Platzbon
Rutzenberg 41
39042
Brixen, Italia
architetto
Owner
Contact Details
Other Information
Use as residential house and holiday apartments - www.platzbon.it
http://itaspreis.gruppoitas.it/die-gewinner-2017/
Climate Zone F
Altitude 1330 s.l.m.
HDD 3214
CDD 0
Conservation Area:
No
Level of Protection:
Year of last renovation:
2016
Year of previous renovation:
1970
Secondary use:
Agricultural & Fishery
Building occupancy:
Permanently occupied
Number of occupants/users:
4
Building typology:
Tenement (apartments)
Number of floors:
3
Basement yes/no:
Si
Number of heated floors:
3
Gross floor area [m²]:
435,0
Thermal envelope area [m²]:
699,0
Volume [m³]:
1196,5
NFA calculation method:
NGF (de)
External finish:
Rendered
Internal finish:
Exposed woodwork
Roof type:
Pitched roof
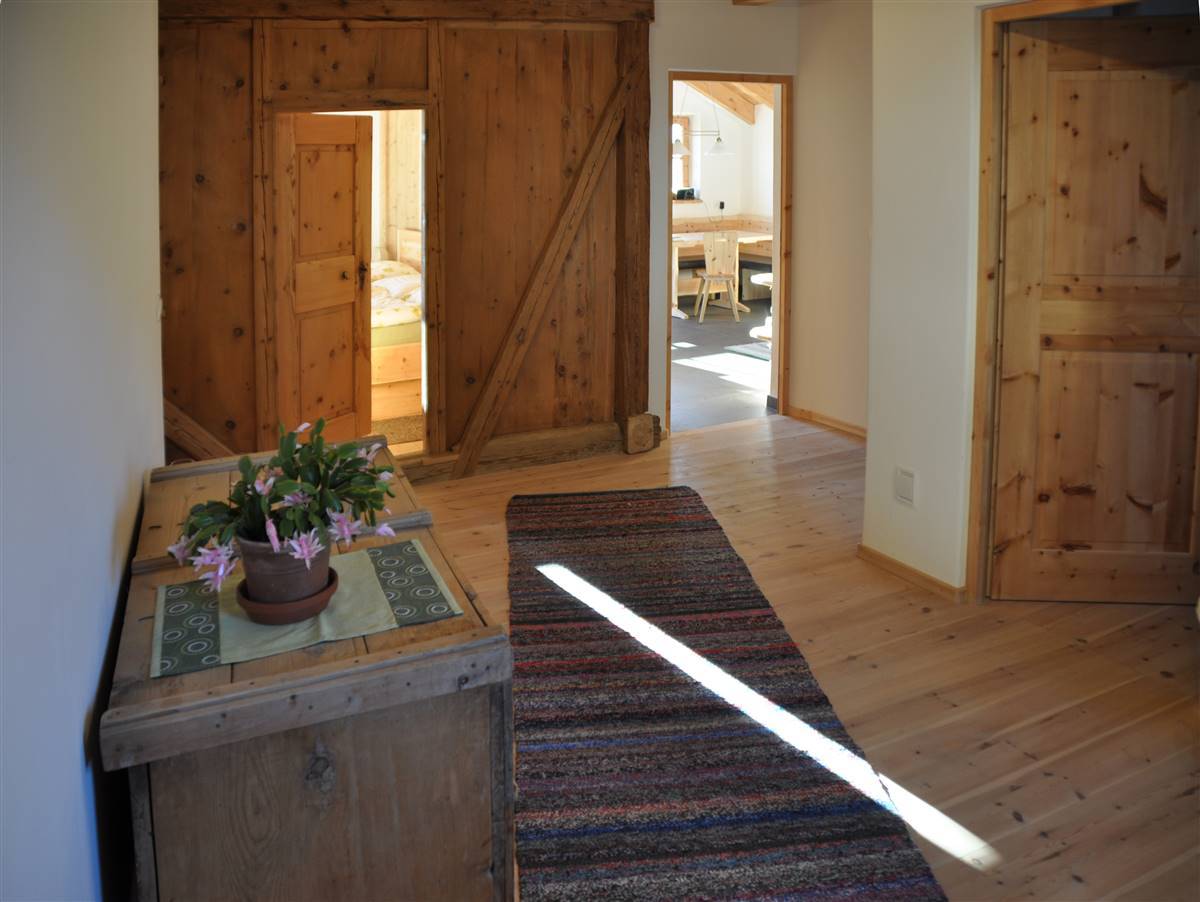
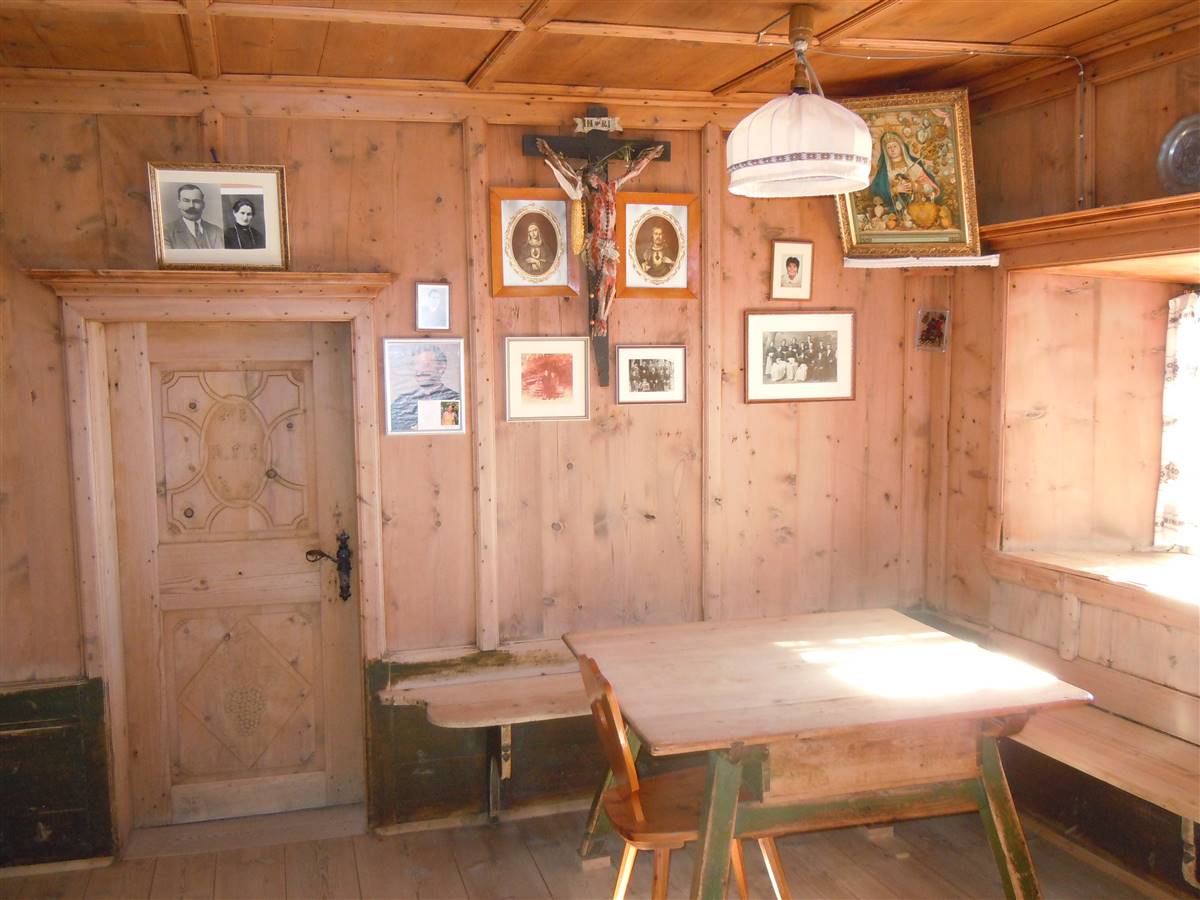
.jpg)
.jpg)
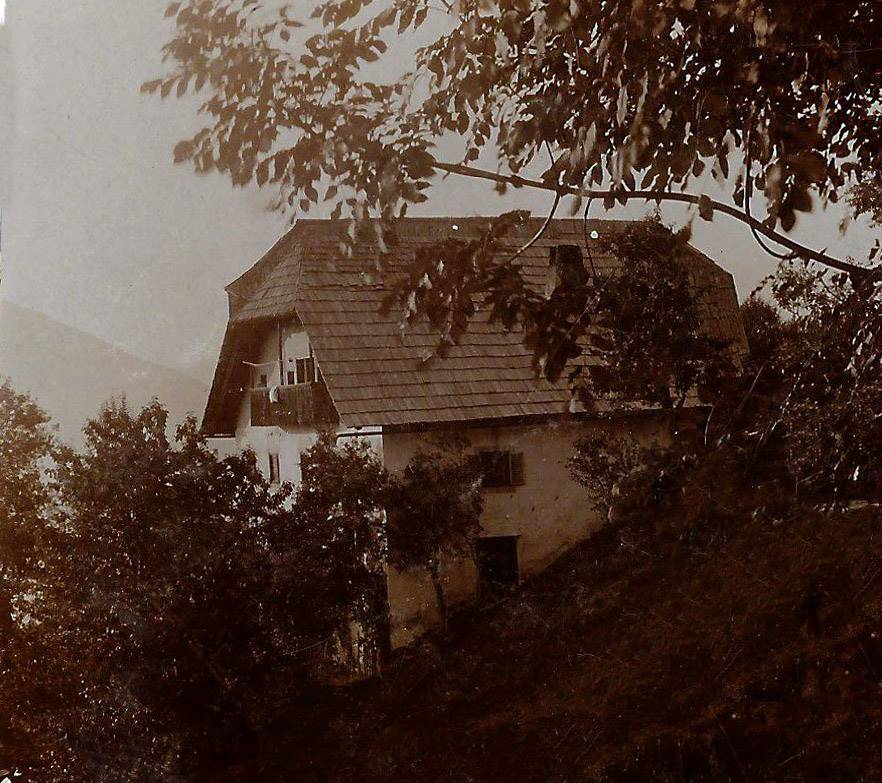
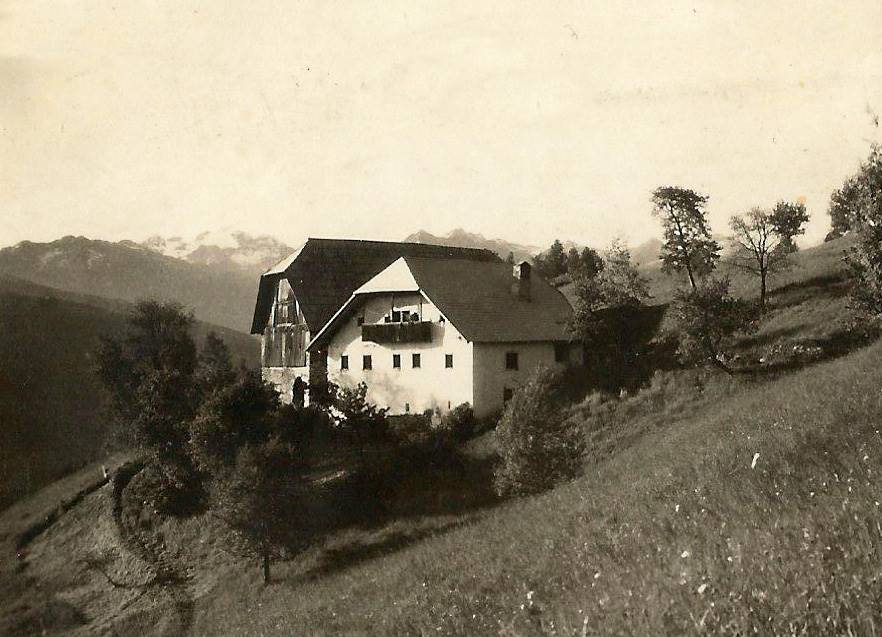
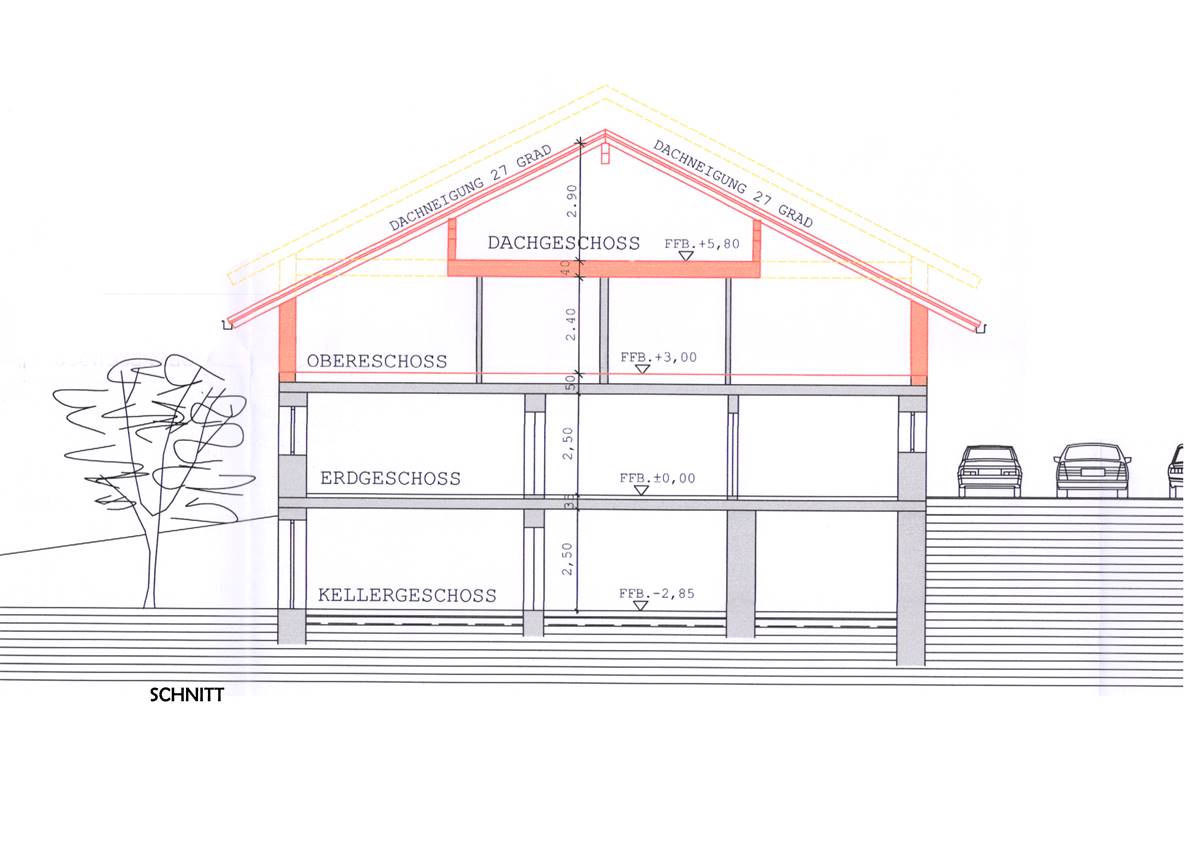
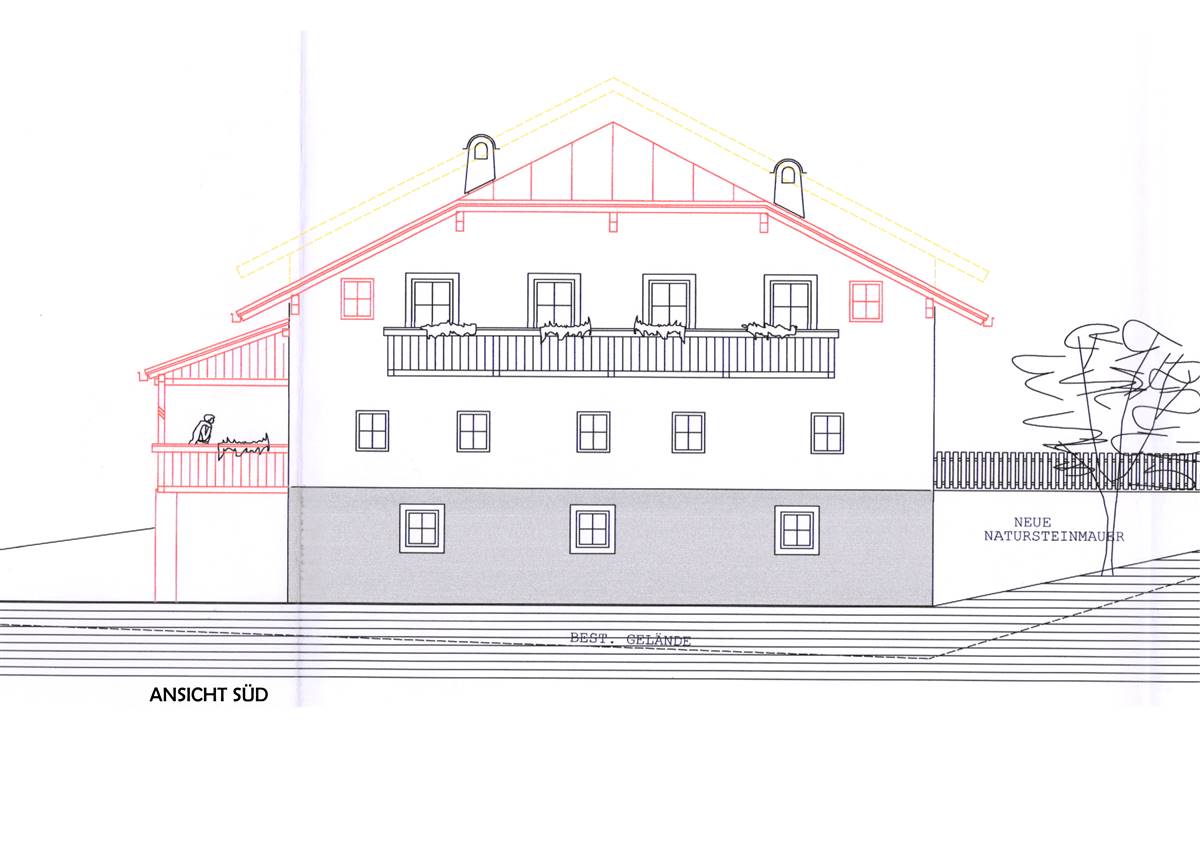
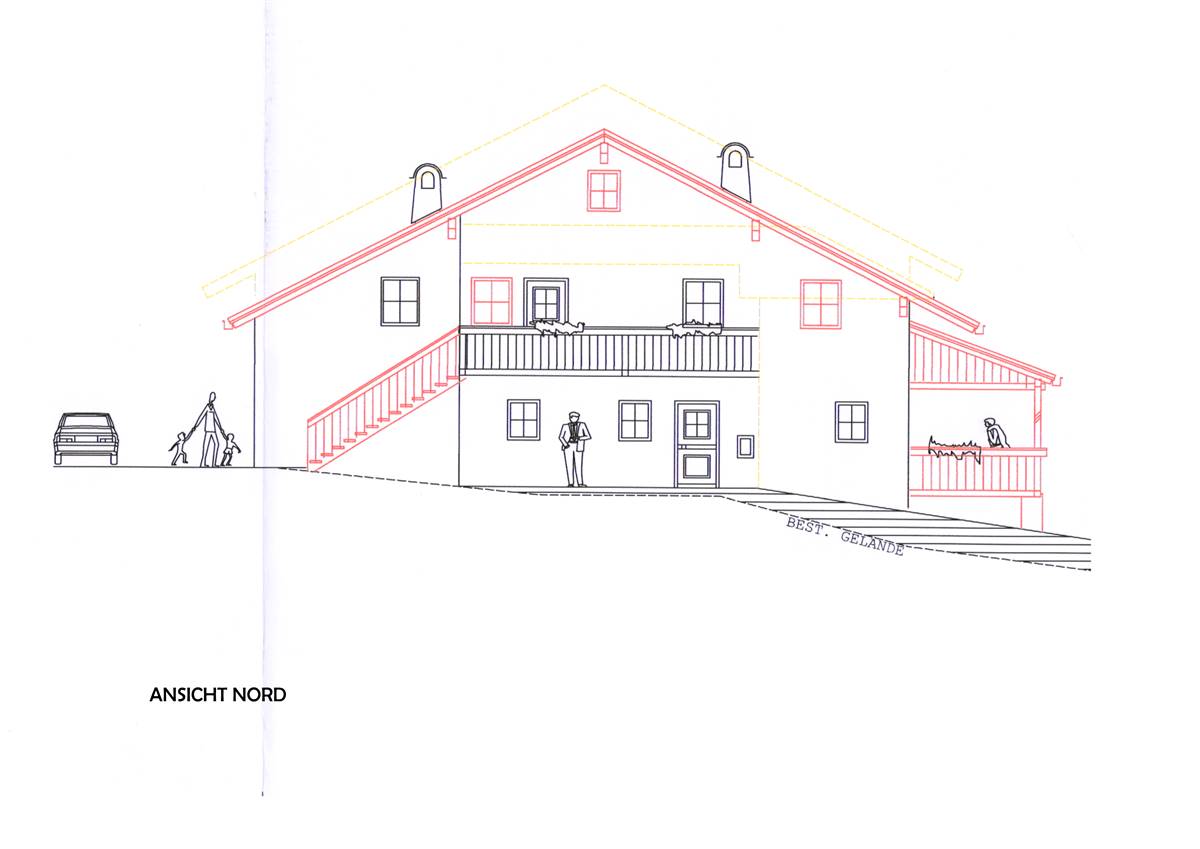
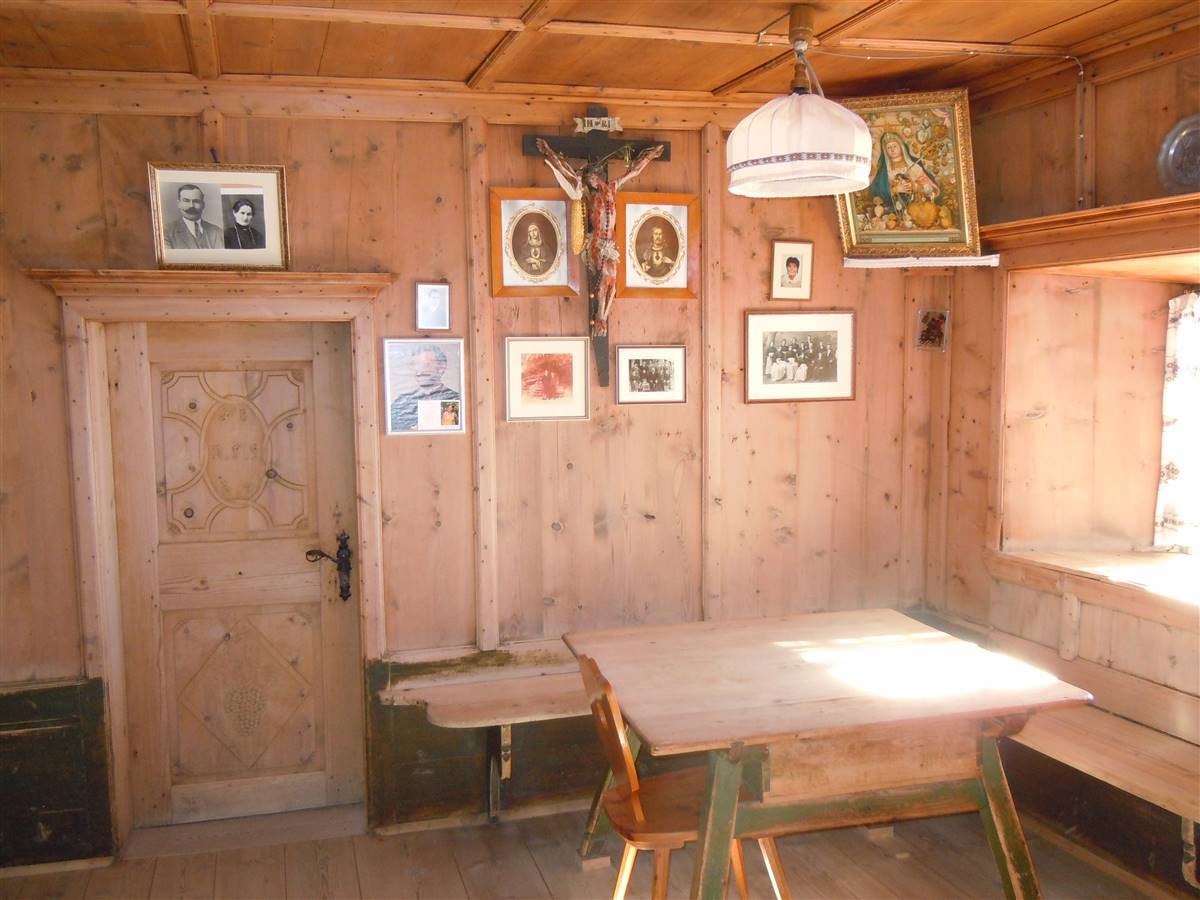
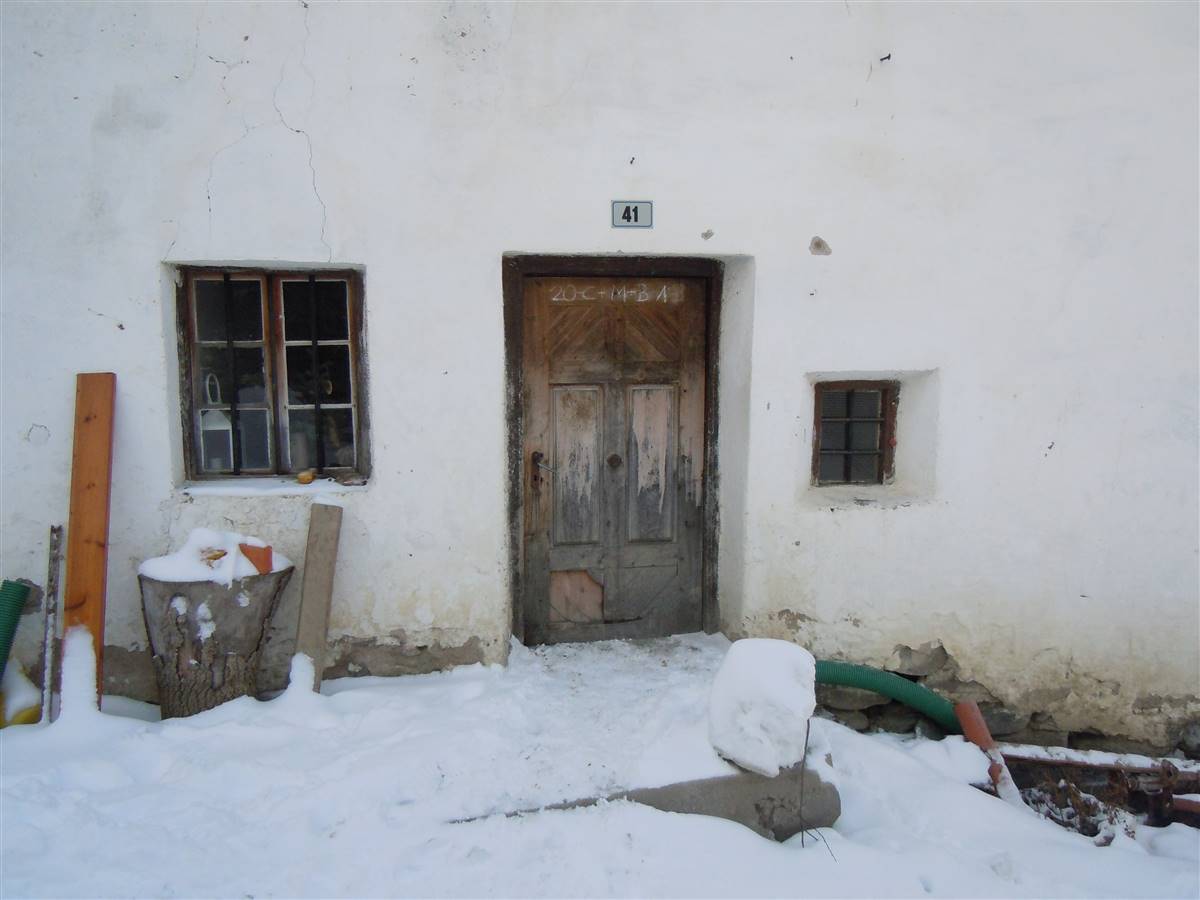
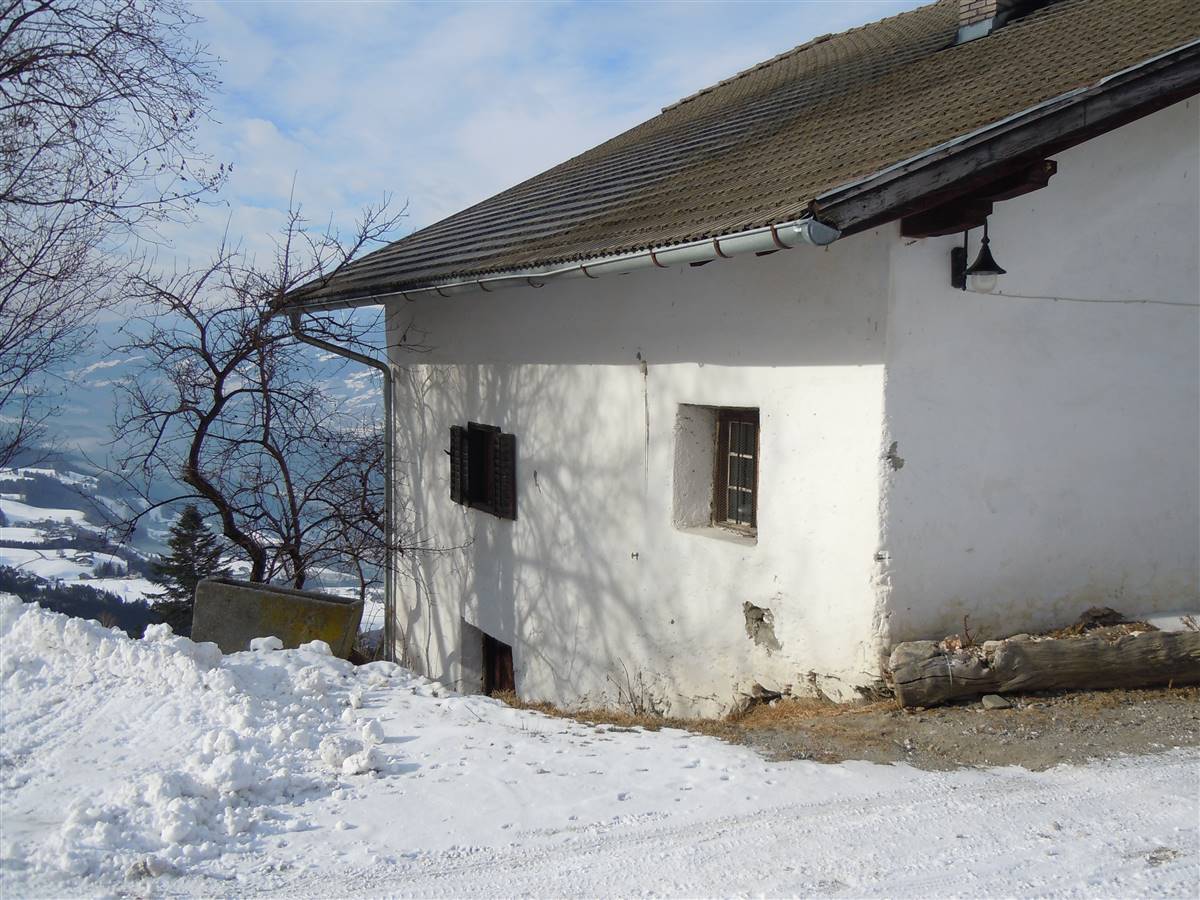
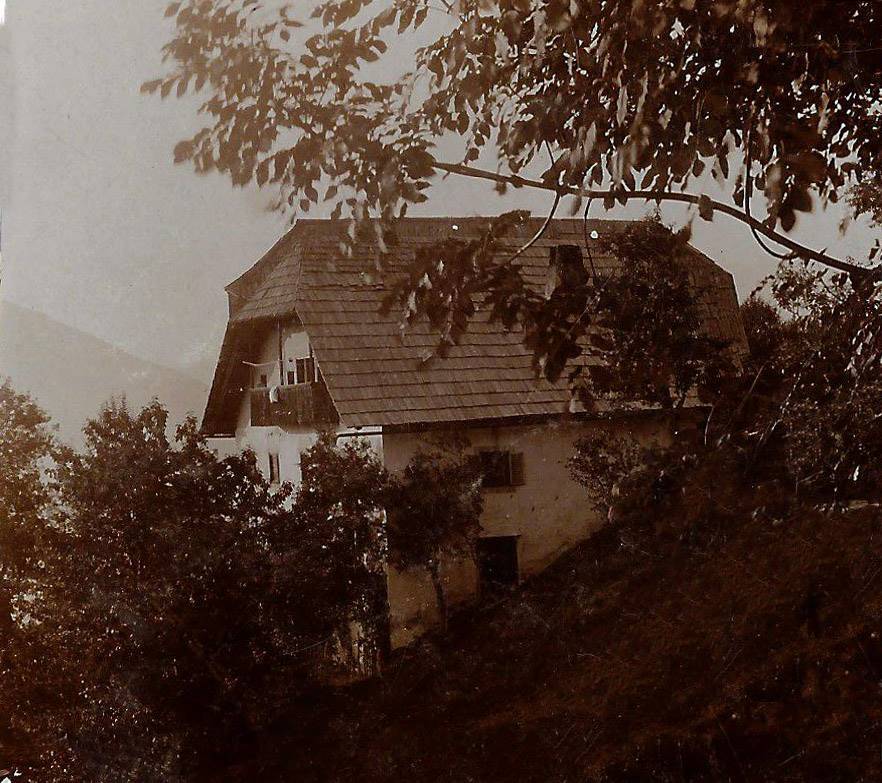
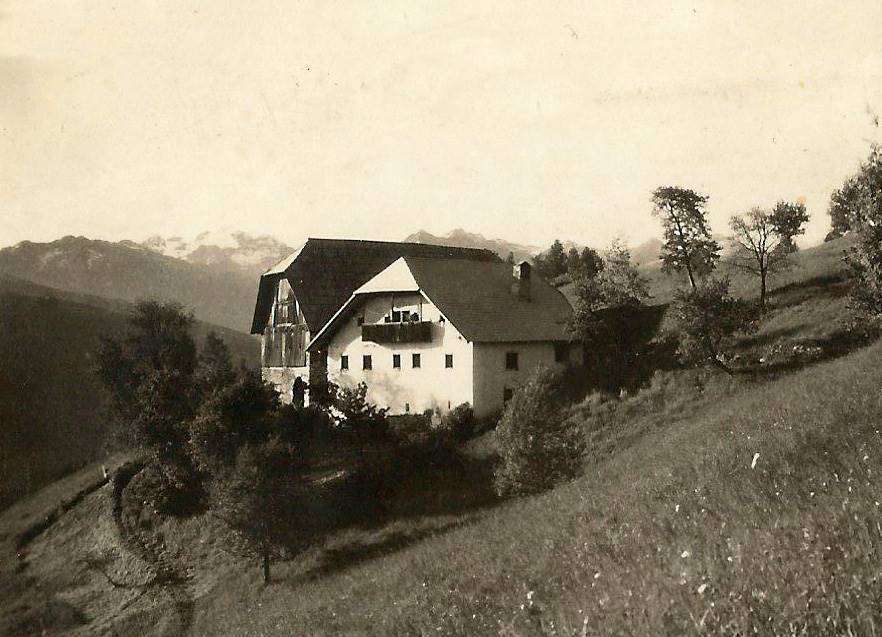
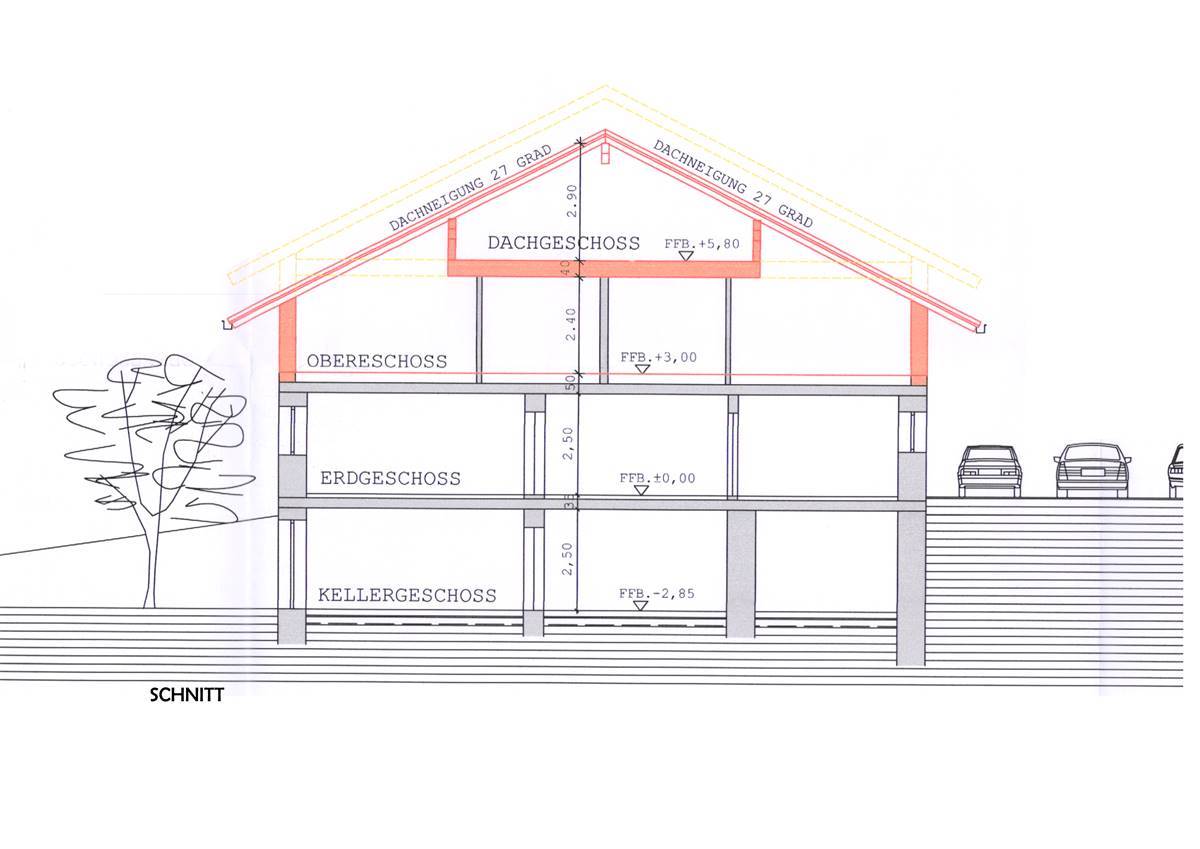
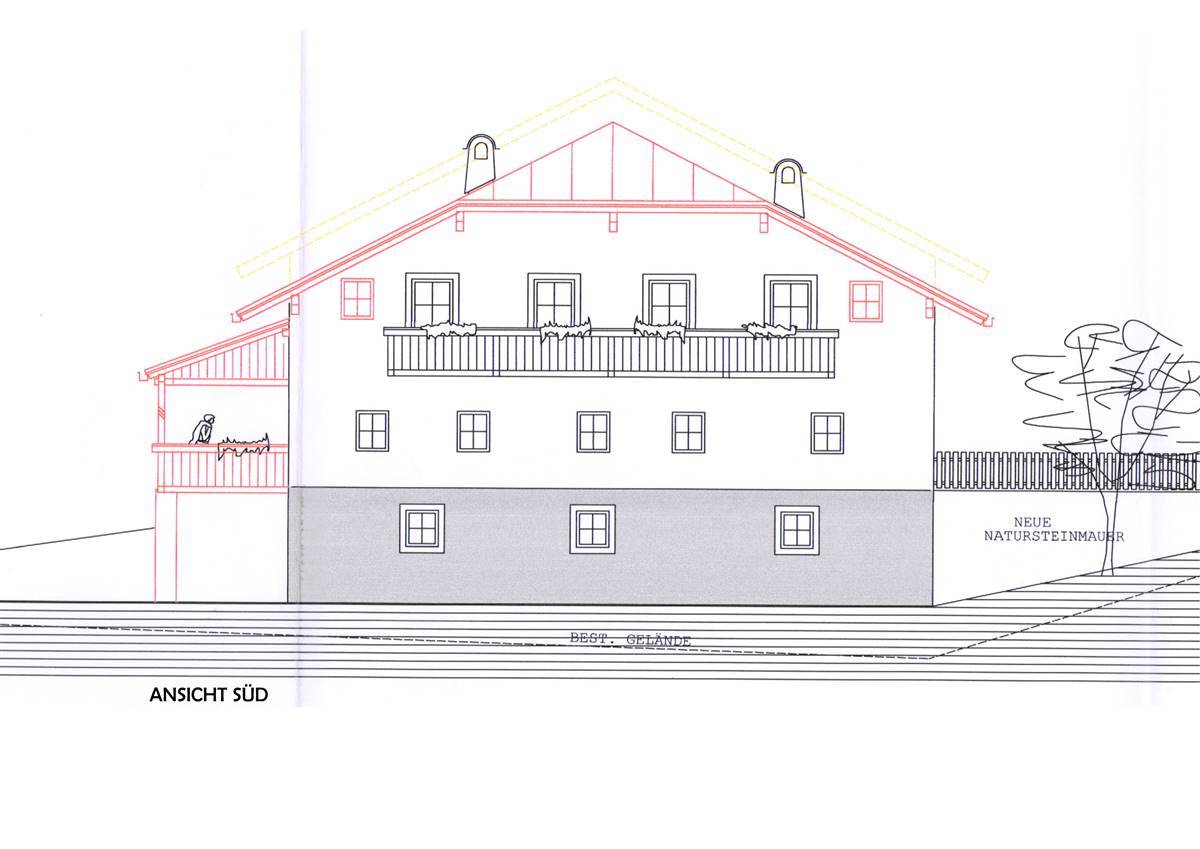
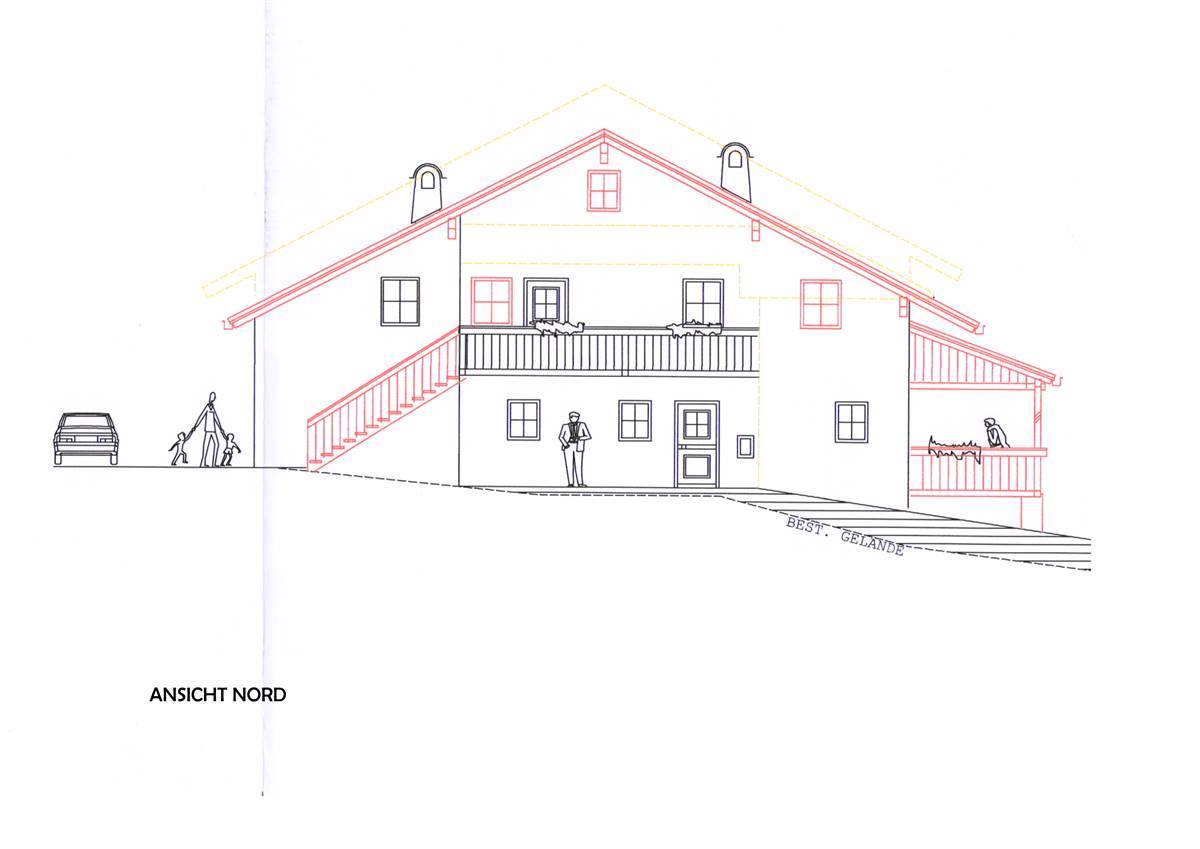
RENOVATION PROCESS
Architecture
BUILDING DESCRIPTION
State of repair
HERITAGE SIGNIFICANCE
Aim of retrofit
Fam. Markus Oberrauch
Rutzenberg 41, 39042 Brixen
info@platzbon.it
Tel. 39 334 18 40 958
Dr. Ing. Benno Graus
Rienzdamm 14, 39042 Brixen
ing.graus@gmx.net
Tel.+39 0472 835374
Klimahaus Energieberater - Geom. Thomas Graus
Am Hohen Feld 6, 39042 Brixen (BZ)
thomas.graus@gmail.com
Tel.+39 347 7448812
Dr. Ing. Benno Graus
Rienzdamm 14, 39042 Brixen
ing.graus@gmx.net
Tel.+39 0472 835374
RETROFIT SOLUTIONS
External Walls
Ground floor
Upper floor
The 70cm thick, repaired existing wall of quarry stones was provided with a 12cm thick layer of lime-based insulating plaster. Röfix CalceClima Thermo (with a lambda value of 0.067 W/mK)and CalceClima Fino were used for the exterior plaster. For the interior plaster, Röfix CalceClima Ambiente and Röfix Smooth Lime were chosen. With these building measures, Climate House Standard B was achieved.
The existing walls on the ground floor were only insulated on the outside, as they were worth preserving on the one hand, and on the other hand, parts of the interior should be visible. This becomes clear from the exposed window lintels.
20 mm
700 mm
20 mm
20mm
700 mm
120 mm
20 mm
On the upper floor a complete demolition of the walls, renovated in the late 1960s, took place. Only the quarry stone wall on the uphill side was preserved. The walls were rebuilt with "insulating bricks" (Unipor W08 Plan bricks, 0.08 W/mK), which allowed to increase the thermal performance considerably.
This was possible, since the walls from the 1960s were not considered worth preserving.
20 mm
365 mm
50 mm
20mm
425 mm
20 mm
Windows
Three sectioned muntin window
New triple-glazed wooden sash bar windows were installed throughout the building. The insulation plaster was pulled up to the window jambs, the window jambs and blind jambs were replaced and airtightly sealed.
The heritage was taken into account mainly by the choice of material - wood - and the traditional division. The windows were completely replaced, only the lintel remained.
Existing window type | Double window |
Existing glazing type | Single |
Existing shading type | Moveable shading |
Approximate installation year | 1970 |
New window type | Double window |
New glazing type | Triple |
New shading type | Moveable shading |
New window solar factor g [-] | 0,55 |
Other interventions
ROOF
GROUND FLOOR
OTHER
The building was partly demolished from the 1st floor onwards, renewed and the roof construction was raised to such an extent that another habitable floor was created.
However, the historical roof form was reconstructed - even if the construction from 1970 itself was not worth preserving. Actually, the roof was renovated at least 3 times in the last 150 years (1880, 1927 and 1967), but not completely, it was always just pieced up and repaired. The uninsulated roof truss would in no way have met the requirements of energy insulation, let alone the requirements of statics. During the renovation, the intermediate ceilings were also acoustically insulated (thickness approx. 50 cm), and the roof was consequently raised somewhat in order to still create sufficient living space on the upper floor.
70 mm
80 mm
240 mm
20 mm
70 mm
80 mm
20 mm
240 mm
20 mm
240 mm
The floor covering was removed, partially repaired and reinstalled. Above the basement the wooden beam ceiling was reinforced, insulated and provided with a new floor construction. The part without cellar was replaced with additional reinforcement and gravel fill. In the area of the kitchen and the bathroom an underfloor heating was installed.
During the renovation, stone slabs of Brixner quartz phyllite were rediscovered. These were reused in the kitchen and the "Labe".
1000 mm
50 mm
785 mm
150 mm
100 mm
15 mm
The parlour and the parlour chamber from 1834 as well as the old panelling of the upper floor were expertly removed, restored and reinstalled.
Since the building had been energetically improved with insulating plaster, there was also no need for coordination conservation - energy.
HVAC
HEATING
DOMESTIC HOT WATER
Before the renovation, heating was only provided by the oven in the parlour and the stove in the kitchen. A boiler was installed, which is fired with wood chips and emits the heat mainly via radiators and partially via underfloor heating.
The historic oven in the parlour is still in operation, alongside the modern heating systems.
New primary heating system | New secondary heating system | |
---|---|---|
New system type | Heizkessel | Stove |
Fuel | Biomass | Biomass |
Distribuition system | Radiators | Radiating surface |
Nominal power | 30 kW | 7 kW |
RENEWABLE ENERGY SYSTEMS
Photovoltaic
Biomass
Two photovoltaic systems of 19 kWp each are installed on the roof of the nearby barn. One serves to generate electricity for the residential house and the other for agricultural use. Exchange with the electricity net takes place in both systems.
In order not to disturb the historical building apperance, the photovoltaic system was installed on the roof of the newly built barn.
Photovoltaic System | |
---|---|
Type | Polycrystalline |
Collector area | m² |
Total nominal power | 38,0 kW |
The heating system is fired with wood chips. It consumes 120m³ per year - for hot water and heating for the house, but also hot water for the barn (milking machine cleaning and cattle watering).
The wood from the adjacent forests can be used, thus keeping the ecological footprint low.
The boiler and wood chip silo found a place under the entrance of the hayrick - additional soil had to be excavated for this purpose. The 2000-liter buffer storage is located in the cellar of the house and accessible via an external staircase.
Biomass System | |
---|---|
Type | Chips |
Storage size | |
Origin of biomass | Holz aus anliegenden Wäldern |
Overall yearly production | 30,0 kWh |
Energy Efficiency
Voluntary certificates: No
Consumption_estimation_Calculation_method: Steady state simulation (e.g. EPC, PHPP)
Consumption_estimation_After: 74 kWh/m2.y
Primary Energy
Consumption_estimation_Calculation_method: Steady state simulation (e.g. EPC, PHPP)
Consumption_estimation_Including_DHW: Si
Consumption_estimation_After: 39 kWh/m2.y
Internal Climate
The interior temperature is described by the residents as comfortable. The different heating systems - underfloor heating, radiators and the parlour oven - can be used independently of each other and according to your well-being.
Due to the natural ventilation, the air quality is perceived as pleasant. In turn, the residents must contribute to a pleasant indoor climate by regularly airing the rooms through the windows.
The rooms are all sufficiently lit and give a pleasant feeling.
The acoustics have been significantly improved by installing impact sound insulation in the ceilings and the windows are now soundproofed.
Costs
NA
No
Environment
emissions_at_use_stage_after_intervention: 4 per m2
emissions_before_use: NA