Farm house Huber
Fröllerberg 117
39037
Rodeneck, Italie
Architect
Owner
Contact Details
Other Information

Climate Zone D/E
Altitude 1500
HDD 2669
CDD 5442
Conservation Area:
No
Level of Protection:
Architectural protection DGP-LAB 5041 07/10/1985
Year of last renovation:
2008
Secondary use:
Residential (rural)
Building occupancy:
Permanently occupied
Number of occupants/users:
3
Building typology:
Detached house
Number of floors:
2
Basement yes/no:
Oui
Number of heated floors:
2
Thermal envelope area [m²]:
394,0
Volume [m³]:
1277,0
NFA calculation method:
Useful area (it)
External finish:
Rendered
Internal finish:
Plastered (on hard)
Roof type:
Pitched roof

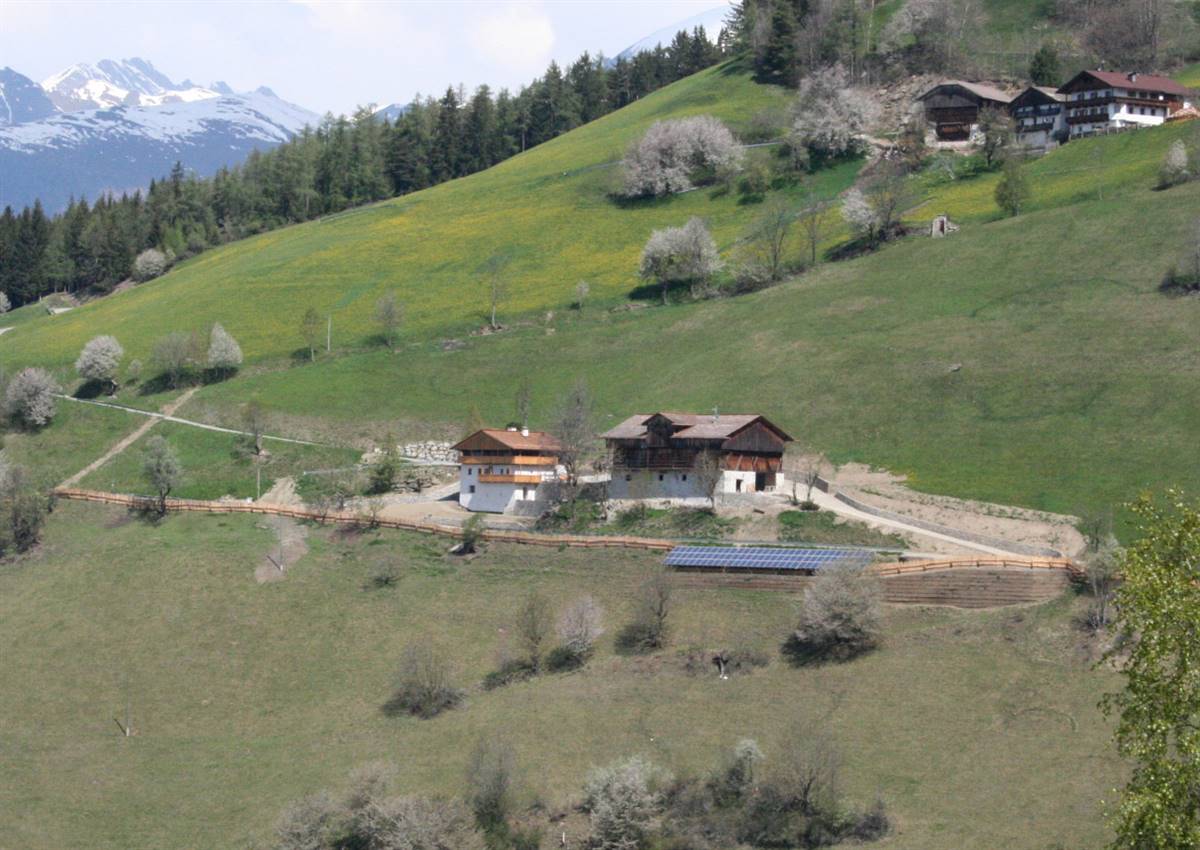
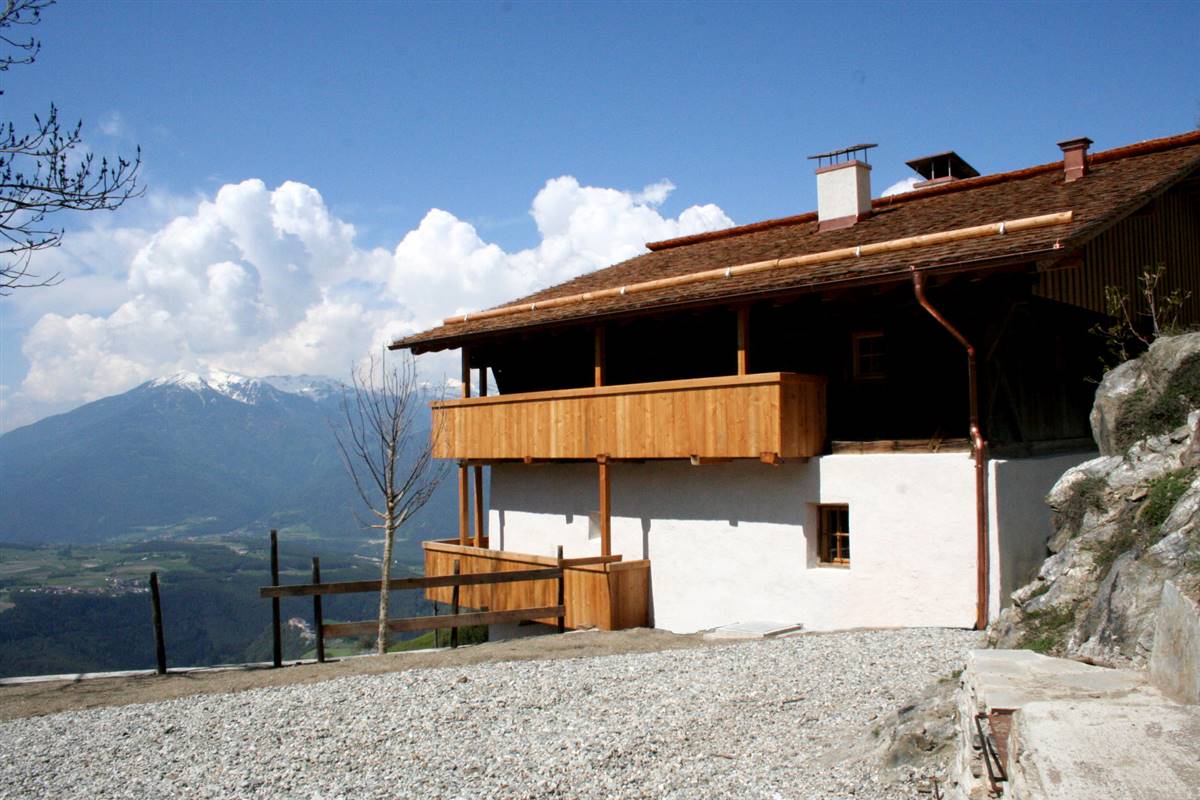
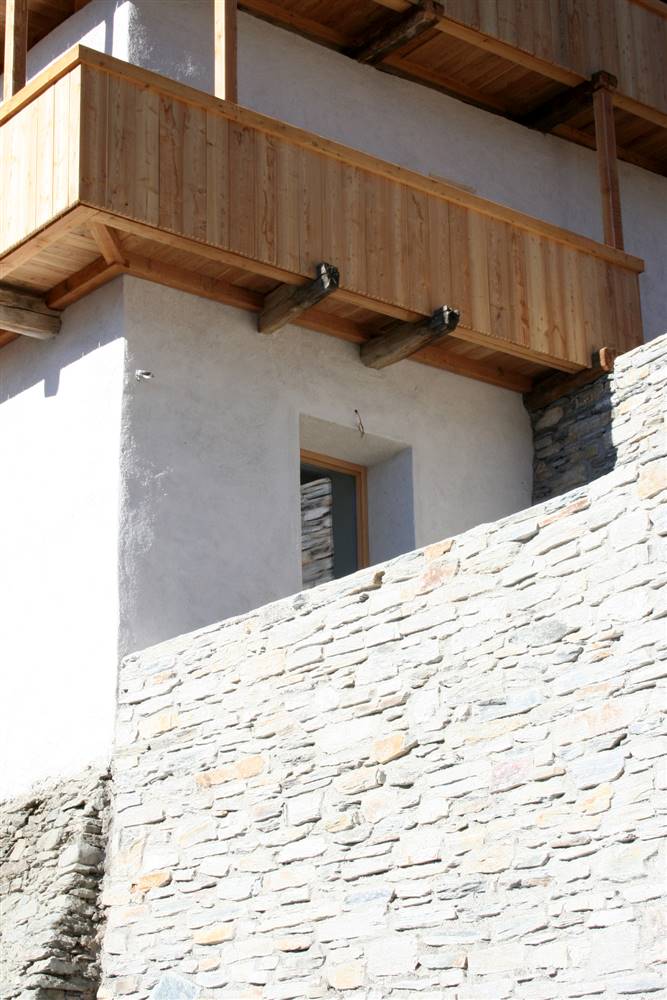
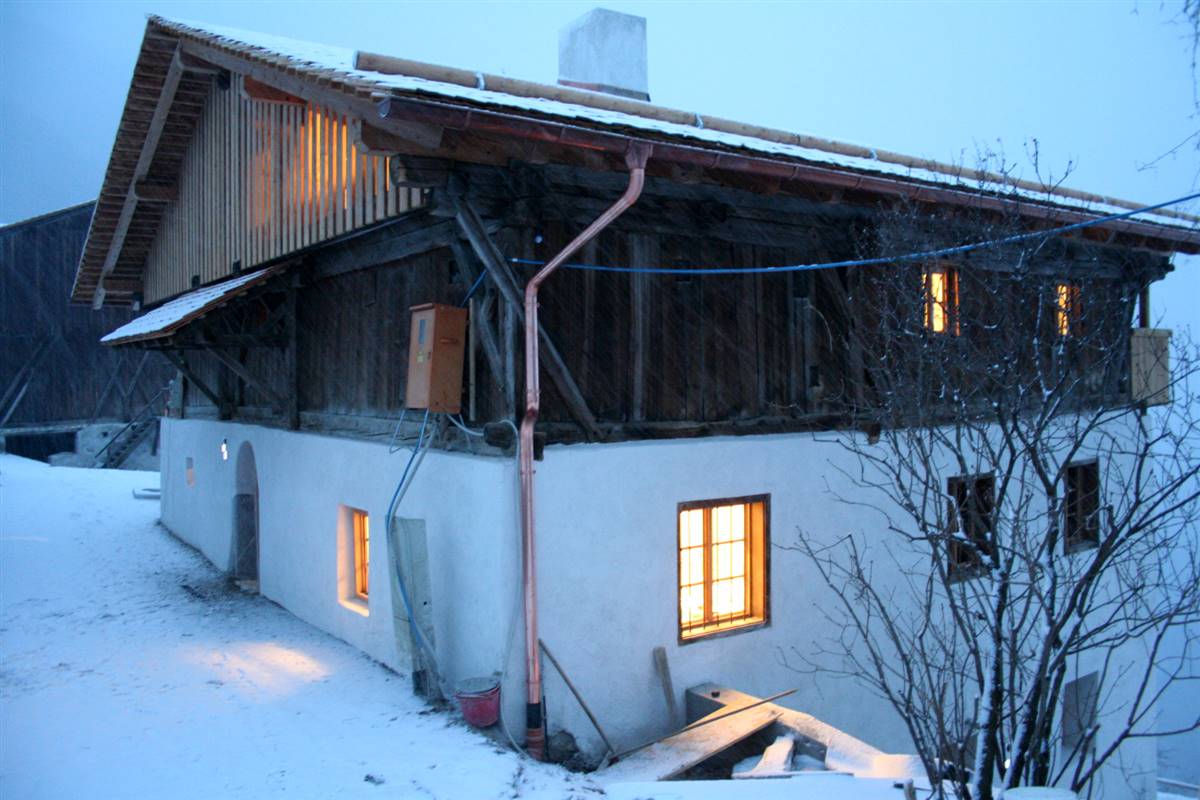
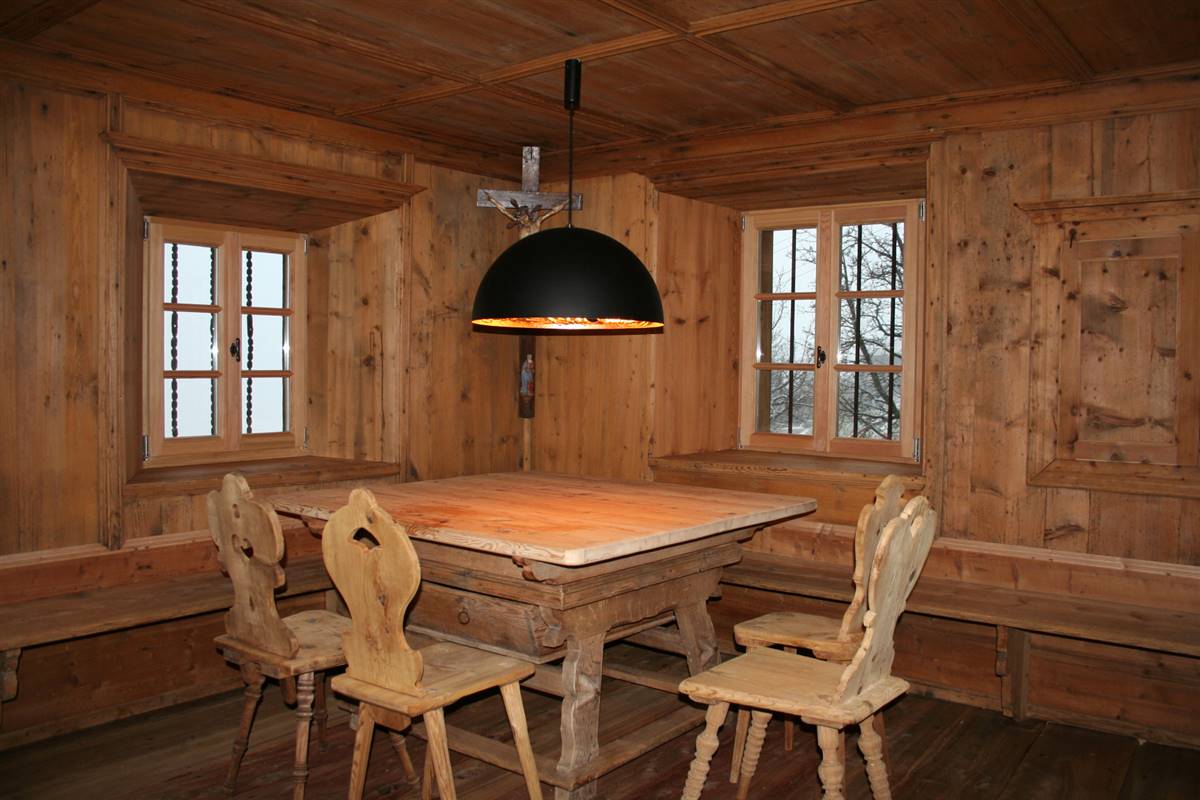
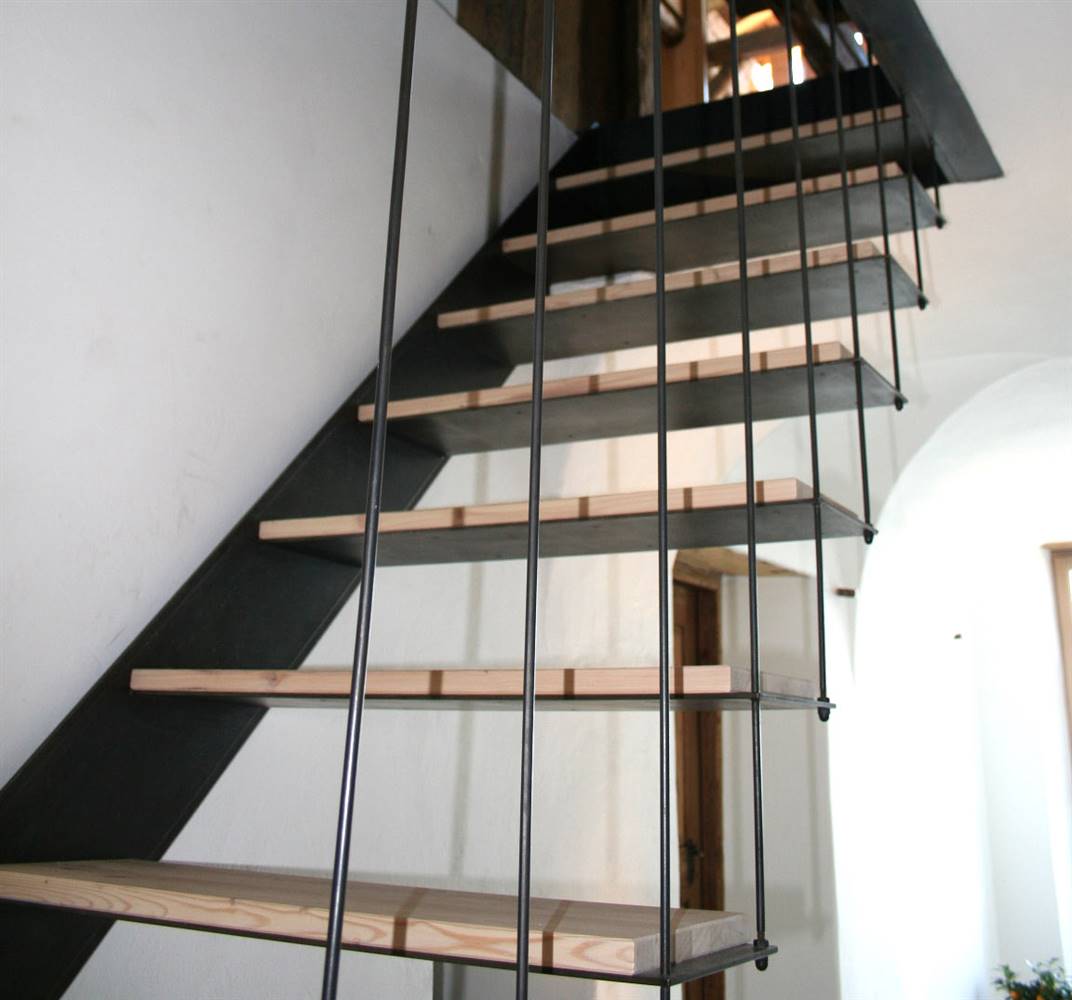
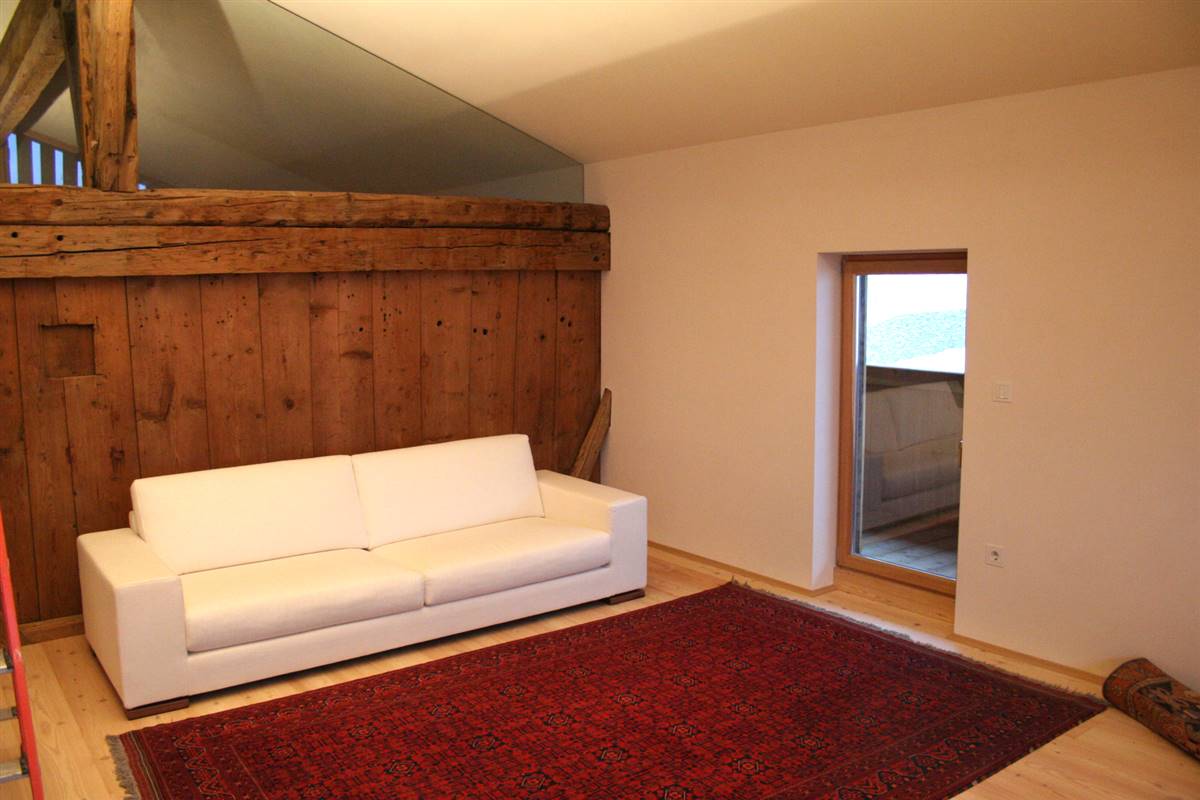
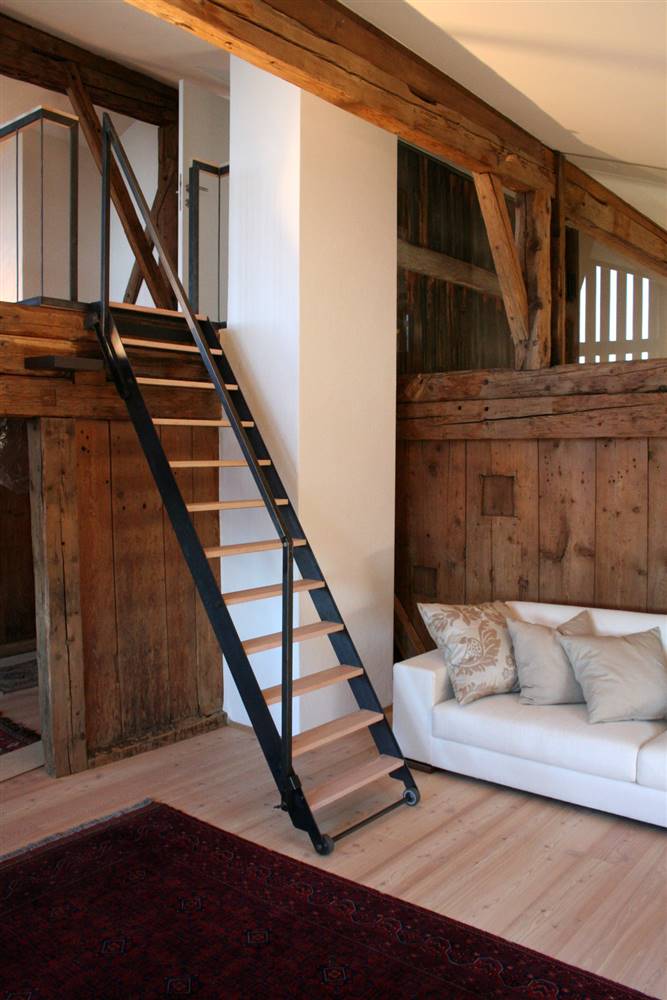
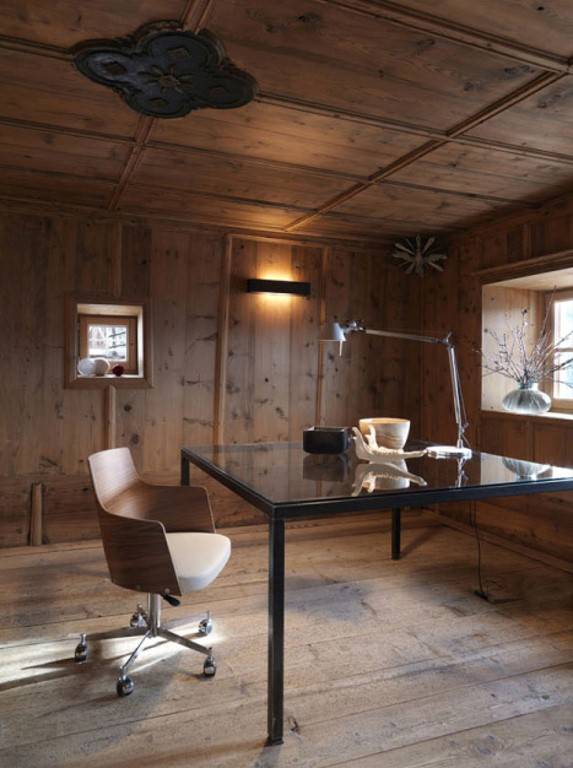
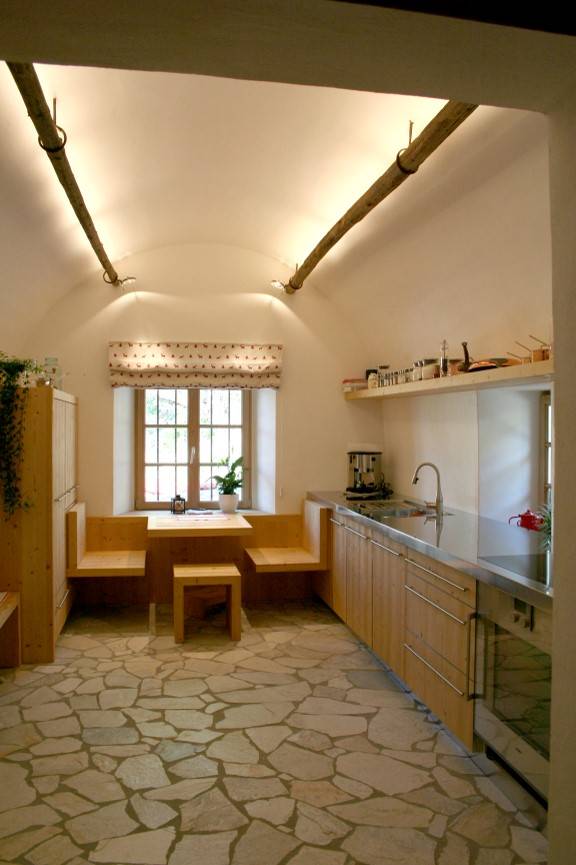

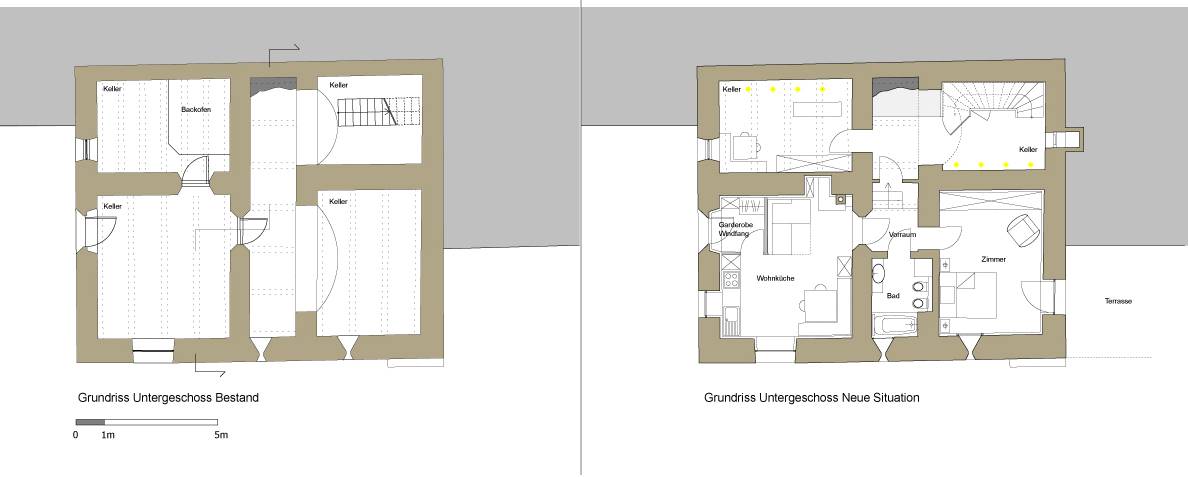
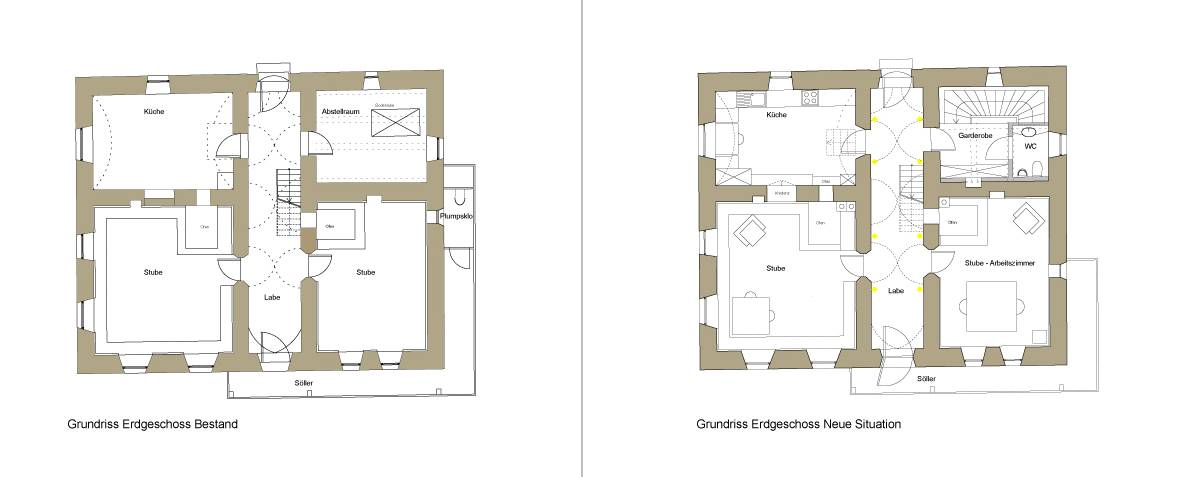
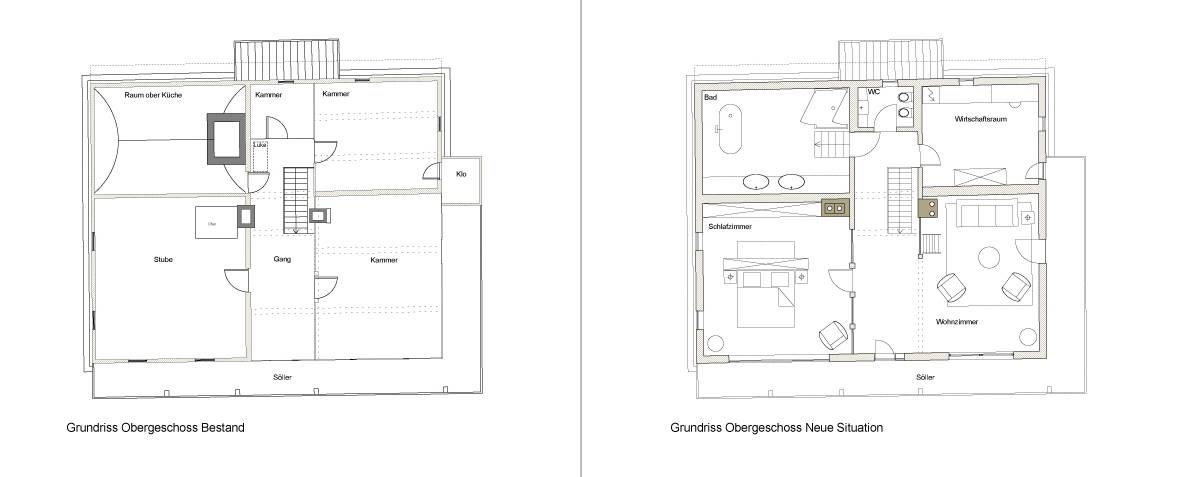
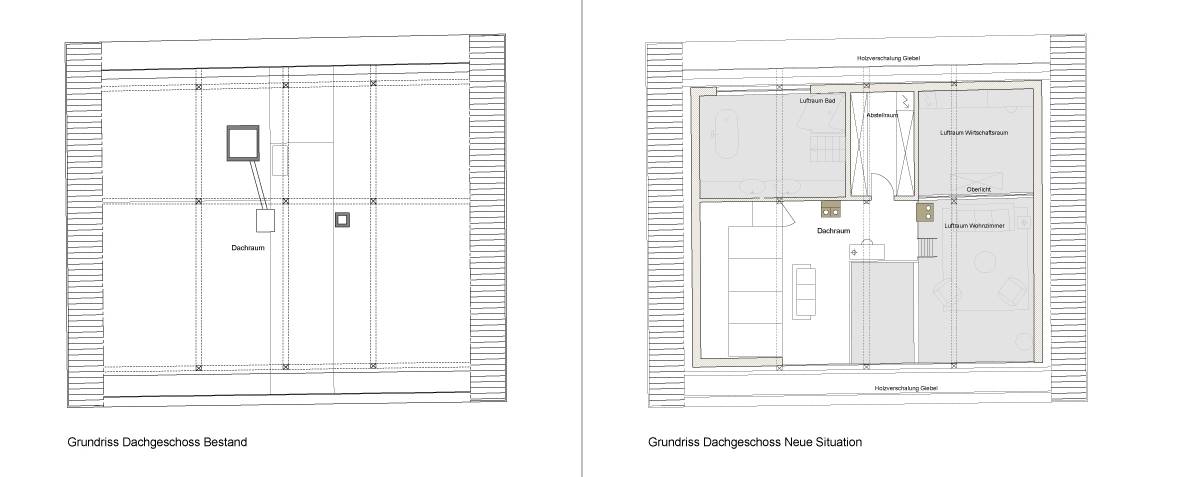
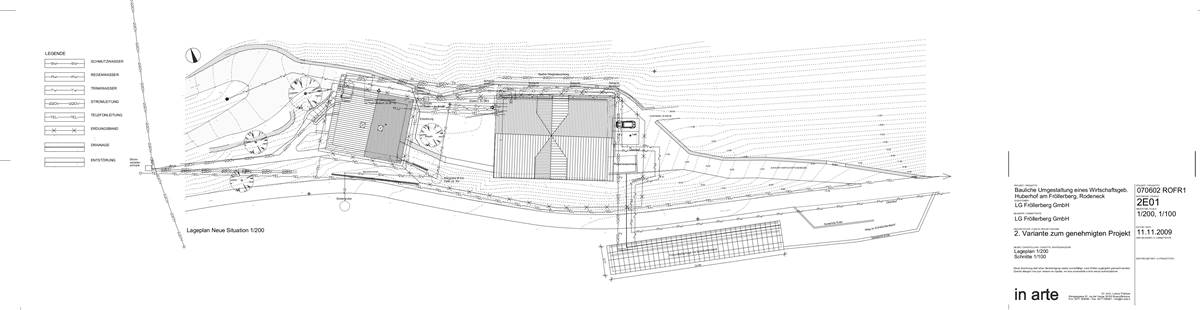
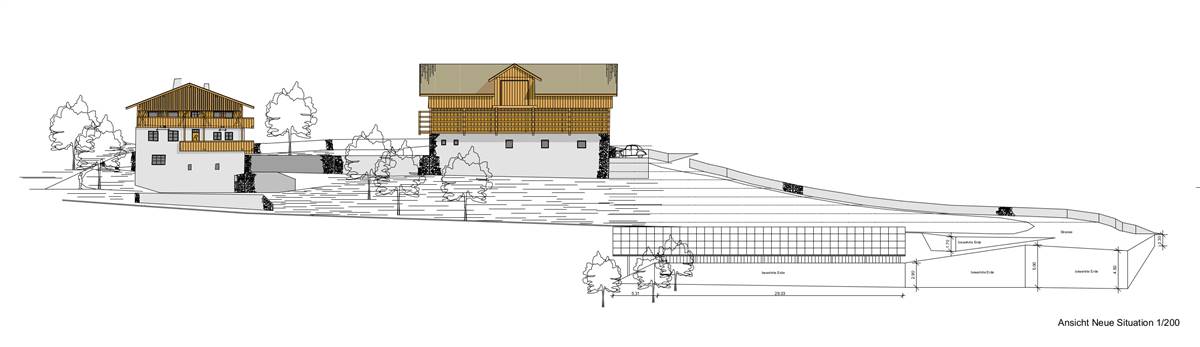
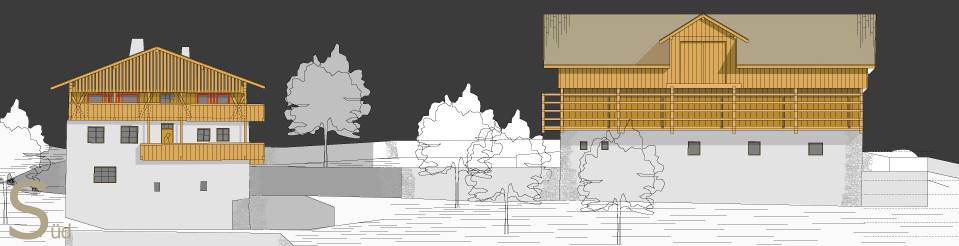
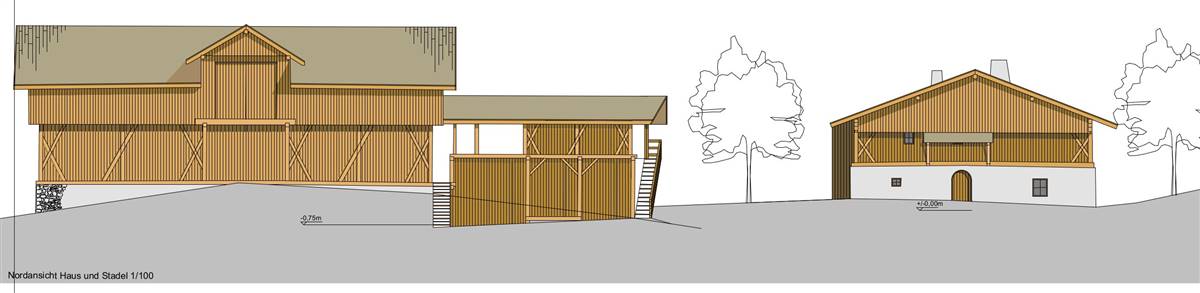
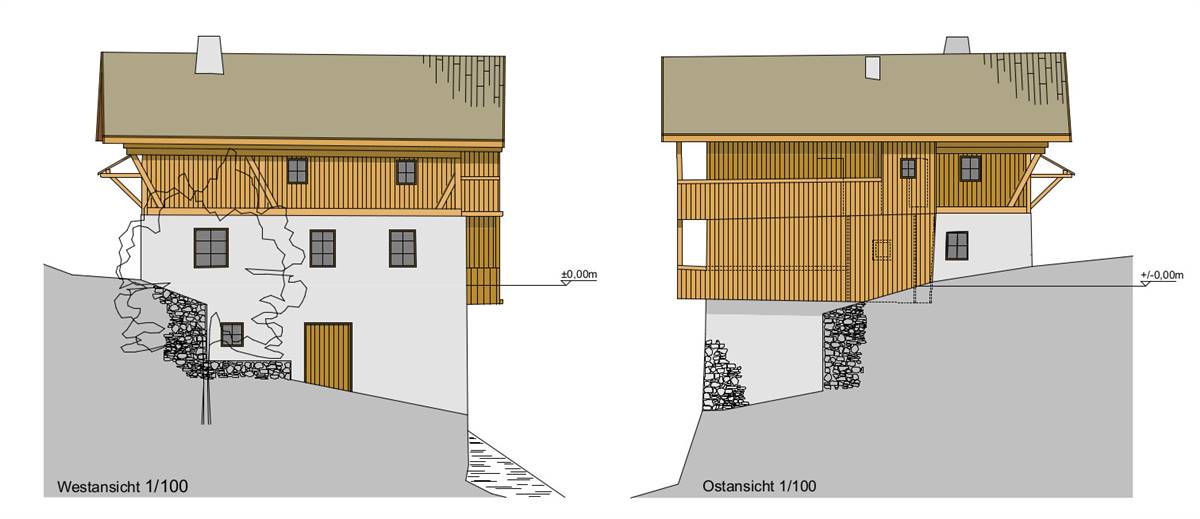
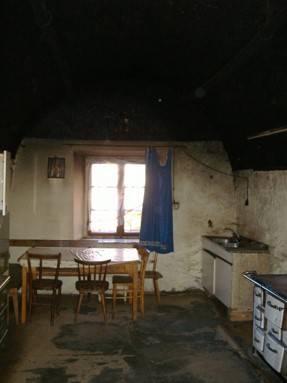
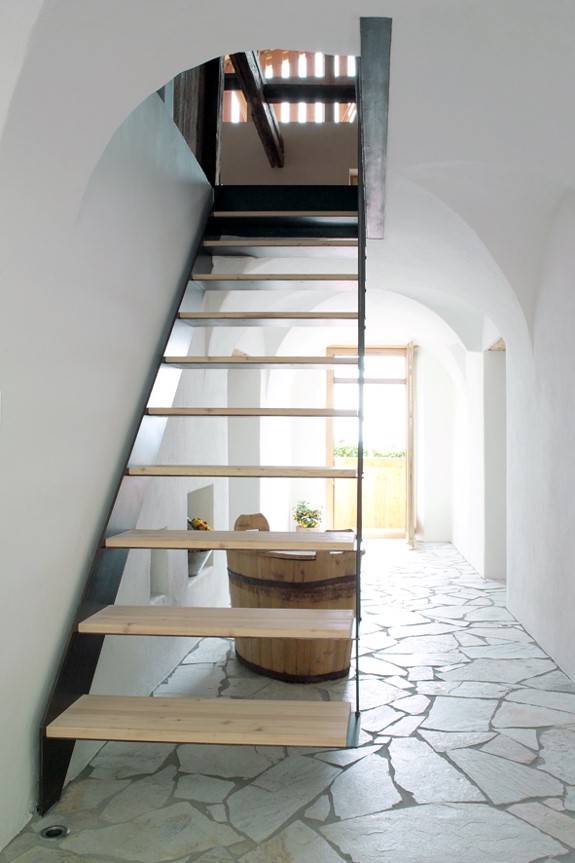
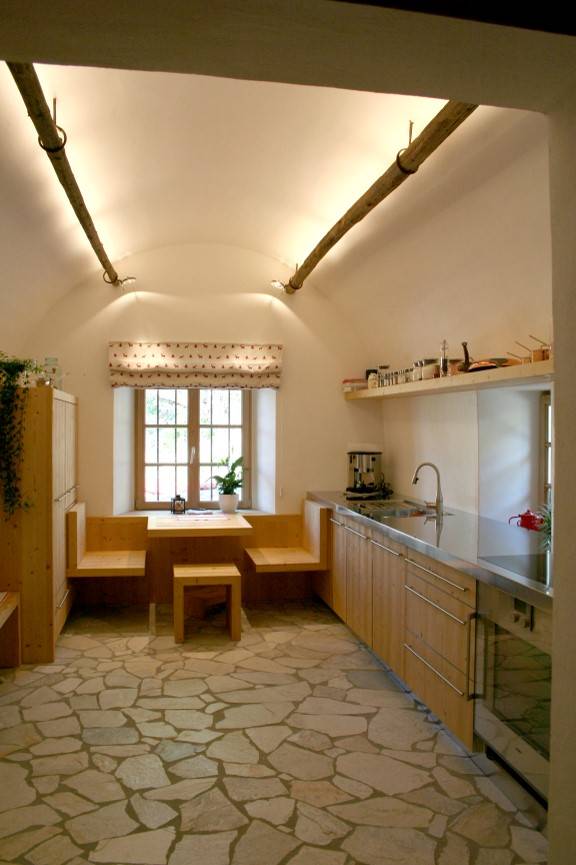
RENOVATION PROCESS
Architecture
BUILDING DESCRIPTION
State of repair
HERITAGE SIGNIFICANCE
Aim of retrofit
Lorenz Pobitzer
Sparkassenstraße 5 / Via cassa di risparmio 5 I-39100 Bolzano / Bozen
info@in-arte.it
RETROFIT SOLUTIONS
External Walls
Basement stone wall
External wall I
External wall II
An 80 mm gaseous concrete wall was placed in front of the original stone wall for thermal insulation and protection from the raising dump.
As the building is listed, it can only be insulated towards the inside.
700 mm
700mm
80 mm
20 mm
The main wall was a masonry wall of approximately 60m, partly not plastered with wood panelling towards the inner surface. Its refurbishment dealt with the exterior plaster's renovation, the application and roughening to the interior plaster, then internal wall insulation in wood fibre panels 2 + 2 cm between the masonry wall and the panelling.
The solution was successful from a conservation point of view. The masonry wall was insulated from the inside. Hence, the wall's original wooden panelling appearance remained unchanged while offering the appropriate level of thermal insulation.
600 mm
20 mm
20mm
600 mm
20 mm
20 mm
20 mm
The first-floor wall was a half-timbered construction. A black windproof paper barrier was attached to the old wooden formwork's inner surface, then a new wooden construction was added, which was insulated with a 12 cm wood fiberboard. Additionally, a 4 cm continuous wooden fibreboard was included along with glued OSB panels and a vapour barrier. A plaster finishes completed the solution.
.
400 mm
20 mm
400mm
2 mm
120 mm
40 mm
30 mm
20 mm
Windows
Double single-glazing
Existing windows were exchanged with custom-made new units by a local furniture maker. The aim was to build a two-sash window with two glazing bars to achieve high energy performance while being of high aesthetic quality.
In order to preserve the appearance of the original windows, new windows were modelled according to the old ones in terms of proportions and profile widths. To improve the thermal performance of the window, an insulating glass unit was installed.
Existing window type | Double window |
Existing glazing type | Single |
Existing shading type | NA |
Approximate installation year | 1900 |
New window type | Casement window |
New glazing type | Double |
New shading type | NA |
New window solar factor g [-] | 0,0 |
Other interventions
ROOF
GROUND FLOOR
OTHER
The roof was completely refurbished.
The refurbishment was conducted according to traditional construction technologies.
20 mm
30 mm
20 mm
0 mm
0 mm
80 mm
120 mm
20 mm
The floor was lowered to accomplish the habitability requirements. A 14 cm concrete layer was added to a gravel substructure with drainage and and a subfloor with 10 cm reinforced cement. 12 cm rigid foam insulating XPS boards were also added. Then an 8 cm screed and a wooden floor completed the slab.
.
19 mm
600 mm
21 mm
80 mm
120 mm
100 mm
140 mm
600 mm
600 mm
The upper floor ceiling was partly removed to satisfy the users' desire for brightness, view, and spaciousness. An open roof-space with a gallery was created. The cladding of the existing gable was removed and replaced with broken laths in brushed flat boards. Behind the cladding, there are large glazed fields that lit the living room in one case and the bathroom in the other. A skylight in the living room also lit the workspace behind it and widens the feeling of space.
The glazed cladding preserves the external historic appearance and allows visuals, lights and shadows at the same time.
HVAC
HEATING
DOMESTIC HOT WATER
Three traditional wood stoves provided heating: two on the ground floor and one on the basement in the kitchen. For the other parts of the building, a floor heating system was installed. The hot water needed is produced by electrical boilers mainly powered by the PV system.
The wood stoves in trouble were demolished and rebuilt true to the original.
New primary heating system | New secondary heating system | |
---|---|---|
New system type | Stove | Boiler |
Fuel | Biomass | Electricity |
Distribuition system | Air | Radiating floor |
Nominal power | - kW | kW |
RENEWABLE ENERGY SYSTEMS
Photovoltaic
Photovoltaic panels were installed on the roof of a sheepfold. The PV system covers 88% of the electrical needs of the building.
This solution allows the character and the appearance of the historic building to remain unchanged while producing energy.
The solution adopted is considered as a decentralised power production where PVs are placed on a structure closed to the main historic building so that the building remains unchanged.
Photovoltaic System | |
---|---|
Type | |
Collector area | 200,0 m² |
Total nominal power | 0,0 kW |
Overall yearly production | 45000,0 kWh |
Energy Efficiency
Voluntary certificates: No
Consumption_estimation_Calculation_method: NA
Consumption_estimation_Before: 151 kWh/m2.y
Consumption_estimation_After: 129 kWh/m2.y
Primary Energy
Consumption_estimation_Calculation_method: NA
Consumption_estimation_Including_DHW: No
Type_of_monitoring: Punctual
Internal Climate
The temperature of the building during day and night was considered adequate all over the year. No ventilation measures are taken during the summer, neither at daytime (no shielding elements are in place) nor at nighttime.
Occupants are greatly satisfied with the air quality of the building.
Occupants are greatly satisfied with the level of daylight in the building.
The occupants reported that the building envelope adequately shields by any unwanted noise.
Costs
NA
No