Giatla house
Kalkstein 154
9932
Innervillgraten, Austria
Architect
Owner
User
Contact Details
Other Information
http://www.giatla.at/
https://www.madritschpfurtscheller.at/projekte/projekt/giatla-apartmenthaus-in-einem-alten-bauernhaus-als-umnutzung/
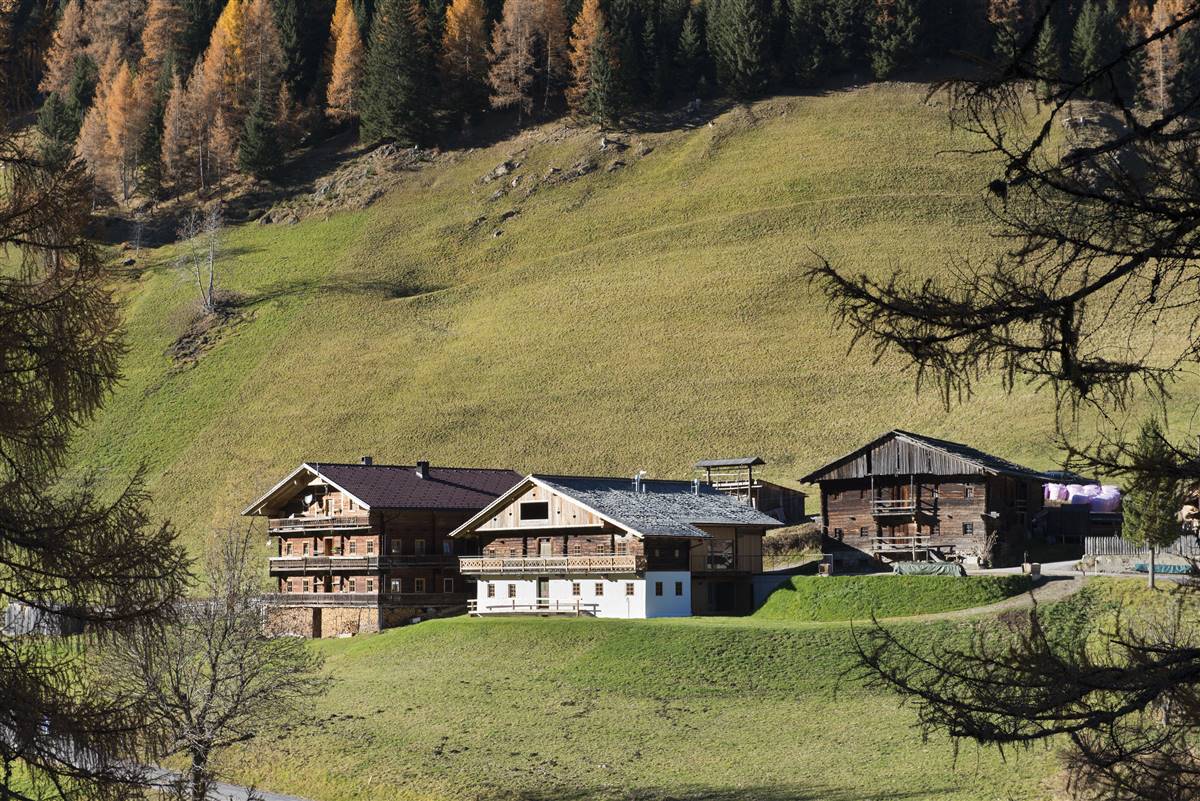
Climate Zone Dfc
Altitude 1641 m a.s.l.
HDD 6029
CDD 185
Conservation Area:
No
Level of Protection:
Kein offizieller Schutz, der Bauherr schützte das Gebäude selbst
Year of last renovation:
2015
Secondary use:
4 vacation apartments
Building occupancy:
Discontinuous occupancy (i.e. holiday home)
Number of occupants/users:
12
Building typology:
Detached house
Number of floors:
3
Basement yes/no:
Yes
Number of heated floors:
3
Gross floor area [m²]:
0,0
Thermal envelope area [m²]:
629,0
Volume [m³]:
718,0
NFA calculation method:
NGF (de)
External finish:
Exposed woodwork
Internal finish:
Exposed woodwork
Roof type:
Pitched roof
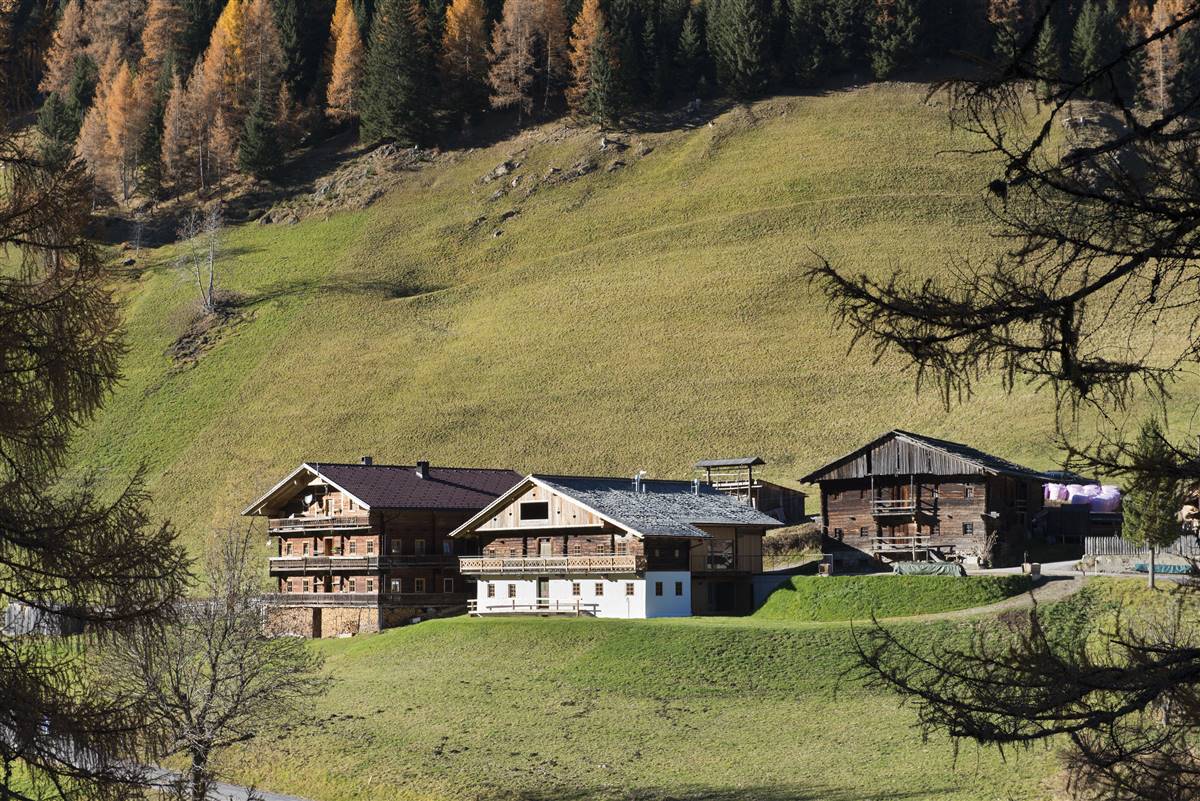
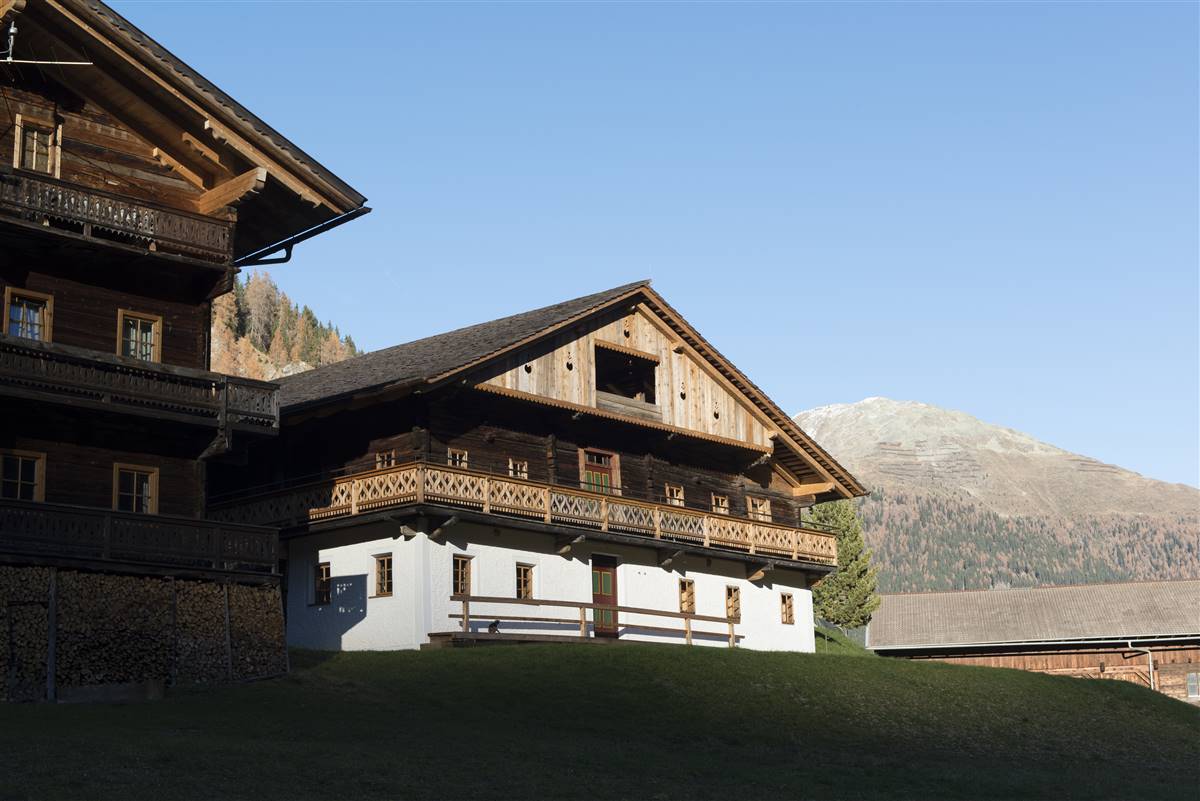
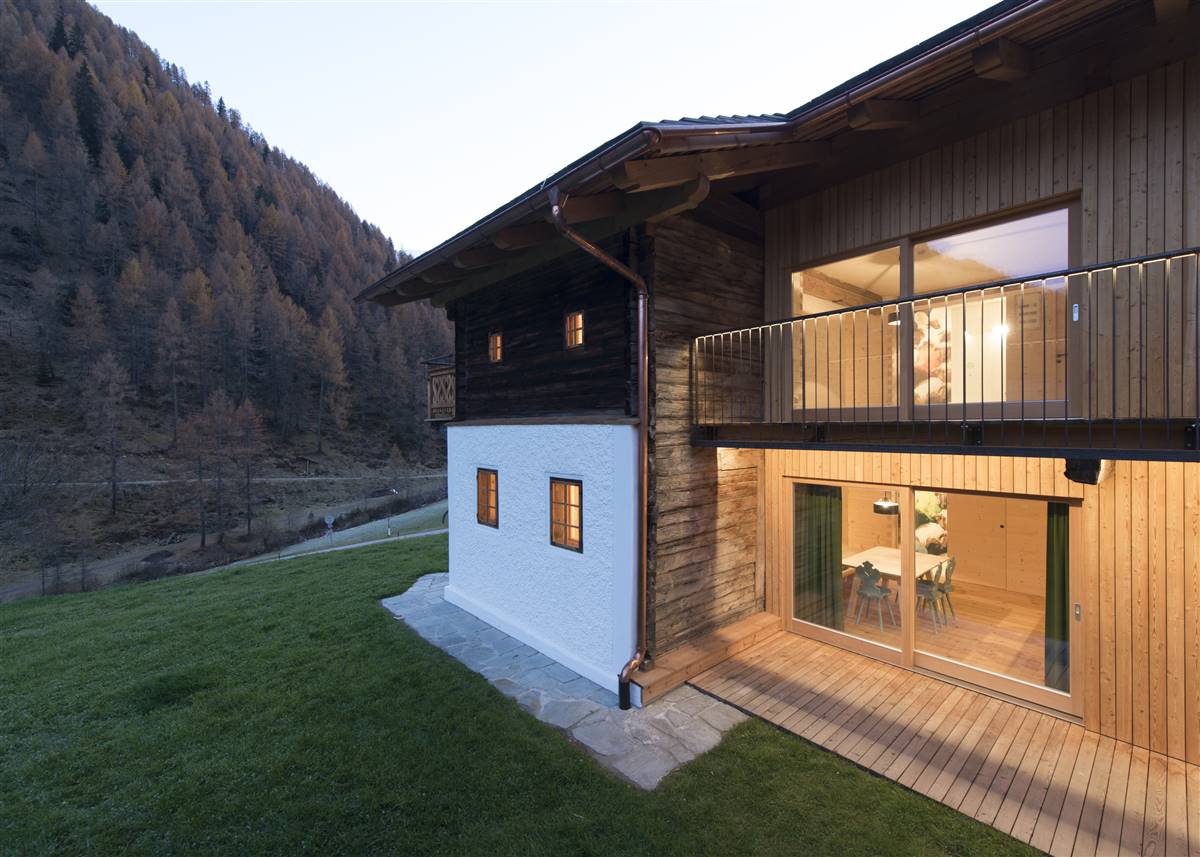
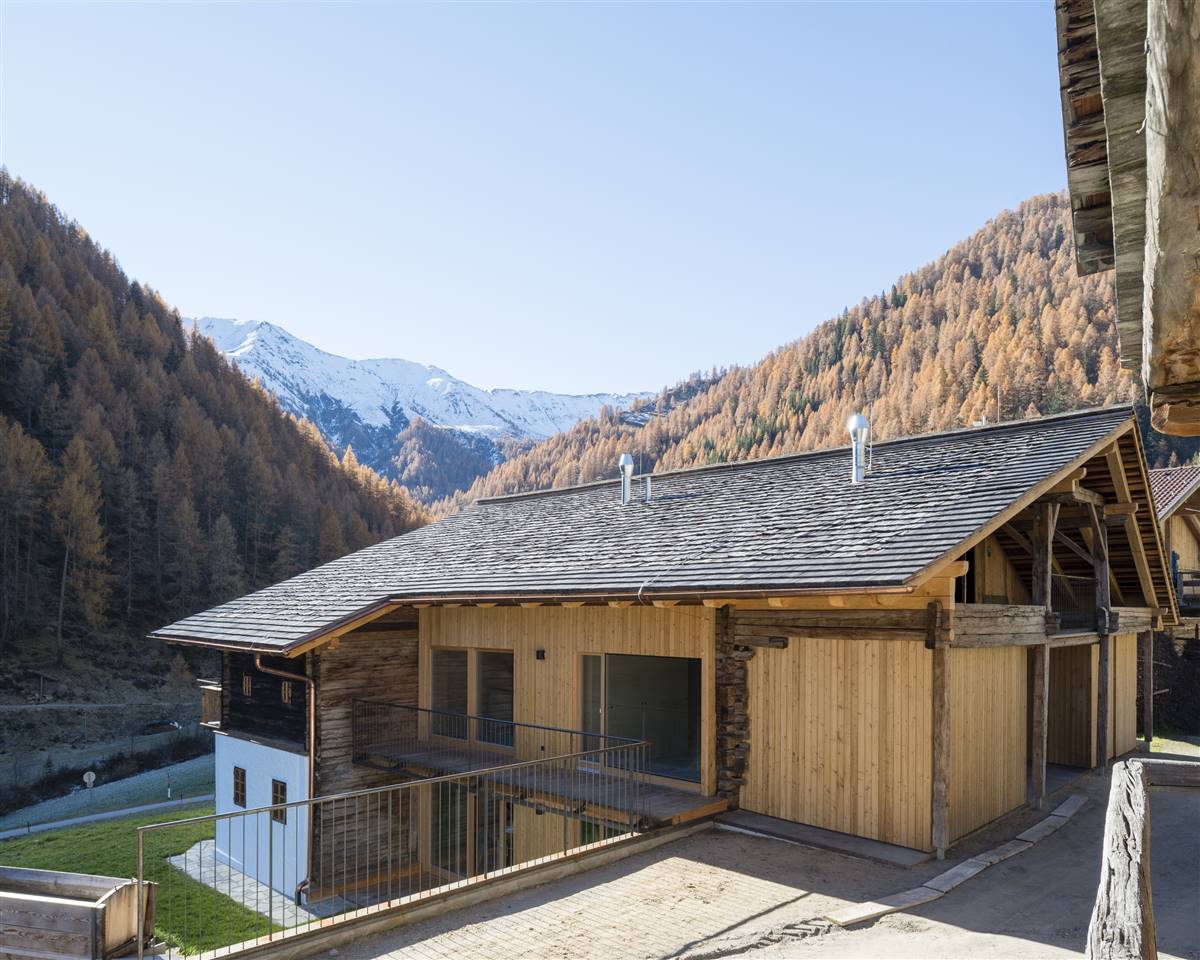
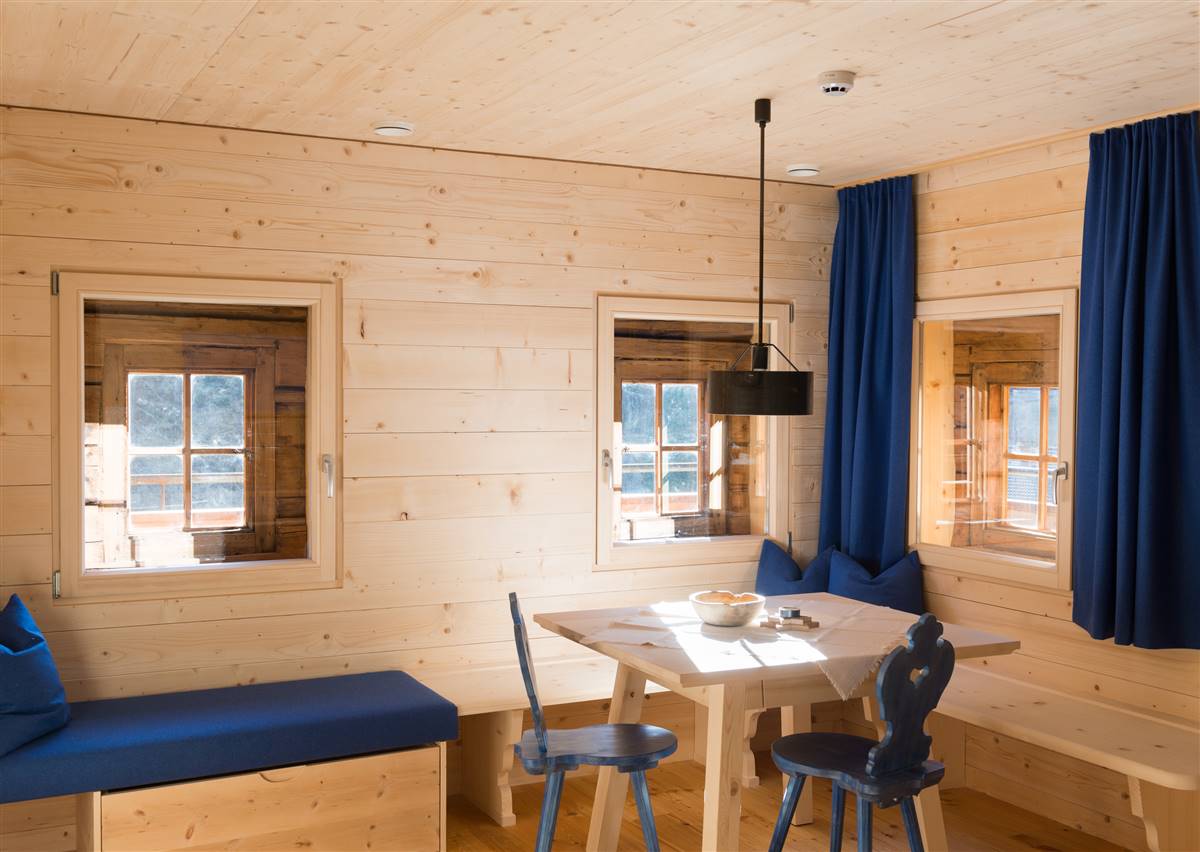
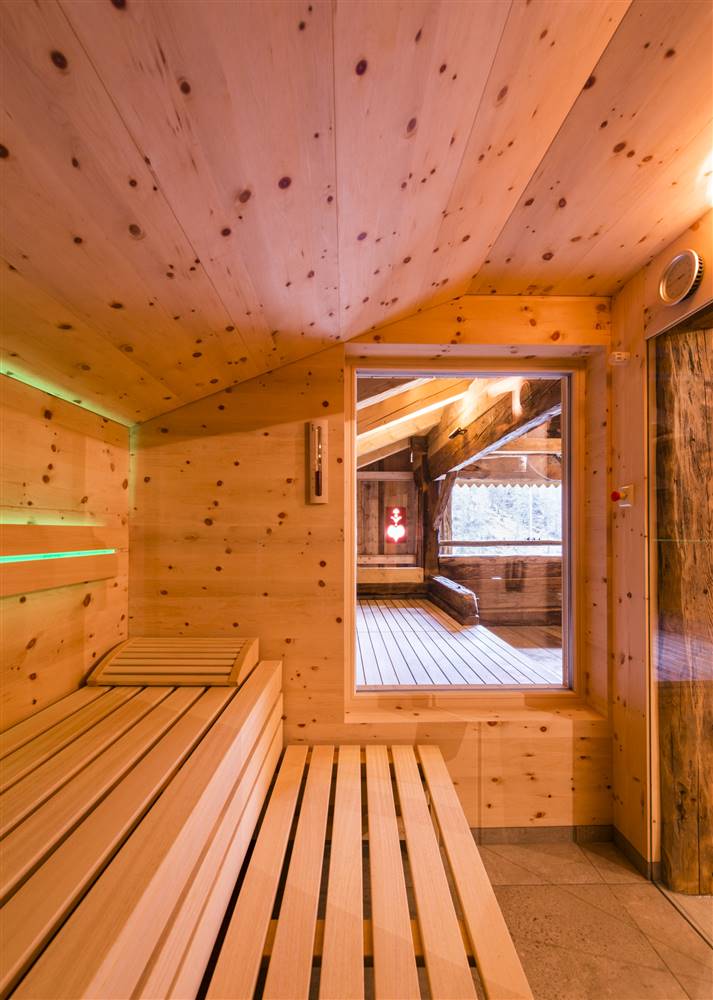
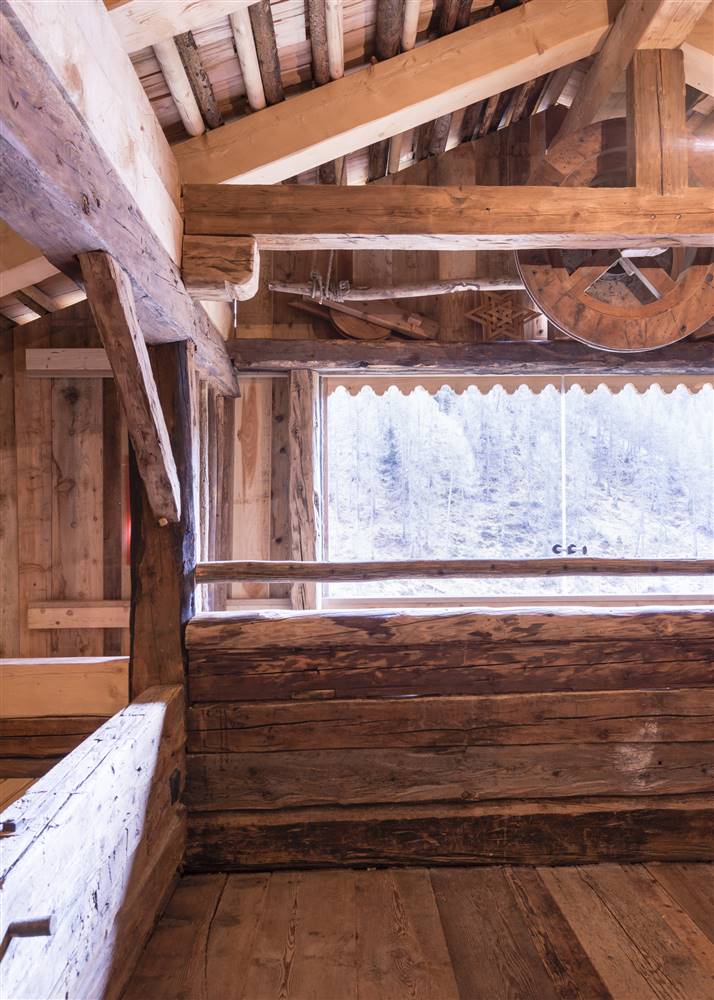
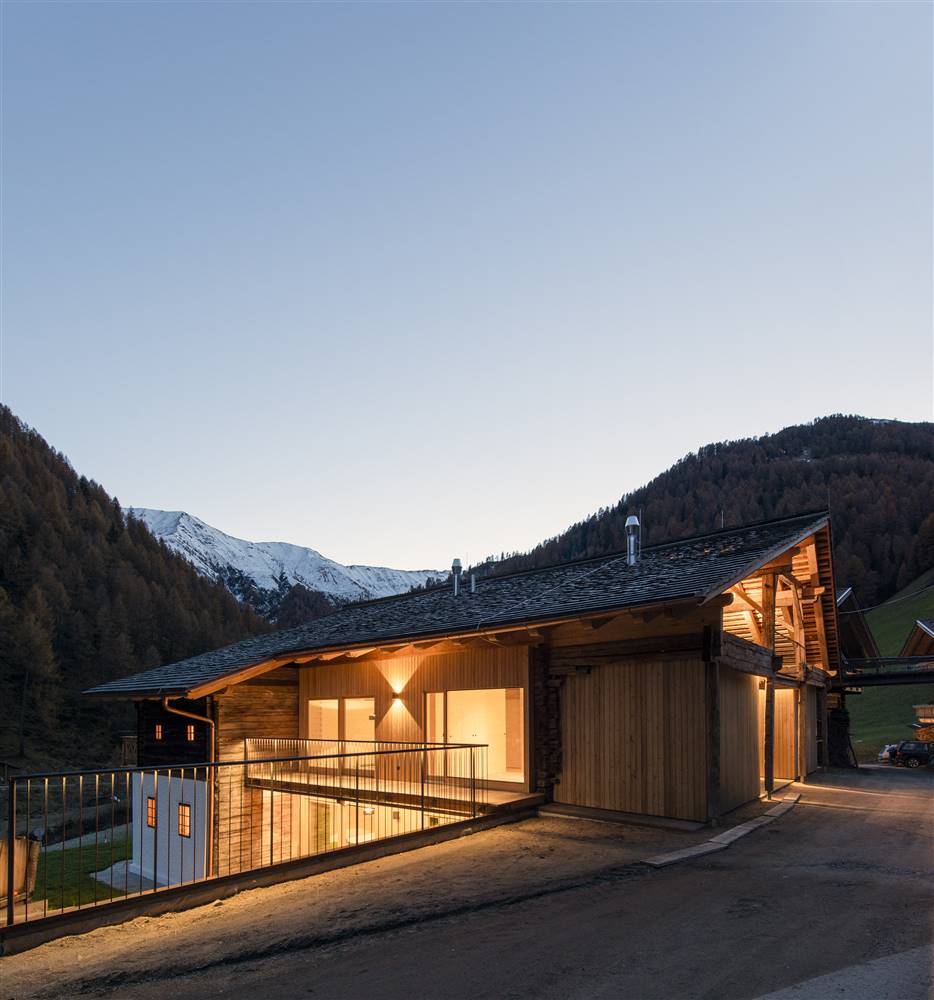
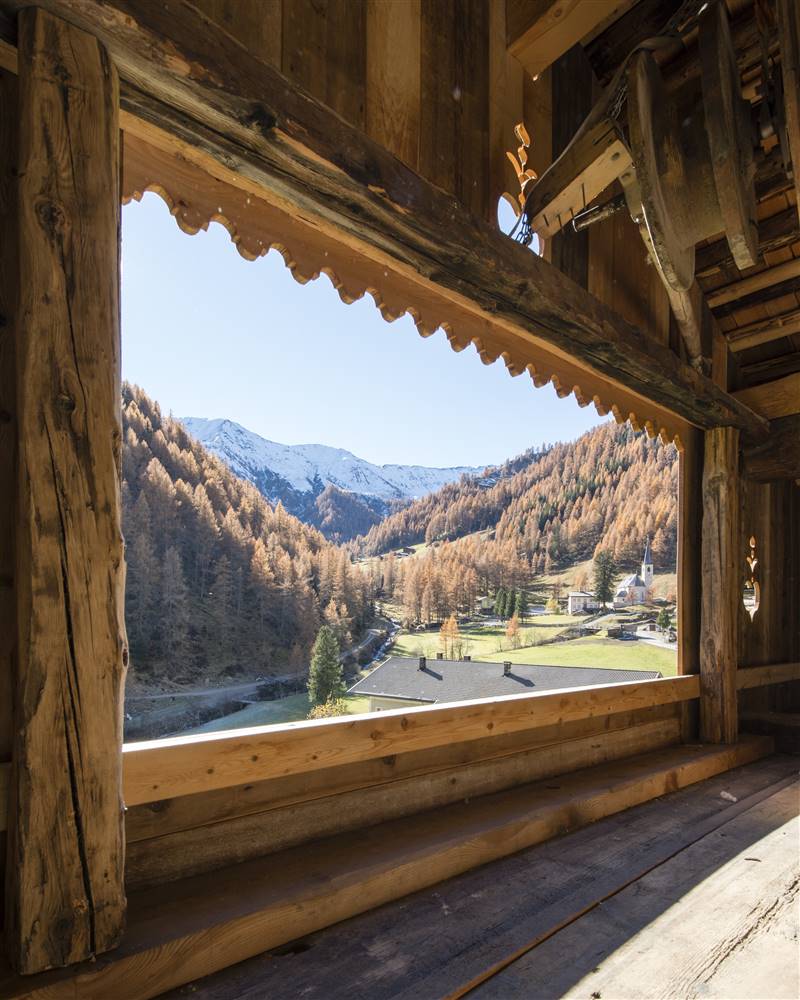
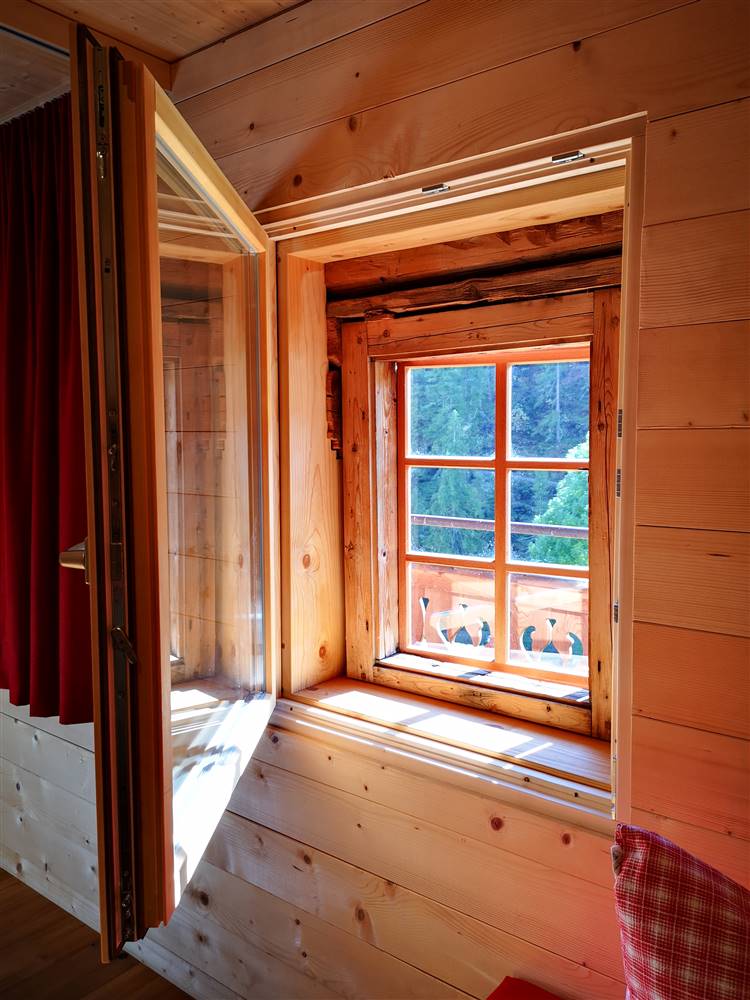
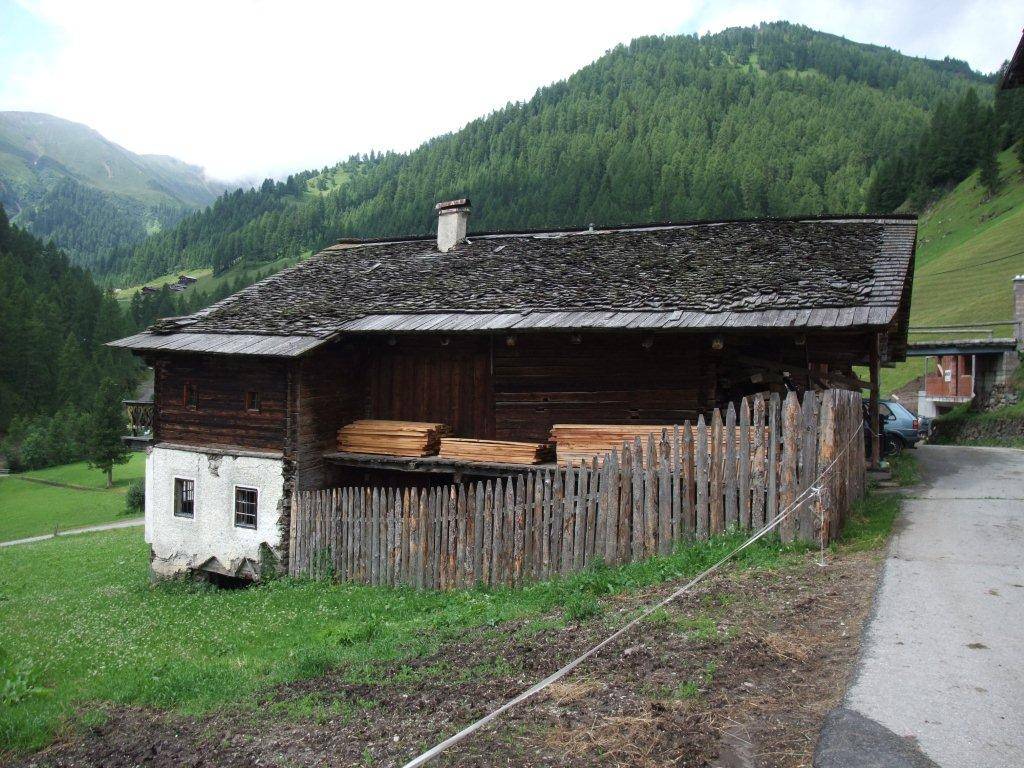
RENOVATION PROCESS
Architecture
BUILDING DESCRIPTION
State of repair
HERITAGE SIGNIFICANCE
Aim of retrofit
Andreas Gardener
Außervillgraten 204, 9931 Außervillgraten, AT
Arch. DI Reinhard Madritsch & Robert Pfurtscheller
Anton Rauch Straße 18*5, 6020 Innsbruck, AT
Reinhard Hutter
Hauptplatz 1, 9754 Steinfeld, AT
Hygrothermal assessment no
Life Cycle Analysis (LCA) Die Materialien und die Art und Weise des Bauens waren meist traditionell mit dem Prosepkt einer sehr langen Lebensdauer. / The materials and the way of building were mostly traditional with the prospect of a very long life.
Other 3D Design in Rhinoceros
RETROFIT SOLUTIONS
External Walls
Log construction
Log construction in the log construction with interim insulation
The old façade was preserved as far as possible. Inside, a new eight-centimetre thick wall structure has been created, which blends into the old walls or wooden walls like a new block. Between the old and the new building the insulation and vapur barier was inserted, whereby local sheep insulation was used as a natural building material". (Benjamin Schaller)
120 mm
0 mm
120mm
0 mm
60 mm
0 mm
80 mm
Windows
Single glazed windows
New Larch-windows behind the historical windows
The new highly thermally insulating window was placed behind the historic window in the thermal insulation layer from the inside.
Existing window type | Casement window |
Existing glazing type | Single |
Existing shading type | NA |
Approximate installation year | 1930 |
New window type | Casement window |
New glazing type | Triple |
New shading type | NA |
New window solar factor g [-] | 0,5 |
Other interventions
ROOF
GROUND FLOOR
MEASURES TO INCREASE AIRTIGHTNESS
The shingle roof including the rafters and the round timber battens were replaced in the traditional way. The roof was also thermally insulated in places where there is a heated area underneath.
The roof was built strictly in the traditional way. Bringing the thermal insulation into the roof is less problematic compared to the wall constructions.
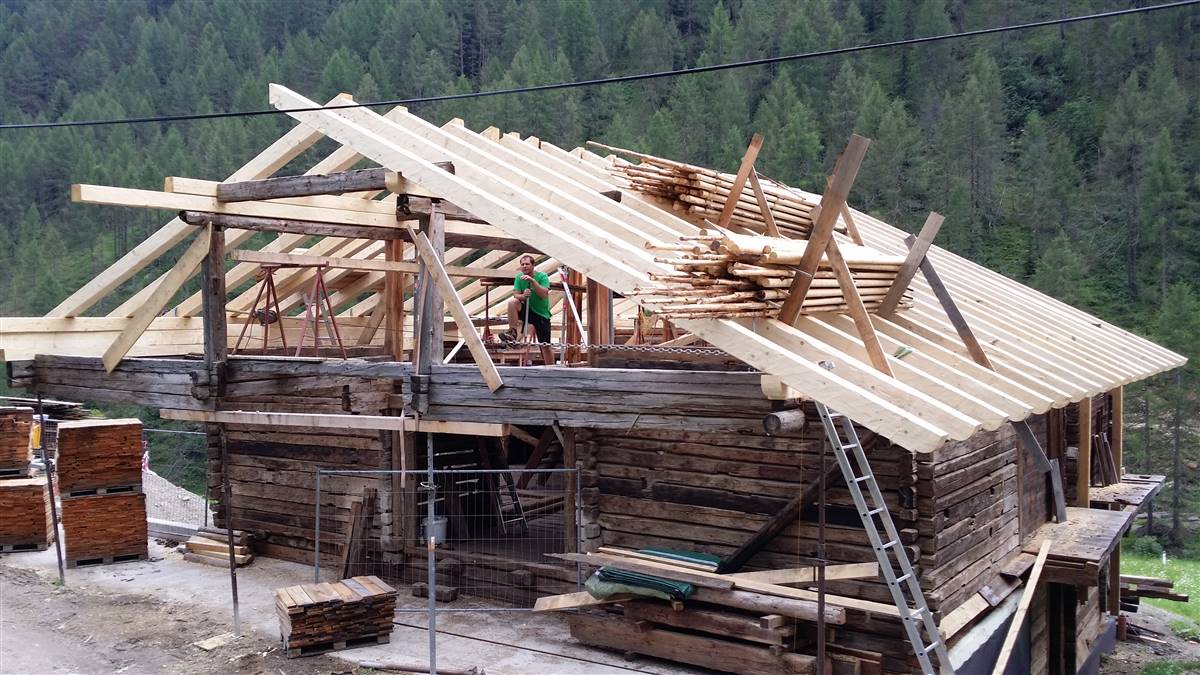
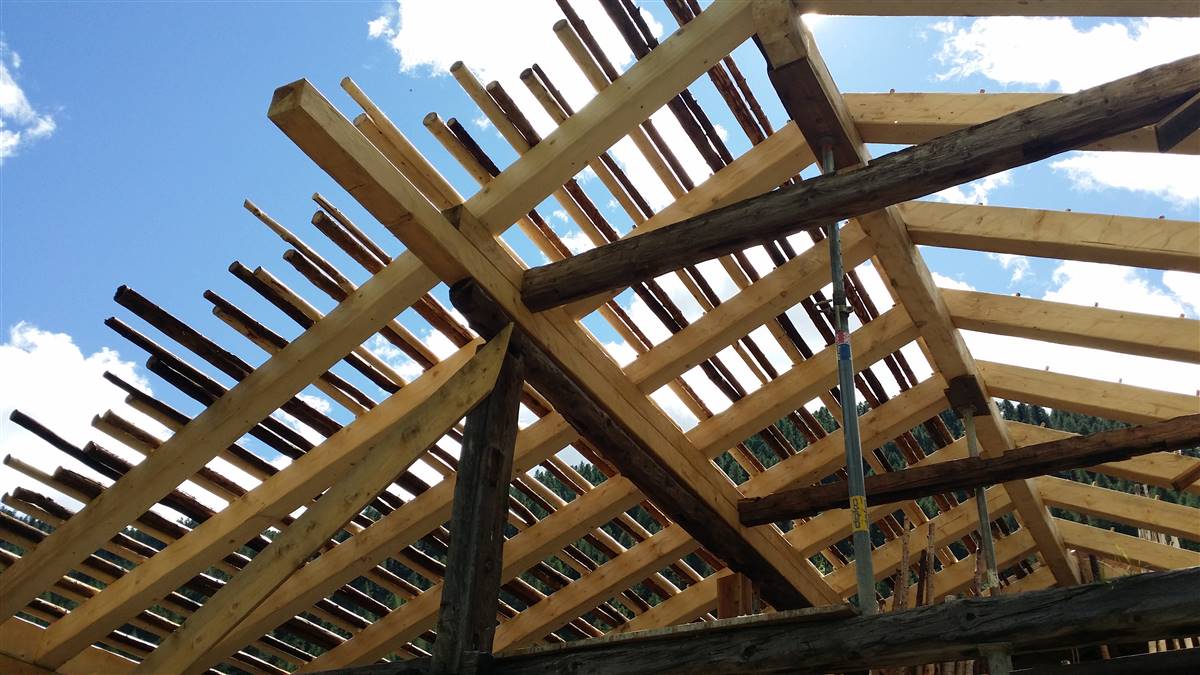
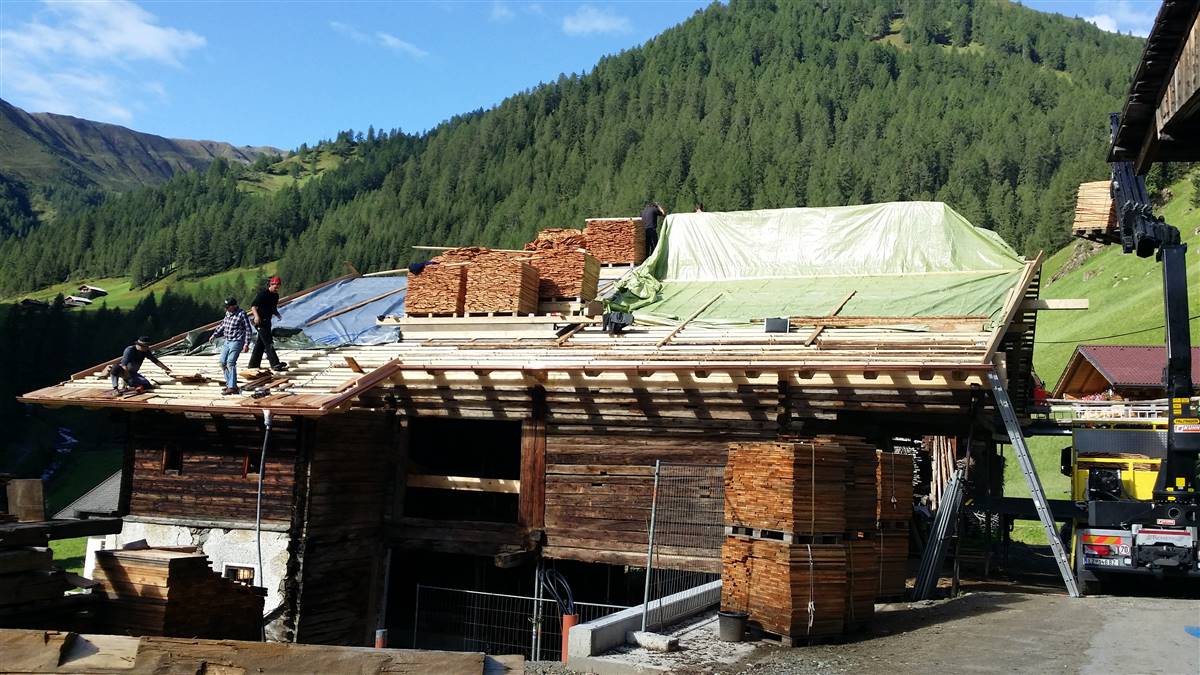
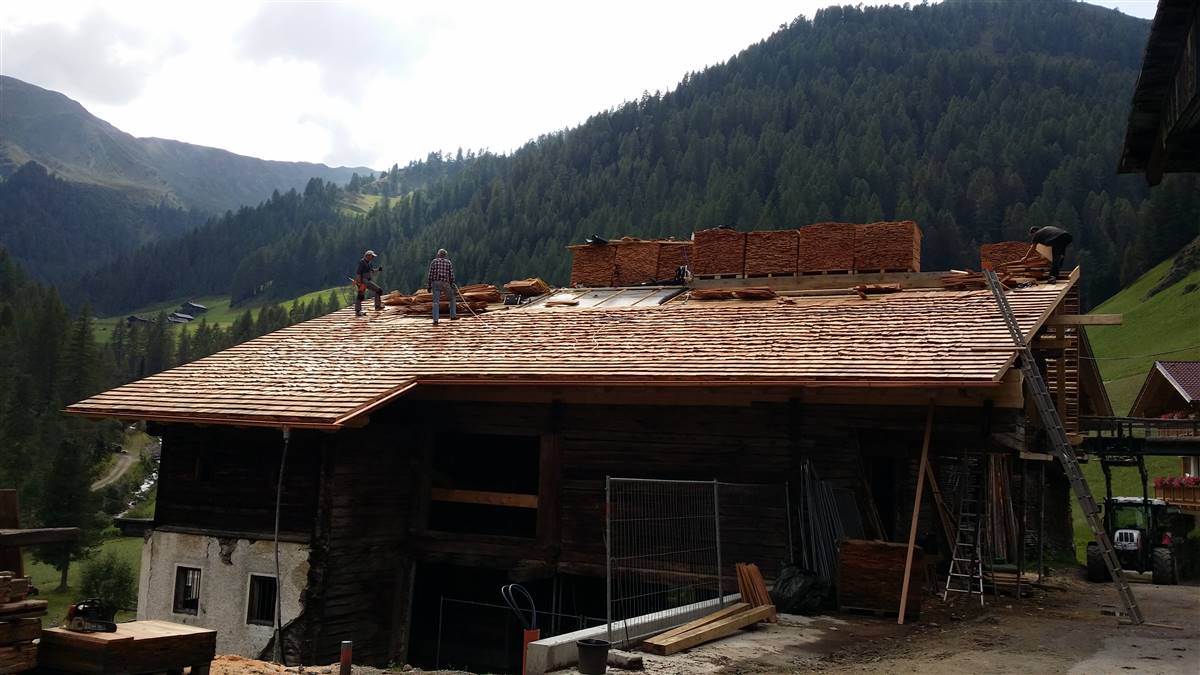
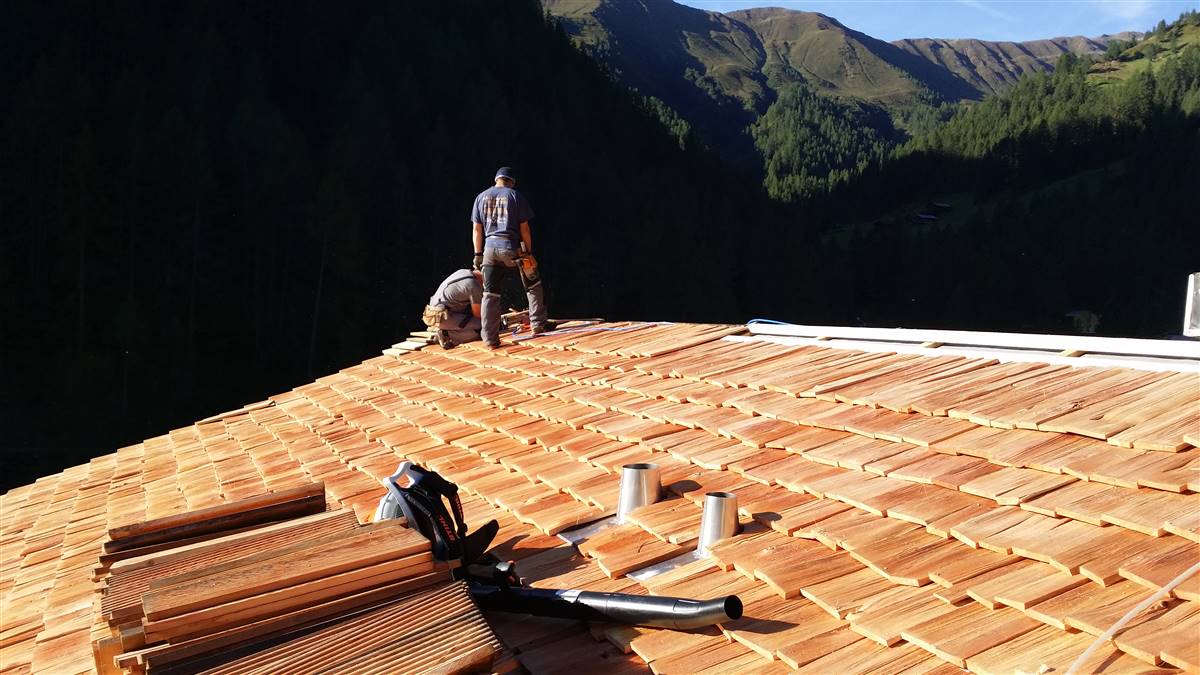
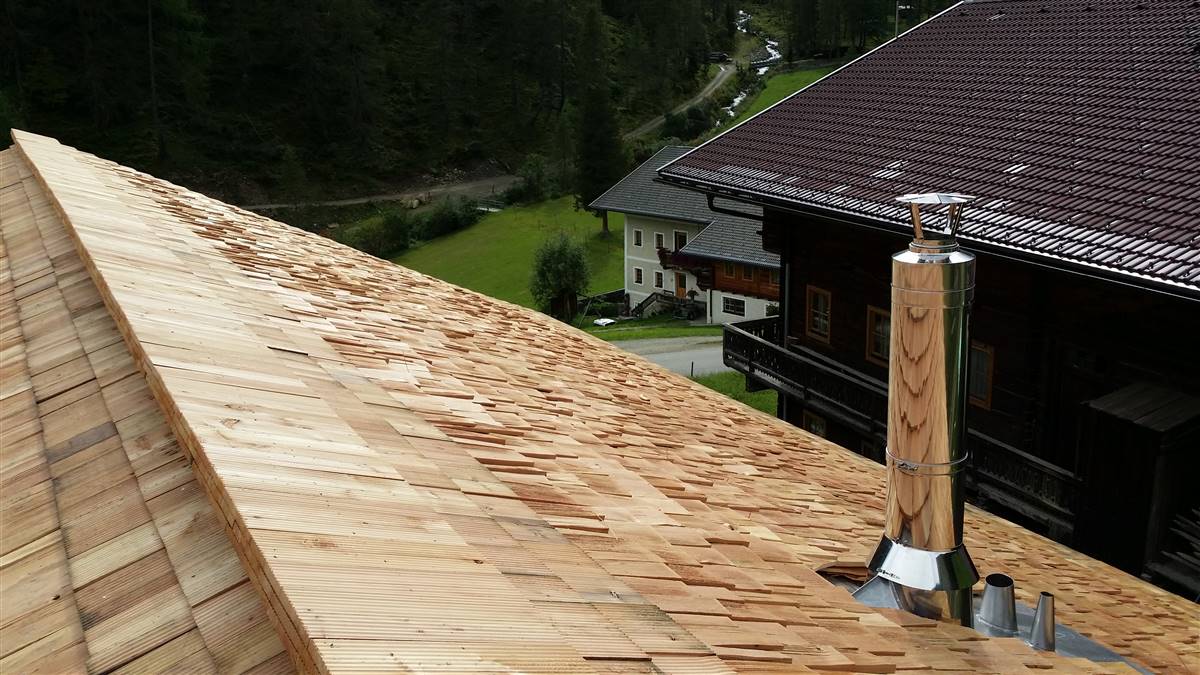
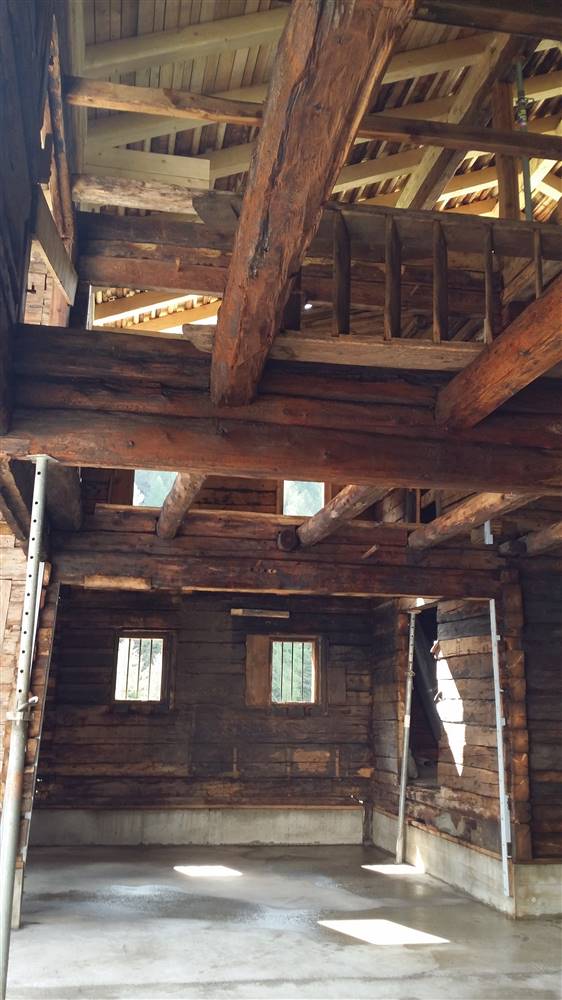
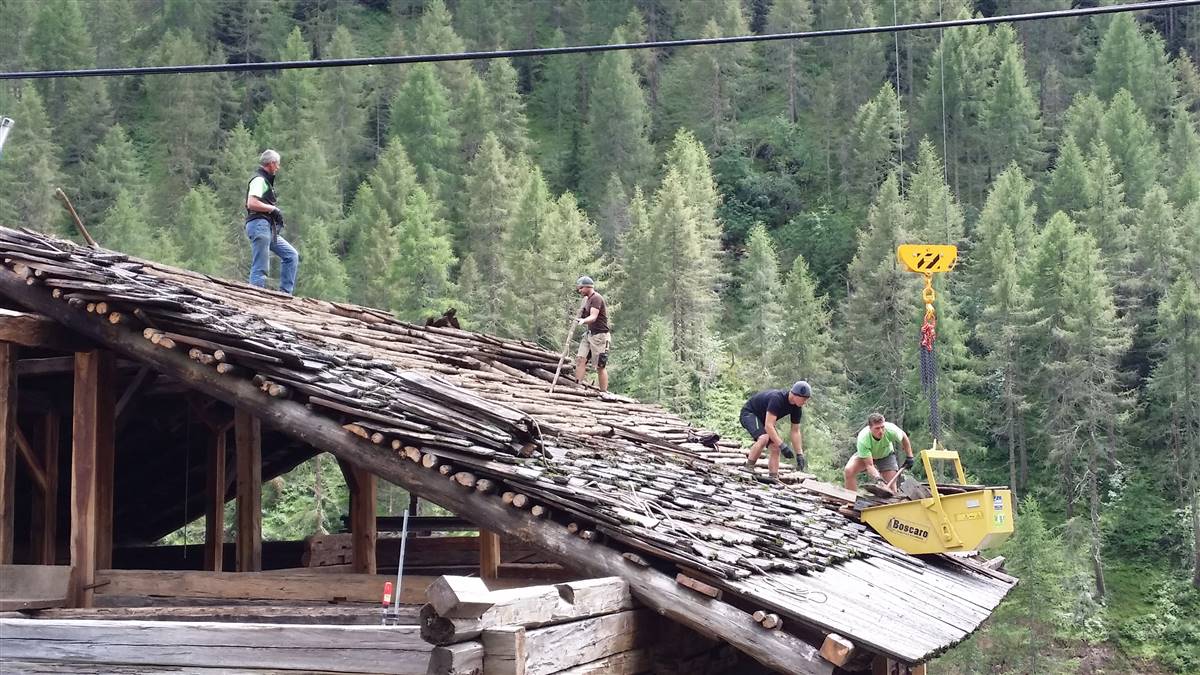
100 mm
30 mm
30 mm
200 mm
100 mm
30 mm
30 mm
0 mm
20 mm
180 mm
35 mm
The entire building was raised by means of its wooden log structure, supported only by metal beams. Then the earth volume was removed at a height of about 2 m below the house to make the missing foundation strips. The ground floor slab was then made of concrete and completely thermally insulated so that the floor heating could be fully utilized. The old cellars were filled with earth and new cellars were created on the north side of the house.
Due to their low weight and flexibility, the block constructions can be completely lifted and supported with the usual technical means. This technology is therefore available to every carpentry firm. The disadvantage is the high labour costs, as the craftsmen have to be experienced and the work progresses more slowly. The advantage is that the whole building is preserved in its original state and shape.
150 mm
25 mm
20 mm
70 mm
35 mm
30 mm
200 mm
4 mm
250 mm
HVAC
HEATING
VENTILATION
DOMESTIC HOT WATER
The house in its original state was only partially heated by a tiled stove with wood.
After the renovation a boiler for wood pellets was used for space heating and hot wate. The heat is distributed to the rooms via floor heating. The technical room was built in the new extended basement next to the original house, so as not to reduce the space. The reason for the high performance heating is also the energetically extensive wellness area in the building. It is also possible to connect the neighbouring house to this heating system.
New primary heating system | |
---|---|
New system type | Stove |
Fuel | Biomass |
Distribuition system | Radiating floor |
Nominal power | 21,8 (1,7kW Pelletenbläser; 63W Umwälzpumpe; 57W Speicherpumpe, 32 Kesselpumpe) kW |
A new central ventilation system with heat recovery, humidity recovery and additional humidifation unit were installed in the building.
The ventilation ducts were led into the wooden floors and walls. As the owner said, the choice of "comfort ventilation air distribution" has resulted in a large number of ducts and a complicated distribution system. Next time he would prefer a simplified distribution system such as the " cascade ventilation principle".
Original roof build-up | New ventilation system |
---|---|
Type ventilation system | Centralized |
Type flow regime | Each room has an air inlet and outlet |
Heat recovery | Yes |
Humitidy recovery | Yes |
Nominal power | 0,35 kW |
Electric power | 0,35 kW |
Control system | CO2 und Feuchtigkeit |
The hot water is prepared centrally with a wood pellet stove in a central hot water tank and distributed by circulation to all tapping points in the building.
The reason for the high-performance heating is also the energetically extensive wellness area in the building.
New DHW system | |
---|---|
Type | with heating system |
Hot_water_tank | Yes |
With heat recovery | No |
RENEWABLE ENERGY SYSTEMS
Biomass
See heating system
See heating system
See heating system
Biomass System | |
---|---|
Type | Pellet |
Storage size | |
Origin of biomass | |
Overall yearly production | kWh |
Energy Efficiency
Voluntary certificates: No
Consumption_estimation_After: 65,4 kWh/m2.y
Primary Energy
Consumption_estimation_Calculation_method: Derived from energy bills
Consumption_estimation_Including_DHW: No
Costs
The builders said that even the cost of renovation was higher than the cost of a new building. The higher costs were worth it simply because of the charm of a historic building combined with modern technology and interior comfort.
No