Hof Neuhäusl
Seebach 23
6351
Scheffau am Wilden Kaiser, Austriche
Architect
Owner
Contact Details
Other Information
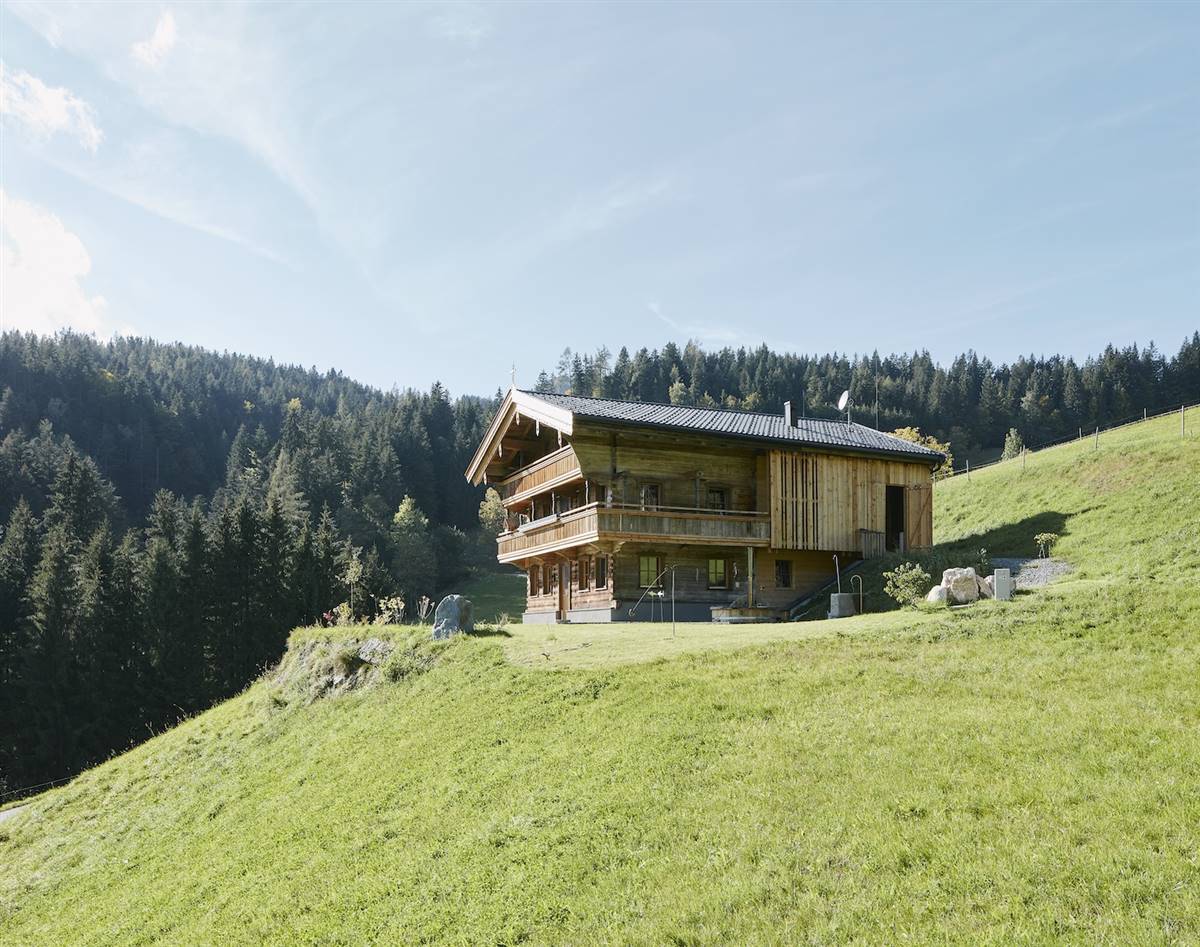
Climate Zone Dfb
Altitude 772
HDD 2446
CDD 574
Conservation Area:
No
Level of Protection:
Year of last renovation:
0
Building occupancy:
Discontinuous occupancy (i.e. holiday home)
Number of occupants/users:
2
Building typology:
Detached house
Number of floors:
3
Basement yes/no:
No
Number of heated floors:
3
Volume [m³]:
483,0
NFA calculation method:
NGF (de)
External finish:
Exposed woodwork
Internal finish:
Wood panelling
Roof type:
Pitched roof
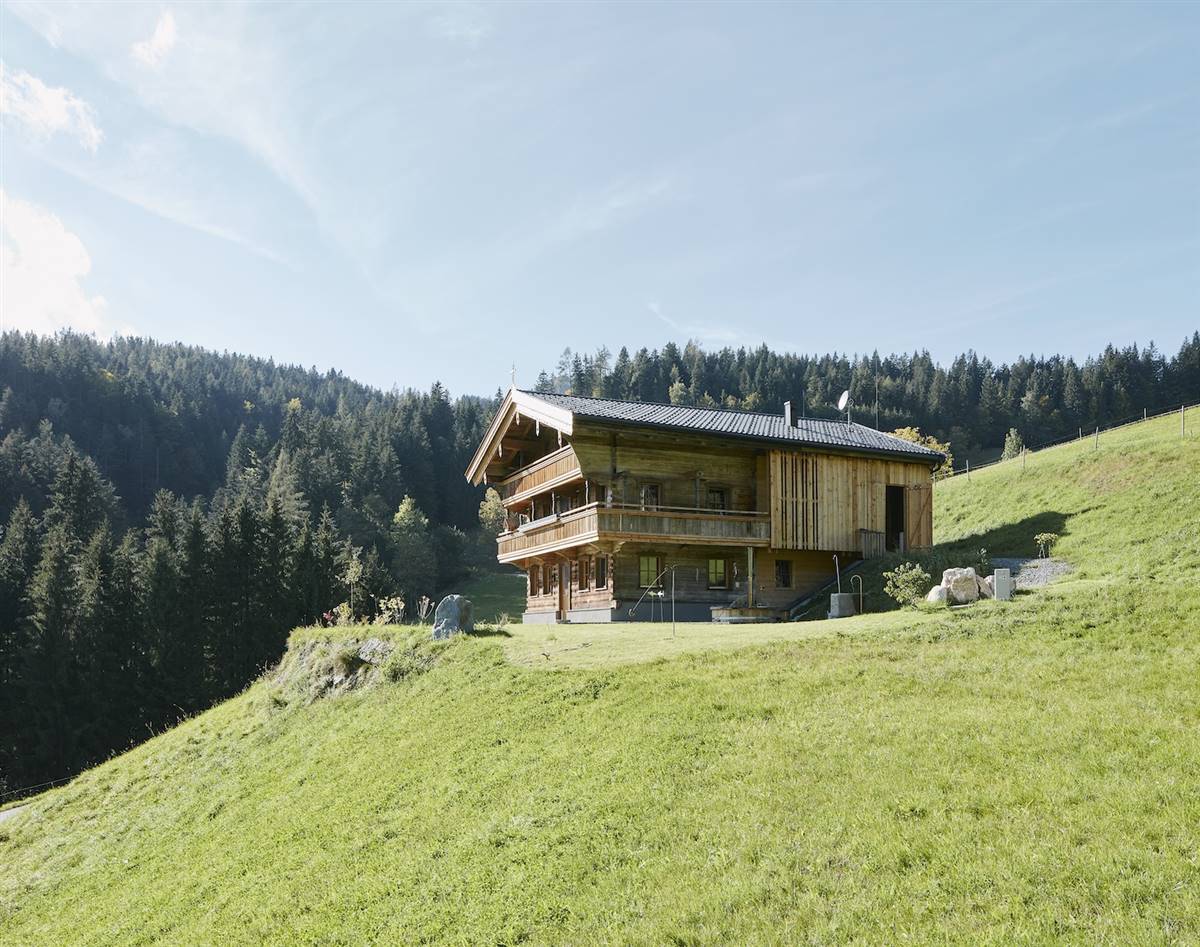
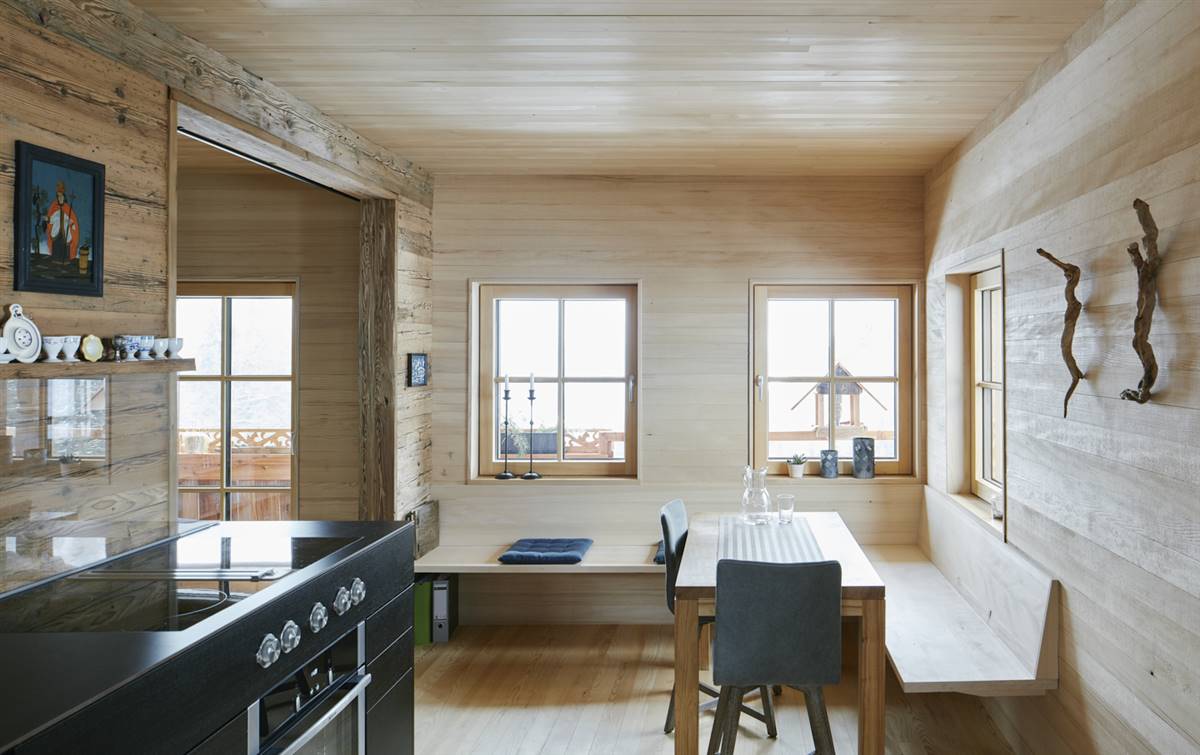
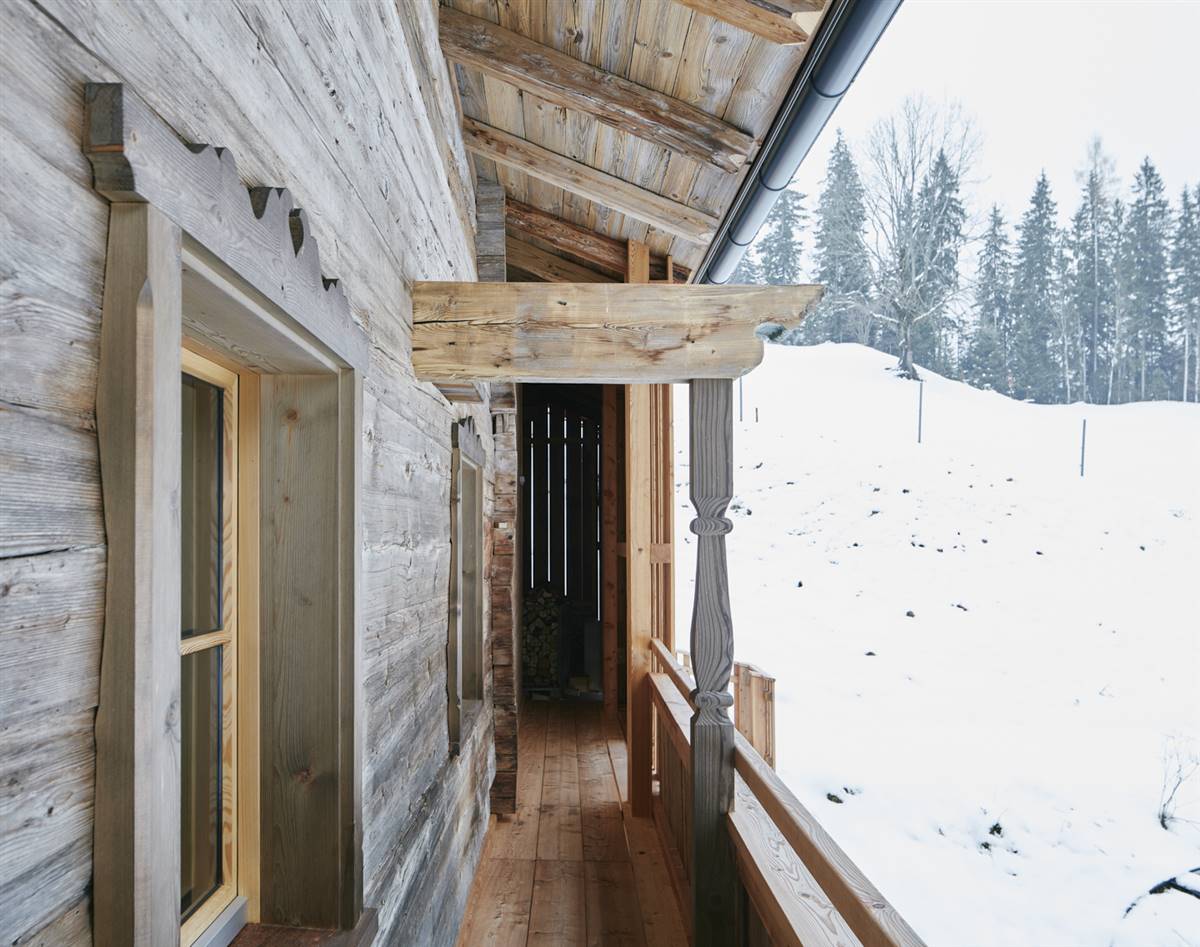
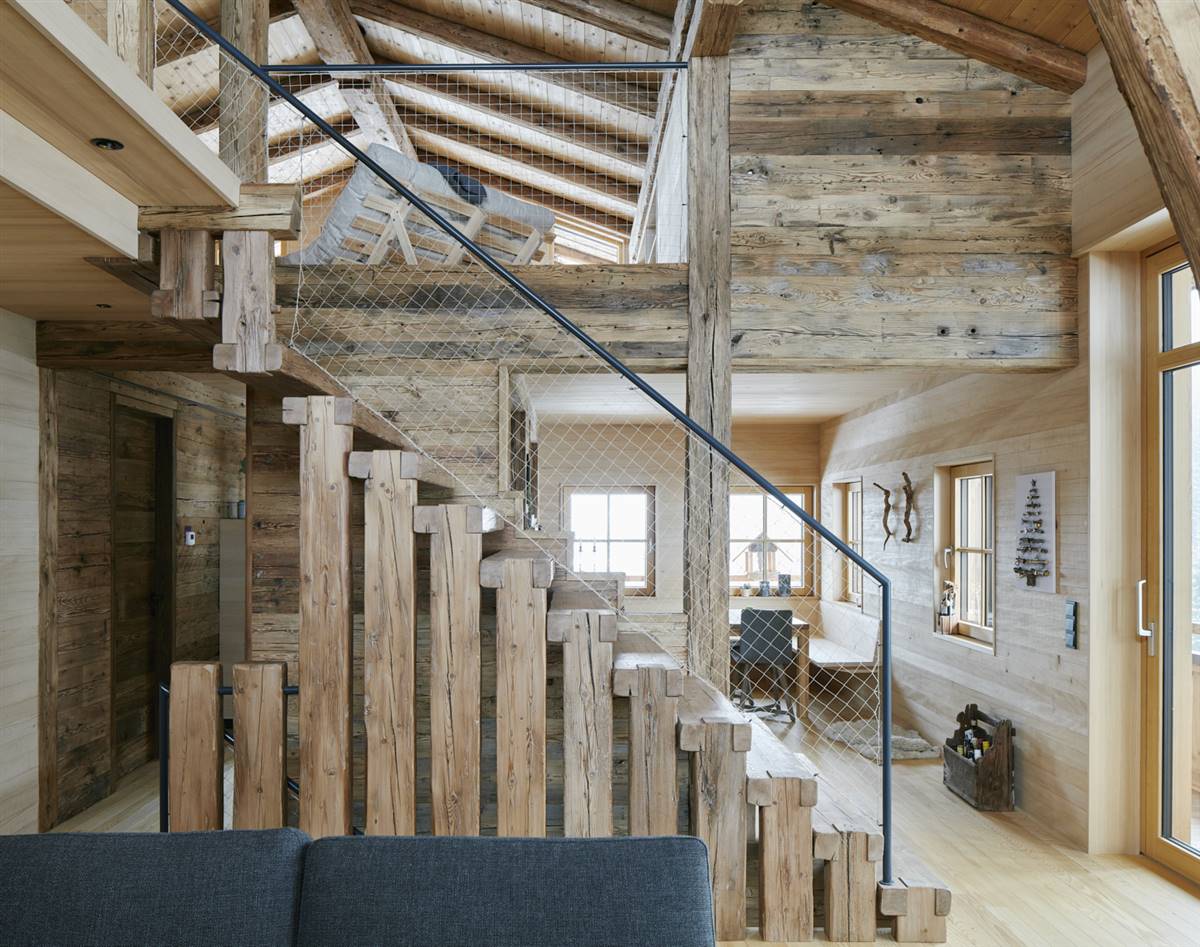
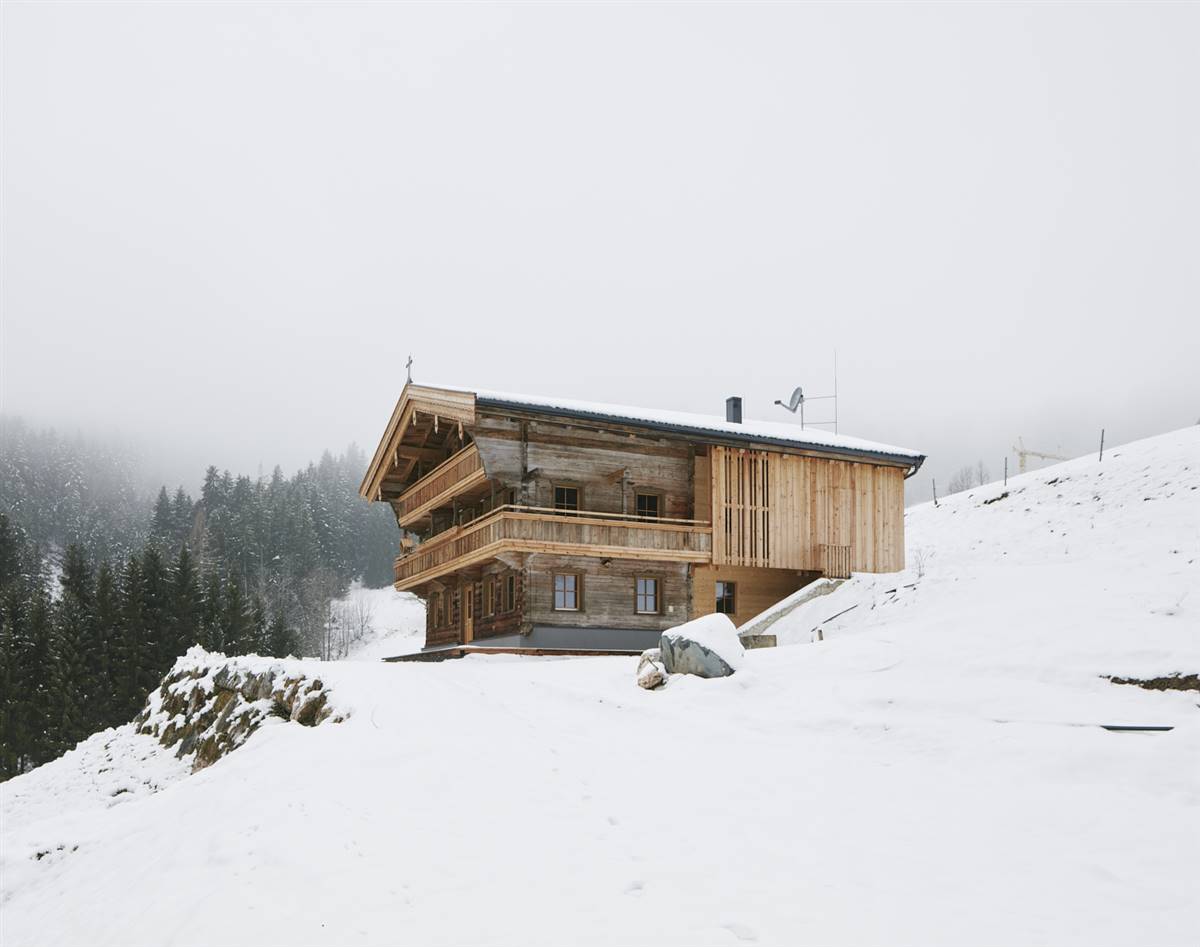
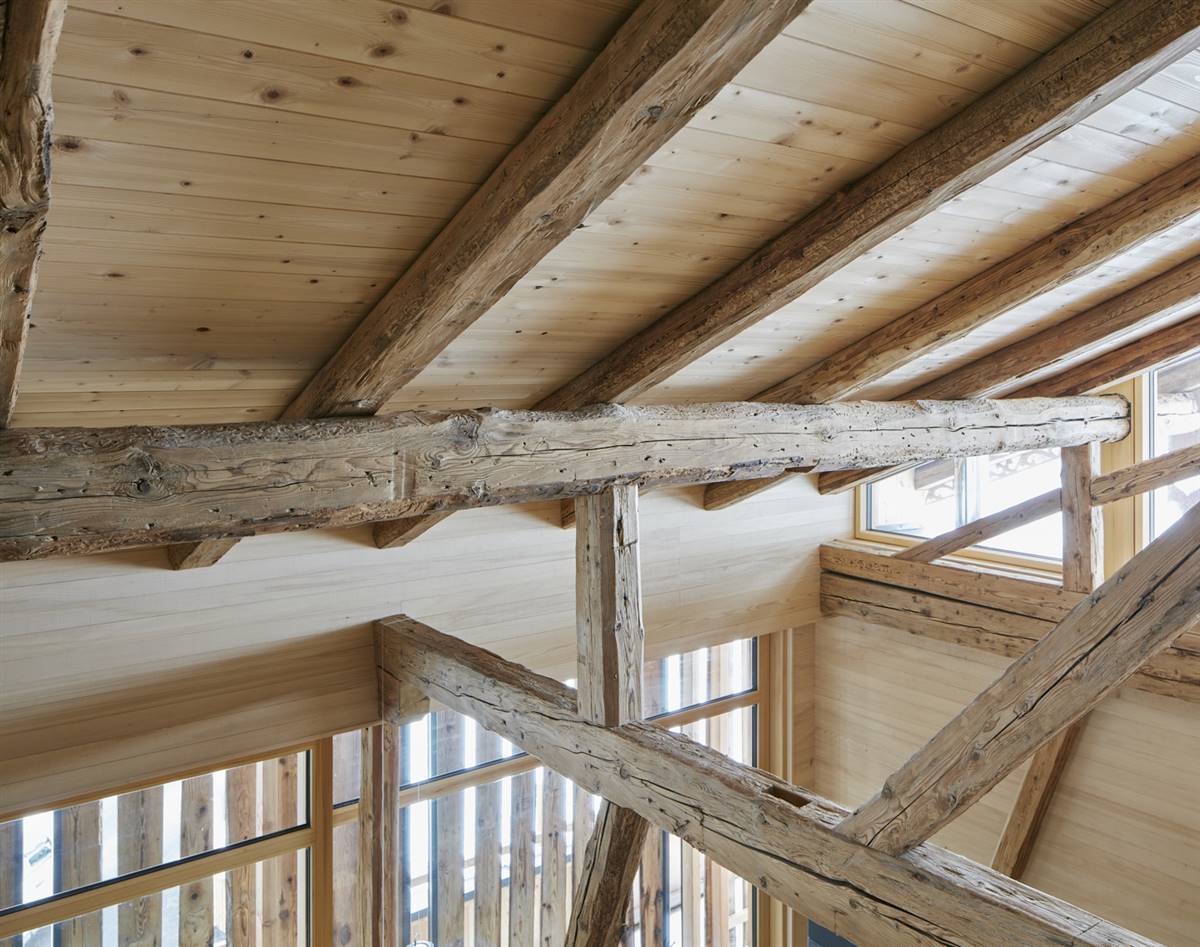
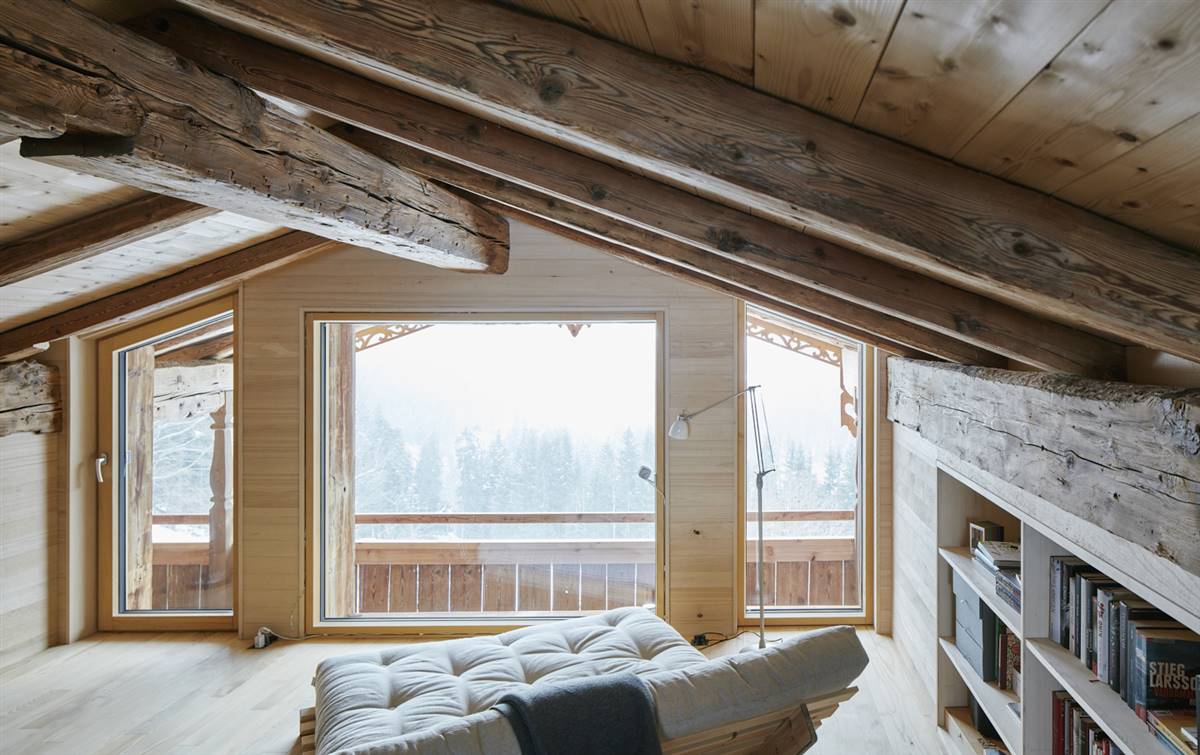
RENOVATION PROCESS
Architecture
BUILDING DESCRIPTION
State of repair
HERITAGE SIGNIFICANCE
Aim of retrofit
DI Hans Peter Gruber
Lindenstraße 2, 6020 Innsbruck
gruber@hpgruber.at
Tel.+43 512 343884
FS1 Fiedler Stöffler Ziviltechniker GmbH
Anichstraße 17, 6020 Innsbruck
office@fs1-gmbh.at
Tel.+43 512 260440
Hygrothermal assessment WUFI®
RETROFIT SOLUTIONS
External Walls
wooden log wall
Concrete base with internal insulation and thermal insulation system
In order to maintain the external appearance of the farmhouse, it was necessary to implement a consistent internal insulation. This was achieved with a 22 cm thick cellulose insulation on the log walls. The construction corresponded to a diffusion-limiting interior insulation system. The vapour barrier was realised by a butt glued OSB board (15 mm), which also creates the airtight level. A saw-rough silver fir formwork was applied to the OSB board. The combination of capillary-active properties of cellulose and the reduction of vapour diffusion through the OSB board contribute to the functionality of this solution. Another essential aspect is the existing wood block wall. Due to the relatively high thermal resistance of the wooden wall, the temperature between the existing wall and the insulation is much higher compared to a solid stock wall. Another important factor is the air circulation through the wooden beams. The air exchange has a positive effect on the drying behavior of the construction. Despite the lack of driving rain protection on the surface of the wooden wall, a certain constructive driving rain protection is given by the surrounding balcony and a relatively high base wall, which minimizes the moisture input from outside. Due to the thick insulation it had been necessary to test this solution by means of simulations. On-site measurements had confirmed the functionality of this solution. The system has to be tested depending on the situation and climate.
120 mm
120mm
1 mm
220 mm
15 mm
19 mm
The concrete base was necessary to eliminate the problem of rising moisture. Due to the additional distance of the wooden block wall to the adjacent terrain, the ingress of moisture through splash water is also minimized. A further positive effect is the increase of the constructive driving rain protection. In order to ensure a functioning structure in terms of building physics, the concrete base was insulated with 80 mm XPS insulation in the exterior area and later plastered. This makes it possible to create a driving rain resistant facade and to increase the temperature in the layer between the internal insulation and the reinforced concrete wall. Since reinforced concrete has a high thermal conductivity, the temperatures on the inner surface would cool down considerably without additional external insulation and lead to condensation. To play it safe, the load-bearing structure for the internal insulation in the base area was made of purenite, a moisture-resistant material based on PUR / PIR rigid foam.
18mm
15 mm
220 mm
4 mm
200 mm
2 mm
80 mm
Windows
OPTIWIN - Lignuma
The old box-type windows were removed in the process of reconstruction and replaced by new windows. On the upper floor, some larger window openings were built.
It was important to the architect that the new windows should have the same appearance as the old windows. A modern passive house window made of wood was chosen where the frame is as small as possible and corresponds approximately to the appearance of the original windows. In addition, wooden crosses were inserted into the window area in accordance with the regional townscape.
Existing window type | Box-type window |
Existing glazing type | Single |
Existing shading type | NA |
New window type | Casement window |
New glazing type | Triple |
New shading type | NA |
New window solar factor g [-] | 0,53 |
Other interventions
ROOF
GROUND FLOOR
MEASURES TO INCREASE AIRTIGHTNESS
The old rafters and purlins of the roof truss were checked statically, adjusted and refurbished. The wooden formwork was replaced by a new visible formwork and a classic above-rafter insulation (system Steinbacher - Steinothan) was applied.
The appearance of the roof has also changed due to the significantly higher roof construction. Nevertheless, the architect has tried to adopt the original structures. For example, the decoration of the wind chest was taken over and restored true to the original. The heart-shaped purlin plank was also reproduced and adopted.
30 mm
40 mm
120 mm
30 mm
30 mm
60 mm
5 mm
200 mm
3 mm
20 mm
Since the log construction at the "Neuhäusl" farm was only supported on punctiform stone foundations and the original floor construction only consisted of an elevated wooden floor, action was necessary. The elevation prevented rising damp for the most part, but would have made renovation while retaining this structure very difficult. Another important point was the low room height in the existing building. In order to achieve a room height of 2.50 m, the entire timber construction was elevated - in a rather adventurous action - by means of wooden beams, which were attached to the block walls. To keep the block walls together, they were lashed together with tension belts. After the elevation, the entire building was undermined and a reinforced concrete foundation slab including concrete plinths was built. This measure solved the problem of rising damp and created a contemporary room height. Thanks to the massive floor construction, it was subsequently possible to apply a sealing as well as internal insulation and implement a classic floor construction.
The structure reflects the state of the art and was necessary for a damage-free refurbishment. Even in very old comparable buildings, plinths made of natural stone were often used to control the rising damp.
100 mm
40 mm
260 mm
220 mm
0 mm
50 mm
0 mm
60 mm
15 mm
During the refurbishment, attention was paid to creating a building envelope that was as airtight as possible. This was achieved by using OSB boards for the walls. These were airtightly sealed at the joints. The windows were also integrated with appropriate care. In order to keep the sources of error as small as possible, an attempt was made to place all installations on the interior walls. Thus no additional installation level was necessary. The abut ceilings and walls were also integrated into the concept and a penetration of the airtight level was avoided. (see also the respective detailed descriptions) The rafters and purlins of the visible roof truss posed a challenge. The penetrations of the airtight level could not be avoided. For this reason, the cracks in the beams were drilled to the core with an 8 mm drill and pressed out with a permanently elastic special rubber (e.g. Dörken, Delta Than).
HVAC
HEATING
VENTILATION
DOMESTIC HOT WATER
Due to the extensive renovation of the building it was possible to install a completely new heating system. The heat supply for the heating and hot water is provided by a compact unit from Drexel + Weiss with a connected fresh water system tank. The heat distribution takes place classically over the heating screed. The underfloor heating is controlled by the decentralised pump system Wilo Geniax, which allows an exact dosing of the water quantity and a lower flow temperature.
The original tiled stove was no longer integrated into the renovation.
New primary heating system | New secondary heating system | |
---|---|---|
New system type | Heat pump | Stove |
Fuel | Electricity | Biomass |
Distribuition system | Radiating floor | stove |
Nominal power | 7,0 kW | around 6 KW kW |
Due to early consideration in the planning, a very efficient duct network using flexible pipes could be implemented. The ventilation unit itself is installed in the compact unit from Drexel und Weiss. The heat recovery amounts up to 90% according to PHI. The supply air is introduced in the sleeping rooms on the respective floor and extracted via overflow openings in the bathroom and kitchen.
Because of the central situation of the distribution a suspended ceiling is only necessary in the toilet.
Original roof build-up | New ventilation system |
---|---|
Type ventilation system | Room-by-room |
Type flow regime | Cascade |
Heat recovery | Oui |
Humitidy recovery | No |
Nominal power | kW |
Electric power | 0,33 kW |
Control system |
Energy Efficiency
Voluntary certificates: No
Primary Energy 17 (without DHW) kWh/m2.y
Consumption_estimation_After: 17 kWh/m2.y
Primary Energy
Consumption_estimation_Calculation_method: Steady state simulation (e.g. EPC, PHPP)
Consumption_estimation_Including_DHW: No
Consumption_estimation_After: 17 (without DHW) kWh/m2.y
Internal Climate
Building owners and guests evaluate the interior temperatures as very pleasant. Due to the well-insulated walls there are no cold surfaces that cause discomfort due to a radiation difference.
Building owner and guests evaluate the indoor air quality as very positive.
Due to the window openings on all sides, the rooms appear bright and attractive.
The acoustic comfort is described as good. The sound insulation between the floors is perceived as slightly in need of improvement.