Kasperhof
Römerstraße 13
6082
Patsch, Austriche
Architect
User
Contact Details
Other Information
silbersalz.jpg)
Climate Zone Dfb
Altitude 1013
HDD 4657
CDD 13
Conservation Area:
Oui
Level of Protection:
Ortsbildschutz
Year of last renovation:
2019
Secondary use:
Offices
Building occupancy:
Permanently occupied
Building typology:
Tenement (apartments)
Number of floors:
5
Basement yes/no:
Oui
Number of heated floors:
4
Gross floor area [m²]:
1123,0
Thermal envelope area [m²]:
459,93
Volume [m³]:
1765,86
NFA calculation method:
ArchiPhysik - gross floor area
External finish:
Plaster facade, wooden facade on the upper floors
Internal finish:
Plastered (on hard)
Roof type:
Pitched roof
silbersalz.jpg)
silbersalz_1.jpg)
silbersalz-min_1.jpg)
silbersalz-min_1.jpg)
silbersalz-min_1.jpg)
silbersalz.jpg)
silbersalz-min_1.jpg)
silbersalz_1.jpg)
silbersalz-min_1.jpg)
silbersalz_1.jpg)
silbersalz_1.jpg)
silbersalz-min_1.jpg)
silbersalz_2.jpg)
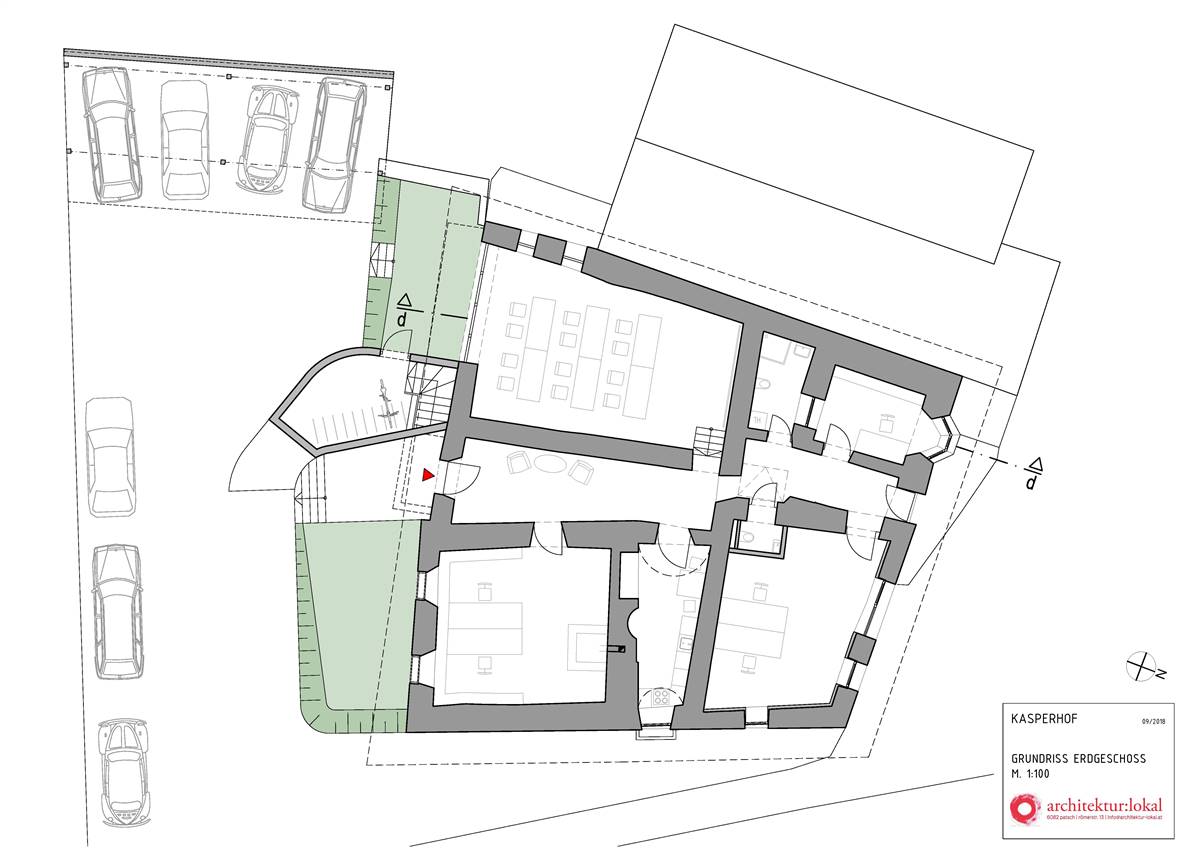
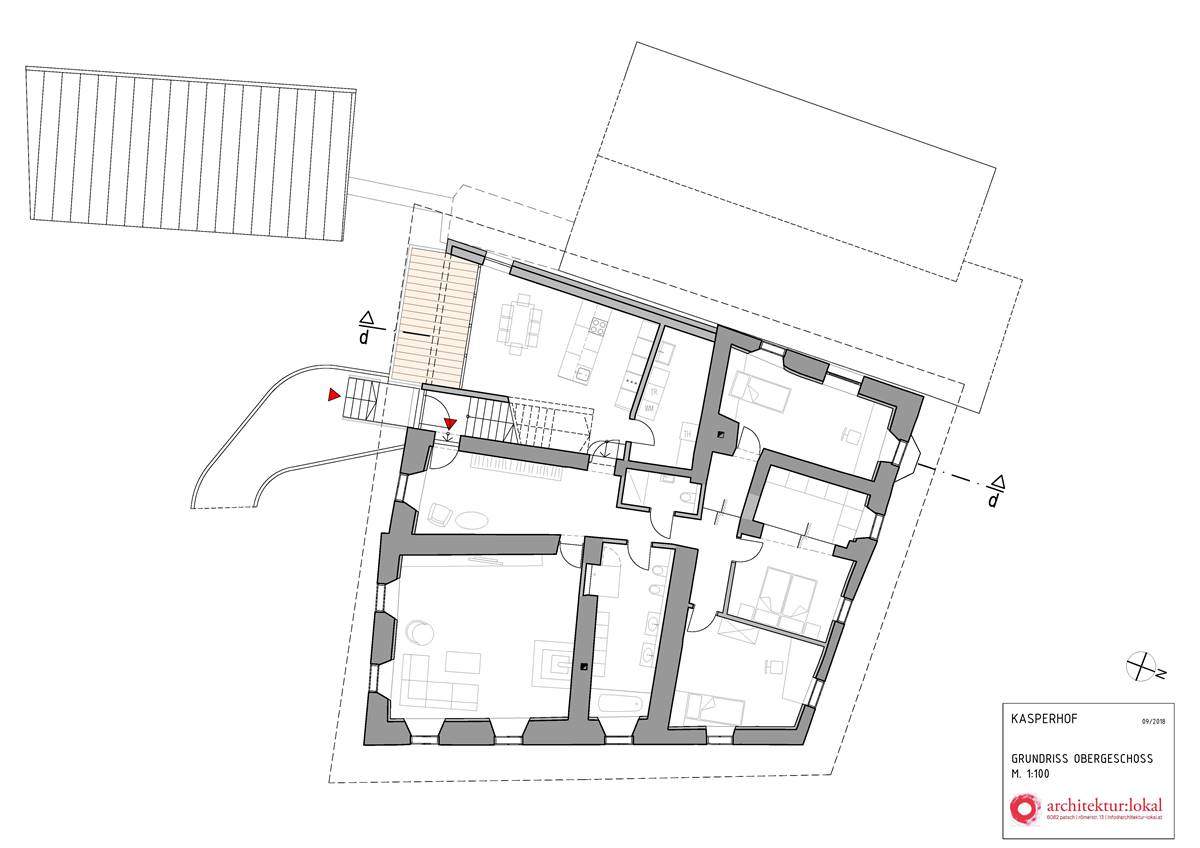
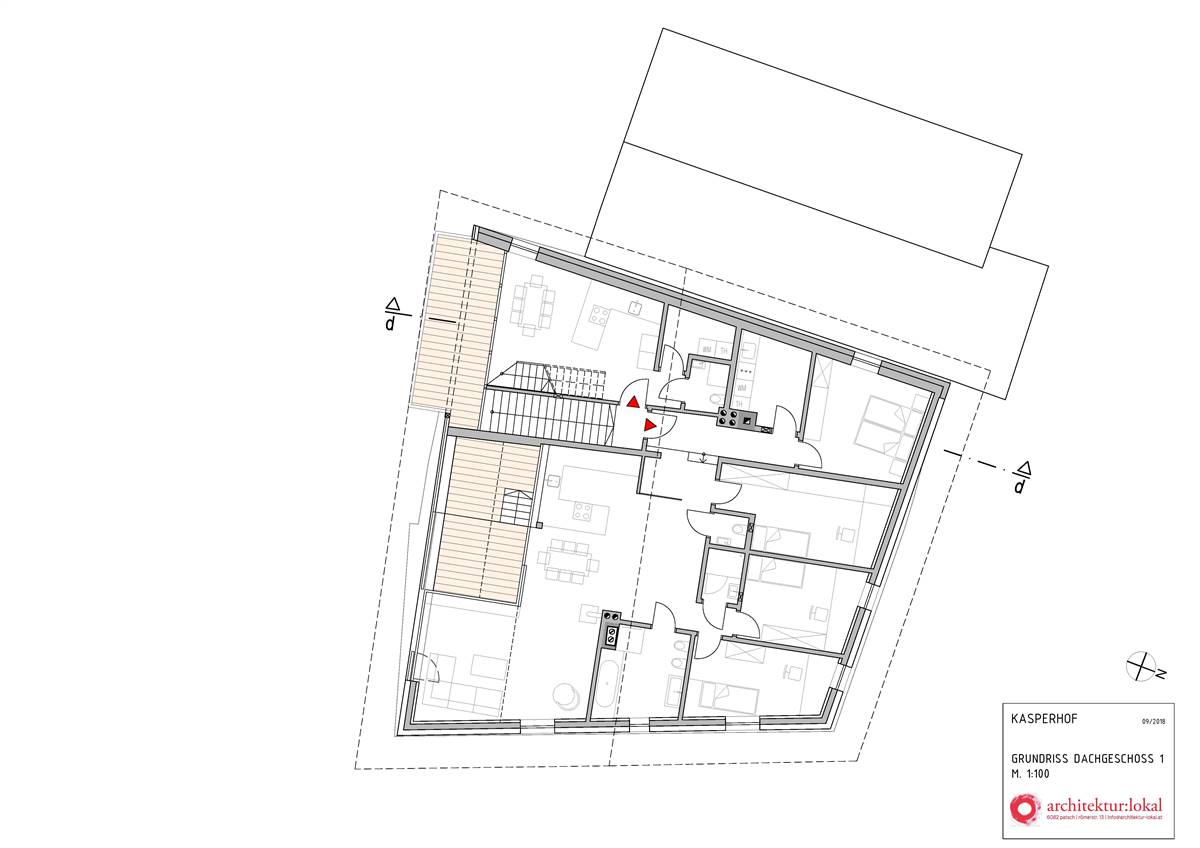
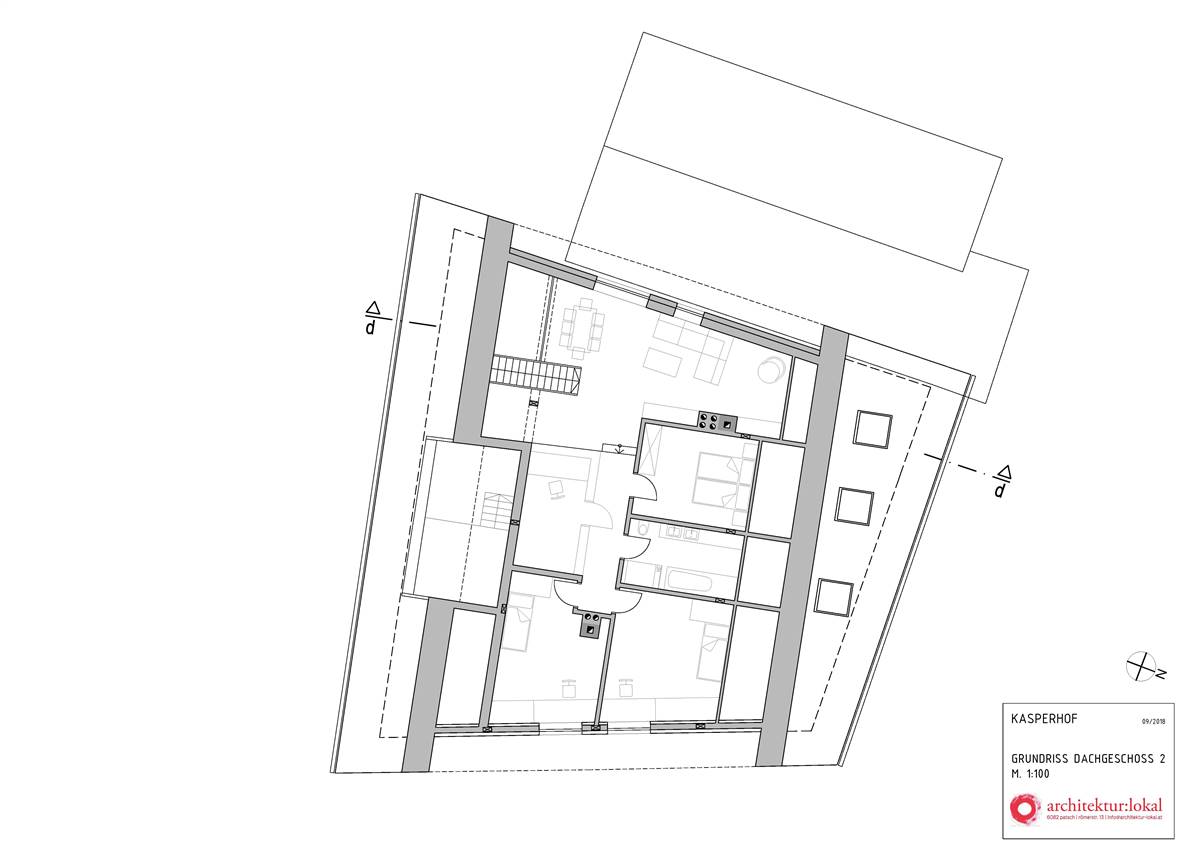
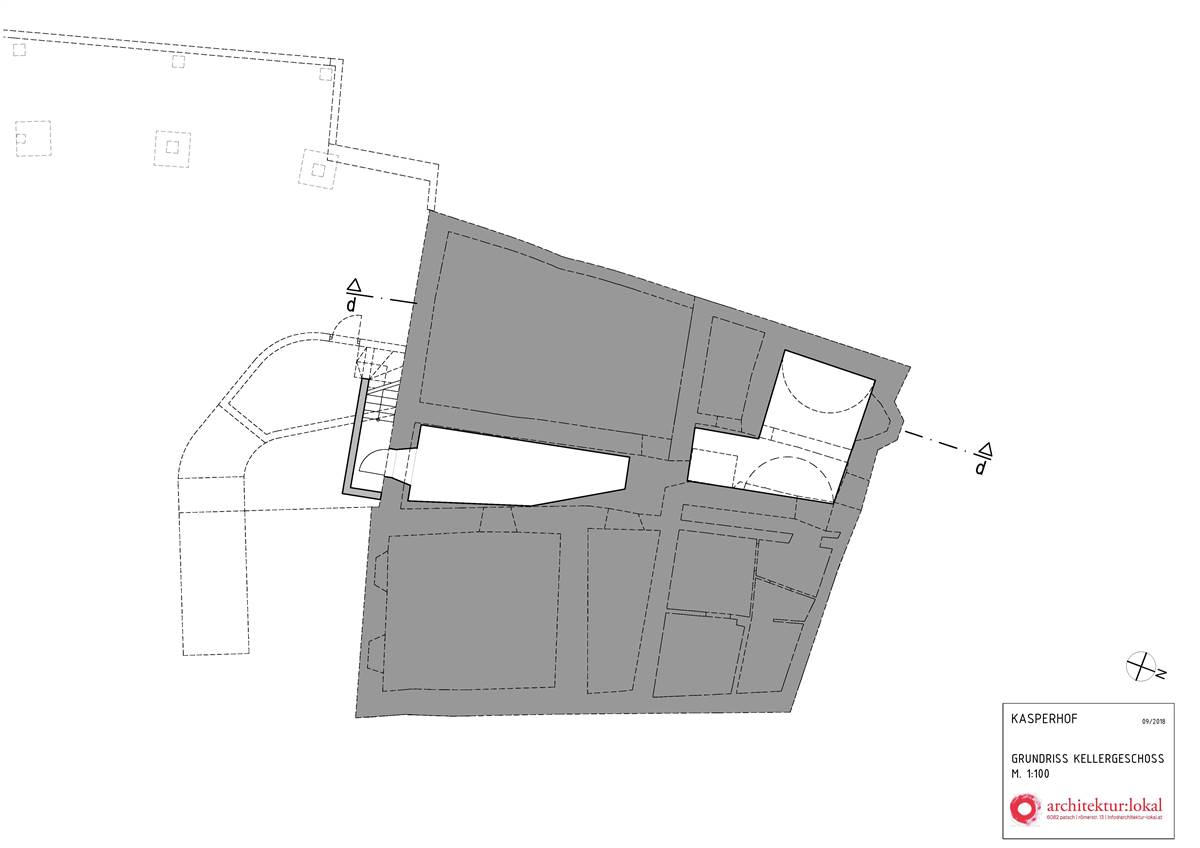
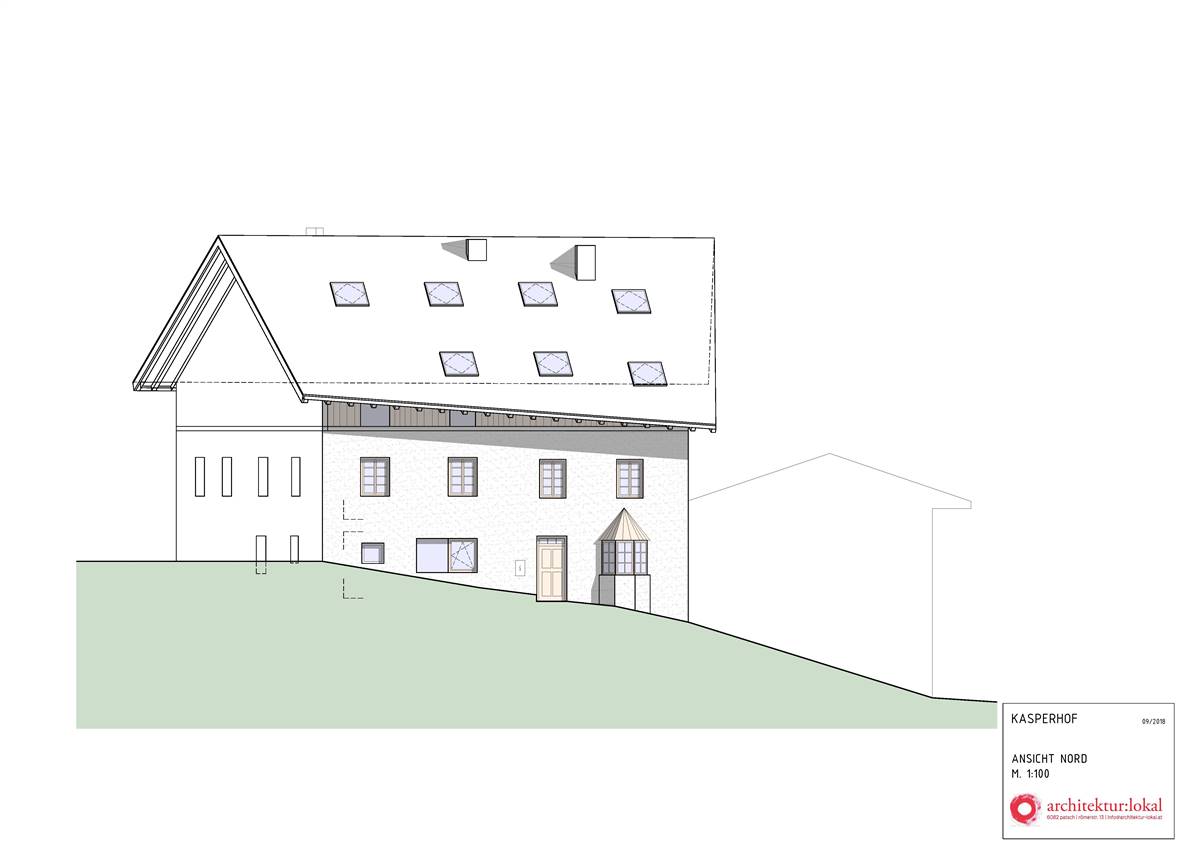
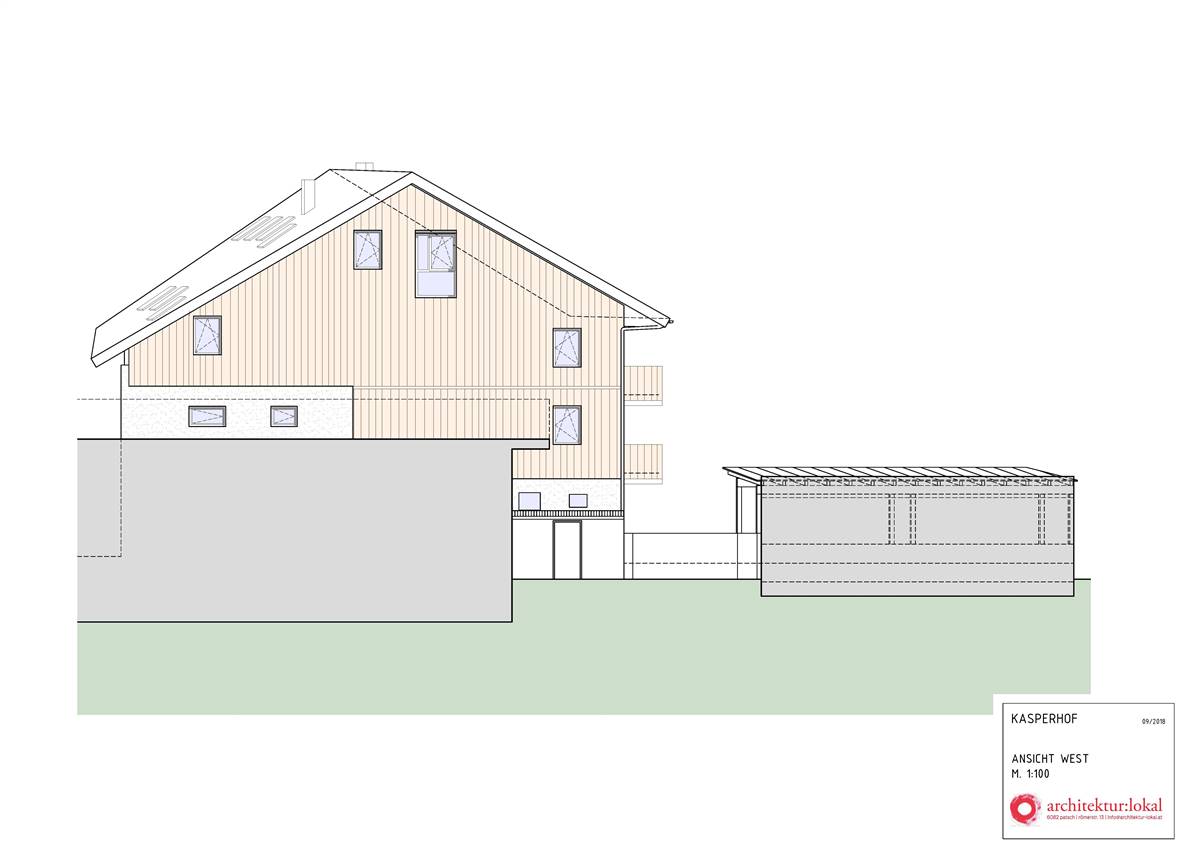
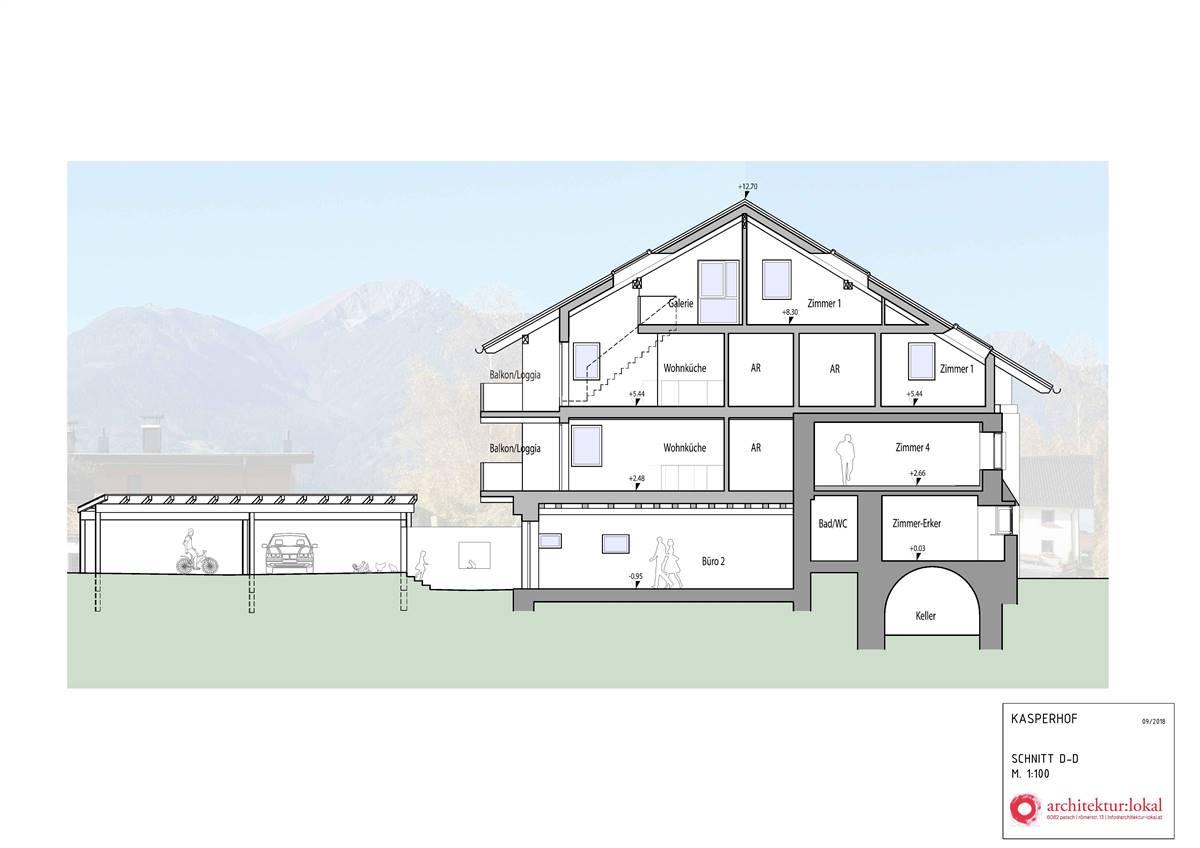
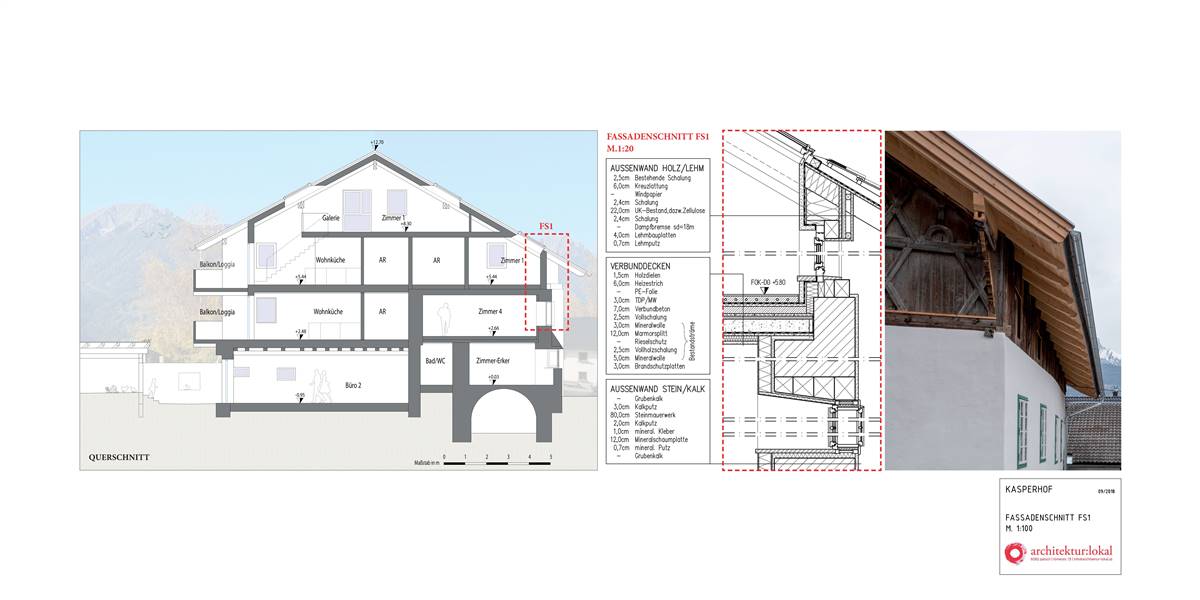
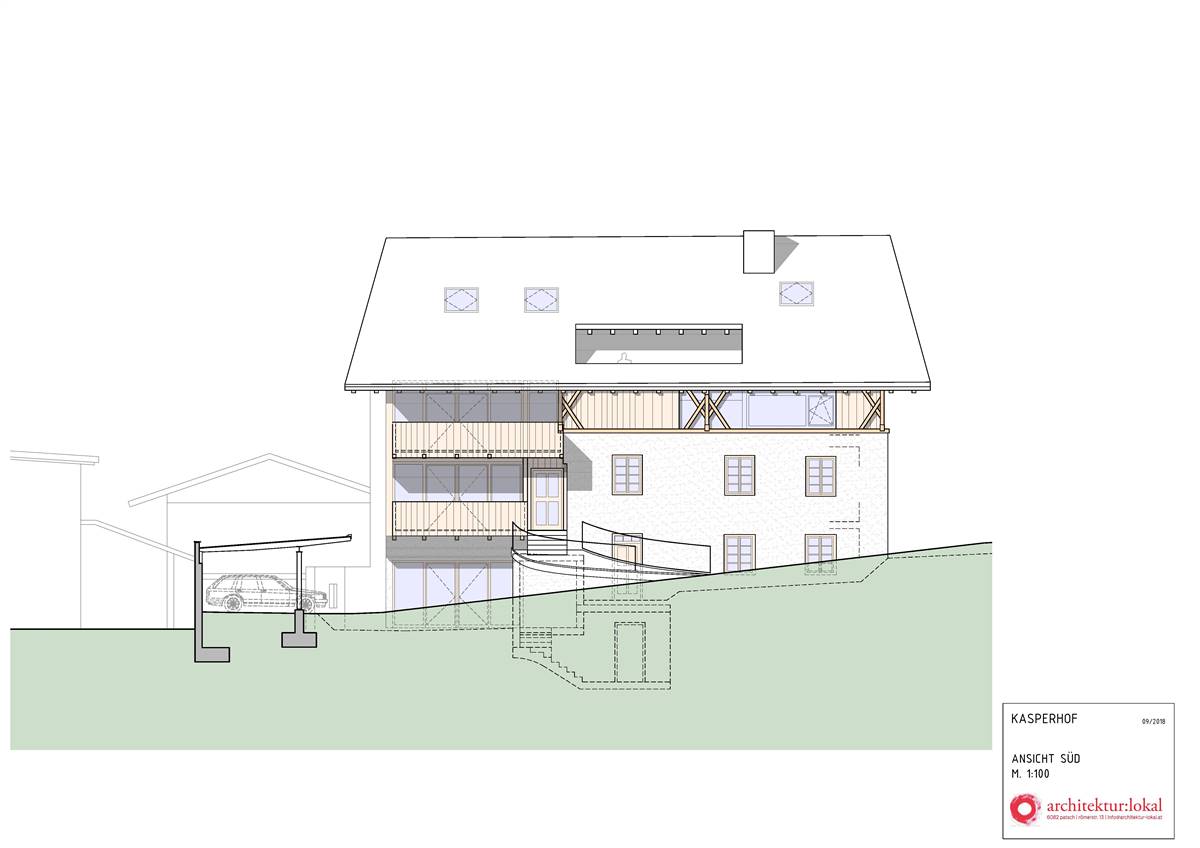
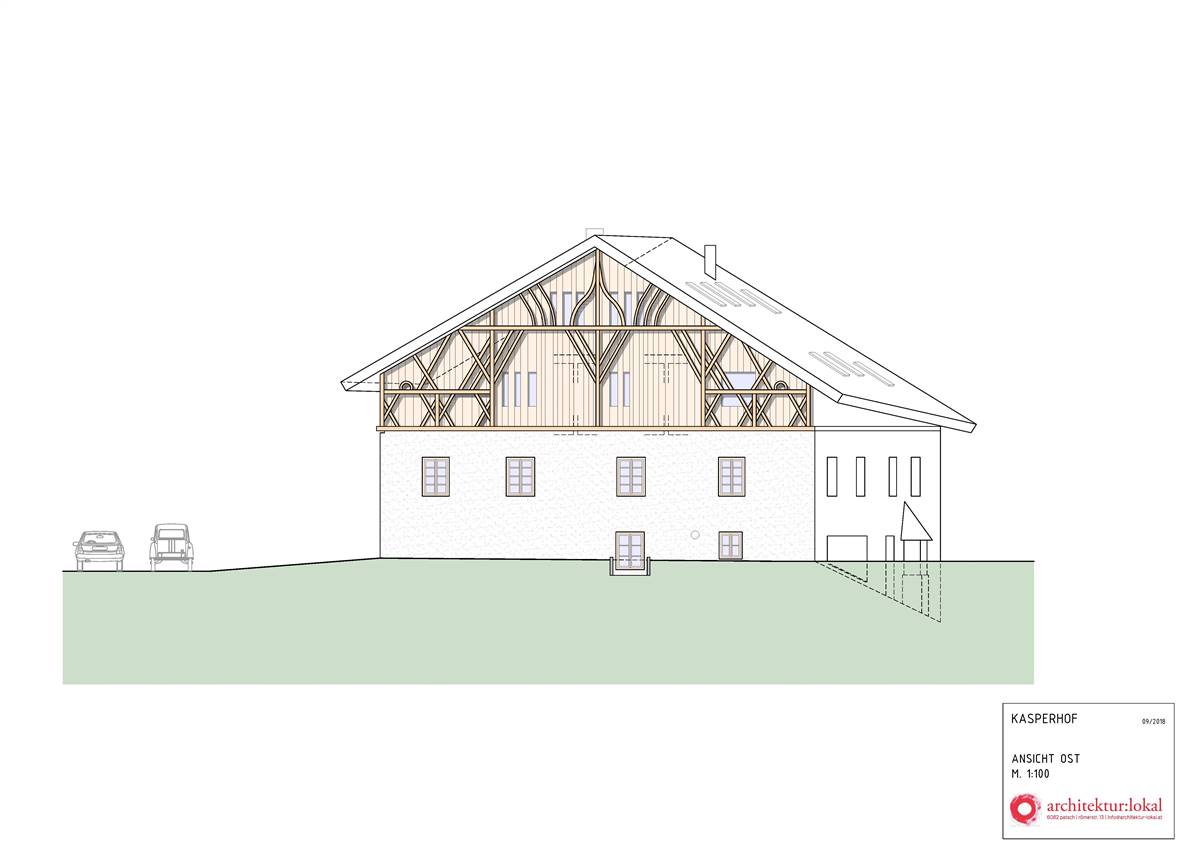
RENOVATION PROCESS
Architecture
BUILDING DESCRIPTION
State of repair
HERITAGE SIGNIFICANCE
Aim of retrofit
architektur:lokal - DI Dr. Gertrud Tauber, Arch.DI Andreas Semler
Römerstraße 13, A - 6082 Patsch
info@architektur-lokal.at
Tel.+43 (0)512 371400
Wibmer & Aigner ZT GmbH
Johann-Federer-Straße 2, A - 6300 Wörgl
office@wa–ingenieure.at
Tel.+43 (0)5332 73920
DI Andreas Danler
Moos 10, A - 6082 Patsch
di.danler@ikbnet.at
Tel.+43 (0) 664 137 87 57
RETROFIT SOLUTIONS
External Walls
stone masonry
During the renovation, an attempt was made to preserve the existing façade. A large part of the 90 cm (i.m.) thick stone masonry on the ground floor of the existing house was not insulated but lime plastered in the traditional way. Only the window reveals were insulated with calcium silicate panels. The 70 cm thick stone walls in lime mortar were insulated, depending on their orientation, with 10 to 12 cm mineral foam panels and a mineral interior plaster. Particular importance was attached to maintaining a diffusion open overall system.
50 mm
700 mm
30 mm
30 mm
50mm
700 mm
120 mm
30 mm
In the attics, the former function of the barn has been preserved due to the preservation of the roof truss, the decorative gable and the sunburned scarfboards remained legible. The new, insulated external wall was installed facing to the inside. A solid wood post and mullion construction has been assembled and blown out with cellulose. After the installation of an internal vapour barrier, 4 cm thick clay building board was applied and plastered with a 1 cm thick clay plaster.
20 mm
20mm
16 mm
200 mm
18 mm
0 mm
40 mm
10 mm
Windows
box-type window
The existing box-type windows were in desolate condition. In order to preserve the original appearance of the façade, the old box-type windows were replaced by new box-type windows. The windows were painted similar to the existing ones. All new windows were made of local larch. All units were equipped with generous 4-part lift and slide elements as access to a private outdoor area (balcony/terrace). All windows were equipped with heat insulation glass (Ug 0.6 W/m2K).
Thanks to the detailed reproduction of the box-type windows, there is hardly any change in the appearance of the façade. The new openings and windows represent an intervention in the historical appearance. By using wooden windows, the new windows were integrated into the wooden facade in the best possible way and guarantee generous lighting of the living space.
Existing window type | Box-type window |
Existing glazing type | Single |
Existing shading type | NA |
Approximate installation year | 1900 |
New window type | Box-type window |
New glazing type | Triple |
New shading type | NA |
New window solar factor g [-] | 0,63 |
Other interventions
ROOF
GROUND FLOOR
The roof truss was preserved and was upgraded according to static requirements. Above the visible existing rafters a rafter-mounted insulation with wood fibre insulation was implemented. The roof was covered with hand-beaten concrete roof tiles. Large roof windows were installed.
The existing cold roof truss had to be upgraded for the use of the attic as living space. The old rafters were retained as exposed rafters. However, the new construction changed the thickness of the roof, which is hardly visible from the outside. The integration of skylights and loggias resulted in a change in the appearance. However, care was taken to preserve certain details such as the decorative gable and to cover the roofing with materials appropriate to the time.
10 mm
20 mm
140 mm
30 mm
80 mm
0 mm
20 mm
240 mm
0 mm
25 mm
The largest part of the ground floor was built directly above ground level and has no basement.The new floor was installed floating and set off from the walls (gap). The gap to the floor structure serves to remove any rising damp as quickly as possible via the strip foundations and stone walls. On the outside of the outer wall, half-sided concrete blocks were placed against the existing wall to ensure ventilation and thus drying out of the wall. In combination with lime plaster and a sump lime paint, the moisture can be quickly removed. After excavation of the existing floor structure, 15 cm of foam glass gravel was laid. A foil and a granular subbase (5 cm) were applied over this insulating levelling layer. Subsequently, a bituminous waterproofing layer with an overlying fill layer (3.5 cm) and another classic floor construction with a footfall sound insulation layer (3 cm), PE-foil and heated screed were installed. The former plank floors were planed off at the bottom and glued to the new screed.
By reusing the original wooden planks from the upper floors, the appearance of the existing floors was changed but adapted to suit the building.
10 mm
100 mm
40 mm
150 mm
50 mm
35 mm
30 mm
1 mm
60 mm
30 mm
HVAC
HEATING
DOMESTIC HOT WATER
Only gas floor heating was used for the building's heating system. The distribution in the ground floor and in the two attics is done by floor heating, in the first floor by radiators. Solar panels were not permitted by the town and village council. A heating system such as pellets or wood chips was not possible due to the lack of space (no correspondingly large cellar with storage facilities available). A district heating connection does not exist in the community of Patsch.
New primary heating system | |
---|---|
New system type | Boiler |
Fuel | Gas |
Distribuition system | Radiating floor |
Nominal power | 36,91 kW |
The domestic hot water is heated with the gas heating system and stored in a boiler.
New DHW system | |
---|---|
Type | with heating system |
Hot_water_tank | Oui |
With heat recovery | No |
Energy Efficiency
Voluntary certificates: No
Primary Energy 107,61 kWh/m2.y
Consumption_estimation_After: 33,07 kWh/m2.y
Primary Energy
Consumption_estimation_Calculation_method: NA
Consumption_estimation_Including_DHW: No
Consumption_estimation_After: 107,61 kWh/m2.y
Costs
The refurbishment was also successful from a financial point of view. By developing the project in advance and presenting it directly to the interested parties, with whom the project was finally implemented, the ancillary purchase costs could be reduced. Thus the costs for an apartment with 180 m² were about 450,000 € gross. This results in a gross price of 2500 € per m² living space, which is even less than the value for a normal new building.
2500 € (per m2)
No