Ackerbürgerhäuschen
Maria-Dorothea-Str. 2
91161
Hilpoltstein, Germany
Architect
Owner
Contact Details
Other Information
https://www.kfw.de/stories/gesellschaft/bauen/restaurierter-altbau-zweiter-platz/

Climate Zone warm-gemäßigte Klimazone
Altitude 384 m a.s.l.
HDD 2401
CDD 592
Conservation Area:
Yes
Level of Protection:
Denkmalschutz / Listed Building
Year of last renovation:
2015
Year of previous renovation:
0
Secondary use:
NA
Building occupancy:
Permanently occupied
Number of occupants/users:
3
Building typology:
Detached house
Number of floors:
2
Basement yes/no:
Yes
Number of heated floors:
2
Gross floor area [m²]:
283,0
Thermal envelope area [m²]:
484,25
Volume [m³]:
648,5
NFA calculation method:
NGF (de)
External finish:
Rendered
Internal finish:
Plastered (on hard)
Roof type:
Pitched roof

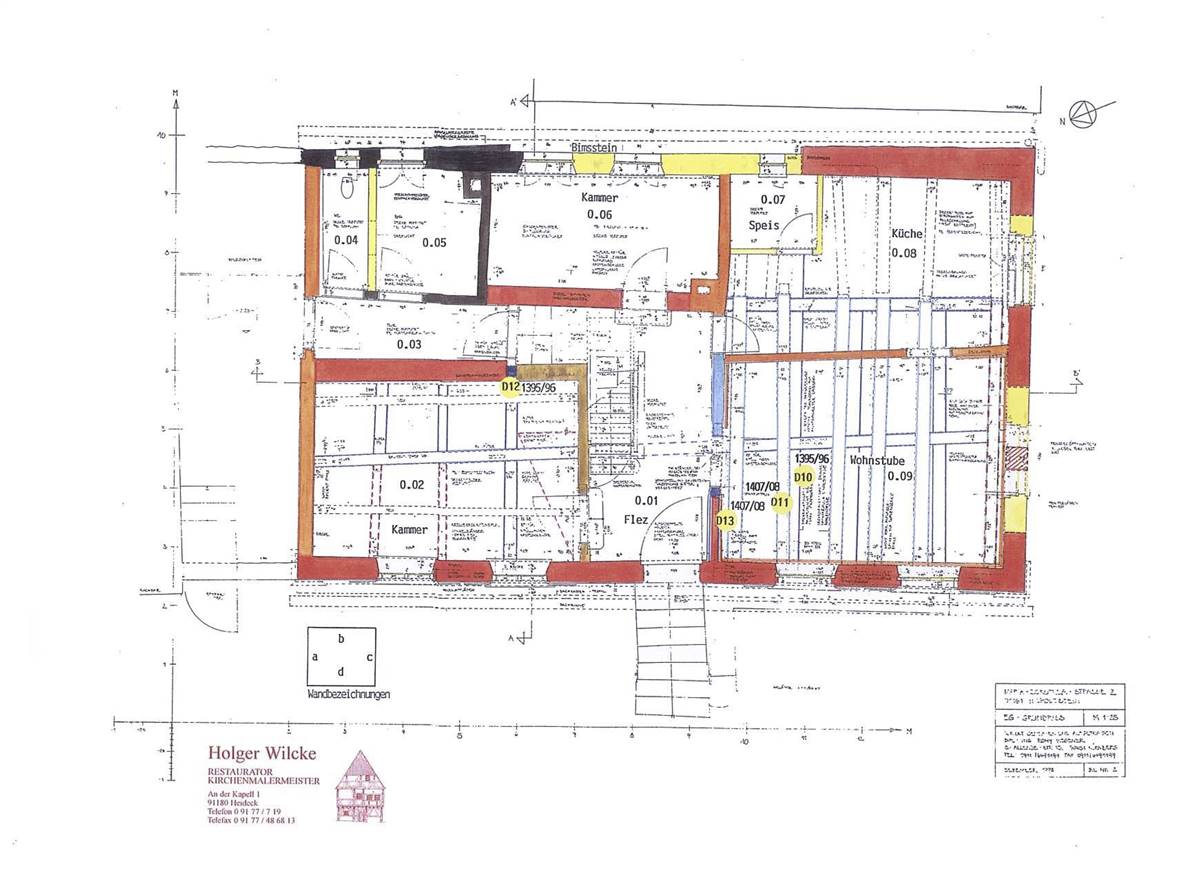
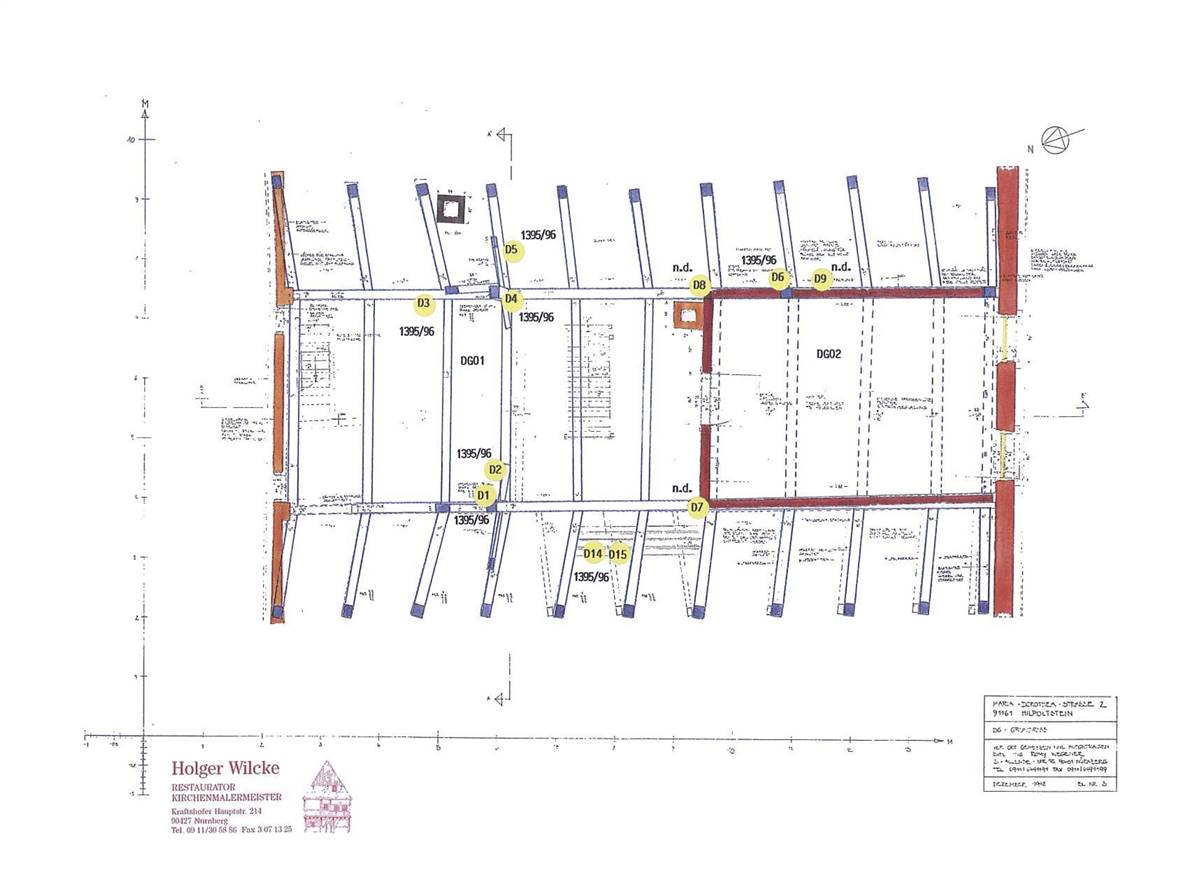
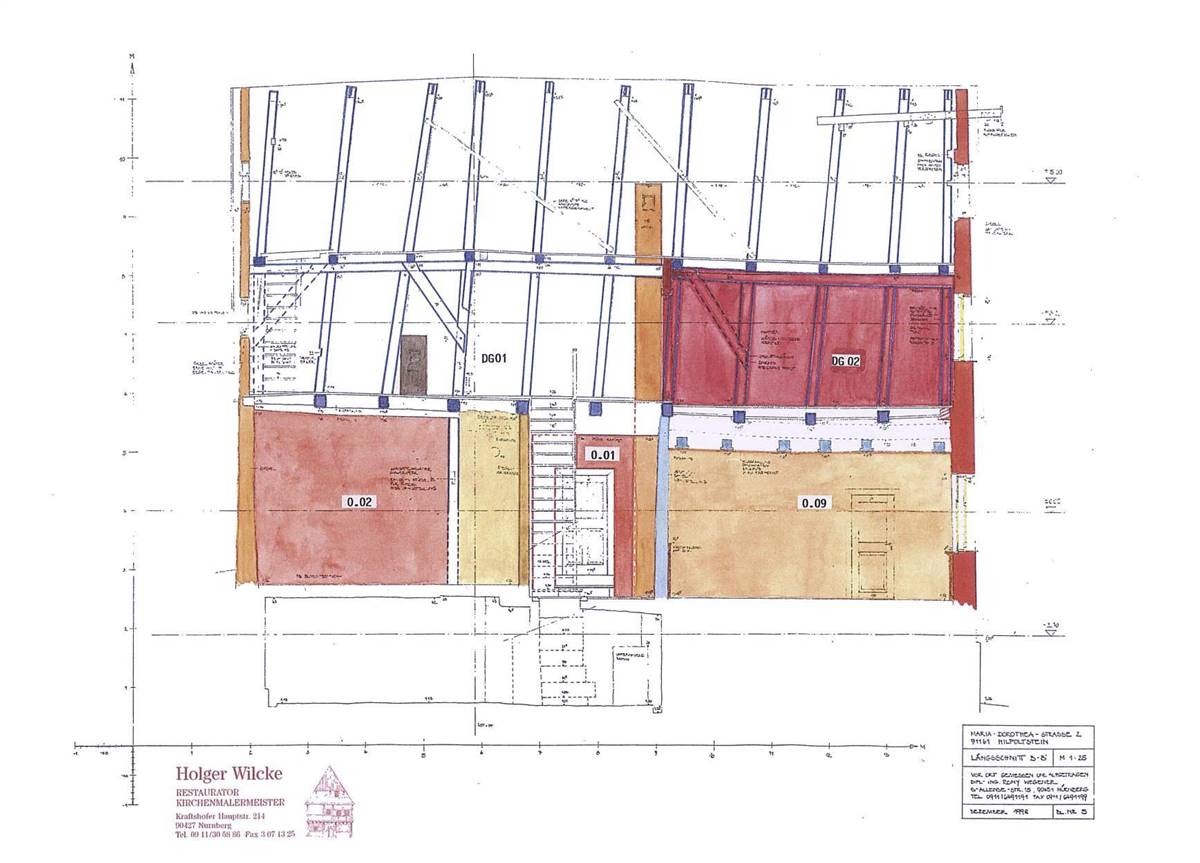
RENOVATION PROCESS
Architecture
BUILDING DESCRIPTION
State of repair
HERITAGE SIGNIFICANCE
Aim of retrofit
Monika und Thomas Fritsch
Kreichwichstr. 2, 92342 Freystadt
Stefan Lerzer
Rennbahnstr. 1, 92318 Neumarkt i. d. Opf.
info@lerzer-ip.de
Tel.09181 - 270 590
Thomas Brandl
Alfred-Bischoff-Str. 8, 92318 Neumarkt i. d. Opf.
info@energieberater- brandl.de
Tel.09181 - 899 822
Hygrothermal assessment in Klärung
Life Cycle Analysis (LCA) Alle wesentlichen Bauphasen wurden durch Bohrkerne dendrochronologisch bestimmt.
Other Des Weiteren wurde ein verformungsgerechtes Bauaufmaß erstellt.
RETROFIT SOLUTIONS
External Walls
Wall outside air east
Wall outside air nord
Wall outside air south
Wall outside air west
Wall outside air west
The existing 300 cm thick sandstone masonry could be preserved. Most of the existing plaster was no longer present. The wall area is 44. 18 m².
The existing wall was insulated on the outside with a thermal insulation composite system as an energy-saving measure. In the inside a plaster mortar of lime gypsum, gypsum, anhydrite and lime anhydrite was applied.
10 mm
300 mm
15mm
300 mm
15 mm
160 mm
10 mm
The existing 250 cm thick brick masonry (klinker) could be preserved. The existing plaster was mostly no longer available. The wall area is 26. 57 m².
The existing masonry was insulated with a composite thermal insulation system as an energy-saving measure both on the outside and on the inside. In the interior, a plaster mortar of lime gypsum, gypsum, anhydrite and lime anhydrite was applied.
10 mm
250 mm
10mm
120 mm
240 mm
15 mm
120 mm
10 mm
The existing 240 cm thick sandstone masonry could be preserved. Most of the existing plaster was no longer present. . The wall area is 42. 87 m².
The existing wall could be preserved. Most of the existing plaster was no longer present. The existing wall was insulated on the outside with a thermal insulation composite system as an energy-saving measure. The existing wall of the south facade was not plastered in the interior and is therefore visible.
10 mm
240 mm
240mm
15 mm
160 mm
50 mm
10 mm
The existing 240 cm thick sandstone masonry could be preserved. Most of the existing plaster was no longer present. The wall area is 34. 91 m².
The existing wall could be preserved. Most of the existing plaster was no longer present. The existing wall was insulated on the outside with a thermal insulation composite system as an energy-saving measure. In the inside a plaster mortar of lime gypsum, gypsum, anhydrite and lime anhydrite was applied.
10 mm
240 mm
15mm
240 mm
15 mm
15 mm
50 mm
50 mm
15 mm
The existing 240 cm thick sandstone masonry could be preserved. The existing plaster was mostly no longer available. The wall area is 4. 98 m².
The existing wall could be preserved. Most of the existing plaster was no longer present. The existing wall was insulated on the outside with a thermal insulation composite system as an energy-saving measure. In the inside a plaster mortar of lime gypsum, gypsum, anhydrite and lime anhydrite was applied.
10 mm
240 mm
15mm
240 mm
160 mm
10 mm
Windows
Window
flat roof windows
The existing wooden windows were replaced by old and new windows with similar forged fittings. The documents show that box windows were installed on the ground floor. By installing a 2-panel thermal insulation glazing, the existing building was energized.
Due to the identical windows with identical wrought iron fittings, the appearance of the existing windows could be preserved as far as possible.
Existing window type | Fixed window |
Existing glazing type | Single |
Existing shading type | NA |
Approximate installation year | 1886 |
New window type | Box-type window |
New glazing type | Double |
New shading type | Outer shutter |
New window solar factor g [-] | 0,6 |
Installation of a DFF 2-panel heat insulation glazing with plastic frame and a stainless steel edge compound. The gable walls have a thermal resistance value of 0.26 W/m2 K. The structure of these gable walls consists of 6cm wood fibreboard WLG 045, a board formwork, 10cm insulation WLG 032 between the beams and a steam brake.
There were no roof windows in the existing building. The roof windows were provided with the same historical window frame as the other windows in the farmer’s house.
Existing window type | no existing window |
Existing glazing type | no existing window |
Existing shading type | NA |
New window type | flat roof windows |
New glazing type | Double |
New shading type | NA |
New window solar factor g [-] | 0,6 |
Other interventions
ROOF
GROUND FLOOR
OTHER
The oldest roof structure of the district should be preserved as far as possible. In order to remove the soot of the last centuries, the owners Thomas and Monika Fritsch brushed the old beams for weeks in the course of the renovation. Parts of the roof structure that could no longer be saved were replaced by new ones.
The oak beams of the roof come from trees that were felled between 1396 and 1408.
25 mm
50 mm
25 mm
27 mm
2 mm
160 mm
52 mm
190 mm
In the course of the renovation a new floor structure was built on all floors. The floor slab against the ground was adequately insulated both from below and from above. The ceiling against the unheated basement was insulated from above. Underfloor heating has been installed in all rooms for a comfortable room temperature and foot warmth.
There was no usable floor structure in the existing building.
50 mm
100 mm
14 mm
40 mm
60 mm
5 mm
150 mm
250 mm
A terrace was built in the west on the roof of the narrow annex. In addition, the no longer existing front garden with wall was reconstructed.
The existing building already had a small half-height intermediate building with a flat roof to the west. This was taken up in the course of the renovation, energetically upgraded and thus extends the usable space on the ground floor. A terrace with a filigree railing was built on the flat roof. By reconstructing the front garden with the wall made of sandstone, a part of the former building was restored.
HVAC
HEATING
VENTILATION
DOMESTIC HOT WATER
While most of the neighbour buildings had already been equipped with modern heating systems, the previous occupant, Mrs Fischbacher, was still living in her almost 600-year-old cottage with a charcoal stove for heat. The charcoal stove was replaced by a central heat generation system. The new gas condensing boiler has a buffer tank for domestic hot water storage, hydraulic balancing (KfW confirmation) and insulated pipes in accordance with EnEV. This gas condensing boiler also heats the underfloor heating installed in all rooms. This has an average temperature of 35/28°C. As an additional heating source, a fireplace stove was connected in the ground floor living room. This also creates a pleasant homely atmosphere.
The farmhouse has only a decentralized coal-fired furnace for heat generation. This was replaced by a central gas-combustible heating system, underfloor heating throughout the building and a fireplace stove.
New primary heating system | New secondary heating system | |
---|---|---|
New system type | Condensing | Stove |
Fuel | Gas | Biomass |
Distribuition system | Radiating floor | Air |
Nominal power | 14,2 kW | NA kW |
A central ventilation system with exhaust air/feed air heat transfer (heat recovery) was installed for a pleasant room atmosphere. The heat supply ratio is 40%.
There was no ventilation system in the existing building. A new system was installed.
Original roof build-up | New ventilation system |
---|---|
Type ventilation system | Decentralized |
Type flow regime | |
Heat recovery | Yes |
Humitidy recovery | No |
Nominal power | 0,30 kW |
Electric power | 0,0 kW |
Control system | Einzelraumregelung |
Prior to the renovation, there was no means of producing hot water, except for the charcoal stove. The new central system has also created a possibility for hot water preparation as well as hot water storage. The gas condensing boiler has a buffer tank for storing domestic hot water.
The existing building did not have any means of generating hot water or storing hot water. Only the old charcoal stove could be heated portions of water. As a result, a completely new system was installed.
New DHW system | |
---|---|
Type | with heating system |
Hot_water_tank | Yes |
With heat recovery | No |
Energy Efficiency
Voluntary certificates: No
Primary Energy 85,1 kWh/m2.y
Consumption_estimation_After: 61,94 kWh/m2.y
Primary Energy
Consumption_estimation_Calculation_method: Derived from energy bills
Consumption_estimation_Including_DHW: Yes
Consumption_estimation_After: 85,1 kWh/m2.y
Internal Climate
Normal indoor temperature
Thanks to the newly installed ventilation system the interior has a consistently good indoor climate.
Due to the numerous existing windows as well as the newly installed roof-gapes, the living rooms have enough natural light. If necessary, the interior spaces can be shaded by the shutters out of wood.
There are pleasant room and building acoustics.
There is no artifact.
Costs
An important aspect is energy saving. Costs are saved by reed insulation, ventilation and the condensing boiler. The exact amount is not known. During construction, efforts were also made to reduce costs. Due to the high demands of the monument protection it was possible to work only in small steps. Therefore, all trades were assigned to local craftsmen. Thus, the craftsmen did not have to charge long distances to get there, if they worked every now and then for a few days or hours.
2.648 € (per m2)