Rainhof
Magdalenastraße 29
39100
Gsies, Italien
Architekt
Besitzer
Bewohner
Ansprechpartner
Other Information
Please contact either the builiding owner or the architect
Turris Babel no. 106 - 07/2017, page 108: "Rainhof, Gsies"; http://atlas.arch.bz.it/de/rainhofbz/ The retrofitted building was eventually designated “heritage building of the month” by the heritage office: http://www.provinz.bz.it/kunst-kultur/denkmalpfle

Höhe über dem Meer 1500 m ü.d.M.
Heizgradtage 2905
Kühlgradtage 16
Ensembleschutz:
Nein
Stufe der Unterschutzstellung:
Protection status: Unterschutzstellung/Provvedimento di vincolo: BLR-LAB 607 from 16/02/1987
Letzte Sanierung:
2016
Vorhergehende Sanierungen:
0
zusätzliche Nutzung:
Ferienwohnungen
Gebäudebelegung:
Discontinuous occupancy (i.e. holiday home)
Anzahl der Bewohner/Nutzer:
10
Gebäudetyp:
Detached house
Anzahl der Stockwerke:
3
Keller ja/nein:
Nein
Anzahl der beheizten Stockwerke:
3
Bruttogeschossfläche [m²]:
454,0
Thermische Gebäudehülle [m²]:
667,32
Volumen [m³]:
1350,0
NGF Berechnungsmethode:
Useful area (it)
Außen:
Rendered
Innen:
Plastered (on hard)
Dach:
Pitched roof

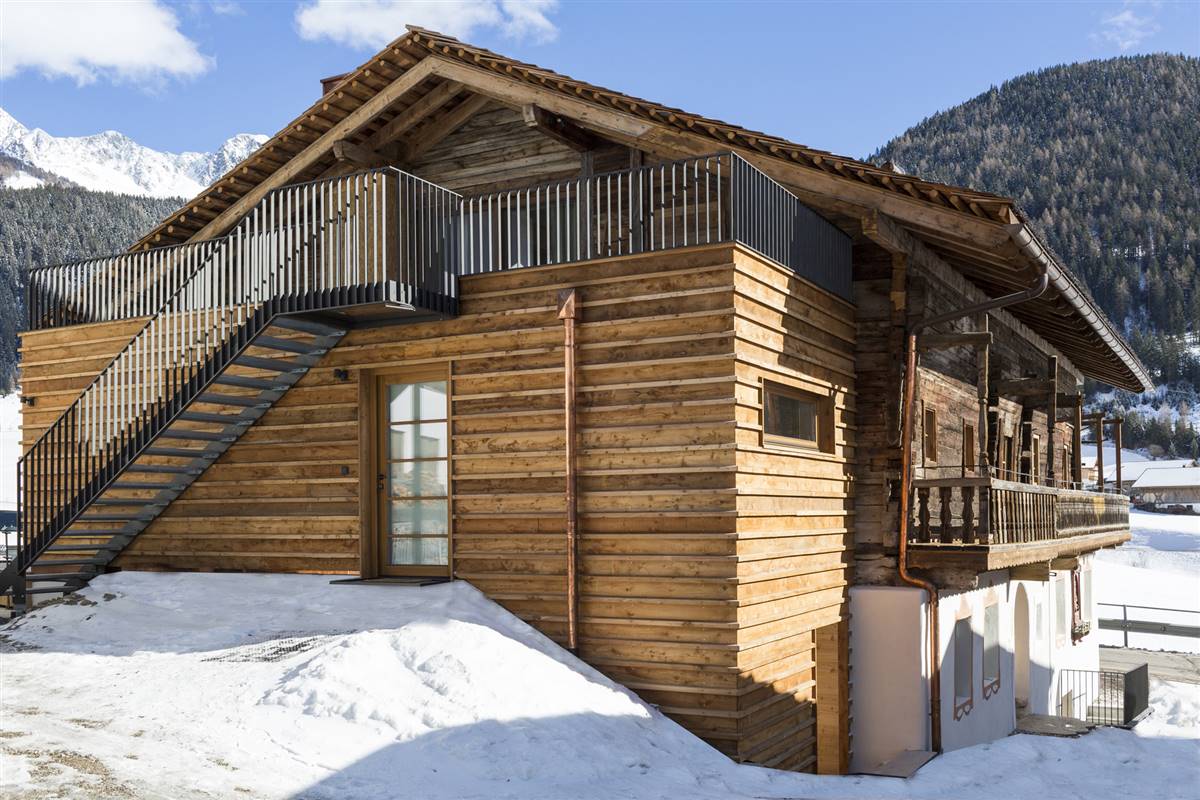
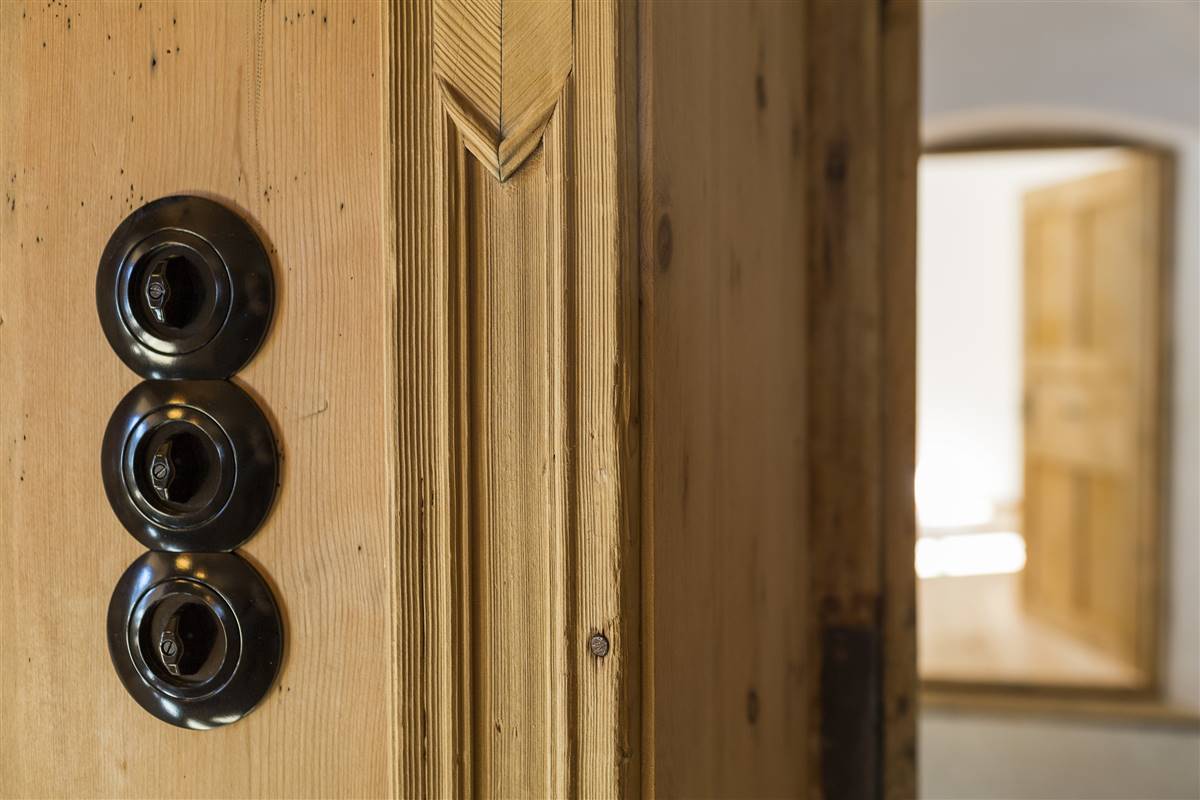
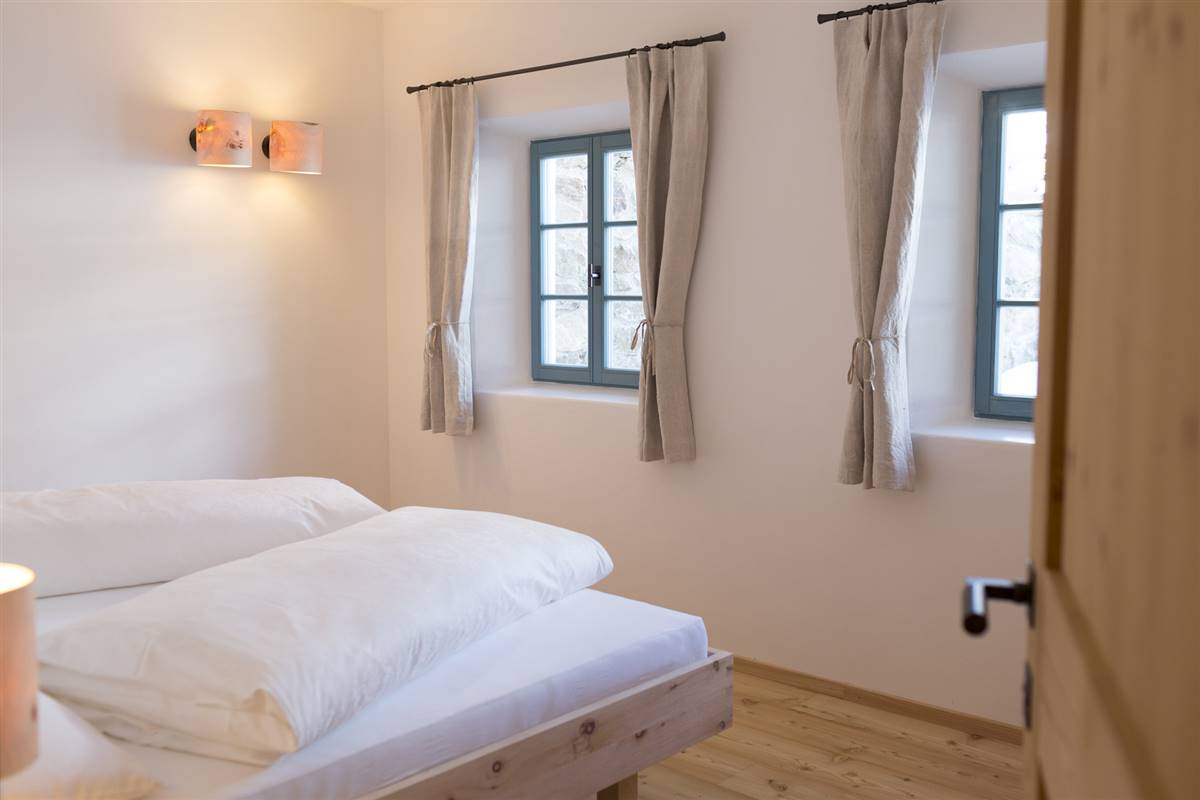
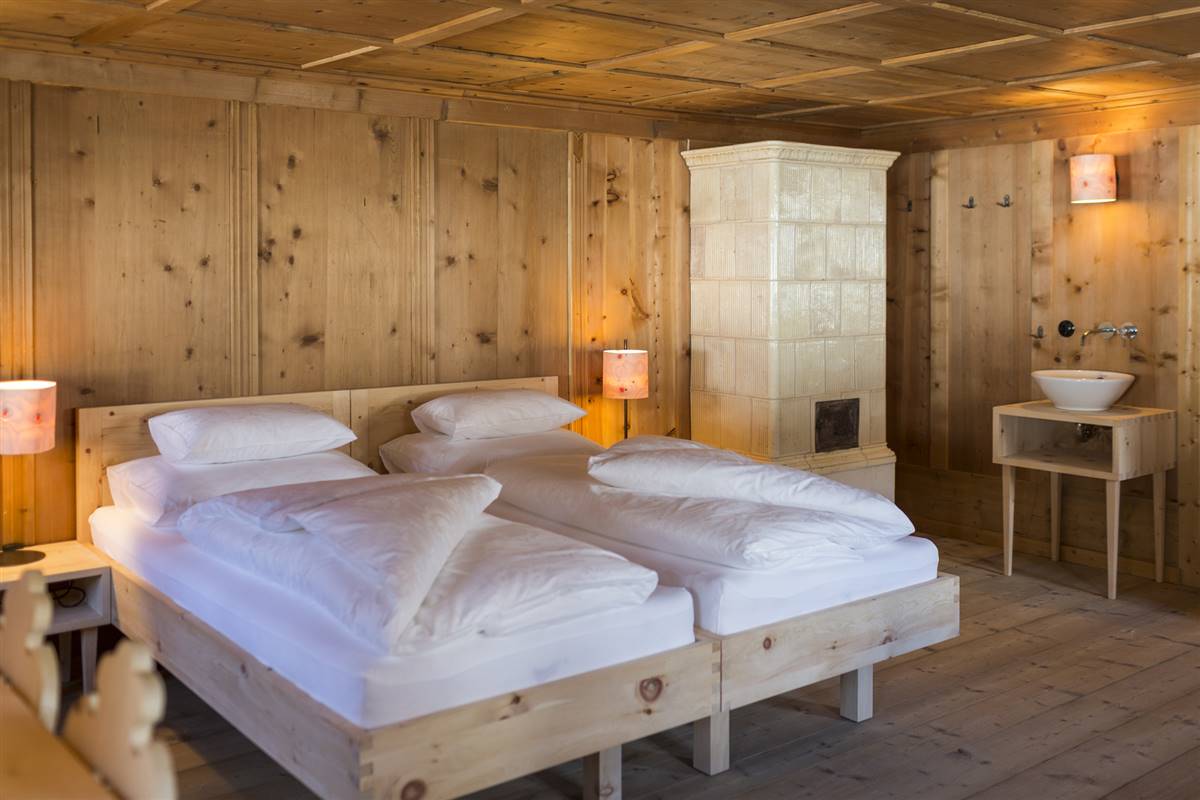
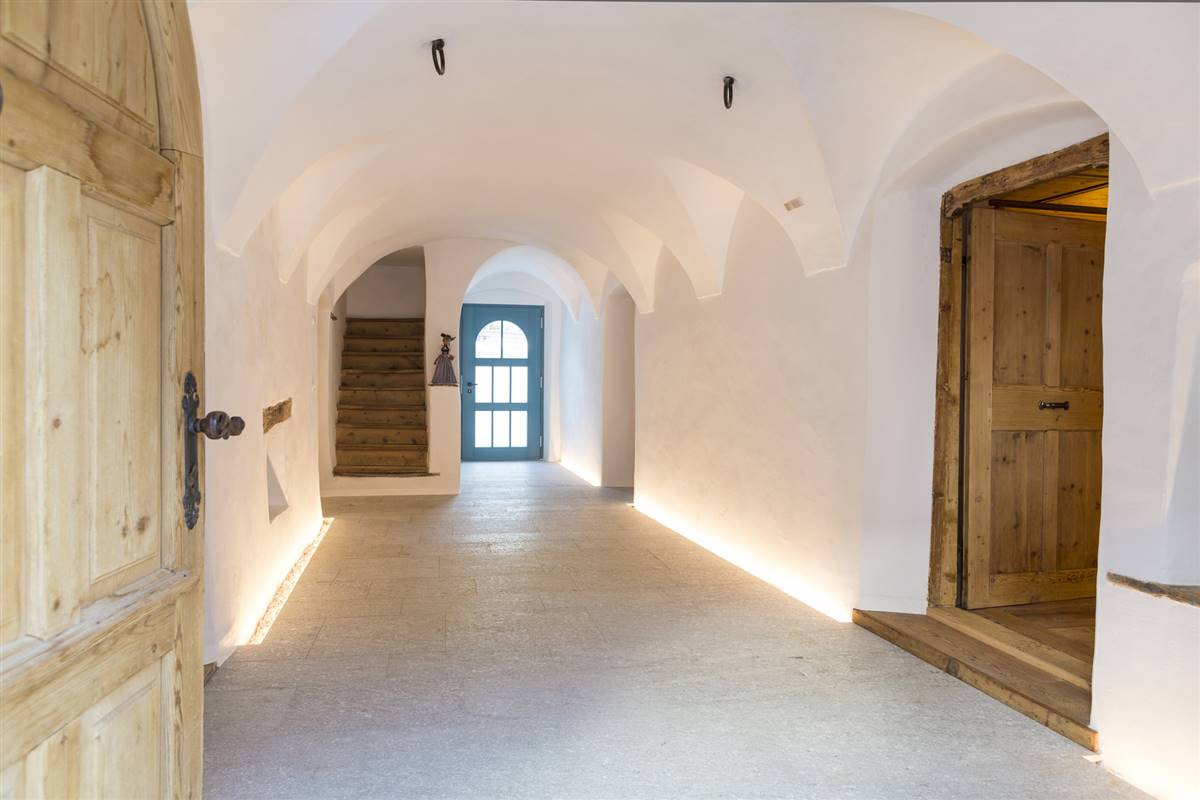
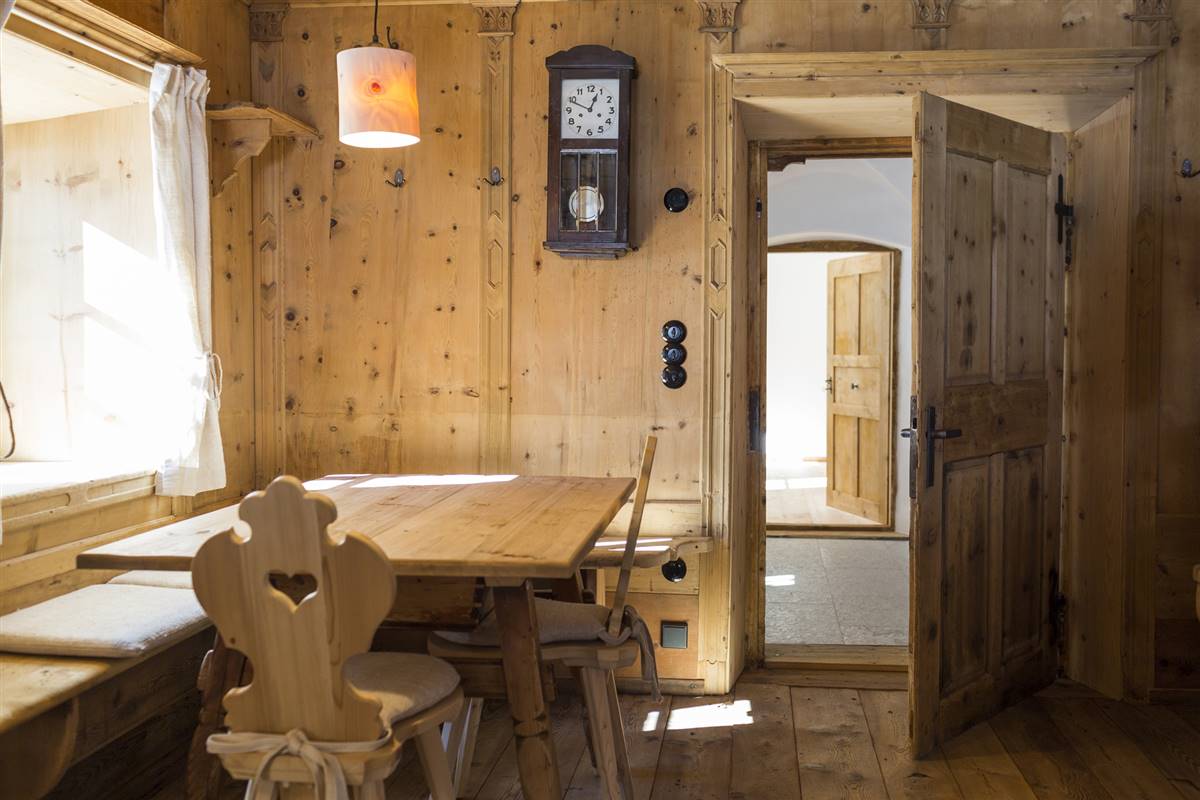
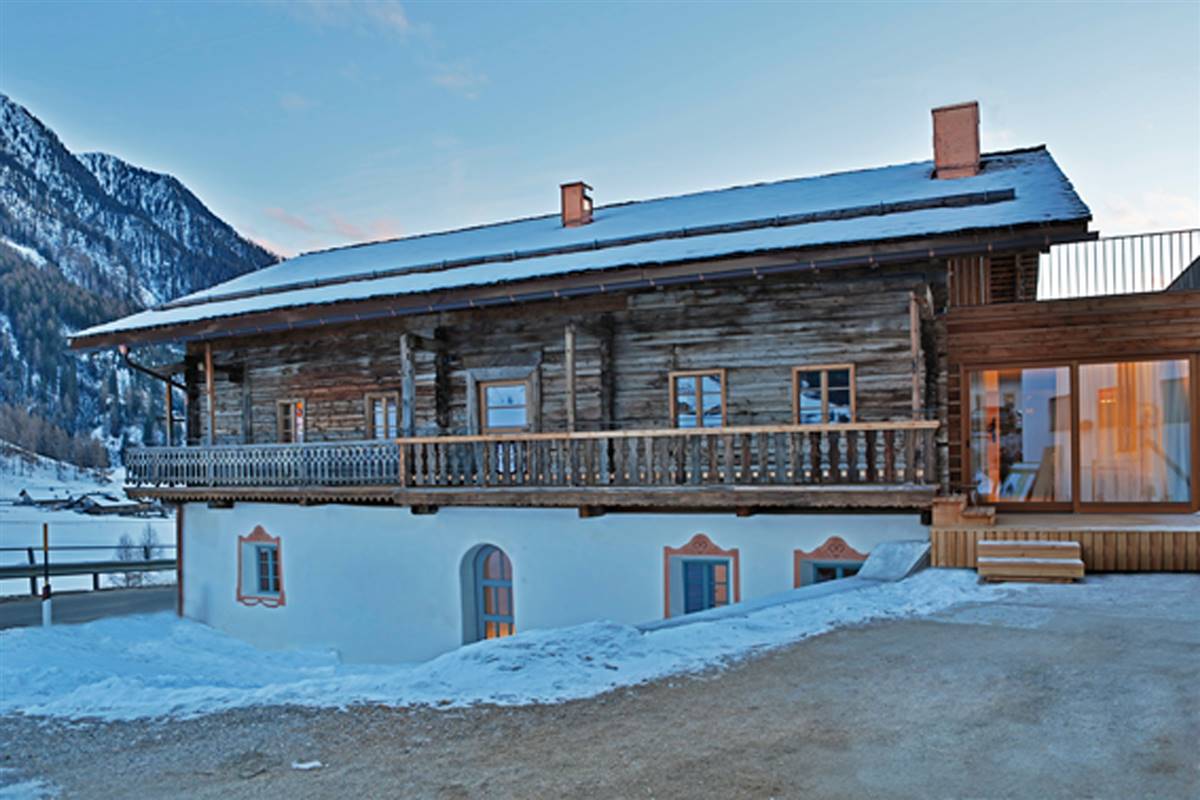
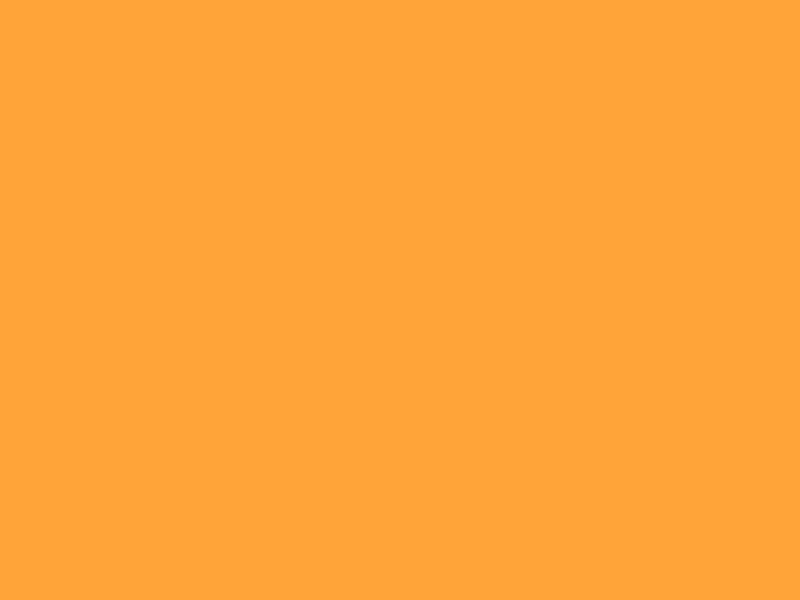
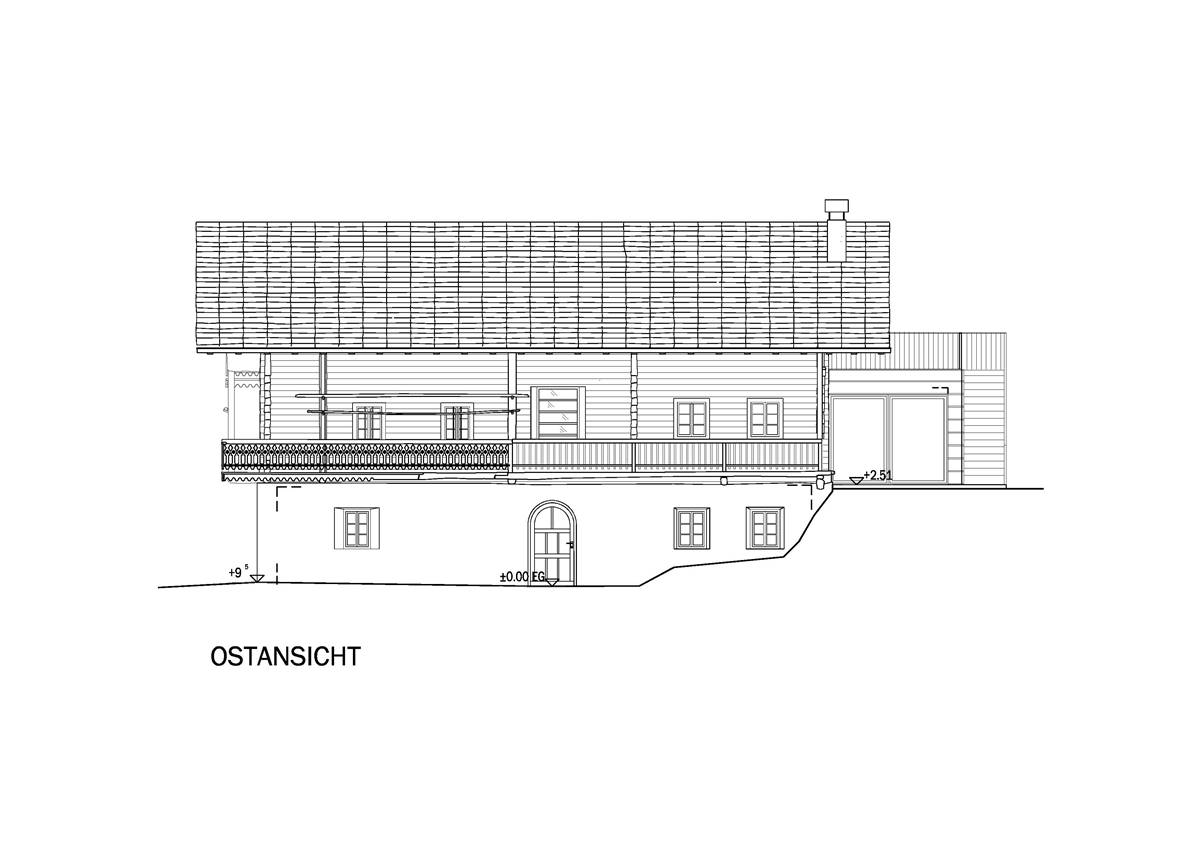
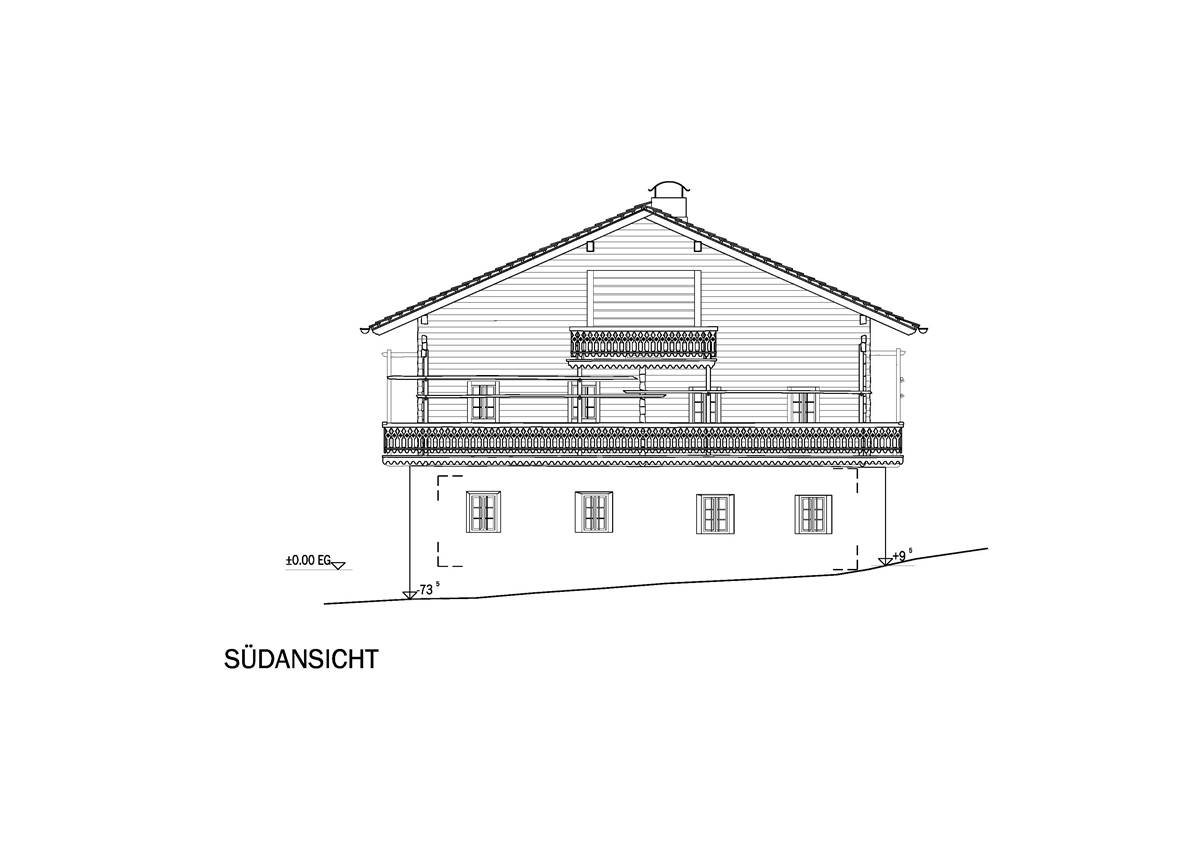
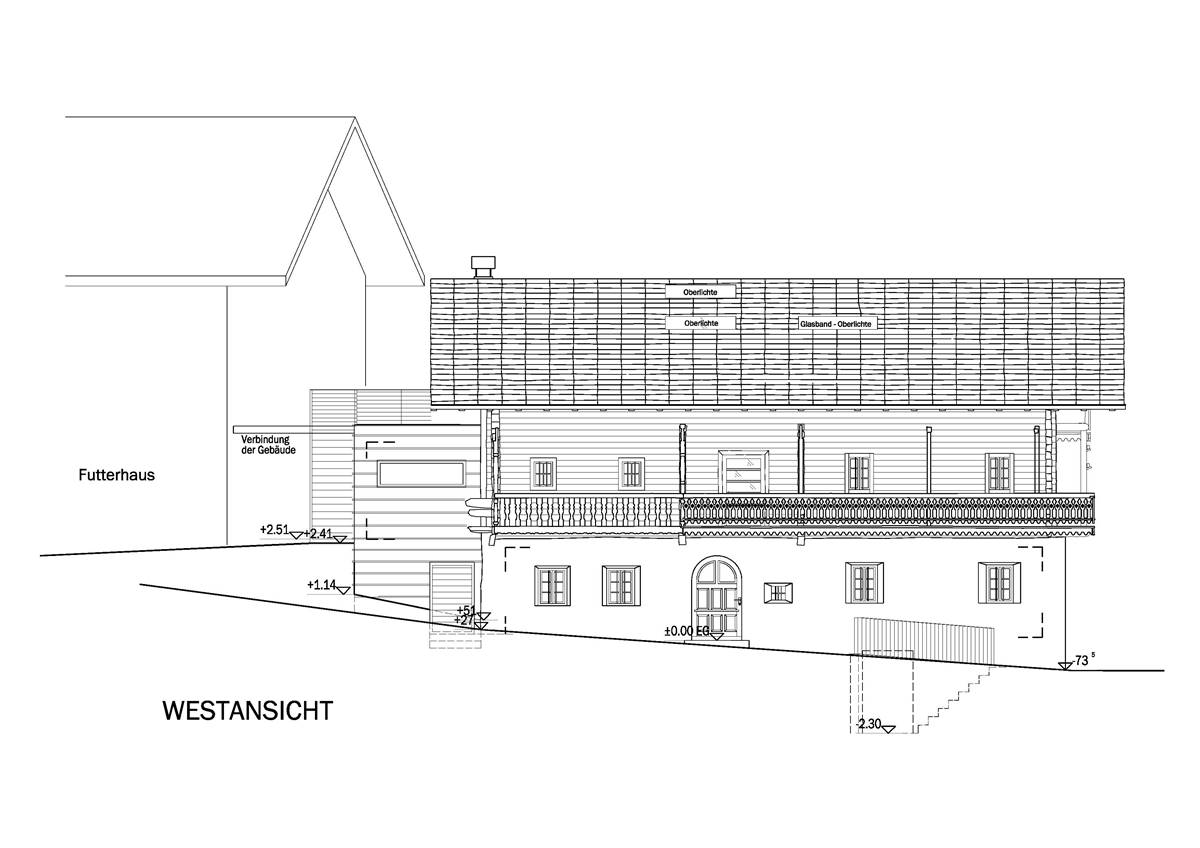
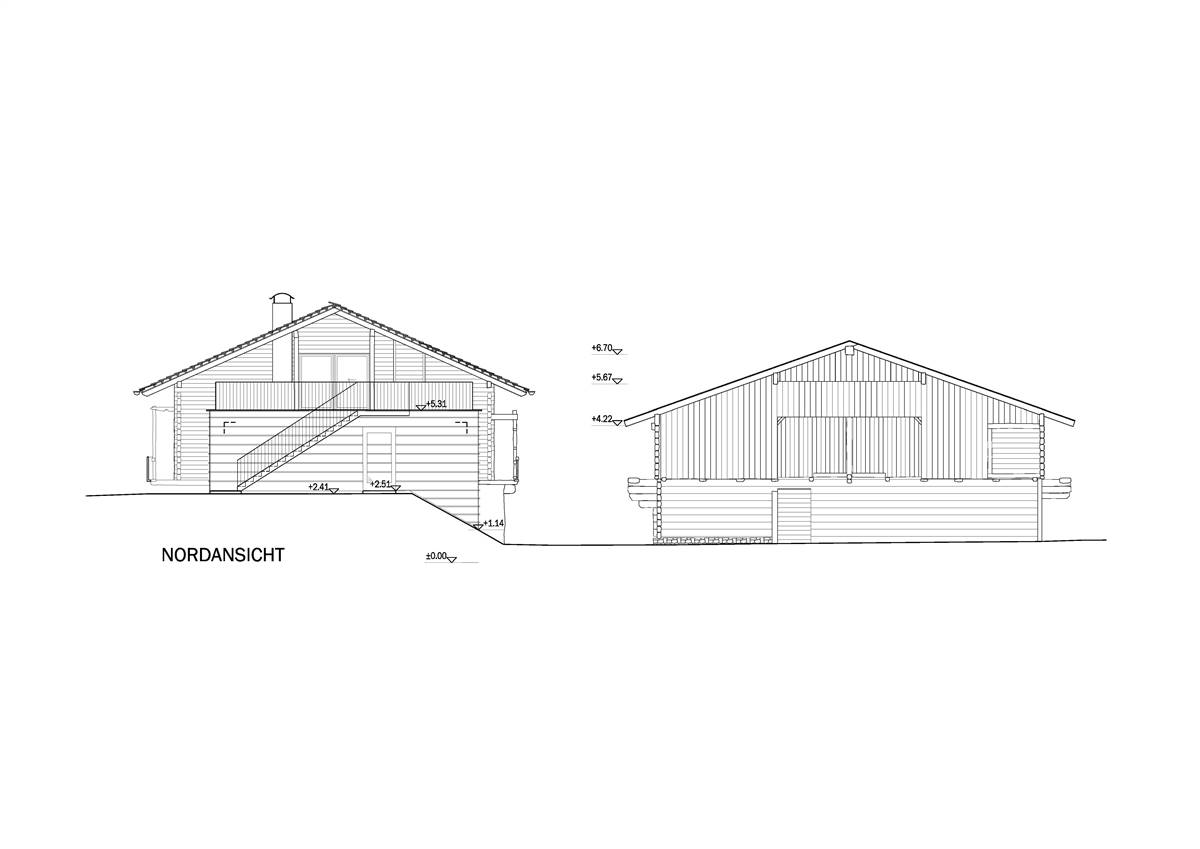
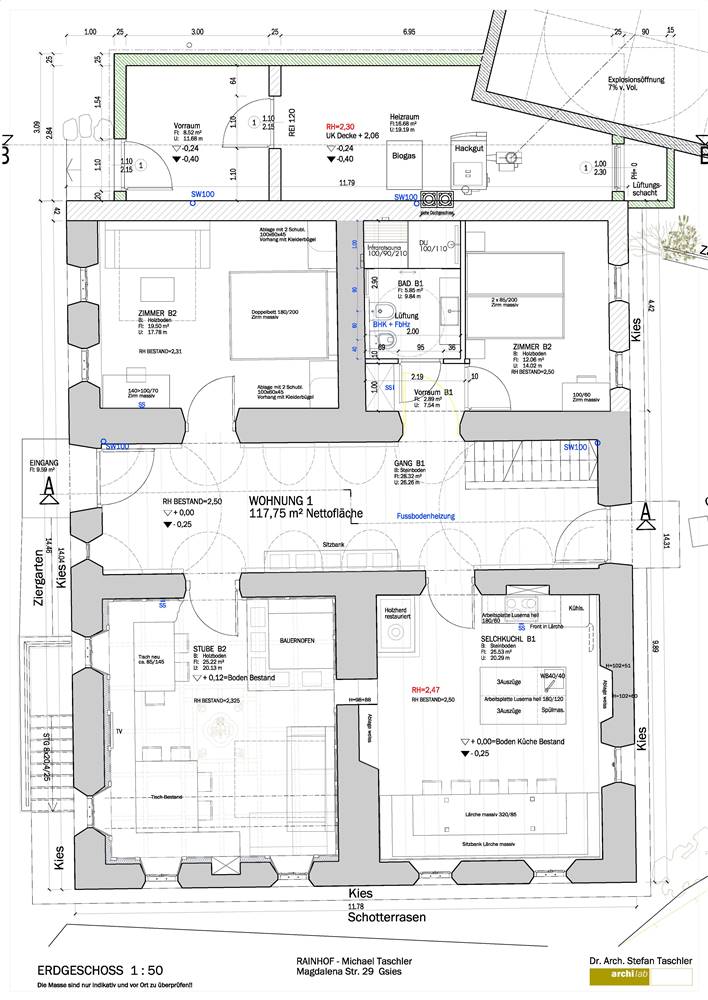
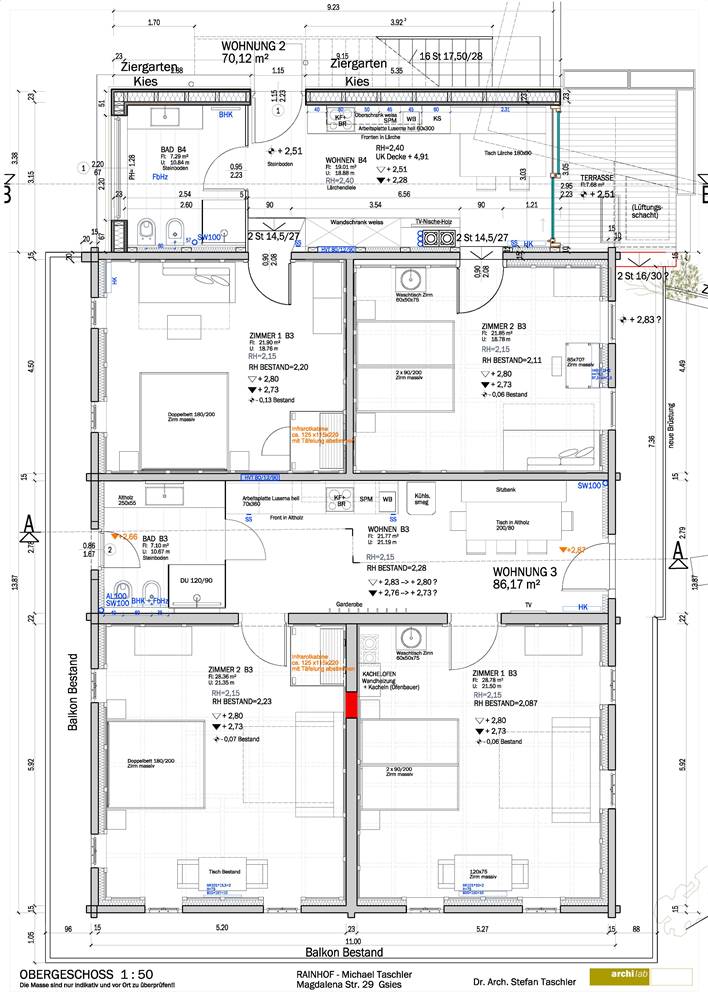
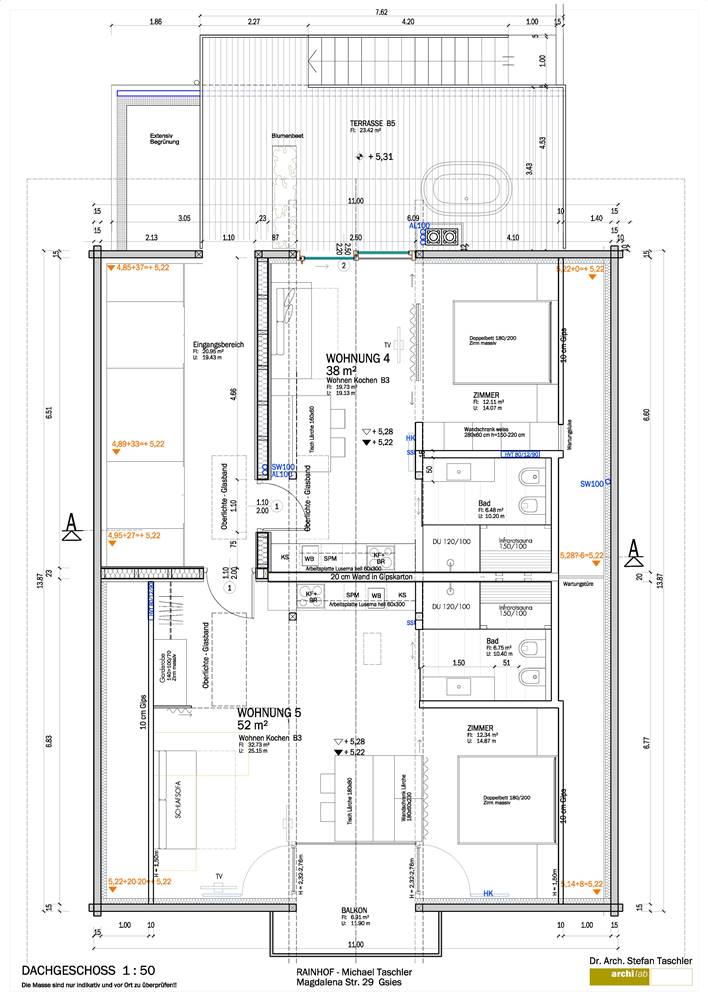
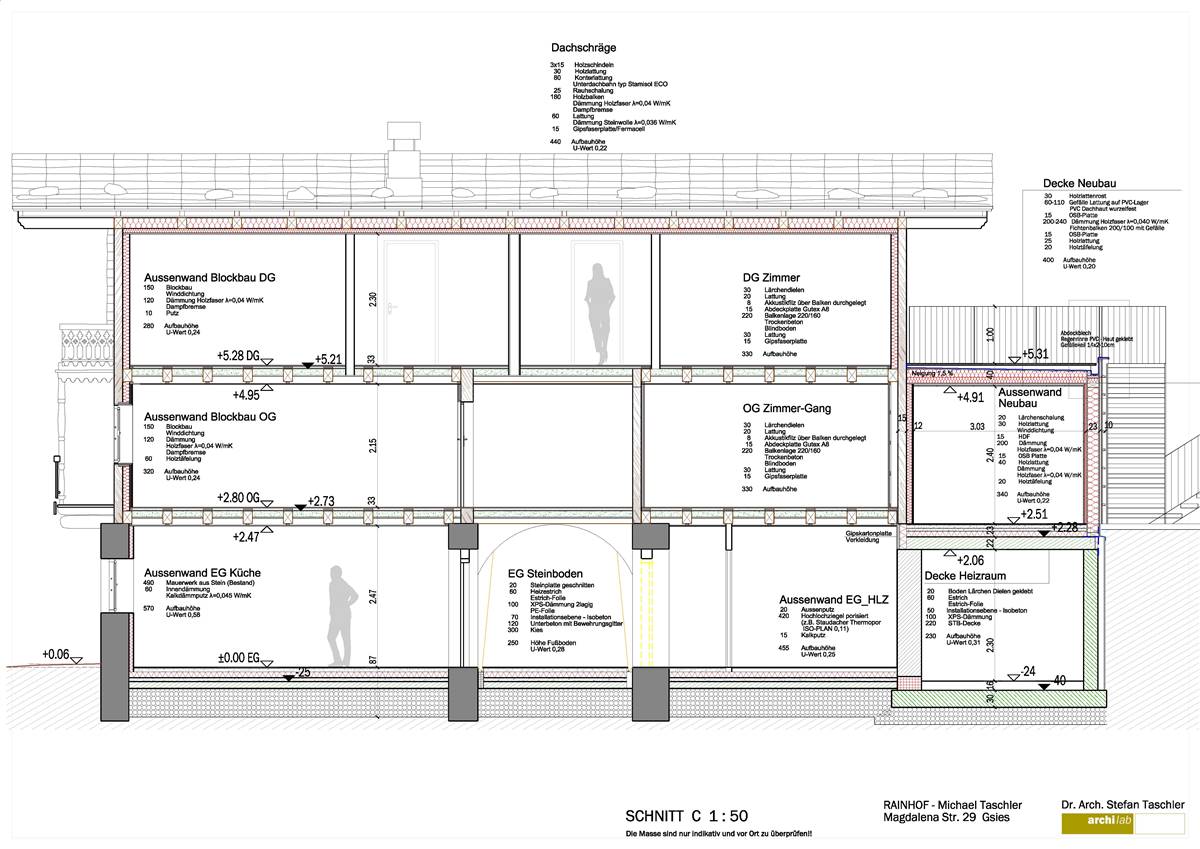
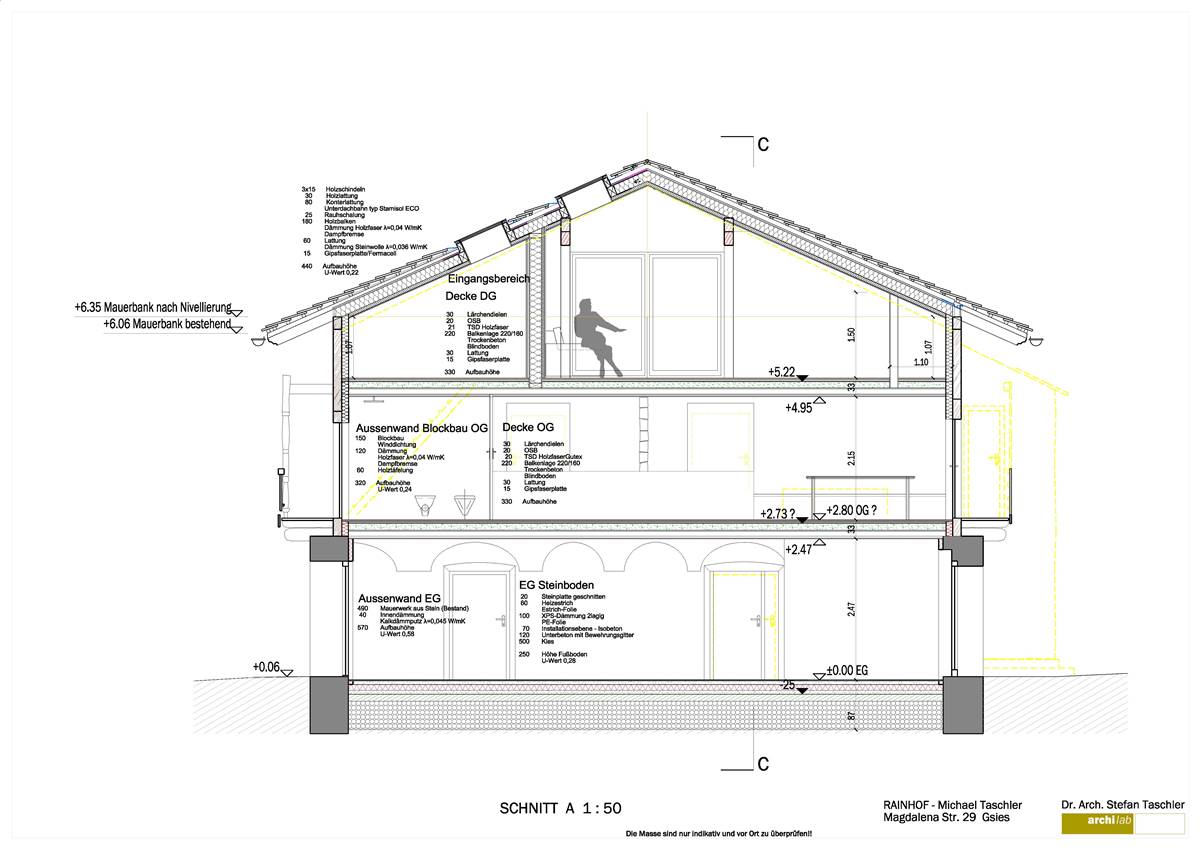
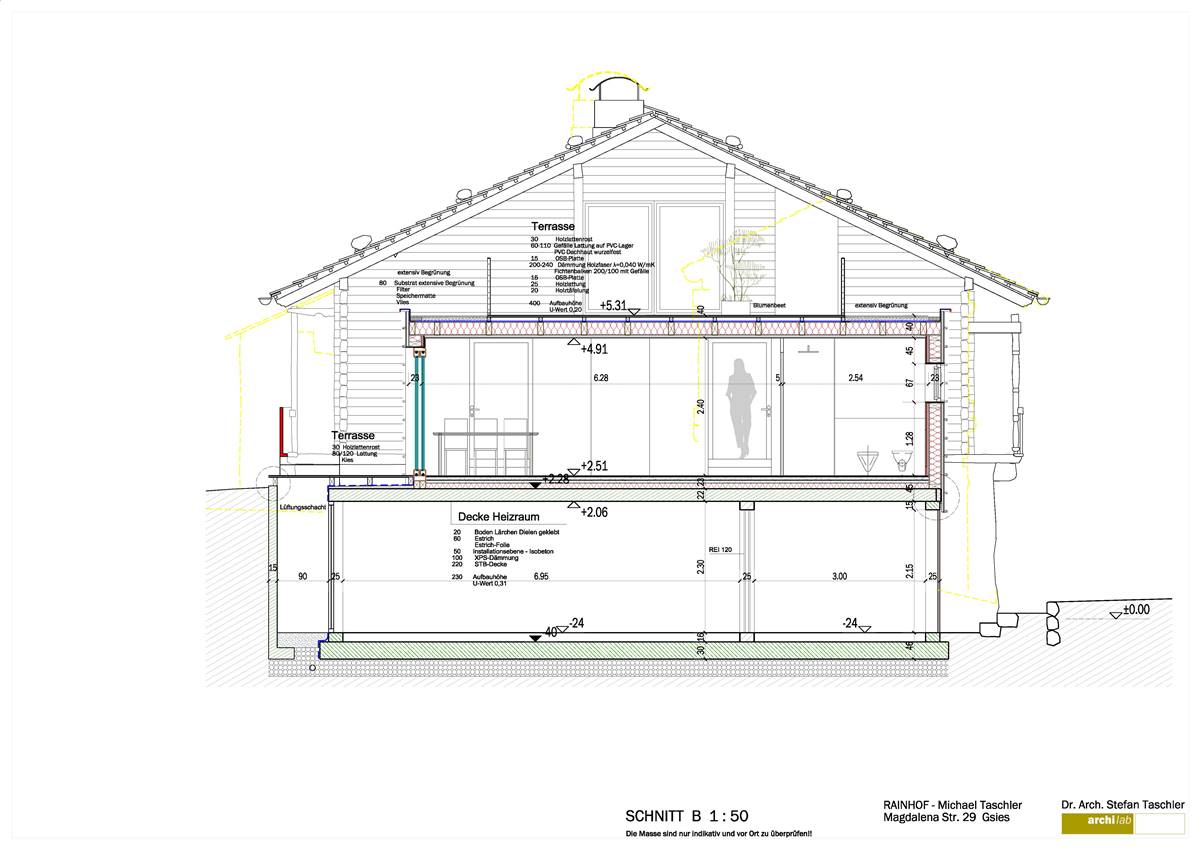
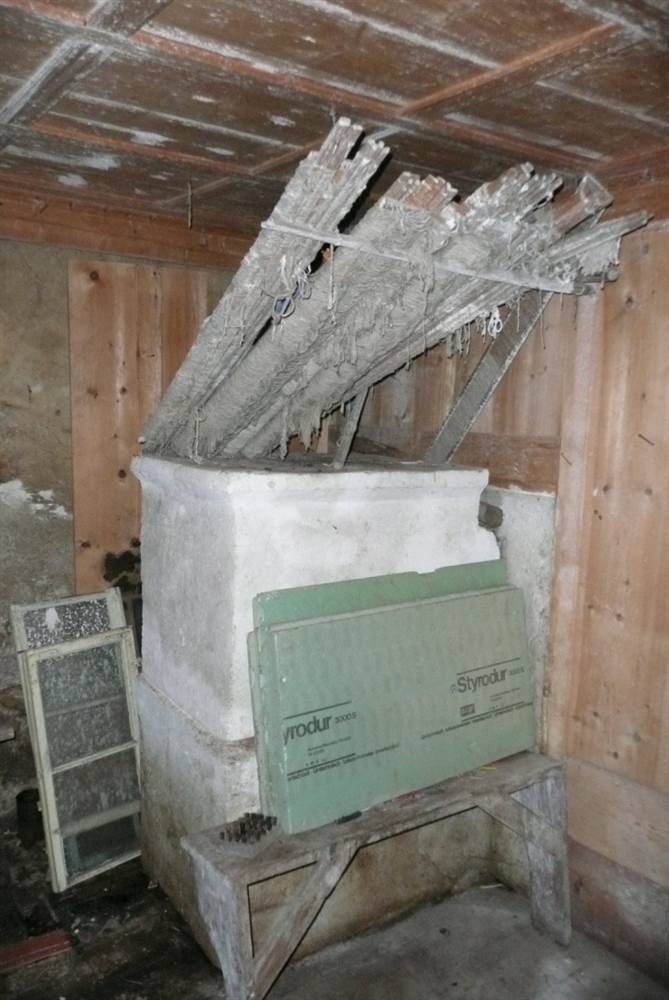

RENOVIERUNGS-PROZESS
Architektur
BESCHREIBUNG
Erhaltungszustand
DENKMALWERT
Ziel der Sanierung
Dr. Arch. Stefan Taschler - archilab
Paul von Sternbach Straße 9; 39031 Bruneck
taschler@archilab.com
Tel.0039 0474 530672
Dr. Arch. Bonaventura, Dr. Kofler Engl (Amt für Bau- und Kunstdenkmäler)
Armando-Diaz-Strasse 8; I-39100 Bozen
kunstdenkmaeler@provinz.bz.it
Tel.0039 0471 41 19 10
Arch. Silvia Bruni
Heilig Kreuz Str. 23 C; St. Lorenzen
arch.silviabruni@gmail.com
Tel.0039 349 5361160
Südtiroler Bauernbund
K.-M. Gamper Str. 5
info@sbb.it
ITAS Versicherungsverein
http://itaspreis.gruppoitas.it/
SANIERUNGS-LÖSUNGEN
Außenwände
Ground floor - Existing stone wall
Ground floor - existing stone wall "Stube"
Ground floor - Substitution of existing wall
First floor - existing "Blockbau" construction (with wooden cladding)
First floor - existing "Blockbau" construction
A large part of the stone masonry wall in the ground floor (except in the "Stube" and "Labe") was insulated internally with a thin layer (4-6 cm) of insulating plaster (Calcetherm λ=0,068W/mK). The U-value was improved from 2,39 W/m2K to 0,87 W/m2K (based on standard values of the energy calculation tool).
This insulating plaster is lime-based and, unlike an insulating panel, it is applied in a thin layer that can follow the uneven surface of the original wall surface ensuring a similar appearance to the original plaster.
30 mm
400 mm
30 mm
30mm
400 mm
30 mm
50 mm
The external wall around the “Stube” was insulated with 8 cm of wood fibreboard placed in the space between the masonry and the wooden cladding.
Using the space behind the wooden cladding, the original wooden panelling and of the proportions of the room were not altered.
30 mm
400 mm
30 mm
80 mm
30 mm
30mm
400 mm
30 mm
80 mm
30 mm
Due to the salt contamination of the northeast corner of the building, it was necessary the demolition of part of the existing wall. A new wall was built with perforated thermal bricks (lambda 0,11 W/(mK)).
Here the appearance from outside is similar to the original wall. Most parts of this wall are also below ground and thus not visible from outside.
30 mm
400 mm
30 mm
20mm
420 mm
15 mm
The existing “Blockbau” (solid wood) construction, consisting of horizontal rectangular hewn beams and wooden paneling was insulated from the inside with 12 cm of wood fiber board. In addition to the thermal resistance improvement (from 0,64 W/m2K to 0,24 W/m2K) the addition of a windproof layer between the old structure and insulation panel improved significantly the air tightness of the whole construction. The insulation layer is covered from the inside with a vapor barrier and a service gap that allows the installation of ducting and wires while protecting the integrity of the construction.
Through the intervention from inside the original wooden construction, the outside appearance does not change. The existing wooden cladding similar was reinstalled as internal finish of the wall. Thus, the original wooden construction was kept with minor modifications to the internal appearance of the rooms.
150 mm
150mm
0 mm
120 mm
15 mm
29 mm
25 mm
In those parts of the existing “Blockbau” (solid wood) construction, where there was no internal wooden paneling the wood construction was as well insulated from the inside with 12 cm of wood fiber board (cf. Wall "First floor - existing "Blockbau" construction (with wooden cladding)") . Also here, in addition to the thermal resistance improvement (from 0,76 W/m2K to 0,24 W/m2K) the addition of a windproof layer between the old structure and insulation panel improved significantly the air tightness of the whole construction. The insulation layer is covered from the inside with a vapor barrier and a service gap that allows the installation of ducting and wires while protecting the integrity of the construction.
A new wooden cladding similar to the original surface was installed as internal finish of the wall. Thus, the original wooden construction was kept with minor modifications to the internal appearance of the rooms.
Fenster
All windows
All existing windows were exchanged with new units made ad-hoc by a local furniture maker. The aim was building a two-sash window with two glazing bars each that on the one hand achieved high levels energy performance and on the other hand were of high aesthetic quality.
In order to preserve the original appearance of the windows in the façade, one of the original windows was used as a model for the new windows in terms of proportions and profile widths. To improve the thermal performance of the window, an insulating glass unit was installed.
Fenstertyp Bestand | Box-type window |
Verglasungsart Bestand | Single |
Verschattung Bestand | Outer shutter |
Neuer Fenstertyp | Casement window |
Verglasungsart des neuen Fensters | Double |
Verschattung des neuen Fensters | NA |
Neuer Energiedurchlassgrad g [-] | 0,0 |
Weitere Maßnahmen
DACH
ERDGESCHOSS
Insulation of the former "cold" pitched roof. The insulation was applied internally to maintain the existing wood shingle roof.
To improve the supply of daylight in the two holiday apartments in the attic, two glass bands were installed in consultation with the heritage office.
15 mm
110 mm
30 mm
180 mm
15 mm
110 mm
30 mm
180 mm
40 mm
Usually the ground floor was built directly on the soil. The retrofit included 50 cm of gravel, subconcrete (12 cm), installation layer/insulating concrete (7 cm), insulation (7 + 2 cm ), floating floor with radiation system, stone slabs (2,5)
30 mm
120 mm
500 mm
30 mm
65 mm
75 mm
120 mm
500 mm
HVAC
HEIZUNG
BRAUCHWARMWASSER
A new heating system works as a combination of a biogas boiler and wood-chip boiler (2). Almost all rooms are heated through a floor heating system.
The traditional stove is kept in the “Stube” although it is not heated with firewood anymore, instead it is connected to the central boiler. In the rooms where the old wood floorboards were restored, no floor heating was used, but single radiators.
Heizungssystem nach Sanierung | zusätzliches Heizungssystem nach Sanierung | |
---|---|---|
Art der Heizung | Boiler | Stove |
Brennstoff | Gas | Biomass |
Wärmeverteilung | Radiating floor | Stove |
Nennleistung | test kW | NA kW |
ERNEUERBARE ENERGIE
Biomasse
As described above, space heating and domestic hot water is provided by two different boilers, both running with renewable energy. The biomass boiler uses wood chip produced directly from the farm woodland and stored in the silo next to the building. The gas boiler runs with the biogas produced from the manure of the cattle reared in the farm in a biogas plant built between the stable and residential building. The energy produced from biogas and wood chips cover the energy need of the Rainhof, a nearby house (included holiday apartments) and the stable.
Biomass System | |
---|---|
Type | |
Storage size | |
Origin of biomass | |
Overall yearly production | 50,0 kWh |
Energieeffizienz
Freiwillige Zertifikate Nein
Energieverbrauch nach Sanierung 60 kWh/m2.y
Primärenergie
Berechnungsmethode The energy produced from biogas and wood chips cover the energy need of the Rainhof, a nearby house (included holiday apartments) and the stable.
Raumklima
The impact of the intervention on the indoor climate was evaluated by means of a post-occupancy evaluation, including the opinions of the building owner (and occupier of the main dwelling unit) and a number of guests. The overall impression on the comfort was positive. Guests opinions on the thermal comfort was very positive. They appreciated the control of two independent circuits of the heating system in the apartment (kitchen, living room, and bedroom and separately the bathroom).
Building owner and guests evaluate the indoor air quality as positive.
Building owner and guests evaluate the daylight supply as sufficient, despite the reduced dimensions of traditional window openings, even in winter.
Building owner and guests evaluate the overall living comfort as positive. The appartments towarts the courtyard have better conditions, as they are turned away from the street