Mercado del Val, Valladolid (Spain)
Calle Sandoval 2 (2 Sandoval st.)
47001
Valladolid, Spain
Owner
User
Contact Details
Other Information
It is an open market, so it is possible to enter and visit the common areas of the building without any restriction. For to visit the restriction areas (technical rooms, etc.), you need to contact with the owner.
As this building has been part of the FP7 European project CommONEnergy, you can find specific public reports in the web: https://cordis.europa.eu/project/id/608678/es

Climate Zone Csb
Altitude 690 m a.s.l.
HDD 1834
CDD 894
Conservation Area:
Yes
Level of Protection:
Mercado del Val is classified as P3 (art. 5.2.7. PECH)
Year of last renovation:
2016
Year of previous renovation:
1982
Building occupancy:
Permanently occupied
Number of occupants/users:
48
Building typology:
Market
Number of floors:
2
Basement yes/no:
Yes
Number of heated floors:
3
Gross floor area [m²]:
4792,0
NFA calculation method:
Useful area (es)
External finish:
Glazing façade and Brick
Internal finish:
Glazing façade
Roof type:
Pitched roof
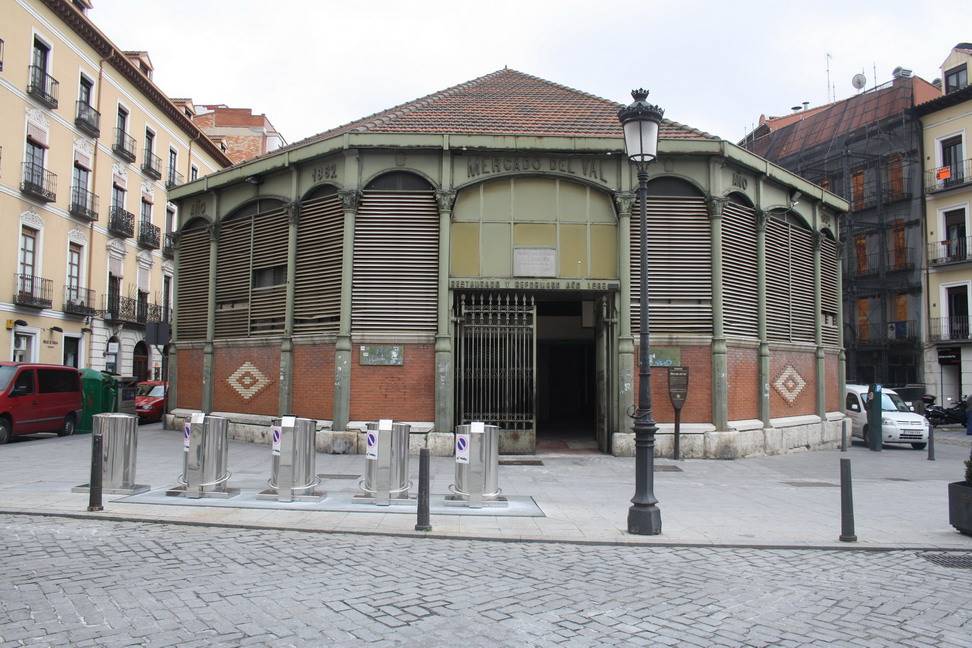
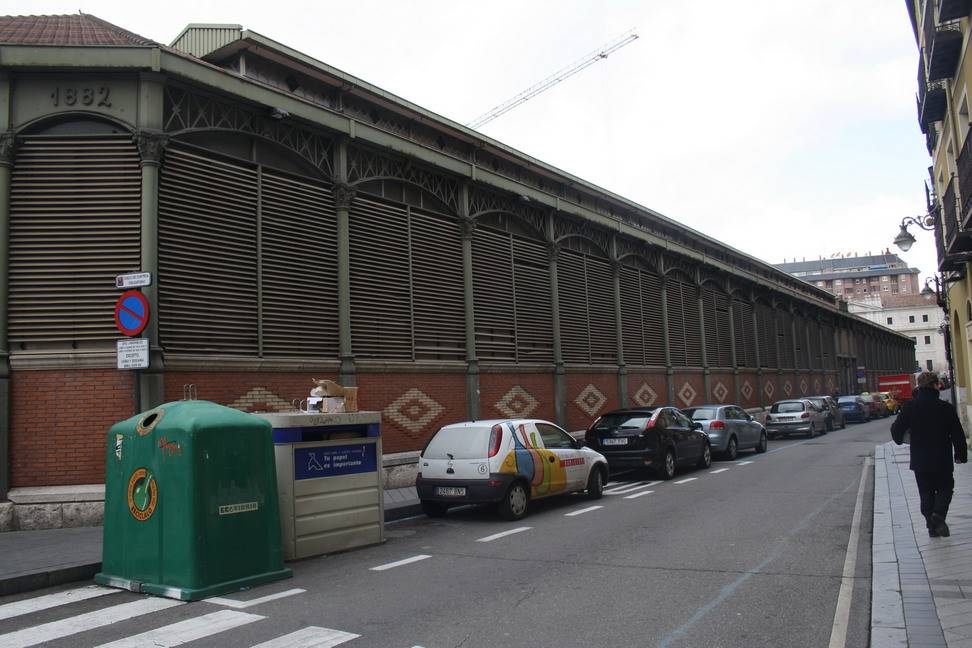
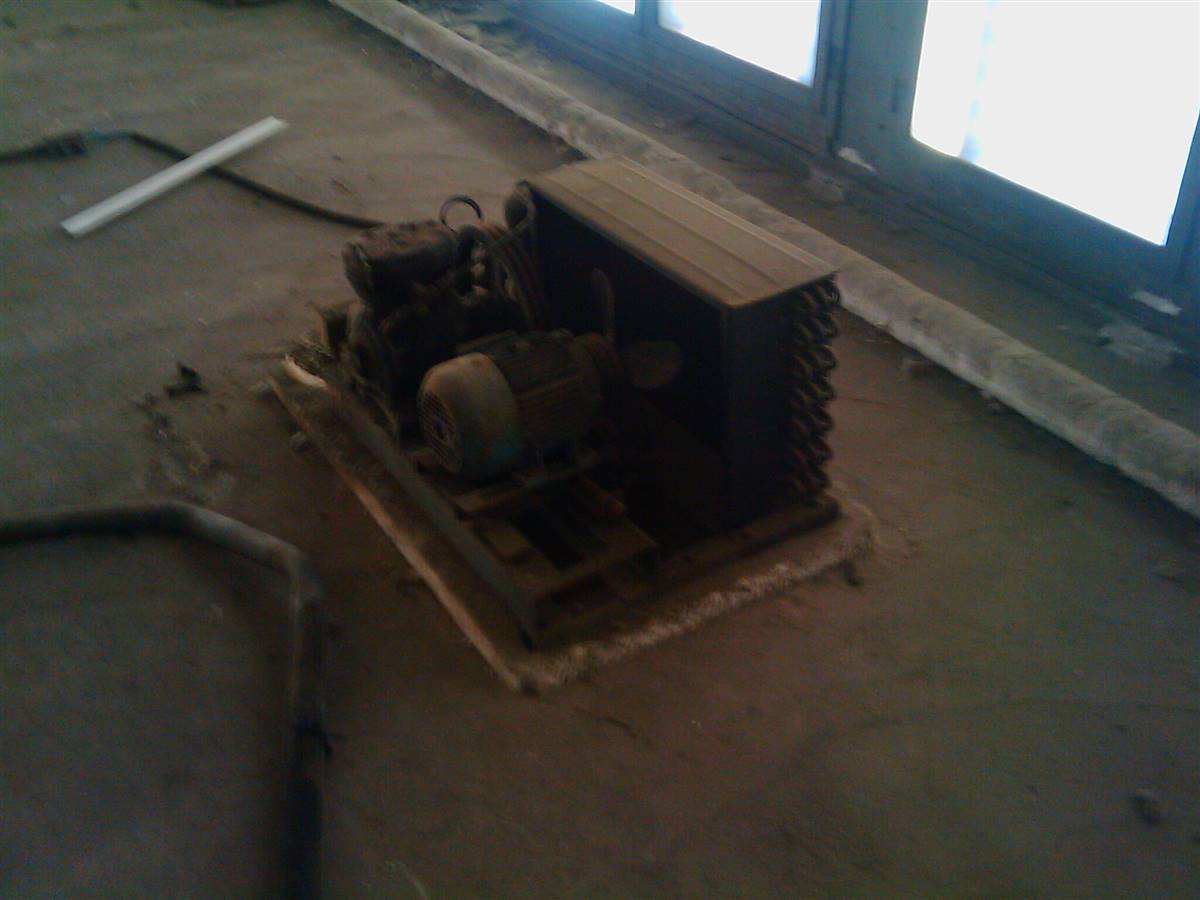
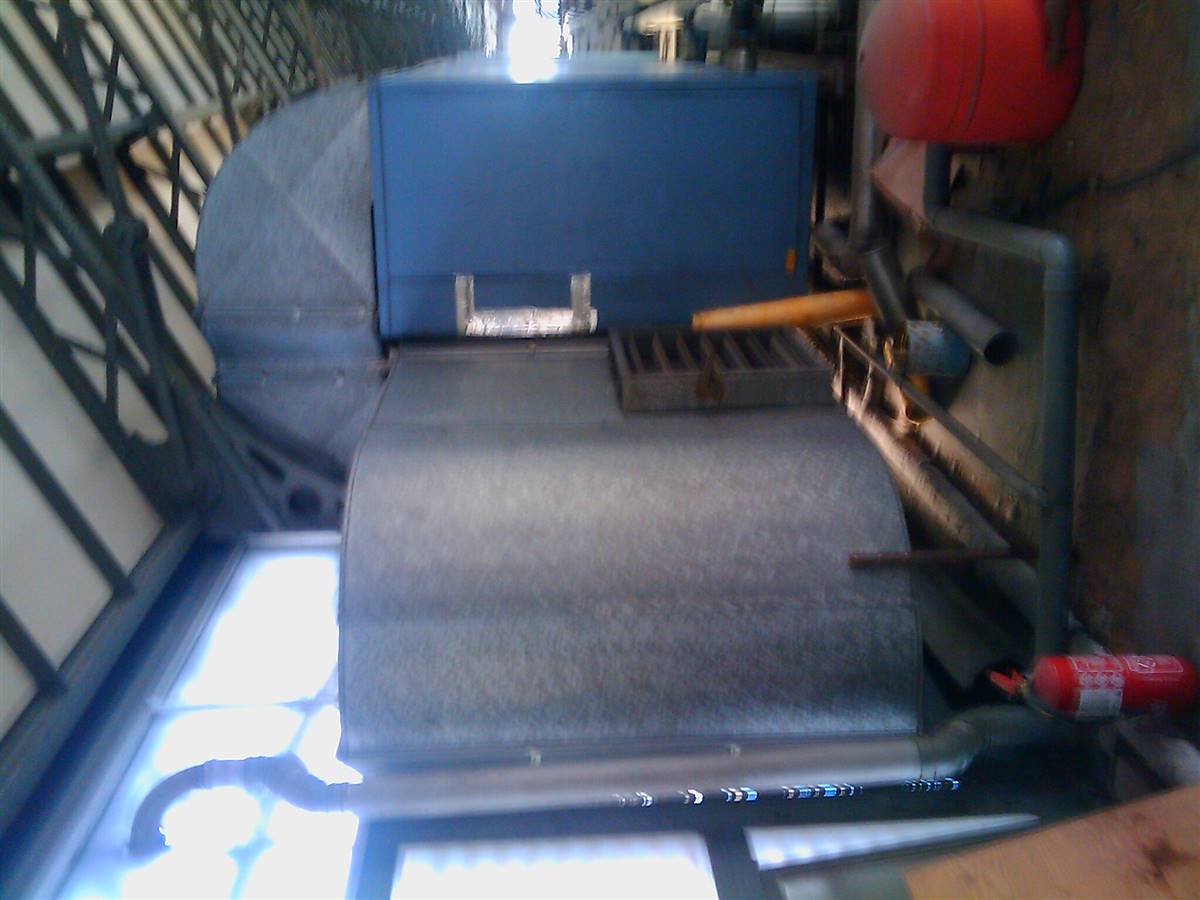
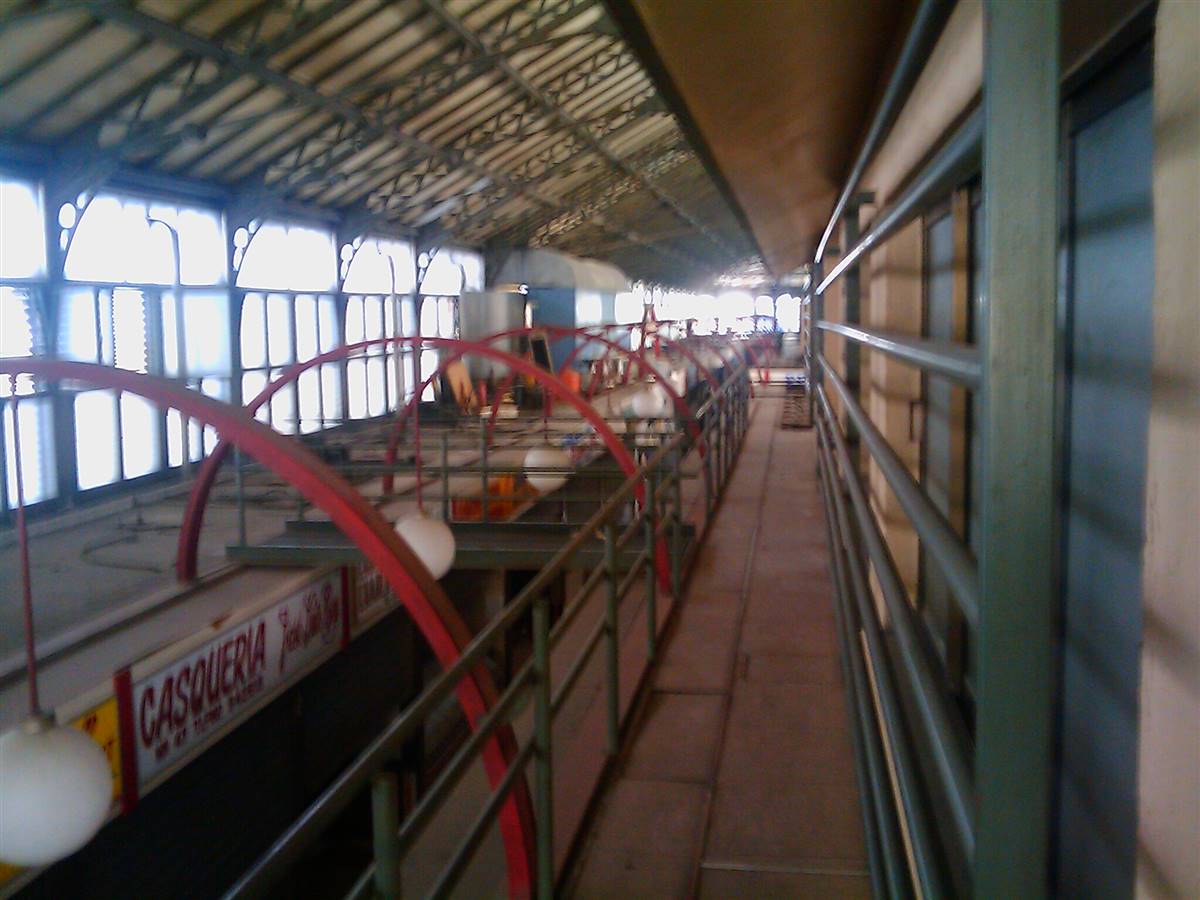
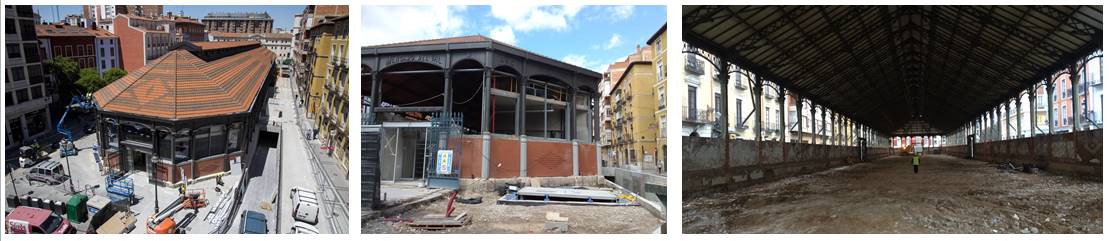
RENOVATION PROCESS
Architecture
BUILDING DESCRIPTION
State of repair
HERITAGE SIGNIFICANCE
Aim of retrofit
Valladolid City Council
Plaza Mayor 1, Valladolid (Spain)
Construction company and subcontractors
Valladolid (Spain)
R&D companies within the CommONEergy project
-
-
-
CommONEnergy partners
-
HVAC and electrical engineers in charge of the detailed definition of the HVAC and electrical layouts of the market.
-
RETROFIT SOLUTIONS
External Walls
Solid brick at bottom
Bricks at top
The old wall was replaced by a new glazing façade. The glazed façade is made by modular façade elements that aim at integrating thermal, daylighting and ventilation functions being responsive when internal and external loads change.
The old brick wall from 1982 was not catalogued as a heritage part of the building.
20 mm
60 mm
0 mm
30 mm
20 mm
120 mm
0mm
0 mm
Glazing wall
The old brick wall from 1982 was not catalogued as a heritage part of the building.
20 mm
60 mm
0 mm
60 mm
0mm
0 mm
Windows
Glazing façade and skylights
New glazing façace and windows for the natural ventilation. The glazing façade increase daylighting and make the commercial activities visible from the outside.
The original windows and skylights were not catalogued as a heritage part of the building.
Existing window type | Awning/Hopper |
Existing glazing type | Single |
Existing shading type | Roller blinds |
Approximate installation year | 1983 |
New window type | Fixed for the façade and movable for the natural ventilation windows |
New glazing type | Double |
New shading type | Shading elements in the south façade (movable lamellas). |
New window solar factor g [-] | 0,333 |
Other interventions
ROOF
GROUND FLOOR
MEASURES TO INCREASE AIRTIGHTNESS
The old roof was completely removed
The old roof was not catalogued as a heritage part of the building.
200 mm
200 mm
20 mm
24 mm
10 mm
50 mm
8 mm
More info D6.3 Energy Audit "CommONEnergy project"
The floor was not catalogued as a heritage part of the building.
20 mm
250 mm
350 mm
50 mm
150 mm
Reconstruction of the complete envelope (Façade, roof, windows).
HVAC
HEATING
VENTILATION
AIR CONDITIONING
DOMESTIC HOT WATER
Heating is covered with three reversible geothermal heat pumps getting temperature from vertical bareholes done in the ground (42 bareholes of 120 m). To cover the energy needs it has been selected a low temperature heating and cooling system with radiant floor on the ground floor and first floor and fan coils in the basement. The is also an AHU which can work also in free-cooling mode and has a heat recovery efficiency of more than 65%.
The old heating system based on Air/Water heat pumps was not maintaned.
New primary heating system | |
---|---|
New system type | Heat pump |
Fuel | Electricity |
Distribuition system | Radiant floor, fan coils and AHU |
Nominal power | 325.5 kW (heating) kW |
New AHU (Air Handling Unit). Natural ventilation strategies using the windows and skylights implemented in the contol system. When Natural Ventilation covers copletely the ventilation needs of the market, the AHU is OFF.
In the old building there was no mechanical ventilation system. Natural ventialtion was performed through doors and windows.
Original roof build-up | New ventilation system |
---|---|
Type ventilation system | AHU and Natural ventilation. Natural ventilation system reduce the cooling needs during summer and reduce the energy consumption for the mechanical ventilation. |
Type flow regime | The connection of natural ventilation system to the BEMS allow introducing control strategies (e.g: swith off the mechanical ventilation in ther market when natural ventilation is activated) |
Heat recovery | Yes |
Humitidy recovery | No |
Nominal power | kW |
Electric power | kW |
Control system | BEMS controls all the energy systems of the market. The BEMS includes all the natural ventilation strategies implemented. There are in the market CO2 sensors to measure the quality of the air. |
Cooling is covered with three reversible geothermal heat pumps getting temperature from vertical bareholes done in the ground (42 bareholes of 120 m). To cover the energy needs it has been selected a low temperature heating and cooling system with radiant floor on the ground floor and first floor and fan coils in the basement.
The old cooling system based on Air/Water heat pumps was not maintaned.
New cooling system | |
---|---|
Type | Heat pump |
Distribuition system | Radiant floor and fan coils |
Nominal power | 387 kW (cooling) kW |
Electric power | kW |
For the DHW the geothermal heat pumps are supported by storage tanks with electric immersion heaters for legionella prevention. The geothermal heat pumps can produce at the same time DHW and cooling in summer.
The old DHW system based on a natural gas boiler was not maintaned.
New DHW system | |
---|---|
Type | with heating system |
Hot_water_tank | Yes |
With heat recovery | Yes |
RENEWABLE ENERGY SYSTEMS
Geothermal
In order to supply both heating and cooling three reversible ground to water geothermal heat pumps are installed, getting temperature from vertical boreholes done on the ground (42 boreholes of 120 m). In order to cover the energy needs it has been selected a low temperature heating and cooling system, with radiant floor on the ground floor and first floor and fan coils in the basement. For the DHW supply, the geothermal pumps will be supported by storage tanks with electric immersion heaters for legionella prevention. The geothermal pumps can produce at the same time DHW and cooling in summer.
Not affect the conservation of the building as the geothermal system is within the building in the basement. Before the retrofitting, no RES systems were installed
Geothermal System |
---|
Energy Efficiency
Voluntary certificates: No
Primary Energy 326,9 kWh/m2.y
Consumption_estimation_Before: 61,7 kWh/m2.y
Consumption_estimation_After: 20 kWh/m2.y
Primary Energy
Consumption_estimation_Calculation_method: Based on primary energy factors from RITE (Spanish Regulation of Thermal Installations in Buildings)
Consumption_estimation_Before: 1300,2 kWh/m2.y
Consumption_estimation_After: 326,9 kWh/m2.y
Type_of_monitoring: Continuous
Description: Internal monitoring network with temperature, RH and CO2 sensors.
External Climate
Type_of_monitoring: Continuous
Description: Weather Station with temperature, humidity, wind speed, wind direction, precipitation and radiation sensors.
Construction
Type_of_monitoring: Continuous
Description: A large number of sensors (Thermal and electrical meters, comfort, etc.) were installed in the market with control and evaluation purposes. The innovative integration of the multifunctional façade together with the ventilation and shading system, in addition to the geothermal heat pumps and other devices, made necessary the integration of a high number of sensors.
Internal Climate
The project addressed thermal comfort mainly through natural ventilation and shading strategies. Also the HVAC system was completely redesign.
Yes, the project addressed the IAQ mainly with natural ventilation strategies. Inside the market there were installed CO2 sensors to contol the levels of CO2. Also some punctual measurements of COVs and formaldehide were performed inside the market.
The project addressed visual comfort and for this a new glazzing façade with a shading system was installed to improve as much as possible the daylighting. Also the project installed some luminosity sensors inside the market for the control purposes.
Some punctual measurements of acoustic comfort were developed inside the market.
Costs
The total intervention cost was covered with different sources: - European Commission provide a grant through the European Project "CommONEnergy". - Public funds from the Valladolid City Council and Junta de Castilla y León. - Private funds from the owners of the stalls.
No
Environment
emissions_at_use_stage_before_intervention: 193 kgCO2/m2 per m2
emissions_at_use_stage_after_intervention: 48 kgCO2/m2 per m2
emissions_before_use: NA