Rhine Valley House Irgang
Montfortstraße 13
6830
Rankweil, Austriche
Architect
Owner
User
Contact Details
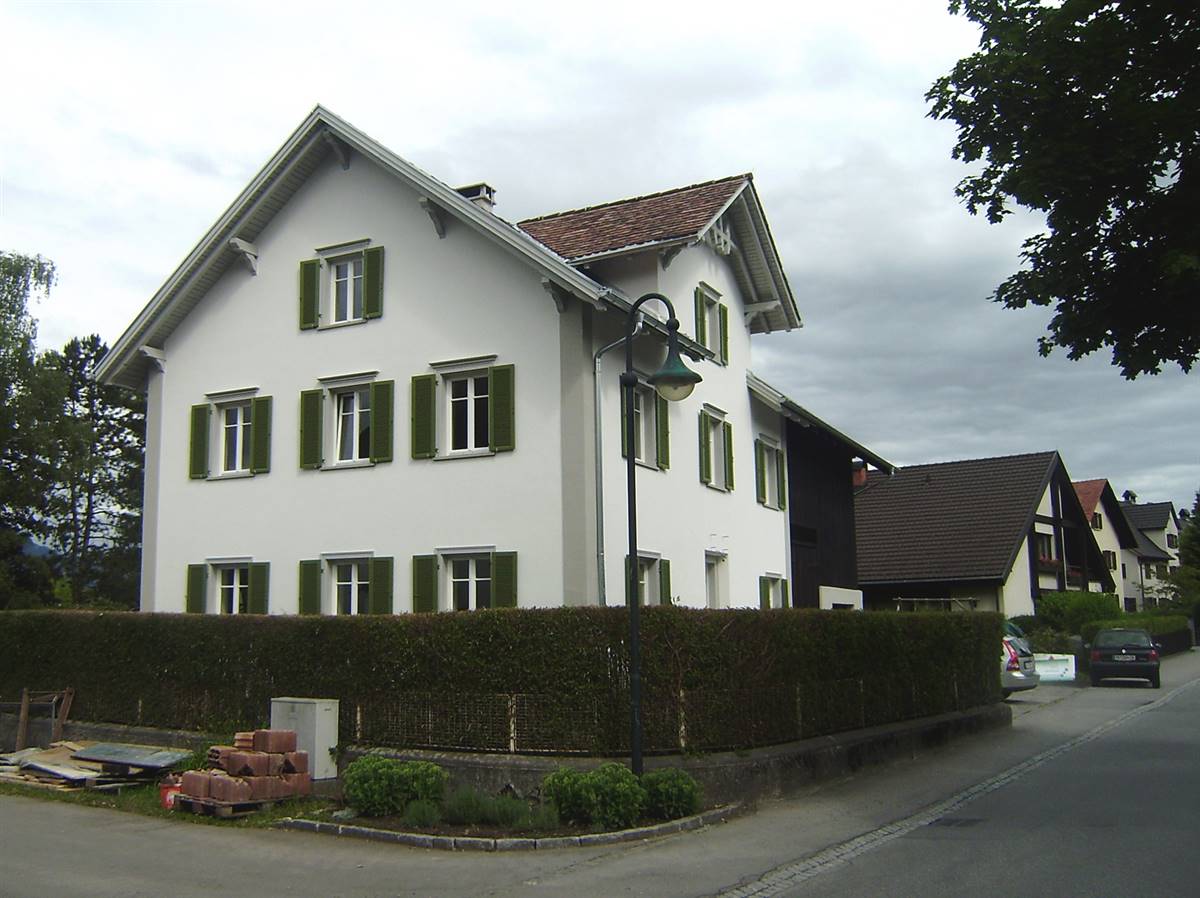
Climate Zone Cfb
Altitude 468
HDD 3385
CDD 63
Conservation Area:
No
Level of Protection:
Year of last renovation:
2008
Secondary use:
Residential (rural)
Building occupancy:
Permanently occupied
Number of occupants/users:
5
Building typology:
Detached house
Number of floors:
3
Basement yes/no:
Oui
Number of heated floors:
3
Gross floor area [m²]:
284,0
Thermal envelope area [m²]:
539,23
Volume [m³]:
756,0
NFA calculation method:
NGF (de)
External finish:
The main building is plastered with lime gypsum and lime cement
Internal finish:
The interior walls are partly plastered, partly clad with wood
Roof type:
Pitched roof
RENOVATION PROCESS
Architecture
BUILDING DESCRIPTION
State of repair
HERITAGE SIGNIFICANCE
Aim of retrofit
Dipl. Ing. Arch Beate Nadler-Kopf
Eisplatzstraße 1-1a, 6845 Hohenems
nadler-kopf@aon.at
Ökoberatung G. Bertsch
Dorfstraße 192, 6713 Ludesch
g.bertsch@oekoberatung.at
Kratzer Roland - Stuckateur- und Gipsermeister
Rautenastraße 14, A-6832 Röthis
office@kratzer-roland.com
Frick & Schöck Ziviltechniker GmbH
Treietstraße 20, A-6830 Rankweil
office@fszt.at
Tel.+43 5522 41130-0
Hygrothermal assessment NA
Life Cycle Analysis (LCA) NA
Other NA
RETROFIT SOLUTIONS
External Walls
Tuff masonry with lime-cement plaster ground floor
wooden block wall first upper floor
Insulated wooden frame wall in the attic
During the renovation it was found that the outer walls of the basement and ground floor were built as solid walls, the first and second floors as wooden block walls, and the attic floor as timber-framed masonry. The façade was not classified as worthy of preservation, but it was important to preserve the typical façade structure of the courtyard near the Rheintalhaus. Thus the difference between the farm building and the barn is still clearly visible today. For the energetic renovation of the façade, 16 cm EPS was applied on the ground floor and covered with lime plaster.
In the 140 years of existence, the building and thus also the façade has been adapted again and again. For this reason, the façade was not considered worth preserving and attention was paid to energy efficiency during the renovation.
400 mm
10 mm
20mm
400 mm
30 mm
160 mm
6 mm
The facade was not classified as worth preserving, which is why the renovation focused on energy efficiency. However, care was taken to maintain the typical structure of the Einhof, namely the clear distinction between farm buildings and barn.
The exterior facade was insulated in accordance with energy efficiency requirements in 2008.
125 mm
28 mm
160 mm
30 mm
125mm
30 mm
160 mm
30 mm
160 mm
6 mm
The entire attic was converted and insulated for later residential purposes, thus meeting the energy requirements of 2008. Care was taken to maintain the roof shape of the Einhof Rheintalhaus, namely the continuous single ridge.
The walls and roof slopes were adapted to today's energetic requirements, taking into account their originality.
160 mm
30 mm
125mm
30 mm
160 mm
40 mm
160 mm
6 mm
Windows
wooden windows
Even before the renovation, it was discovered that the windows were no longer in their original condition. Probably during the last renovation in 1970 the original windows were replaced by new, then more modern windows. For this reason, during the renovation in 2008, a partial restoration of the window view by means of a muntin division was taken into account when installing the windows.
The newly installed wood windows meet the standards for energy efficiency and ecology from the year of renovation 2008.
Existing window type | Single sash turn-tilt windows |
Existing glazing type | Double |
Existing shading type | Outer shutter |
Approximate installation year | 1970 |
New window type | Double window |
New glazing type | Double |
New shading type | Outer shutter |
New window solar factor g [-] | 0,54 |
Other interventions
ROOF
GROUND FLOOR
MEASURES TO INCREASE AIRTIGHTNESS
The attic was insulated and all installations were moved forward so that it can later be completed as an additional living floor if required.
Special attention was paid to the shape of the roof so that the typical shape of the courtyard is maintained. The continuous ridge was retained. The roof character of the Rheintalhaus was retained.
25 mm
23 mm
18 mm
24 mm
180 mm
80 mm
15 mm
A 15 cm insulation layer of glass wool was laid under the floorboards to the cold cellar.
The old floorboards in the living room were preserved. The appearance has therefore not changed.
25 mm
50 mm
50 mm
80 mm
150 mm
24 mm
HVAC
HEATING
DOMESTIC HOT WATER
The existing building was equipped with oil heating. The renovated building was now equipped with a tiled stove heating system. This is a tiled stove which has water pockets and heats the heating water. This water is then partly stored in the buffer tanks and distributed via pipes to the other rooms which are not heated directly by the tiled stove. In these rooms, the heat is usually emitted with radiators and also with a wall heating system.
The building already had a distribution and delivery system due to previous renovations. This was renewed in the course of the current renovation in 2008 and replaced by a more environmentally friendly heating system, a tiled stove whole house heating system.
New primary heating system | |
---|---|
New system type | Kachelofen als Ganzhausheizung |
Fuel | Biomass |
Distribuition system | Radiators and wall heating System |
Nominal power | 15 kW |
Before the rehabilitation, the hot water generation was connected to the oil heating system. Now the building has a solar system. The energy yield is stored in a 2,000 l boiler. The tiled stove all house Heating supports the solar thermal energy in winter, in summer there is probably an electric backup heating system.
The building has already had a distribution and delivery system due to previous renovations. This was renewed during the current renovation and replaced by a more environmentally friendly heating system. As a result, no further changes were made to the building. However, the very first heating system was not restored.
New DHW system | |
---|---|
Type | RES |
Hot_water_tank | Oui |
With heat recovery | No |
RENEWABLE ENERGY SYSTEMS
SolarThermal
Biomass
A solar system was installed on the roof to produce hot water.
The solar plant was installed on the roof part of the former farm building. Thus turned away from the street side, so that the solar plant is normally not visible.
The solar thermal system was integrated into the roof and not designed as an elevated system. It is thus embedded in the roof without standing out.
SolarThermal System | |
---|---|
Type | Flat collector |
Collector area | 20,0 m² |
Elevation angle | 38,0 |
Azimuth | 45,0 |
Overall yearly production | 5314,0 kWh |
Heating_contribuition | 0,0 kWh |
DHW contribuition | 3400,0 kWh |
Cooling contribuition | 0,0 kWh |
A tiled stove was installed as heating. With it the whole house is heated by the built-in water pockets and radiators. As heating material piece wood is used.
The old, unecological oil heating was removed and the storage tanks were installed instead.
The tiled stove is used as a whole-house heating system. The heat is emitted in small areas via radiators and wall heating.
Biomass System | |
---|---|
Type | Logs |
Storage size | 2000 Liter |
Origin of biomass | Regional |
Overall yearly production | 21267,0 kWh |
Energy Efficiency
Voluntary certificates: No
Consumption_estimation_After: 45 kWh/m2.y
Primary Energy
Consumption_estimation_Calculation_method: NA
Consumption_estimation_Including_DHW: No
Type_of_monitoring: Punctual
Description: The residents feel very comfortable in the building. The heat distribution as well as the room climate is very pleasant.
Internal Climate
The residents report a pleasant and balanced temperature in the rooms.
The desired air quality is achieved manually and individually for each room by shock ventilation.
The large windows provide the rooms with plenty of daylight.
NA
NA
Costs
Net building costs including fees EUR 1500 per m2
No
Environment