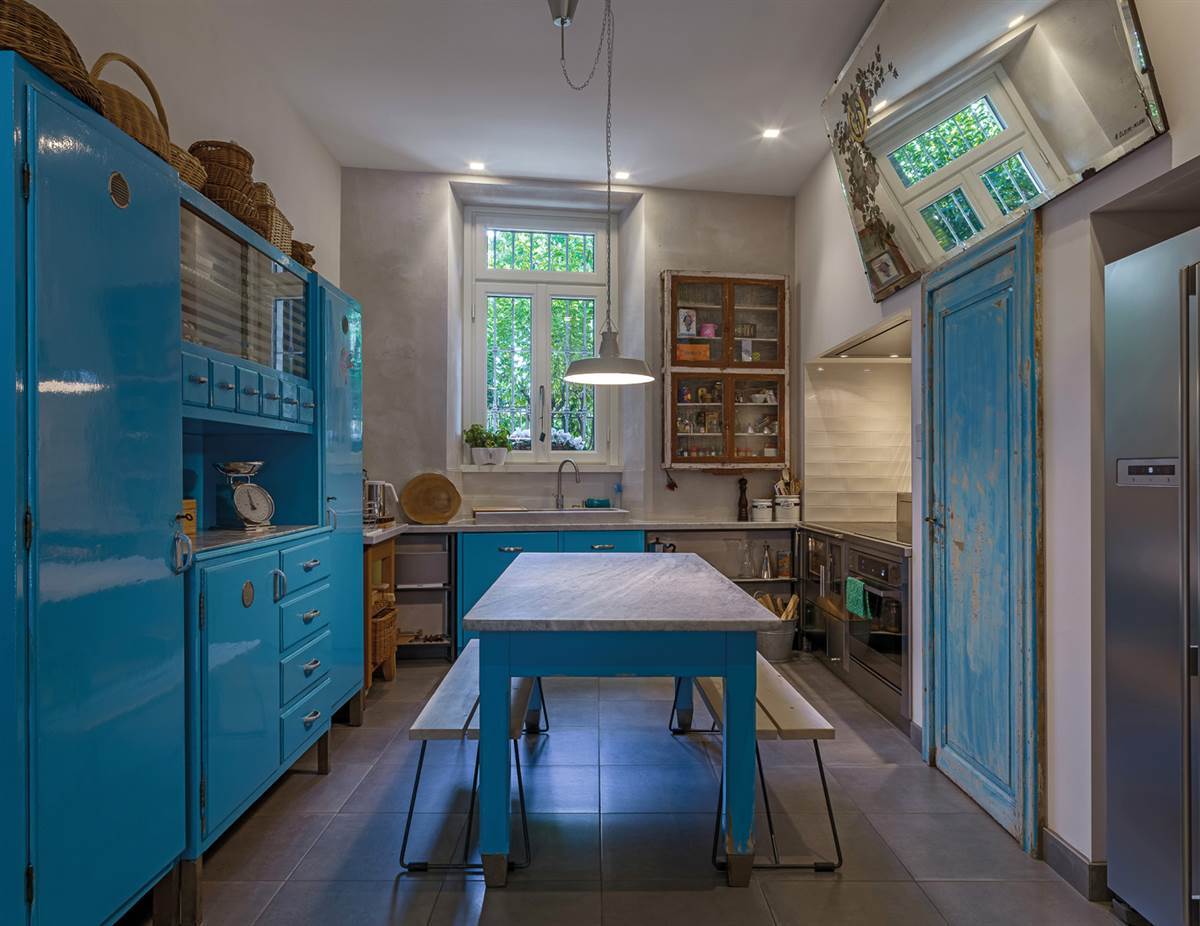
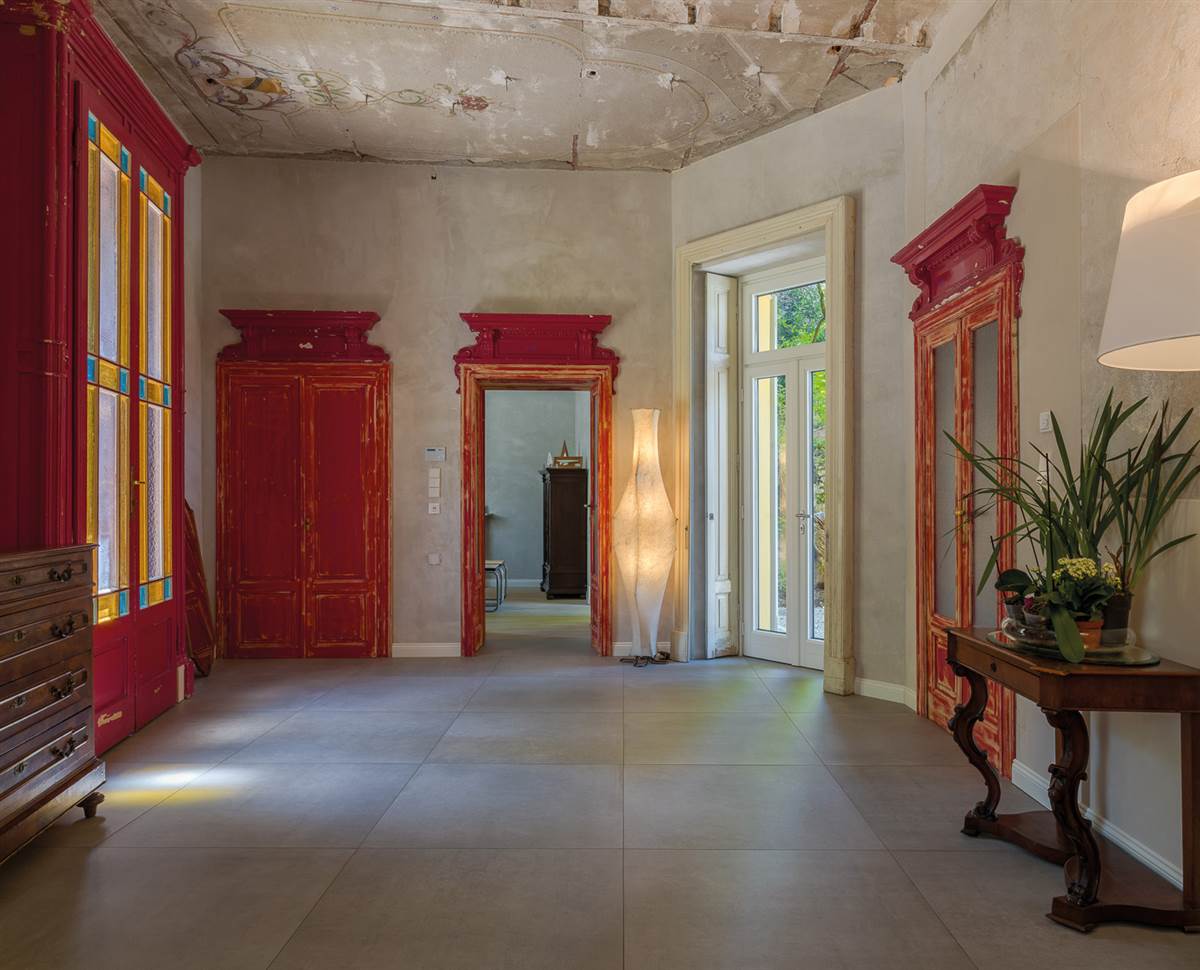
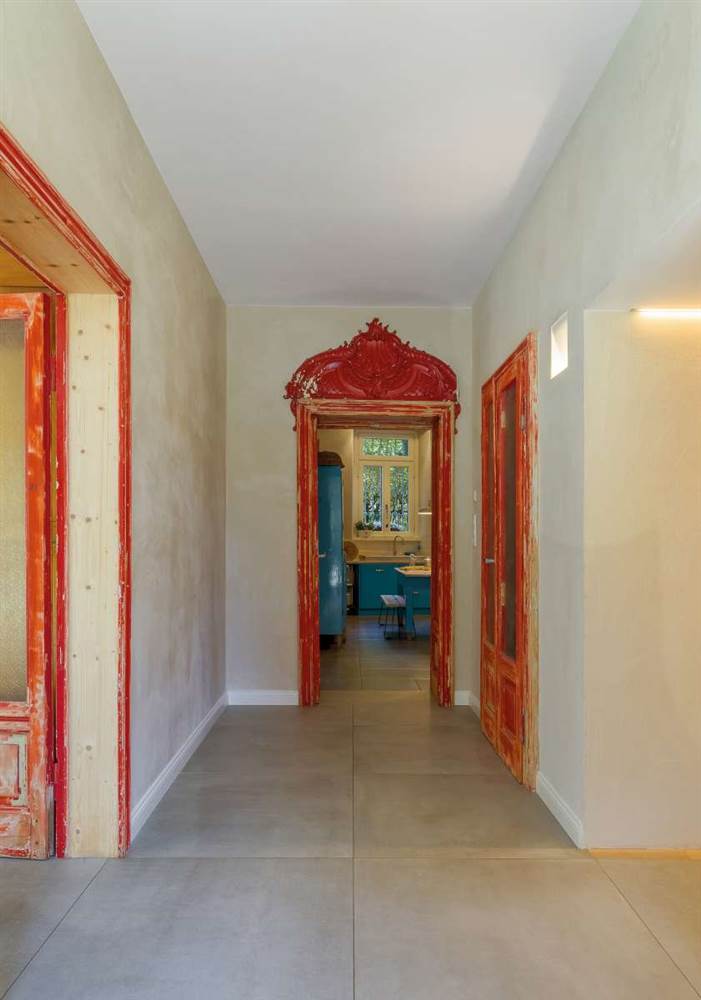
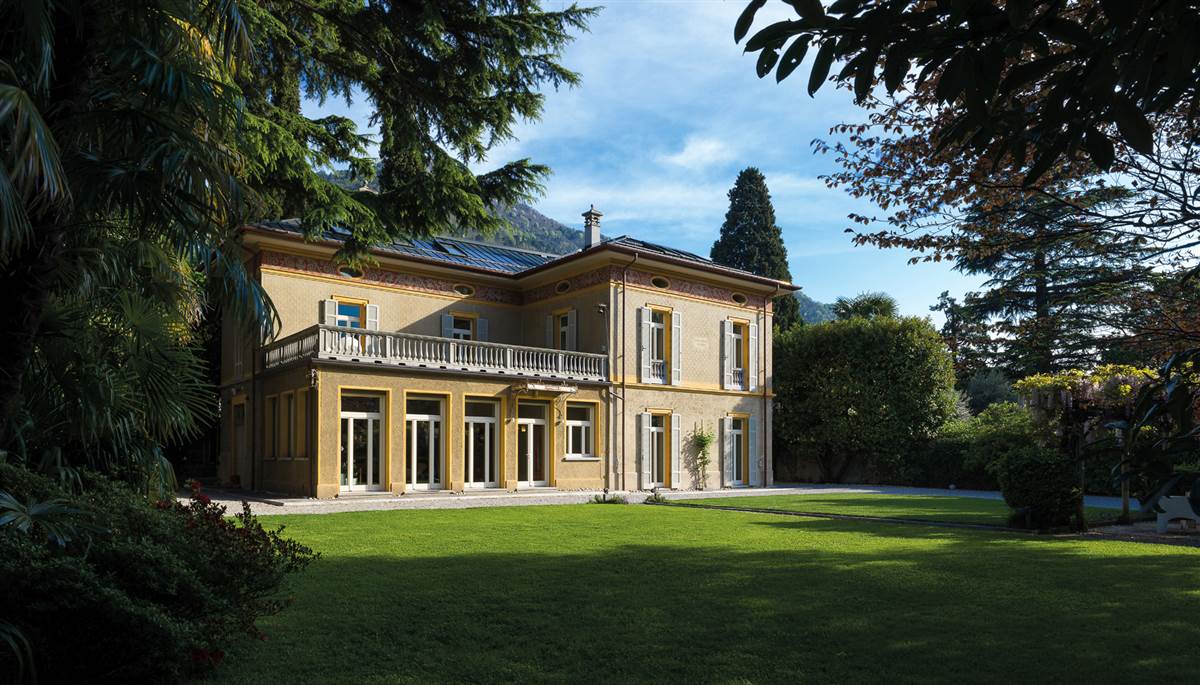
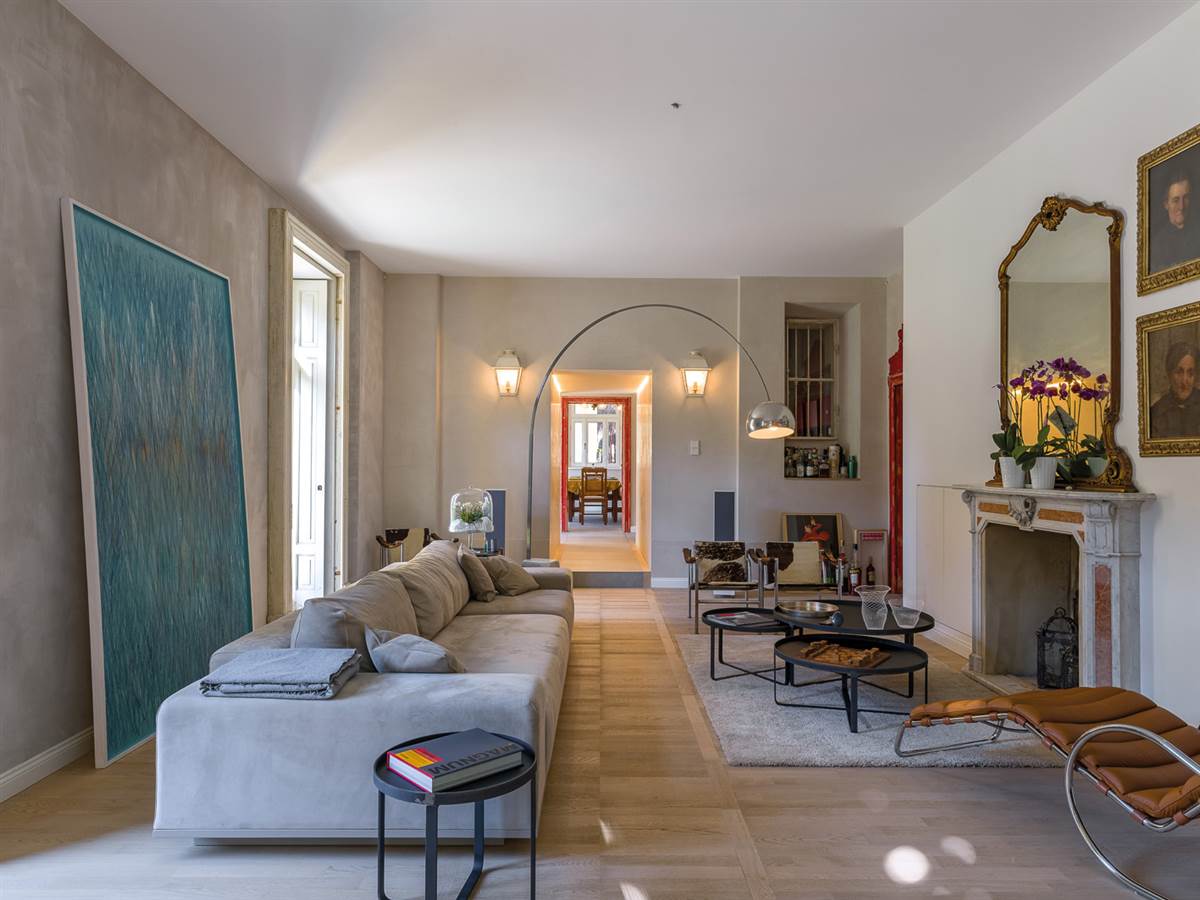
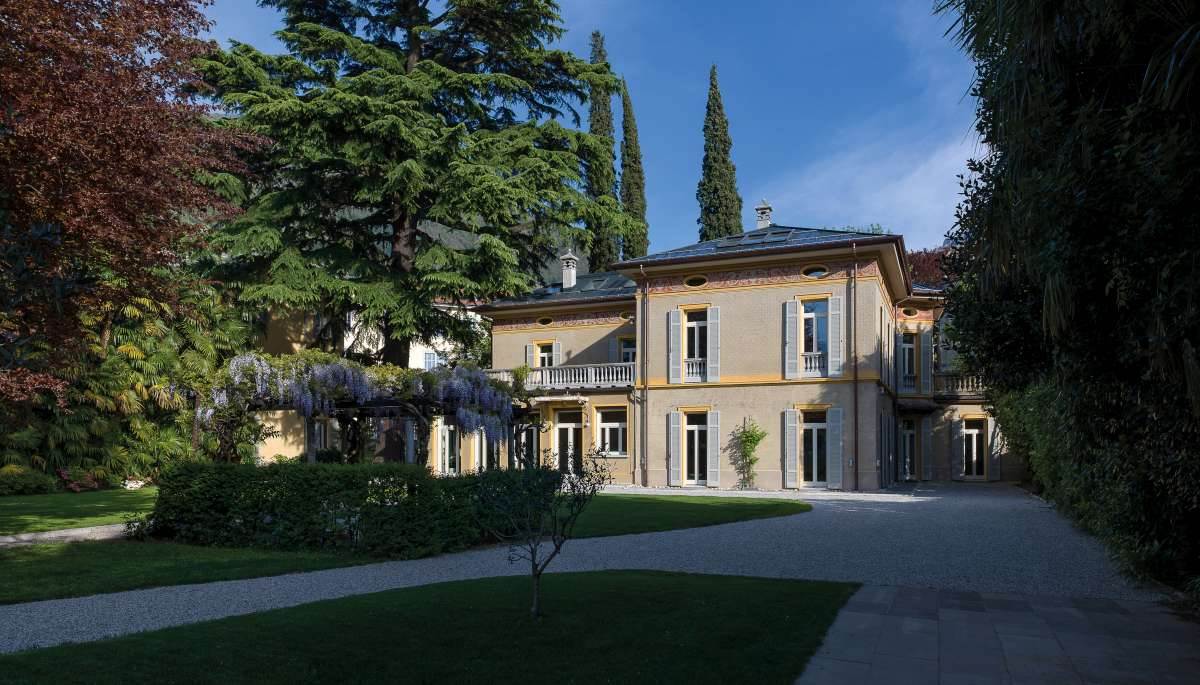
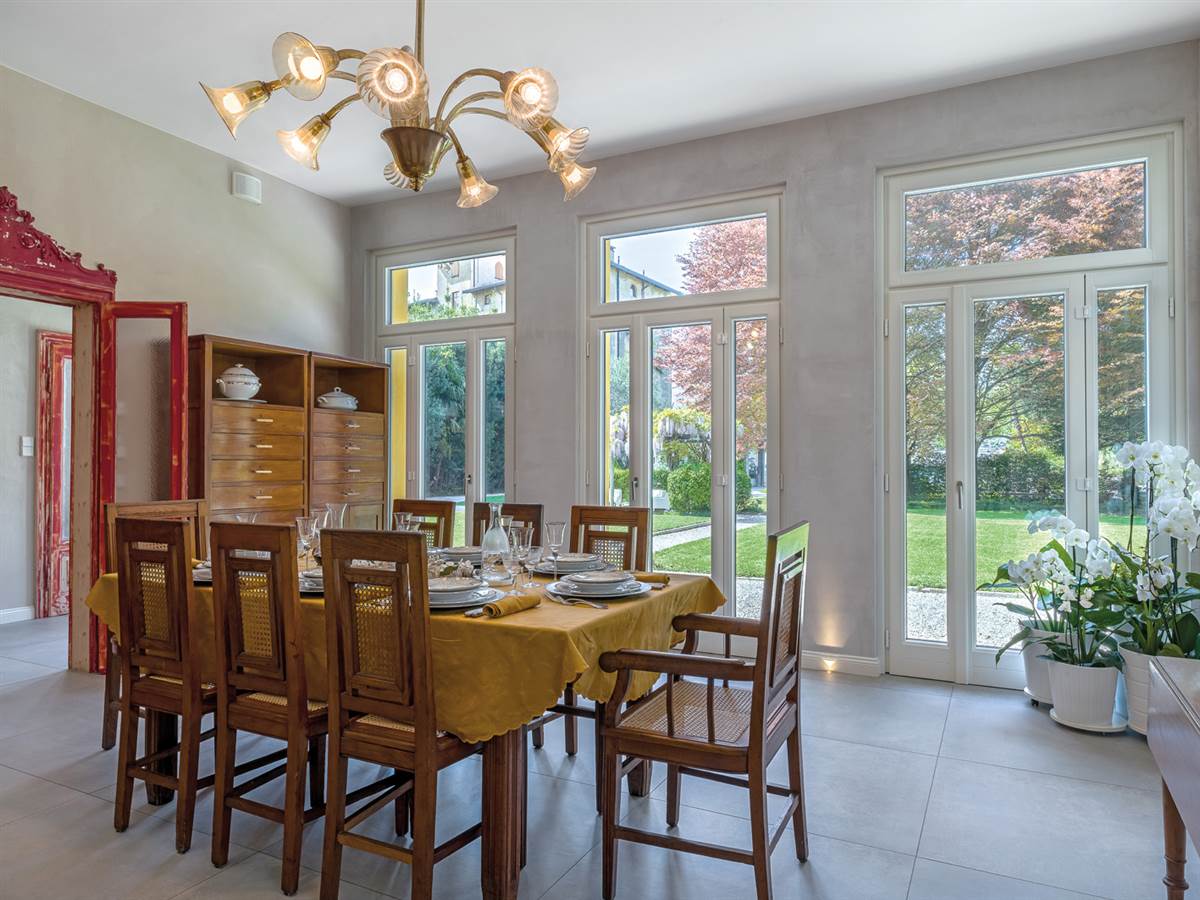
RENOVATION PROCESS
Architecture
BUILDING DESCRIPTION
State of repair
HERITAGE SIGNIFICANCE
Aim of retrofit
EURAC research, Institute of renewable energies, research group: retrofit of historic buildings
Via A. Volta 13/A, 39100 Bolzano (BZ), Italy
alexandra.troi@eurac.edu
Tel.+39 0471 055602
Valentina Carì
Via Loreti 4, 23822 Bellano (LC), Italy
tiacari000@gmail.com
Tel.+39 0341821602
x
x
Oscar Stuffer "Solarraum - architecture, energy, mobility"
Via Goethe 3, 39100 Bolzano (BZ), Italy
info@solarraum.it
Tel.+39 0471 707064
Vincenzo Buizza “Studio di Ingegneria Tecnica"
Corso Martiri della Liberazione, 6 23900 Lecco LC
vb@ingbuizza.it
Tel.0341 363915
Hygrothermal assessment WUFI, Delphin
RETROFIT SOLUTIONS
External Walls
Exterior wall in natural stones + perlite insulation (type 1)
Concrete wall + aerogel insulation (type 2)
Wall in solid brick + perlite insulation (type 3)
The exterior wall in local natural stone masonry with lime mortar was insulated from inside with 20 cm perlite, applying on the existing lime plaster layer another layer of lime plaster as leveling layer, the glue, the perlite insulation panel and the interior plaster. For the wall construction with internal insulation the moisture transport was simulated (WUFI). In addition, all nodes were designed and planned in detail with special attention to air tightness, vapor diffusion and convection.
The appearance of the facades should not be changed from conservator´s point of view. This constraint, in addition to the beauty of the exterior surfaces, which were still very well preserved, were the base of the decision for an insulation on the inner surfaces of the exterior walls. In this way, although being aware of the difficulty to avoid thermal bridges, a conservation compatible solution for the opaque parts could be found, as the internal insulation did not alter the exterior building appearance.
40 mm
410 mm
40 mm
40mm
410 mm
40 mm
30 mm
10 mm
200 mm
10 mm
Where it was geometrically not possible to install the 20 cm thick perlite insulation layer, 8 cm of Aerogel were applied as internal insulation (e.g. to the concrete wall of the staircase). The internal insulation of the exterior walls has followed the criteria to standardize the thicknesses of the insulation layers. A difference has been made in the area e. g. of the veranda in order to not alter the very thin architectural shape: while the majority of the walls the insulation is of 20 cm perlite, in the area of the veranda, it was planned to cover the pillars of reinforced concrete with a high-performance material with reduced thickness, such as aerogel.
x
40 mm
310 mm
40 mm
40mm
310 mm
40 mm
30 mm
10 mm
80 mm
10 mm
Also those parts of the exterior wall in solid brick stone masonry was insulated from inside with 20 cm perlite, applying on the existing lime plaster layer another layer of lime plaster as leveling layer, the glue, the perlite insulation panel and the interior plaster.
x
40 mm
310 mm
40 mm
40mm
310 mm
40 mm
30 mm
10 mm
200 mm
10 mm
Windows
All windows
The windows and doors have been substituted with high energy performance system. Triple glazing filled with Argon, casing in a wood-aluminum frame, reduce the thermal losses through the windows system. Thanks to the low solar heat gain coefficient of the glazing system, the solar radiation can be controlled during the summer period, guaranteeing a high indoor comfort for the users.
The original windows were not of heritage value from conservators point of view and could be replaced with a new energy-efficient window. The new windows were handmade by a carpentry as wood-aluminium windows. Input requirement of the heritage authority was to maintain the original layout of the windows (so the number of sashes - in case e.g. of the veranda windows 4 sashes), while the original proportions (relation glazing-wood/frame thickness) was not considered. The interventions foresaw the renovation and repositioning of the original decorated interior doors and window frames with the aim to assure the original building appearance it had and craftsmanship. In particular, the “window furniture”, an ornate wooden construction framing the window with shading elements that can be folded into the door reveal.
Existing window type | Casement window |
Existing glazing type | Single |
Existing shading type | Outer shutter |
Approximate installation year | 1925 |
New window type | Casement window |
New glazing type | Triple |
New shading type | Outer shutter |
New window solar factor g [-] | 0,58 |
Other interventions
ROOF
GROUND FLOOR
OTHER
MEASURES TO INCREASE AIRTIGHTNESS
The roof has been completely replaced with a new structure in laminated wood, with a package of insulation of 32 cm, consisting of 18 cm cellulose fiber between the rafters, 8 cm of wood fiber boards and 6 cm rock wool (fire protection under the photovoltaic system) on the rafters. In the course of renovation, also the roofing, originally roof tiles "monk and nun", was replaced with a metal roof in aluminum. The roof skin, double-crimped aluminum sheets hosts a mono-crystalline photovoltaic plant (see also RES).
x
40 mm
60 mm
80 mm
20 mm
180 mm
18 mm
1 mm
12 mm
The insulation of the floor slab against ground was carried out with 20 cm XPS lying on a 15 cm thick layer of lean concrete. Above the insulation layer, the installation level is located in a light, fast-drying subfloor (Lecacem) of 12 cm on which the floor heating system with expanded polystyrene (ISODOMUS) and the parquet are posed.
x
40 mm
15 mm
150 mm
1 mm
200 mm
120 mm
1 mm
75 mm
15 mm
Restauration: The façade has been completely restored according to the input requirements of the heritage authority: cleaned, consolidated (acrylic resin with brush and syringe), missing parts supplemented in original technique. For a perfect function of the internal insulation special care was taken to close all joints and cracks. Sealing: The exterior walls have been sealed, injecting at high pressure a micro emulsion of concentrated silicones into regular drilled holes at a height of about 0,5 m above the interior floor level. The horizontal sealing of the baseplate was then pulled up on the interior sides to the level of horizontal cut in the exterior walls. Static consolidation: In order to consolidate the building statically, in certain areas the existing ceilings were removed and replaced by timber-concrete composite slabs, which distribute the loads better and reinforce the building itself. Detail planning/hygrothermal simulation: Based on the holistic pre-intervention survey, the individual components and junctions were analyzed and solutions were developed within an integrated design process, which included energy efficiency as well as thermal bridges, the correct humidity behavior, architectural aspects and static specifications (earthquake resistance!). The critical points in the design planning as well as in the execution of the construction work were certainly the high number of different nodes (about 30 pcs.). To simplify the design as much as possible, the planning was limited to two internal insulation thicknesses (20 cm perlite and 8 cm aerogel, where geometrically required). The moisture transport in the wall construction was simulated for both interior insulations (with WUFI). In addition, all knots were planned in detail and with special attention to airtightness, vapour diffusion and convection.
x
An airtight building envelope was important in two respects: firstly, to ensure that the interior insulation was not damaged in the long term and secondly to limit ventilation losses in view of the location exposed to the wind. The installation of a comfort ventilation system ensures optimum air hygiene (primarily CO2 concentration, but also room humidity). Particularly when using internal insulation, a continuous layer airtightness layer all around the building envelope is crucial in order to avoid condensation of warm room air behind the internal insulation or in construction nodes. In case of the external wall, the internal plaster forms the airtight layer, whereas on the underside of the roof the vapor barrier under the internal gypsum plasterboard and on the baseplate a foil under the subfloor on the XPS insulation forms the airtightness layer. In all points where this continuous air-tightness layer is interrupted/penetrated, e.g. by ceiling beams, detailed solutions were be sought individually to guarantee air-tightness.
HVAC
HEATING
VENTILATION
AIR CONDITIONING
DOMESTIC HOT WATER
A heat pump with a geothermal plant (probes) supplies the production of heating and cooling and hot water. The heat for heating is distributed to the rooms through a radiant floor system.
New primary heating system | |
---|---|
New system type | Heat pump |
Fuel | Electricity |
Distribuition system | Radiating floor |
Nominal power | 14 kW kW |
A mechanical ventilation system with heat recovery was installed. It guarantees a pollen-free, healthy indoor environment and improve the comfort indoor for the users. It controls the air humidity in the rooms, given that the building is lying in a zone closed to the lake. A set of CO2 sensors regulates automatically the air exchanges and the heat exchanger allows a further reduction of the building energy demands. The mechanical ventilation system is centralized at each floor, in order to guarantee the independency of each flat. Thus, three centralized comfort ventilation units with 480m³/h per unit and a heat recovery of 87% (according to the passive house certificate) were installed.
Original roof build-up | New ventilation system |
---|---|
Type ventilation system | Centralized |
Type flow regime | |
Heat recovery | Si |
Humitidy recovery | No |
Nominal power | kW |
Electric power | kW |
Control system | CO2 sensors |
The heat pump also supplies the air conditioning. It must be emphasized that the specific power of cooling is very low (soft cooling) in order to avoid condensation in the floor structure.
New cooling system | |
---|---|
Type | Heat pump |
Distribuition system | Radiating floor |
Nominal power | 14 kW kW |
Electric power | kW |
RENEWABLE ENERGY SYSTEMS
Photovoltaic
WindEnergy
Geothermal
The remaining energy demand had to be covered locally and in a renewable way. Electrical energy is produced with a PV-system, integrated in the roofing and not visible from outside. Before the heritage authorities approved the PV system, several prototypes were developed for a roof-integrated and preferably invisible installation. The heritage authorities opted for the double-curled aluminum sheet covering of the roof - which is quite common for buildings of this age in a similar way - with integrated mono-crystalline PV modules, folded plates with integrated photovoltaic cells, of about 11 kWp. A sailboat outfitter supplied the extra-thin PV modules.
The heritage office in charge of the project has evaluated as fundamental criteria: (i) the aesthetic characteristics of the panels (color and surface finish); (ii) their geometric arrangement in relation to the shape of the roof surface and the orientation of the building (shape of the plant, modularity); (iii) the adherence and coplanarity to the roofing; (iv) the non-reflective surfaces; (v) the perceptibility from around, with particular reference to the road, lake and circus-standing landscape level. The design of the panel respects the triangular or trapezoidal shape of the roof surface, trying to promote as much as possible the perception of a homogeneous coating of the entire surface. All the panels have the same orientation, consistent with the general orientation of the building, in order to minimize their perceptibility from around.
Photovoltaic System | |
---|---|
Type | Monocrystaline |
Collector area | m² |
Total nominal power | 11,0 kW |
Overall yearly production | 0,0 kWh |
Also micro wind turbines installed on the roof contribute to the production of electricity.
WindEnergy | |
---|---|
Type | |
Position in relation to building | |
Total_nominal_power | kW |
Overall_yearly_production | kWh |
Energy Efficiency
Voluntary certificates: No
Primary Energy 32,4 kWh/m2.y
Consumption_estimation_Before: 230,19 kWh/m2.y
Consumption_estimation_After: 18,27 kWh/m2.y
Primary Energy
Consumption_estimation_Calculation_method: Steady state simulation (e.g. EPC, PHPP)
Consumption_estimation_After: 32,4 kWh/m2.y
Internal Climate
General comment of the building owner with regard comfort and costs: “Expenses of 3.800,00 € per year only for heating and hot water, in addition often the use of 2 fireplaces, nevertheless a temperature of 17.7 ° C was never exceeded. On days after there was strong wind from the north, we had to put on a jacket in the house. A very particular experience. The kitchen was supplied with gas. After the first year in the renovated house, from February 2015 to February 2016, with the first months of increased consumption (cold house and doors that were constantly opened to complete the construction work), we spent 2.400,00 euros on electricity (all'inclusive!). We are satisfied with that. For 680 m² in a super-comfortable house (20 °C and controlled CO₂ content), with external hydromassage and Turkish steam bath (which also consume electricity). In the second year, we expect to spend even less.”
Costs
In total, the costs for the renovation of the three-storey villa amounted to € 1.5 million - at around € 2,200/m² gross floor area; this corresponds roughly to the new construction costs for a building of the same quality standard in this region. However, the clients receive a clear benefit compared to the new building: a villa with modern living comfort and historical charm in the Park am See. The masonry works and the interior finishing accounted for a considerable part of the costs. The work included on the one hand the static consolidation and on the other hand internal work to change the room layout according to the client's wishes. The plant technology also had a major impact, as the entire heat generation and distribution as well as the sanitary technology were renewed.
2.200,00 Euro/m² (per m2)
Amount includes: The total costs include project planning costs, interior construction and masonry work, refurbishment and renovation, thermal insulation, windows and shading, roof, building services, furniture and other.
Cost of energy related interventions:
570,00 Euro/m² (per m2)
Amount includes: The costs for the energetic renovation amounted to total 388.000,00 Euro, around 570 €/m² (gross floor area), about 26 % of the total costs. They include a part of the project planning costs, all thermal insulation measures (including work), the new windows and the energy efficiency components of the system technology (ventilation system, geothermal system, heat pump and PV system).
Winter 2016/2017: 1.800,00 Euro (total energy costs including lighting) (total)
Lifecycle cost
No