Ryesgade 30 A-C
Ryesgade
2200
Copenhagen (Nørrebro), Dänemark
Architekt
Besitzer
Ansprechpartner
Other Information
Reports in Danish

Klimazone Cfb
Höhe über dem Meer 50 m ü.d.M.
Heizgradtage 2906
Kühlgradtage 0
Ensembleschutz:
Nein
Stufe der Unterschutzstellung:
SAVE lvl 4 - Facade can not be changed
Letzte Sanierung:
2011
Vorhergehende Sanierungen:
0
zusätzliche Nutzung:
Wholesale & Retail
Gebäudebelegung:
Permanently occupied
Anzahl der Bewohner/Nutzer:
60
Gebäudetyp:
Tenement (apartments)
Anzahl der Stockwerke:
8
Keller ja/nein:
Ja
Anzahl der beheizten Stockwerke:
6
Bruttogeschossfläche [m²]:
3680,0
Thermische Gebäudehülle [m²]:
1260,0
Volumen [m³]:
8280,0
NGF Berechnungsmethode:
Danish Building Regulations
Außen:
Exposed brickwork
Innen:
Plastered (on substructure)
Dach:
Pitched roof

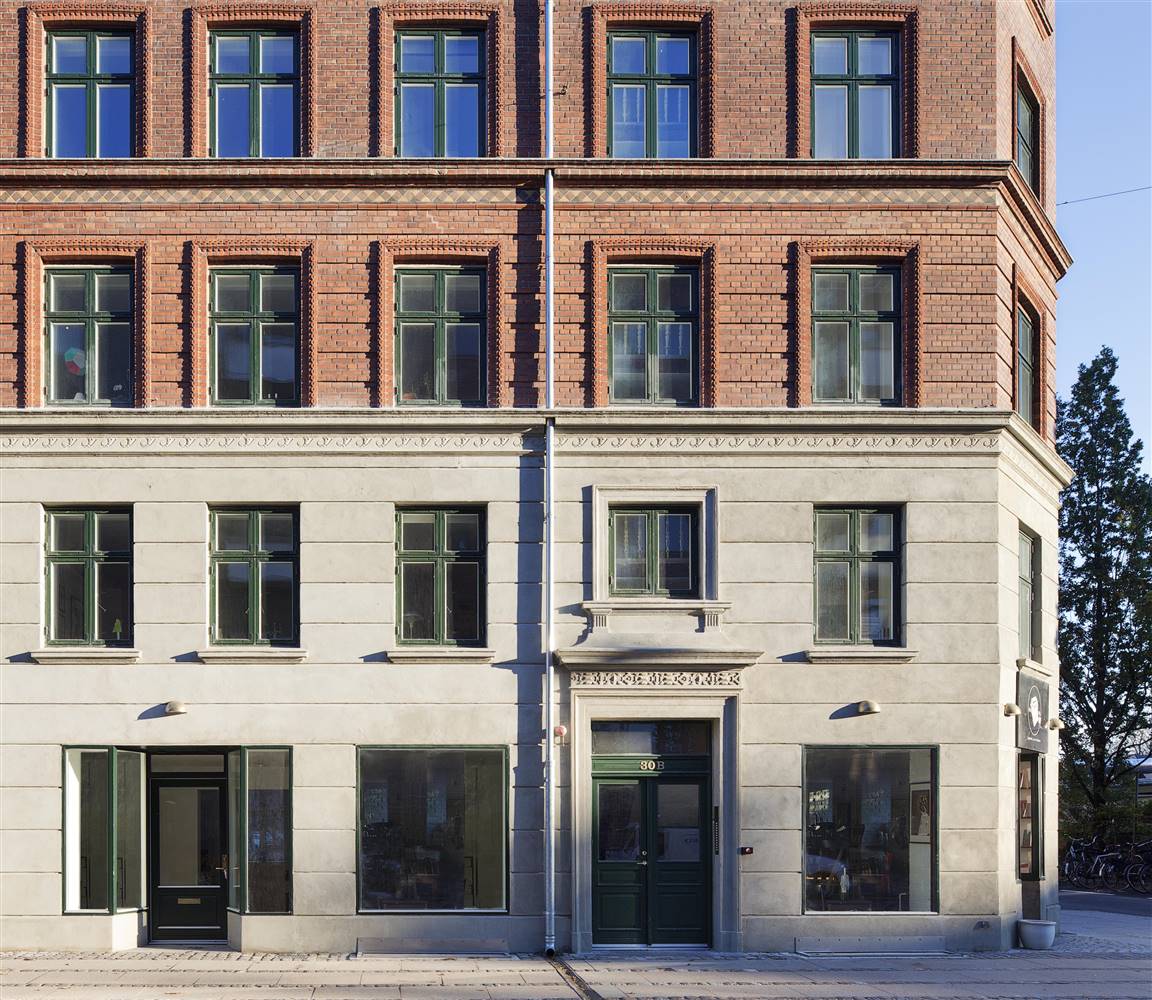
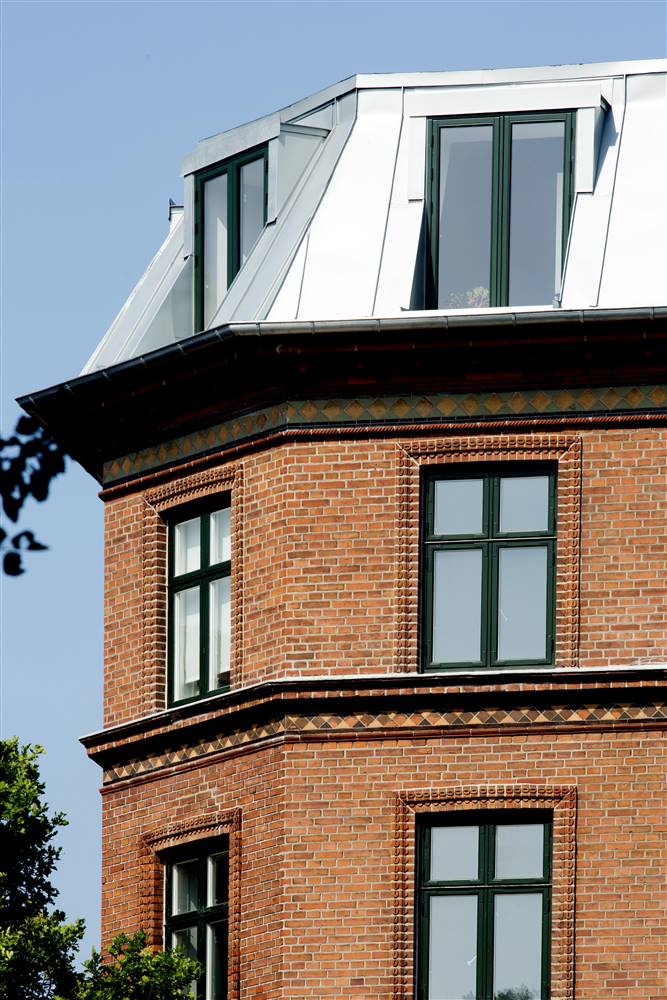
.jpg)
.jpg)
.jpg)
RENOVIERUNGS-PROZESS
Architektur
BESCHREIBUNG
Erhaltungszustand
DENKMALWERT
Ziel der Sanierung
Municipality of Copenhagen
Njalsgade 13, 2300 Copenhagen S, Denmark
NA@NA.NA
Tel.+45 3366 3366
Krydsrum Architects and Rönby.dk (Leif Rönby)
na
leif@ronby.dk
Tel.+45 6160 0699
Ekolab
Vestergade 48 H 2. tv., 8000 C Aarhus, Denmark
ekolab@ekolab.dk
Tel.+45 8613 2016
Falkon Rådgivende Ingeniører
C. F. Richs vej 107, 4. sal, 2000 Frederiksberg, Denmark
info@falkon.dk
Tel.+45 3536 4500
Consultant to the building owner: Advokaterne Arup & Hvidt
Nørre Voldgade 88
ahlaw@aruphvidt.dk
Tel.+45 3313 8580
Hygrothermische Bewertung Yes
Life Cycle Analysis (LCA) None
Anderes None
SANIERUNGS-LÖSUNGEN
Außenwände
Brick wall - facades
The walls are massive brick walls ranging from 1½ stone (350 mm) to 3 stone (710 mm) in thickness with the widest walls at the ground floor. The parapets have 1 stone (235 mm) thickness. The mean U-value before renovation was 1.40 W/m2K. The facade walls were insulated on the inside with 40 mm Aerorock (a mix of rock wool and aerogel with a thermal transmittance of 0.019 W/mK) for apartments in stairwell A and B and 40 mm Kingspan (phenolic foam) insulation (with a thermal transmittance of 0.020 W/mK) for apartments in stairwell C. In both cases the finish is gypsum boards. The U-value after renovation was approx. 0.4 W/m2K. The gable wall (fire-proofing) towards the gate, which was not protected, was insulated on the outside with 250 mm rock wool with a thermal transmittance of 0.039 W/mK. This resulted in a U-value of 0.15 W/m2K.
Adding insulation to the inside of the contruction is a conservation compatible solution since is does not change the appearance of the building facade.
710 mm
710mm
40 mm
13 mm
Fenster
Facade windows
The original windows were wooden frames with 1 pane of glass and a U-value of 4.20 W/m2K, however some of the original windows had had a layer of glass added on the inside to improve energy aspects and reduce draught. The new windows had 1 + 2 panes of glass. The 2-pane section has krypton gas filling and the total U-value of the windows is 0.89 W/m2K.
Due to the building's status as conservation-worthy, the renovation could not change the facade expression. However, the municipality accepted that the windows were replaced with new windows that were constructed like the old windows. The new windows were specially developed for the project with drawn glass in the outer layer of the pane to give the window the same expression and mirroring quality as the original ones from 1896. The new windows that were installed are wooden windows with switched frames 1 + 2 from Frovin Vinduer and Døre A/S.
Fenstertyp Bestand | Double window |
Verglasungsart Bestand | Single |
Verschattung Bestand | NA |
Ungefähres Einbaujahr | 1896 |
Neuer Fenstertyp | Double window |
Verglasungsart des neuen Fensters | Triple |
Verschattung des neuen Fensters | NA |
Neuer Energiedurchlassgrad g [-] | 0,5 |
Weitere Maßnahmen
DACH
Part of the renovation included adding new roof apartments to the top pf the building and thereby a whole new roof was added. Before the renovation the roof had a U-value of 0.52 W/m2K and after the renovation the new roof has a U-value of 0.21 W/m2K.
The roof was not part of the protected facade and therefore no restrictions were present. New roof terraces and PV panels are not visible from the street below.
12 mm
50 mm
2 mm
200 mm
HVAC
LÜFTUNG
Before the renovation the building had natural ventilation through open windows and leaks in the thermal envelope. Original ventilation shafts in toilets/bathrooms and kitchens were either blocked or did not work as intended. The renovation included three different types of mechanical ventilation, one for each entrance/stairwell (A, B and C). The purpose was to test different solutions in order for future projects to have a better understanding of which solutions would fit where. Stairwell A: Traditional central mechanical ventilation with heat recovery. Stairwell B: Central demand controlled mechanical ventilation with heat recovery. Stairwell C: Decentral mechanical ventilation with heat recovery. See documentation for further details.
All ducts and ventilation units are integrated and does not alter the parts of the building that needed preservation and therefore the solution is 100% conservation compatible.
Aufbau Bestandsdach | Neues Lüftungssystem |
---|---|
Lüftungstyp | Centralized |
Type flow regime | Cascade |
Wärmerückgewinnung | Ja |
Feuchterückgewinnung | Nein |
Nennleistung | 1,5 kW |
Elektrische Leistung | 1,0 kW |
Regelung | Supply constant air flow of 140 m3/h. Exhaust air volumen depends on humidity levels and whether the cooker hood is in use. |
ERNEUERBARE ENERGIE
Photovoltaik
80 m2 photovoltaics were added to the roof. The producer has calculated the expected production to 8,950 kWh per year and during the first year after renovation the system produced 11,000 kWh. The electricity production should cover most of the electricity used for mechanical ventilation in the apartments.
The photovoltaic system is placed on the roof and therefore did not influence the protected facade of the building.
The photovoltaic panels are placed on the roof (not integrated), but on a part of the roof that is not visible from the street.
Photovoltaic System | |
---|---|
Type | Monocrystaline |
Collector area | 80,0 m² |
Total nominal power | 10,0 kW |
Elevation angle | 30,0 |
Azimuth | 135,0 |
Overall yearly production | 8950,0 kWh |
Heating contribuition | 0,0 kW |
DHW contribuition | 0,0 kW |
Cooling contribuition | 0,0 kW |
Lighting contribuition | 0,0 kW |
Energieeffizienz
Freiwillige Zertifikate Nein
Berechnungsmethode Steady state simulation (e.g. EPC, PHPP)
Energieverbrauch vor Sanierung 152 kWh/m2.y
Energieverbrauch nach Sanierung 56 kWh/m2.y
Primärenergie
Berechnungsmethode NA
Energieverbrauch incl Brauchwarmwasser Nein
Type_of_monitoring: Punctual
Description: The heating consumption (space heating and domestic hot water) was measured before and after the renovation. Before the renovation the consumption was 155 kWh/m2 per year and after the renovation it was 83 kWh/m2 per year. Compared to calculations the measured consumption matches well for the before-situation but not for the after-situation. This was primarily due to the fact that tenants had a higher indoor temperature than assumed (22-23 C instead of 20 C) and that the efficiency of the heat recovery in ventilation systems was lower than expected. This also means that instead of heating energy savings of 63% the actual savings are around 53% - this is due to the so-called "rebound effect" where tenants "invest" some of the energy savings in an improvement of the indoor climate.
Raumklima
NA
NA
NA
NA
NA
Kosten
NA
Nein